Introduction to PCB Coils
A PCB (Printed Circuit Board) coil, also known as a planar inductor, is an essential component in many electronic devices. It is a type of inductor that is constructed directly on a printed circuit board, using the copper traces as the coil windings. PCB coils are widely used in various applications, such as power electronics, radio frequency (RF) circuits, and wireless charging systems.
In this comprehensive article, we will delve into the world of PCB coils, exploring their fundamental principles, design considerations, and construction techniques. Whether you are an electronics enthusiast, a student, or a professional engineer, this guide will provide you with a solid understanding of PCB coils and equip you with the knowledge to construct your own.
Understanding the Basics of PCB Coils
What is an Inductor?
An inductor is a passive electronic component that stores energy in the form of a magnetic field when an electric current flows through it. It consists of a coil of wire or a conductive material wound around a core, which can be air, ferrite, or other magnetic materials. Inductors are characterized by their inductance, which is measured in henries (H).
Inductance and Its Importance
Inductance is a measure of an inductor’s ability to store energy in its magnetic field. It is determined by several factors, including the number of turns in the coil, the cross-sectional area of the coil, and the permeability of the core material. The higher the inductance, the more energy the inductor can store.
Inductors play a crucial role in various electronic circuits, such as:
-
Filters: Inductors are used in conjunction with capacitors to create low-pass, high-pass, and band-pass filters, which help to remove unwanted frequencies from a signal.
-
Resonant Circuits: Inductors form resonant circuits with capacitors, allowing for frequency selectivity and oscillation.
-
Energy Storage: Inductors can store energy in their magnetic field and release it when needed, making them useful in power supply circuits and voltage regulators.
Advantages of PCB Coils
PCB coils offer several advantages over traditional wire-wound inductors:
-
Space Savings: PCB coils are flat and can be integrated directly onto the printed circuit board, saving valuable space in compact electronic devices.
-
Cost-Effective: Constructing PCB coils using the existing copper traces on a PCB eliminates the need for additional components and reduces manufacturing costs.
-
Repeatability: PCB coils can be easily replicated using standard PCB manufacturing processes, ensuring consistent performance across multiple boards.
-
Customization: PCB coils can be designed to meet specific inductance and frequency requirements, allowing for greater flexibility in circuit design.
Designing PCB Coils
Key Parameters
When designing a PCB coil, several key parameters need to be considered:
-
Inductance: The desired inductance value determines the number of turns, trace width, and spacing between turns.
-
Frequency: The operating frequency of the circuit influences the coil’s dimensions and the choice of core material, if any.
-
Current: The maximum current flowing through the coil affects the trace width and the coil’s power handling capability.
-
Quality Factor (Q): The quality factor represents the coil’s efficiency and is influenced by the trace resistance and any losses in the core material.
Coil Geometry
PCB coils can be designed in various geometries, each with its own characteristics and advantages:
-
Spiral Coil: The most common type of PCB coil, consisting of a spiral pattern of copper traces. Spiral coils offer high inductance values in a compact footprint.
-
Square Coil: A variation of the spiral coil, using square turns instead of circular ones. Square coils have slightly lower inductance compared to spiral coils but are easier to route on a PCB.
-
Toroidal Coil: A coil wound around a toroidal core, which can be made of ferrite or other magnetic materials. Toroidal coils provide high inductance and excellent magnetic field containment.
-
Solenoid Coil: A cylindrical coil with turns wound along the length of the PCB. Solenoid coils are suitable for applications requiring a strong magnetic field in a specific direction.
Calculating Inductance
To calculate the inductance of a PCB coil, several formulas can be used depending on the coil geometry. For a simple spiral coil, the following formula provides a good approximation:
L = (μ₀ × N² × d) / (2 × D)
Where:
– L is the inductance in henries (H)
– μ₀ is the permeability of free space (4π × 10⁻⁷ H/m)
– N is the number of turns
– d is the average diameter of the coil (m)
– D is the outer diameter of the coil (m)
For more accurate results and complex geometries, specialized software tools and finite element analysis (FEA) can be employed.
