Introduction to PCB Color
Printed Circuit Boards (PCBs) are an essential component in modern electronics. They provide a platform for mounting and connecting electronic components, allowing for the creation of complex circuits in a compact and efficient manner. One aspect of PCB design that is often overlooked is the color of the board itself. While it may seem like a purely aesthetic choice, the color of a PCB can actually have significant implications for its functionality, manufacturability, and overall performance.
In this article, we will explore the various aspects of PCB color, including the available options, their properties, and how to select the appropriate color for your specific application. We will also discuss the impact of color on PCB manufacturing, assembly, and testing processes.
Understanding the Basics of PCB Color
What is PCB Color?
PCB color refers to the color of the solder mask, which is a protective layer applied to the copper traces on a PCB. The solder mask serves several purposes, including:
- Protecting the copper traces from oxidation and corrosion
- Preventing accidental short circuits during soldering
- Providing electrical insulation between adjacent traces
- Improving the aesthetics of the PCB
The color of the solder mask is determined by the pigments used in its formulation. These pigments can be organic or inorganic, and they are selected based on their ability to withstand the harsh conditions encountered during PCB manufacturing and use.
Common PCB Colors
There are several standard colors available for PCB solder masks, each with its own unique properties and applications. The most common PCB colors include:
-
Green: The most widely used PCB color, green solder mask is a popular choice due to its excellent contrast with white silkscreen and its ability to hide copper traces.
-
Black: Black PCBs offer a sleek and modern appearance, making them popular for consumer electronics and high-end products. They also provide good contrast with white silkscreen and can help reduce light reflection in optical applications.
-
Red: Red PCBs are often used in aerospace and military applications due to their ability to withstand high temperatures and their resistance to moisture absorption.
-
Blue: Blue PCBs are becoming increasingly popular in consumer electronics, as they offer a unique aesthetic appeal and good contrast with white silkscreen.
-
Yellow: Yellow PCBs are less common but can be used in applications where high visibility is required, such as in warning labels or indicators.
-
White: White PCBs are often used in LED lighting applications, as they can help reflect and distribute light more efficiently.
Color | Properties | Common Applications |
---|---|---|
Green | Excellent contrast with white silkscreen, hides copper traces | General-purpose electronics |
Black | Sleek appearance, good contrast, reduces light reflection | Consumer electronics, optical applications |
Red | High temperature resistance, moisture resistance | Aerospace, military |
Blue | Unique aesthetic appeal, good contrast | Consumer electronics |
Yellow | High visibility | Warning labels, indicators |
White | Light reflection and distribution | LED lighting |
Factors to Consider When Selecting PCB Color
When choosing the color for your PCB, there are several factors to consider, each of which can impact the performance, manufacturability, and cost of your board.
Functionality
The primary consideration when selecting PCB color should be the functionality of your circuit. Different colors have different properties that can affect the performance of your PCB, such as:
-
Thermal properties: Some colors, such as red, have better heat dissipation properties, making them suitable for high-temperature applications.
-
Optical properties: If your PCB will be used in an optical application, such as a camera or scanner, you may need to choose a color that minimizes light reflection, such as black.
-
Electrical properties: The color of the solder mask can affect the dielectric constant and loss tangent of the PCB, which can impact signal integrity and high-frequency performance.
Manufacturability
The color of your PCB can also impact its manufacturability, particularly in terms of the ease of inspection and testing. Some colors, such as green and blue, provide good contrast with copper traces, making it easier to visually inspect the board for defects. Other colors, such as black and red, may require more advanced inspection techniques, such as automated optical inspection (AOI) or X-ray inspection.
Cost
The cost of your PCB can also be affected by the color you choose. Some colors, such as green and black, are more commonly used and therefore may be less expensive than others, such as red or yellow. Additionally, some colors may require special handling or processing during manufacturing, which can increase the overall cost of your PCB.
Aesthetics
While functionality and manufacturability should be the primary considerations when selecting PCB color, aesthetics can also play a role, particularly in consumer electronics or other products where visual appeal is important. Choosing a color that complements the overall design of your product can enhance its perceived value and marketability.
