Introduction to PCB Quality and Failure Analysis
Printed Circuit Boards (PCBs) are essential components in almost all modern electronic devices. The quality of PCBs directly impacts the performance, reliability, and longevity of these devices. Poor quality PCBs can lead to device malfunctions, short circuits, and even complete failures. Therefore, ensuring good PCB quality is crucial for manufacturers to deliver reliable products and maintain customer satisfaction.
PCB failure analysis plays a vital role in assuring the quality of PCBs. It involves investigating and identifying the root causes of PCB failures, and implementing corrective actions to prevent future occurrences. By conducting thorough failure analysis, manufacturers can improve their PCB design, manufacturing processes, and quality control measures.
The Importance of PCB Quality
PCB quality is critical for several reasons:
-
Reliability: High-quality PCBs ensure that electronic devices function reliably without interruptions or failures. This is particularly important for mission-critical applications, such as medical devices, aerospace systems, and automotive electronics.
-
Safety: Poor quality PCBs can pose safety hazards, such as electrical shocks, fires, or explosions. Ensuring good PCB quality helps prevent such incidents and protects users from harm.
-
Cost-effectiveness: Investing in PCB quality upfront can save significant costs in the long run. Defective PCBs lead to product returns, replacements, and repairs, which can be expensive for manufacturers. By ensuring good quality from the start, manufacturers can avoid these additional costs.
-
Reputation: Delivering high-quality products is essential for building and maintaining a positive brand reputation. Customers are more likely to trust and recommend manufacturers who consistently provide reliable and well-functioning products.
Common PCB Failure Modes and Their Causes
PCBs can fail in various ways, each with its own set of causes. Understanding these failure modes and their underlying causes is crucial for effective failure analysis and prevention. Some common PCB failure modes include:
1. Shorts and Opens
Shorts occur when there is an unintended electrical connection between two or more points on a PCB, while opens happen when there is a lack of electrical continuity where it should exist. These failures can be caused by:
- Manufacturing defects, such as incorrect etching or drilling
- Damaged or broken traces due to mechanical stress or impact
- Solder bridging or insufficient solder joints
- Contamination or foreign object debris (FOD) on the PCB surface
2. Component Failures
Component failures involve malfunctions or breakdowns of individual electronic components mounted on the PCB. Common causes include:
- Overheating due to inadequate thermal management or power surges
- Electrostatic discharge (ESD) damage during handling or assembly
- Mechanical stress or vibration leading to component damage
- Aging or wear-out of components over time
3. Delamination and Cracking
Delamination refers to the separation of PCB layers, while cracking involves fractures in the PCB substrate or copper traces. These failures can result from:
- Thermal stress due to excessive heat or rapid temperature changes
- Mechanical stress or bending of the PCB
- Moisture absorption leading to swelling and weakening of the PCB structure
- Improper handling or storage conditions
4. Corrosion and Oxidation
Corrosion and oxidation occur when PCBs are exposed to harsh environmental conditions, such as high humidity, salt spray, or chemical contamination. These failures can cause:
- Degradation of copper traces and pads
- Weakening of solder joints and component connections
- Electrical short circuits or open circuits
- Deterioration of the PCB substrate material
PCB Failure Analysis Techniques
To effectively identify the root causes of PCB failures and implement corrective actions, several failure analysis techniques are employed. These techniques range from visual inspection to advanced analytical methods, depending on the nature and complexity of the failure. Some commonly used PCB failure analysis techniques include:
1. Visual Inspection
Visual inspection is the first step in PCB failure analysis. It involves examining the PCB surface and components for any visible defects, such as:
- Damaged or missing components
- Solder joint issues (bridging, insufficient solder, or cold joints)
- PCB surface contamination or foreign object debris
- Discoloration or charring indicating overheating
Visual inspection can be performed using the naked eye, magnifying lenses, or microscopes, depending on the level of detail required.
