Introduction to PCB Edge Plating
Printed Circuit Board (PCB) edge plating, also known as metalizing circuit board edges, is a process that involves coating the edges of a PCB with a conductive material, typically copper. This process is crucial for various applications, such as providing electrical connectivity, enhancing mechanical strength, and improving the overall durability of the PCB. In this article, we will delve into the world of PCB edge plating, focusing on the electroless copper plating method.
What is PCB Edge Plating?
PCB edge plating is a technique used to deposit a conductive layer, usually copper, on the exposed edges of a printed circuit board. This process is performed after the PCB has been fabricated and the individual boards have been separated from the panel. By plating the edges, designers can achieve several benefits, including:
- Electrical connectivity between layers
- Improved mechanical strength and durability
- Protection against oxidation and corrosion
- Enhanced aesthetics and professional appearance
Importance of PCB Edge Plating
Edge plating is particularly important in multi-layer PCBs, where electrical connections need to be established between different layers. By plating the edges, designers can create a conductive path that allows signals to pass through the layers seamlessly. This is especially critical in high-speed and high-frequency applications, where signal integrity is of utmost importance.
Moreover, edge plating helps to strengthen the mechanical structure of the PCB. The plated edges act as a reinforcement, preventing delamination and improving the overall durability of the board. This is particularly useful in harsh environments or applications where the PCB is subjected to mechanical stress or vibrations.
Electroless Copper Plating Process
Electroless copper plating is a popular method for metalizing PCB edges. This process involves depositing a layer of copper on the PCB edges without the use of an external electrical current. Instead, it relies on a chemical reaction between the copper ions in the plating solution and a reducing agent.
Steps Involved in Electroless Copper Plating
The electroless copper plating process typically consists of the following steps:
-
Cleaning: The PCB edges are thoroughly cleaned to remove any contaminants, such as dirt, grease, or oxidation. This step is crucial to ensure proper adhesion of the copper layer.
-
Activation: The cleaned edges are then activated using a palladium-based catalyst. This catalyst helps to initiate the chemical reaction required for copper deposition.
-
Plating: The activated PCB is immersed in an electroless copper plating solution. The solution contains copper ions, a reducing agent, and other additives that control the plating process. As the chemical reaction occurs, copper ions are reduced and deposited on the PCB edges, forming a uniform layer of copper.
-
Rinsing: After plating, the PCB is rinsed with deionized water to remove any excess plating solution and prevent further chemical reactions.
-
Drying: The rinsed PCB is then dried using hot air or an oven to remove any residual moisture.
-
Inspection: Finally, the plated edges are inspected for uniformity, thickness, and adhesion. If necessary, additional plating cycles can be performed to achieve the desired thickness.
Advantages of Electroless Copper Plating
Electroless copper plating offers several advantages over other edge plating methods:
-
Uniformity: Electroless plating produces a highly uniform copper layer, even on complex edge geometries. This ensures consistent electrical and mechanical properties across the entire PCB.
-
Adhesion: The chemical bond formed between the copper layer and the PCB substrate results in excellent adhesion. This reduces the risk of delamination and improves the overall reliability of the PCB.
-
Versatility: Electroless copper plating can be applied to various PCB materials, including FR-4, polyimide, and high-frequency laminates.
-
Cost-effectiveness: Compared to other edge plating methods, electroless copper plating is relatively cost-effective, especially for high-volume production.
Factors Affecting PCB Edge Plating Quality
Several factors can influence the quality of PCB edge plating. Understanding and controlling these factors is essential to achieve consistent and reliable results.
Edge Preparation
Proper edge preparation is crucial for successful edge plating. The edges should be clean, smooth, and free from any burrs or debris. Rough or contaminated edges can lead to poor adhesion, uneven plating, and potential reliability issues.
Edge Preparation Step | Purpose |
---|---|
Deburring | Removes rough edges and burrs |
Cleaning | Eliminates contaminants and ensures clean surface |
Beveling | Creates a smooth transition between layers |
Plating Solution Composition
The composition of the electroless copper plating solution plays a significant role in determining the quality of the plated edges. The solution should be carefully formulated to achieve the desired plating rate, thickness, and uniformity.