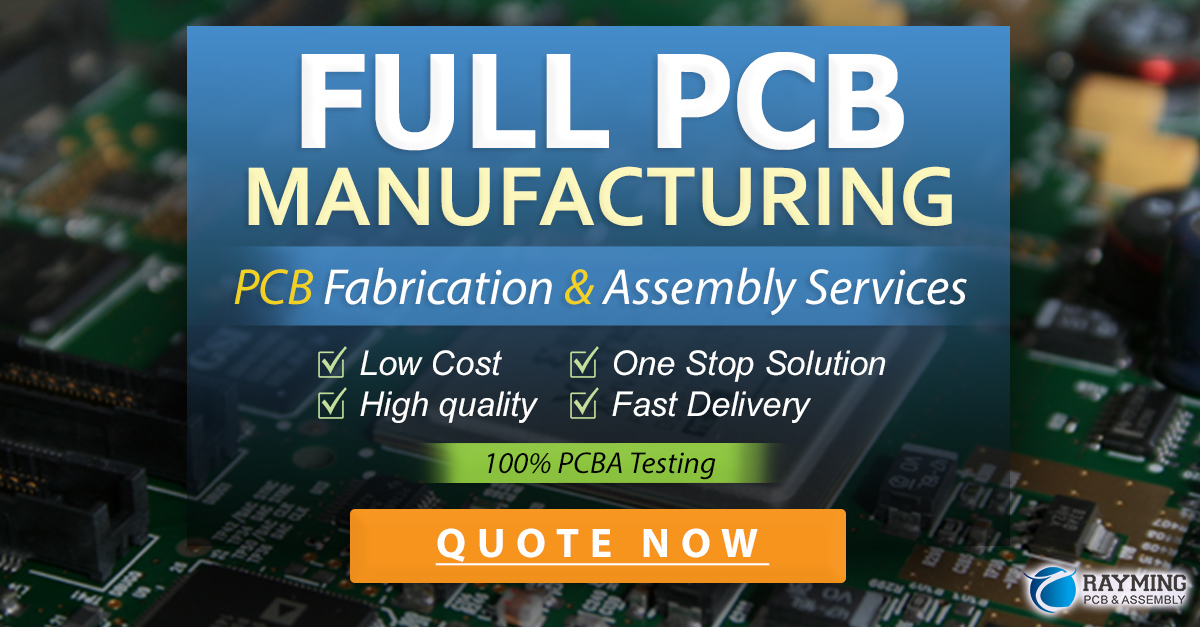
PCB Color and Manufacturing Processes
The color of your PCB can impact various aspects of the manufacturing process, from the selection of materials to the inspection and testing procedures.
Solder Mask Application
The solder mask is typically applied to the PCB using a silkscreen printing process. The color of the solder mask can affect the viscosity and flow properties of the ink, which can impact the thickness and uniformity of the coating. Some colors, such as white and yellow, may require multiple layers of ink to achieve adequate coverage, which can increase the complexity and cost of the manufacturing process.
Inspection and Testing
As mentioned earlier, the color of your PCB can impact the ease of inspection and testing. Green and blue PCBs provide good contrast with copper traces, making it easier to visually inspect the board for defects such as shorts, opens, and misaligned components. Black and red PCBs may require more advanced inspection techniques, such as AOI or X-ray, which can increase the cost and time required for testing.
Soldering
The color of the solder mask can also impact the soldering process. Some colors, such as black and red, may absorb more heat during soldering, which can cause the solder mask to degrade or discolor. This can affect the reliability and longevity of the solder joints, particularly in high-temperature applications.
Selecting the Right PCB Color for Your Application
When selecting the color for your PCB, it’s important to consider all of the factors discussed above and weigh them against the specific requirements of your application. Here are some general guidelines to help you choose the right color:
-
For general-purpose electronics, green is often the best choice due to its excellent contrast with white silkscreen and its ability to hide copper traces.
-
For consumer electronics or other products where aesthetics are important, black or blue may be preferred for their sleek appearance and visual appeal.
-
For high-temperature or moisture-sensitive applications, red may be the best choice due to its thermal and moisture resistance properties.
-
For optical applications or those where light reflection must be minimized, black may be the most suitable option.
-
For applications where high visibility is required, such as warning labels or indicators, yellow may be the best choice.
Ultimately, the right PCB color for your application will depend on a careful consideration of your specific requirements and constraints. By understanding the properties and implications of different colors, you can make an informed decision that balances functionality, manufacturability, cost, and aesthetics.
Frequently Asked Questions (FAQ)
-
Q: Can I mix different colors on the same PCB?
A: Yes, it is possible to use multiple colors on a single PCB, such as using different colors for the top and bottom layers or for different regions of the board. However, this can increase the complexity and cost of the manufacturing process. -
Q: Are there any limitations on the colors available for PCBs?
A: While there are several standard colors available, such as green, black, red, blue, yellow, and white, it is possible to create custom colors by mixing different pigments. However, custom colors may be more expensive and may require additional testing to ensure compatibility with the manufacturing process. -
Q: How does PCB color affect the assembly process?
A: The color of the PCB can impact the ease of component placement and soldering. Some colors, such as green and blue, provide good contrast with components, making it easier to visually inspect the placement. Other colors, such as black and red, may require more advanced inspection techniques to ensure accurate placement. -
Q: Can the color of the PCB affect its long-term reliability?
A: Yes, the color of the PCB can impact its long-term reliability, particularly in harsh environments. Some colors, such as red, have better thermal and moisture resistance properties, making them more suitable for high-temperature or humid environments. Other colors, such as white, may be more susceptible to discoloration or degradation over time. -
Q: Are there any industry standards or regulations governing PCB color?
A: While there are no specific industry standards or regulations governing PCB color, there are some general guidelines and best practices. For example, in the aerospace and defense industries, red is often preferred due to its thermal and moisture resistance properties. In the medical industry, white may be preferred for its ability to reflect light and its clean appearance.
Conclusion
PCB color is an important consideration in the design and manufacturing of electronic circuits. While often overlooked, the color of the solder mask can have significant implications for the functionality, manufacturability, and overall performance of a PCB. By understanding the properties and implications of different colors, and by carefully considering the specific requirements of your application, you can select the right PCB color to ensure optimal performance, reliability, and cost-effectiveness.
Leave a Reply