What is DFM in PCB Design?
DFM, which stands for “Design for Manufacturability”, is a crucial principle in PCB design that aims to optimize the design process to ensure the manufacturability, reliability, and cost-effectiveness of the end product. By considering DFM guidelines during the design phase, engineers can avoid potential manufacturing issues, reduce production costs, and enhance the overall quality of the PCB.
Why is DFM Important in PCB Design?
Implementing DFM principles in PCB design offers several key benefits:
-
Cost Reduction: By designing PCBs that are easier to manufacture, you can minimize production costs, reduce the likelihood of defects, and avoid unnecessary iterations.
-
Improved Reliability: DFM guidelines help ensure that the PCB will function as intended and withstand the rigors of its intended environment, resulting in a more reliable end product.
-
Faster Time-to-Market: By avoiding manufacturing issues and reducing the need for design revisions, DFM can help accelerate the production process and bring your product to market faster.
-
Enhanced Collaboration: DFM encourages collaboration between design and manufacturing teams, fostering a shared understanding of design requirements and manufacturing capabilities.
Key Aspects of DFM in PCB Design
To successfully implement DFM in your PCB design process, consider the following key aspects:
1. Component Selection and Placement
- Choose components that are readily available, have standard packaging, and are compatible with the manufacturing process.
- Place components in a way that facilitates easy assembly and minimizes the risk of defects.
- Consider the orientation and spacing of components to ensure proper soldering and avoid interference.
2. Trace Routing and Spacing
- Follow the manufacturer’s guidelines for minimum trace width and spacing to ensure proper signal integrity and avoid manufacturing issues.
- Use consistent trace widths and avoid sharp angles or abrupt changes in direction to minimize signal reflections and improve manufacturability.
- Provide sufficient clearance between traces and components to prevent short circuits and facilitate assembly.
3. Via and Hole Sizing
- Adhere to the manufacturer’s recommendations for minimum via and hole sizes to ensure proper plating and avoid drilling issues.
- Use standard via sizes whenever possible to reduce manufacturing costs and improve reliability.
- Avoid placing vias under components or in areas that may cause assembly difficulties.
4. Solder Mask and Silkscreen
- Provide adequate solder mask clearance around pads and vias to prevent solder bridging and improve the assembly process.
- Use clear and legible silkscreen labels to aid in component placement and assembly.
- Ensure that silkscreen labels do not overlap with pads or other critical features of the PCB.
5. Panelization and Tooling
- Consider the panelization requirements of the manufacturer to optimize the production process and reduce costs.
- Include appropriate tooling holes and fiducial marks to facilitate accurate alignment and assembly.
- Follow the manufacturer’s guidelines for panel sizes, spacing, and depaneling methods.
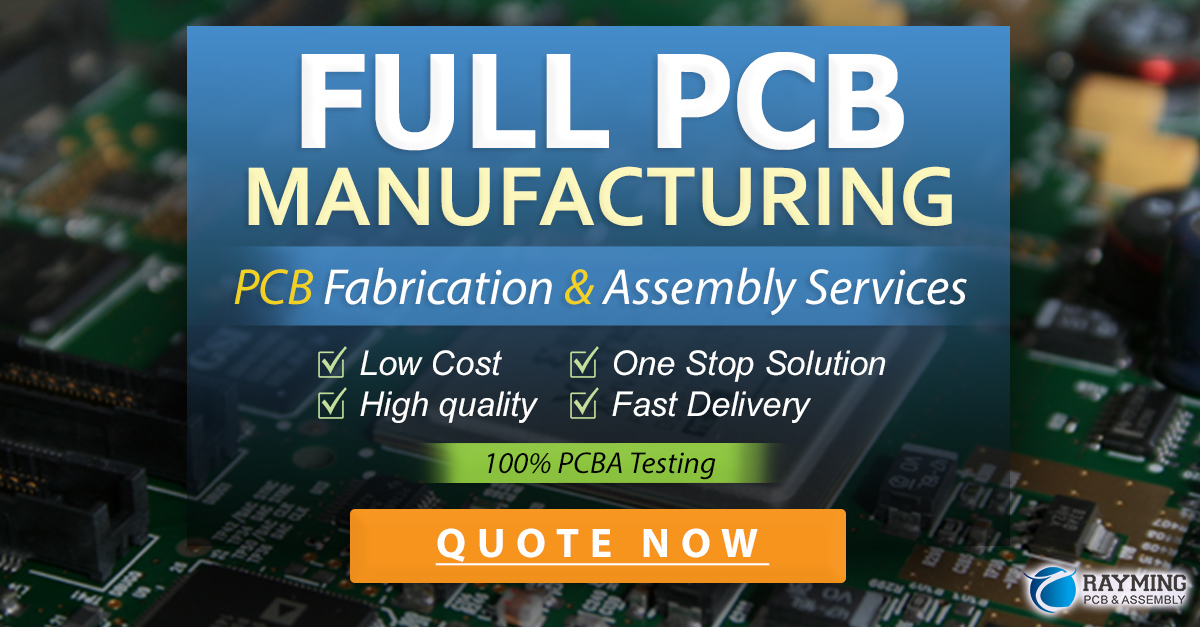
DFM Checklist for PCB Design
To ensure that your PCB design adheres to DFM principles, use the following checklist:
Item | Checked |
---|---|
Components are selected based on availability and manufacturability | ☐ |
Component placement facilitates easy assembly and minimizes defects | ☐ |
Trace widths and spacing meet manufacturer’s guidelines | ☐ |
Via and hole sizes adhere to manufacturer’s recommendations | ☐ |
Solder mask clearance is adequate around pads and vias | ☐ |
Silkscreen labels are clear, legible, and do not overlap critical features | ☐ |
Panelization requirements are considered and optimized | ☐ |
Tooling holes and fiducial marks are included for accurate alignment | ☐ |
Best Practices for Implementing DFM in PCB Design
-