Component | Function |
---|---|
Copper ions | Source of copper for plating |
Reducing agent | Initiates and sustains the chemical reaction |
Complexing agents | Stabilizes the solution and prevents precipitation |
pH regulators | Maintains the optimal pH range for plating |
Plating Temperature and Time
The plating temperature and time are critical parameters that influence the plating rate and the final thickness of the copper layer. Higher temperatures generally result in faster plating rates, while longer plating times lead to thicker copper layers.
Parameter | Typical Range |
---|---|
Temperature | 45-55°C |
Time | 30-60 minutes |
It is important to optimize these parameters based on the specific requirements of the PCB and the plating solution being used.
Post-Plating Processes
After plating, additional processes may be required to enhance the performance and durability of the plated edges. These processes can include:
- Annealing: Heating the plated edges to improve the copper’s ductility and reduce internal stresses.
- Solder mask application: Applying a solder mask layer over the plated edges to provide insulation and protection against oxidation.
- Surface finish: Applying a surface finish, such as ENIG (Electroless Nickel Immersion Gold) or OSP (Organic Solderability Preservative), to improve solderability and protect against corrosion.
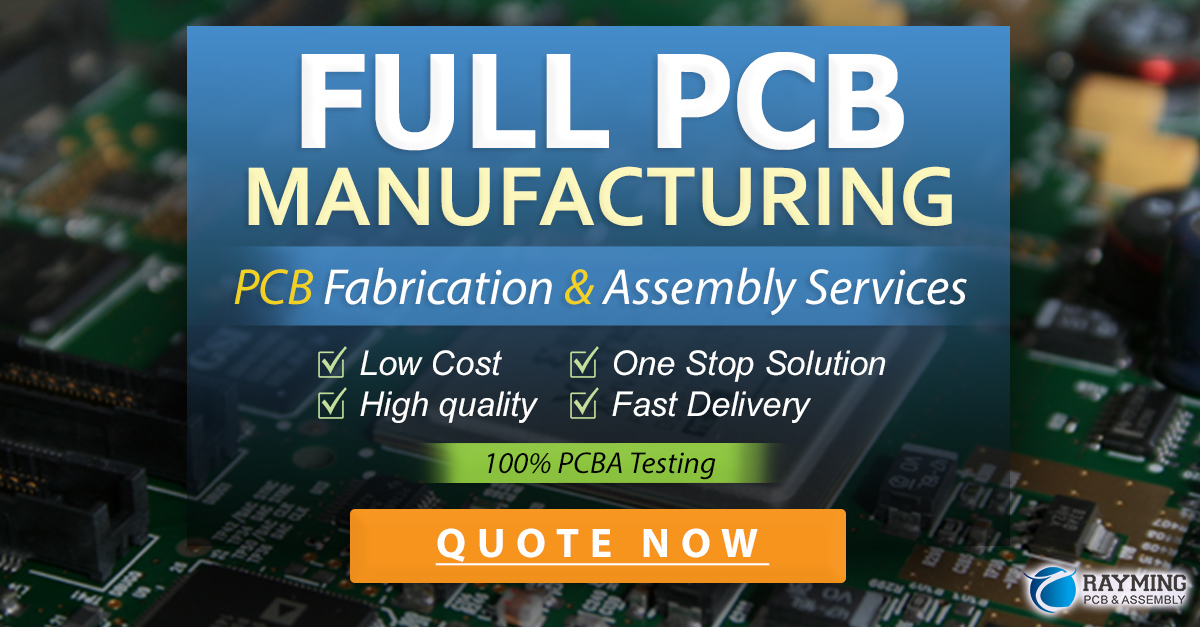
Quality Control and Testing
To ensure the reliability and performance of PCBs with plated edges, it is essential to implement robust quality control measures and testing procedures.