2. X-Ray Imaging
X-ray imaging is a non-destructive technique that allows the internal structure of a PCB to be visualized without disassembly. It is particularly useful for detecting:
- Solder joint defects, such as voids or insufficient solder
- Component placement issues or misalignments
- Broken or damaged internal traces or vias
- Foreign object debris trapped within the PCB layers
X-ray imaging can be performed using 2D or 3D X-ray systems, depending on the complexity of the PCB and the level of detail required.
3. Acoustic Microscopy
Acoustic microscopy uses high-frequency sound waves to create images of the internal structure of a PCB. It is effective for detecting:
- Delamination or voids within the PCB layers
- Cracks or fractures in the PCB substrate or components
- Disbonds or poor adhesion between PCB layers or components
Acoustic microscopy is a non-destructive technique that can provide detailed images of the PCB’s internal structure without the need for cross-sectioning.
4. Thermal Imaging
Thermal imaging, also known as infrared (IR) imaging, is used to detect temperature variations across a PCB surface. It is useful for identifying:
- Overheating components or hot spots on the PCB
- Inadequate thermal management or cooling issues
- Shorts or opens causing abnormal heat generation
Thermal imaging can be performed using handheld IR cameras or specialized thermal imaging systems integrated with failure analysis workstations.
5. Electrical Testing
Electrical testing involves measuring various electrical parameters of a PCB to identify failures or anomalies. Some common electrical tests include:
- Continuity testing to detect open circuits or broken traces
- Resistance measurements to identify shorts or abnormal resistances
- Voltage and current measurements to detect power supply issues or component malfunctions
- Signal integrity testing to assess the quality of high-speed signals
Electrical testing can be performed using multimeters, oscilloscopes, or specialized PCB testing equipment.
6. Microsectioning and Metallography
Microsectioning involves cross-sectioning a PCB to examine its internal structure and components. It is a destructive technique that requires careful sample preparation and analysis. Metallography is the study of the microstructure of metals, such as the copper traces in a PCB.
Microsectioning and metallography are used to:
- Examine the quality and integrity of PCB layers and plated through-holes
- Analyze the microstructure of solder joints and component connections
- Identify cracks, voids, or delamination within the PCB structure
- Investigate the root causes of component failures or PCB defects
These techniques require specialized equipment, such as precision cutting tools, mounting presses, grinding and polishing machines, and high-magnification microscopes.
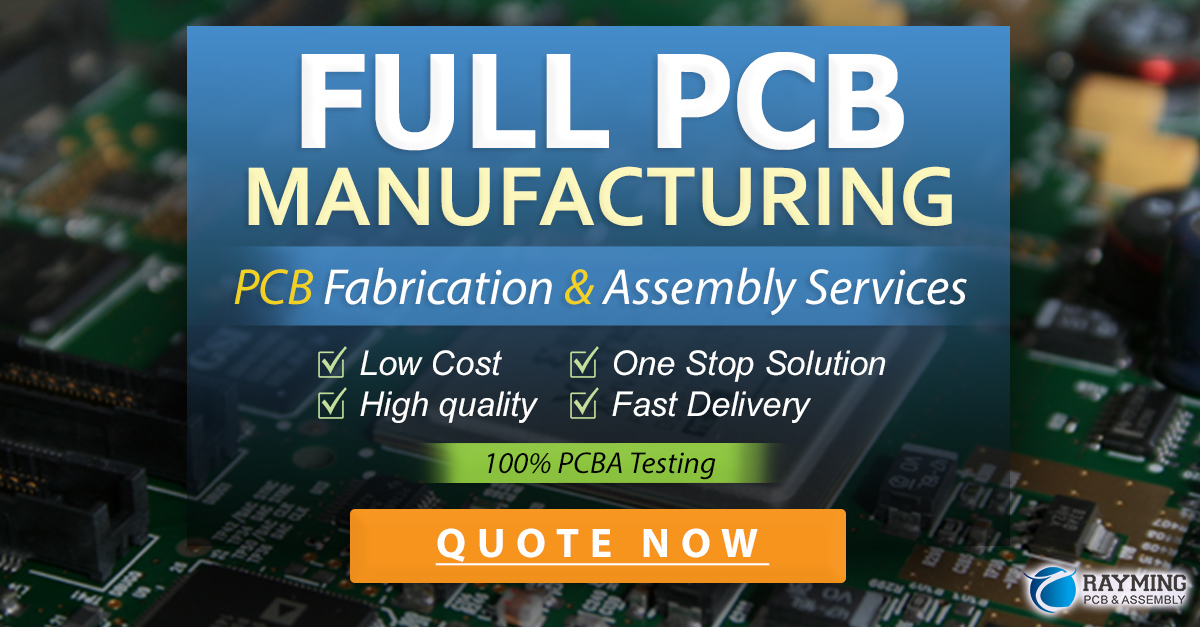
Implementing Corrective Actions and Preventive Measures
Once the root causes of PCB failures have been identified through failure analysis, the next step is to implement corrective actions and preventive measures to avoid future occurrences. These actions can be categorized into three main areas:
1. Design Improvements
Design improvements focus on optimizing the PCB layout, component selection, and manufacturing specifications to enhance reliability and prevent failures. Some design-related corrective actions include:
- Updating the PCB layout to improve signal integrity, thermal management, or mechanical stability
- Selecting more robust or reliable components with better specifications or ratings