Collaborate with Manufacturing Partners: Engage with your manufacturing partners early in the design process to understand their capabilities, guidelines, and recommendations. This collaboration can help you make informed design decisions and avoid potential issues down the line.
-
Use DFM Software Tools: Leverage DFM software tools that can automatically check your design for potential manufacturability issues and provide suggestions for improvement. These tools can save time and reduce the risk of errors.
-
Conduct Regular Design Reviews: Schedule regular design reviews with your team and stakeholders to discuss DFM considerations, identify potential issues, and make necessary adjustments. This iterative process can help refine your design and ensure compliance with DFM principles.
-
Stay Updated with Industry Standards: Keep abreast of the latest industry standards and guidelines related to PCB design and manufacturing. Regularly review and update your design practices to align with these standards and ensure the manufacturability of your PCBs.
-
Document and Share Knowledge: Create and maintain documentation that captures your DFM guidelines, best practices, and lessons learned. Share this knowledge with your team members and stakeholders to promote a culture of DFM awareness and ensure consistency across projects.
FAQ
1. What is the difference between DFM and DFA in PCB design?
DFM (Design for Manufacturability) focuses on designing PCBs that are easy and cost-effective to manufacture, while DFA (Design for Assembly) focuses on designing PCBs that are easy to assemble. Both principles are important for creating reliable and cost-effective PCBs.
2. How can I ensure that my PCB design is compatible with my manufacturer’s capabilities?
To ensure compatibility, engage with your manufacturer early in the design process. Share your design files, discuss your requirements, and ask for their feedback and recommendations. Regularly communicate with your manufacturer throughout the design process to avoid any surprises or issues during production.
3. What are the most common DFM issues in PCB design?
Common DFM issues include:
– Incorrect component selection or placement
– Insufficient trace width or spacing
– Improper via or hole sizing
– Inadequate solder mask clearance
– Unclear or overlapping silkscreen labels
– Suboptimal panelization or tooling
4. Can implementing DFM principles increase the cost of PCB design?
While implementing DFM principles may require additional time and effort during the design phase, it can ultimately lead to cost savings in the long run. By designing PCBs that are easier to manufacture and assemble, you can reduce production costs, minimize defects, and avoid costly rework or redesigns.
5. How can I balance DFM considerations with the functional requirements of my PCB design?
Balancing DFM considerations with functional requirements requires careful planning and trade-offs. Start by clearly defining your functional requirements and then work with your manufacturing partners to identify DFM guidelines that can be incorporated without compromising functionality. Use simulation tools and prototyping to validate your design choices and make iterative improvements as needed.
Conclusion
Implementing DFM principles in PCB design is essential for creating reliable, cost-effective, and manufacturable products. By considering factors such as component selection, trace routing, via sizing, solder mask clearance, and panelization, designers can optimize their PCBs for the manufacturing process and avoid potential issues.
To successfully implement DFM, collaborate with your manufacturing partners, use DFM software tools, conduct regular design reviews, stay updated with industry standards, and document and share your knowledge. By embracing DFM as an integral part of your PCB design process, you can enhance the quality of your products, reduce costs, and accelerate time-to-market.
Leave a Reply