Visual Inspection
Visual inspection is the first line of defense in detecting any defects or anomalies in the plated edges. This includes checking for:
- Uniformity and coverage of the copper layer
- Absence of voids, pits, or cracks
- Proper alignment and registration of the plated edges
Thickness Measurement
Measuring the thickness of the plated copper layer is crucial to ensure compliance with the specified requirements. Various methods can be used for thickness measurement, including:
- X-ray fluorescence (XRF)
- Cross-sectional analysis
- Coulometric testing
Adhesion Testing
Adhesion testing is performed to evaluate the bond strength between the plated copper layer and the PCB substrate. Common adhesion testing methods include:
- Tape test (ISO 2409)
- Peel test (IPC-TM-650 2.4.8)
- Shear test (ASTM D3163)
Electrical Testing
Electrical testing is conducted to verify the continuity and resistance of the plated edges. This can be done using:
- Continuity testing
- Four-wire resistance measurement
- Insulation resistance testing
Troubleshooting Common Issues
Despite careful process control, issues may arise during PCB edge plating. Some common problems and their potential solutions are:
Issue | Possible Cause | Solution |
---|---|---|
Uneven plating | Inadequate edge preparation or contamination | Improve edge cleaning and activation processes |
Voids or pits | Air bubbles or contamination in the plating solution | Filter the solution and ensure proper agitation |
Poor adhesion | Insufficient cleaning or activation | Optimize the cleaning and activation steps |
Thin or incomplete plating | Inadequate plating time or low plating rate | Increase plating time or adjust solution composition |
Future Trends in PCB Edge Plating
As the electronics industry continues to evolve, new trends and technologies are emerging in the field of PCB edge plating. Some of these trends include:
- Selective edge plating: Plating only specific areas of the PCB edges to reduce costs and improve efficiency.
- Alternative plating materials: Exploring the use of other conductive materials, such as graphene or conductive polymers, for edge plating.
- Additive manufacturing: Integrating edge plating with 3D printing technologies to create complex, multi-functional PCB structures.
- Environmental sustainability: Developing eco-friendly plating solutions and processes to reduce the environmental impact of PCB manufacturing.
Conclusion
PCB edge plating is a critical process that ensures the electrical connectivity, mechanical strength, and durability of printed circuit boards. Electroless copper plating is a widely used method for metalizing PCB edges, offering advantages such as uniformity, adhesion, and cost-effectiveness. By understanding the process, controlling the key factors, and implementing proper quality control measures, designers and manufacturers can achieve reliable and high-performance PCBs with plated edges.
As the electronics industry advances, new trends and technologies are expected to shape the future of PCB edge plating. Selective plating, alternative materials, additive manufacturing, and environmental sustainability are just a few examples of the exciting developments on the horizon.
Frequently Asked Questions (FAQ)
-
What is the purpose of PCB edge plating?
PCB edge plating serves several purposes, including providing electrical connectivity between layers, enhancing mechanical strength, protecting against oxidation and corrosion, and improving the overall aesthetics of the PCB. -
How does electroless copper plating differ from electrolytic plating?
Electroless copper plating relies on a chemical reaction to deposit copper on the PCB edges, without the use of an external electrical current. In contrast, electrolytic plating uses an electric current to drive the deposition process. -
What factors influence the quality of PCB edge plating?
Several factors can affect the quality of PCB edge plating, such as edge preparation, plating solution composition, plating temperature and time, and post-plating processes. Proper control and optimization of these factors are essential for achieving consistent and reliable results. -
How is the thickness of the plated copper layer measured?
The thickness of the plated copper layer can be measured using various methods, including X-ray fluorescence (XRF), cross-sectional analysis, and coulometric testing. These methods provide accurate measurements to ensure compliance with the specified requirements. -
What are some common issues encountered in PCB edge plating, and how can they be resolved?
Common issues in PCB edge plating include uneven plating, voids or pits, poor adhesion, and thin or incomplete plating. These issues can be addressed by optimizing edge preparation, filtering the plating solution, adjusting plating parameters, and improving cleaning and activation processes.
Leave a Reply