- Optimizing the placement and routing of components to minimize stress or interference
- Incorporating design for manufacturability (DFM) principles to improve manufacturing yield and quality
2. Manufacturing Process Enhancements
Manufacturing process enhancements involve optimizing the PCB fabrication and assembly processes to minimize defects and improve consistency. Some process-related corrective actions include:
- Calibrating and maintaining manufacturing equipment to ensure proper operation and accuracy
- Implementing statistical process control (SPC) to monitor and control key process parameters
- Enhancing operator training and supervision to minimize human errors or inconsistencies
- Improving cleanroom conditions and contamination control measures to prevent foreign object debris
3. Quality Control and Testing Procedures
Quality control and testing procedures are essential for detecting and preventing PCB failures before they reach the end-user. Some quality-related corrective actions include:
- Implementing more stringent incoming inspection and testing of PCB materials and components
- Enhancing in-process inspection and testing at critical stages of PCB fabrication and assembly
- Conducting thorough final testing and burn-in to identify any latent defects or failures
- Establishing a robust failure reporting and corrective action system (FRACAS) to track and analyze PCB failures over time
By implementing these corrective actions and preventive measures, manufacturers can continuously improve their PCB quality, reduce failure rates, and enhance customer satisfaction.
PCB Failure Analysis Case Studies
To illustrate the practical application of PCB failure analysis techniques and corrective actions, let’s examine two real-world case studies.
Case Study 1: Intermittent USB Port Failure
Problem: A consumer electronics manufacturer received numerous customer complaints about intermittent USB port failures in their latest smartphone model. The USB ports would work initially but would stop functioning after a few weeks of use.
Failure Analysis: The manufacturer conducted a series of failure analysis techniques, including:
- Visual inspection of the USB port and surrounding components
- X-ray imaging to examine the solder joints and internal connections
- Electrical testing to measure the continuity and resistance of the USB port pins
- Microsectioning to analyze the cross-section of the USB port and PCB
The failure analysis revealed that the solder joints connecting the USB port to the PCB were inadequate and prone to cracking under repeated insertion and removal of USB cables. The cracks in the solder joints caused intermittent electrical connections, leading to USB port failures.
Corrective Actions:
- Redesigned the USB port footprint on the PCB to provide more robust solder joint connections
- Modified the solder paste stencil design to ensure sufficient solder volume and coverage
- Optimized the reflow soldering profile to improve solder joint strength and reliability
- Implemented 100% automated optical inspection (AOI) of USB port solder joints during manufacturing
After implementing these corrective actions, the USB port failure rate decreased significantly, and customer complaints were resolved.
Case Study 2: Overheating and Component Burnout
Problem: An industrial control system manufacturer experienced frequent field failures of their motor control PCBs. The PCBs would overheat and suffer component burnout, leading to system shutdowns and costly repairs.
Failure Analysis: The manufacturer conducted a comprehensive failure analysis, including:
- Thermal imaging to identify hot spots and temperature distributions on the PCB
- Visual inspection and X-ray imaging to detect any visible damage or abnormalities
- Electrical testing to measure the power consumption and voltage levels of key components
- Microsectioning and metallography to examine the condition of overheated components and PCB traces
The failure analysis revealed that the PCB layout had inadequate thermal management, with power-dissipating components clustered together without sufficient heat sinking or airflow. This led to localized overheating and eventual component burnout.
Corrective Actions:
- Redesigned the PCB layout to improve thermal management, including:
- Separating power-dissipating components to minimize thermal coupling
- Adding heatsinks and thermal vias to enhance heat dissipation
- Optimizing the placement of temperature-sensitive components
- Selected components with higher temperature ratings and power handling capabilities
- Implemented forced air cooling in the system enclosure to improve overall thermal management
- Conducted thorough thermal testing and validation of the redesigned PCBs
After implementing these corrective actions, the motor control PCBs operated reliably without overheating or component burnout issues, improving overall system reliability and reducing field failure costs.
These case studies demonstrate how PCB failure analysis plays a crucial role in identifying the root causes of failures and guiding corrective actions to improve PCB quality and reliability.
Frequently Asked Questions (FAQ)
-
What are the most common causes of PCB failures?
The most common causes of PCB failures include manufacturing defects, component failures, mechanical stress, thermal stress, and environmental factors such as moisture, corrosion, and contamination. -
How can PCB failure analysis help improve product quality?
PCB failure analysis helps identify the root causes of failures, allowing manufacturers to implement targeted corrective actions and preventive measures. By continuously analyzing failures and improving PCB design, manufacturing processes, and quality control, manufacturers can enhance product quality, reliability, and customer satisfaction. -
What are some key techniques used in PCB failure analysis?
Some key techniques used in PCB failure analysis include visual inspection, X-ray imaging, acoustic microscopy, thermal imaging, electrical testing, and microsectioning with metallography. These techniques help analyze the physical, thermal, and electrical characteristics of PCBs to identify defects, anomalies, and failure mechanisms. -
How can manufacturers prevent PCB failures in their products?
Manufacturers can prevent PCB failures by implementing a combination of design improvements, manufacturing process enhancements, and robust quality control measures. This includes optimizing PCB layouts, selecting reliable components, controlling manufacturing processes, conducting thorough inspections and testing, and continuously monitoring and analyzing field failures for improvement opportunities. -
What role does PCB design play in preventing failures?
PCB design plays a critical role in preventing failures by ensuring the PCB layout, component selection, and manufacturing specifications are optimized for reliability and manufacturability. Proper PCB design considerations, such as signal integrity, thermal management, and mechanical stability, can significantly reduce the risk of failures and improve overall product quality.
Conclusion
PCB failure analysis is a vital process for assuring good quality and reliability in electronic products. By investigating and identifying the root causes of PCB failures, manufacturers can implement effective corrective actions and preventive measures to enhance their PCB design, manufacturing processes, and quality control procedures.
A comprehensive PCB failure analysis approach involves various techniques, such as visual inspection, X-ray imaging, acoustic microscopy, thermal imaging, electrical testing, and microsectioning with metallography. These techniques help analyze the physical, thermal, and electrical characteristics of PCBs to identify defects, anomalies, and failure mechanisms.
Implementing corrective actions based on failure analysis findings is crucial for preventing future occurrences and improving overall PCB quality. These actions may include design improvements, manufacturing process enhancements, and optimized quality control and testing procedures.
Real-world case studies demonstrate the practical application of PCB failure analysis in resolving issues such as intermittent USB port failures and overheating with component burnout. By continuously analyzing failures and implementing targeted improvements, manufacturers can enhance product reliability, reduce field failure costs, and improve customer satisfaction.
In conclusion, PCB failure analysis is an essential tool for assuring good quality and reliability in electronic products. By embracing a proactive approach to failure analysis and continuous improvement, manufacturers can stay competitive in today’s demanding market and deliver high-quality, reliable products to their customers.
Leave a Reply