Simulation and Optimization
Before constructing a PCB coil, it is essential to simulate and optimize its performance using electronic design automation (EDA) tools. These tools allow designers to:
- Model the coil geometry and materials
- Analyze the coil’s inductance, resistance, and quality factor
- Evaluate the coil’s frequency response and electromagnetic interference (EMI)
- Optimize the coil design for specific performance criteria
Popular EDA tools for PCB coil design include:
- Altium Designer
- Cadence Allegro
- Mentor Graphics PADS
- KiCad
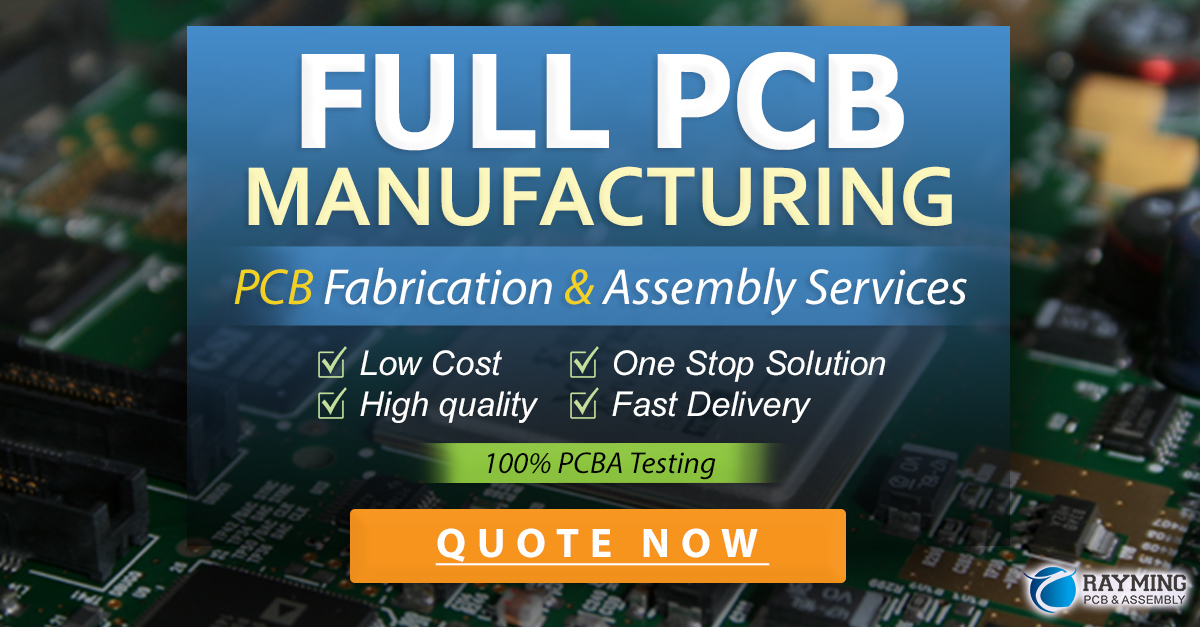
Constructing PCB Coils
PCB Material Selection
The choice of PCB material plays a crucial role in the performance of PCB coils. The most common PCB materials are:
-
FR-4: A glass-reinforced epoxy laminate, widely used for general-purpose PCBs. FR-4 has good mechanical and electrical properties but may have higher losses at high frequencies.
-
Rogers: High-frequency laminates, such as Rogers RO4000 series, offer excellent electrical properties and low dielectric losses, making them suitable for RF applications.
-
Alumina: Ceramic substrates, like alumina, provide superior thermal conductivity and low dielectric losses, ideal for high-power and high-frequency applications.
Copper Thickness and Trace Width
The thickness of the copper layer and the width of the traces determine the coil’s resistance and current-carrying capacity. Thicker copper and wider traces result in lower resistance and higher current handling but may increase the coil’s size and cost.
Typical copper thicknesses for PCB coils range from 1 oz (35 μm) to 4 oz (140 μm), with 1 oz being the most common. Trace widths can vary depending on the coil geometry and the desired inductance, but a minimum width of 0.2 mm is recommended for reliable manufacturing.
Multilayer Coils
For higher inductance values or more compact designs, multilayer PCB coils can be employed. In a multilayer coil, the turns are split across multiple layers of the PCB, connected through vias. This approach allows for a higher number of turns in a given area, increasing the inductance.
When designing multilayer coils, it is essential to consider the layer stackup and the spacing between layers to minimize parasitic capacitance and ensure proper performance.
Manufacturing Process
The construction of PCB coils follows the standard PCB manufacturing process:
-
Design: The coil layout is created using EDA software, adhering to the design guidelines and constraints.
-
Fabrication: The PCB is manufactured using techniques such as etching, drilling, and plating. The copper traces forming the coil are created during this stage.
-
Assembly: If required, additional components, such as capacitors or connectors, are soldered onto the PCB.
-
Testing: The PCB coil is tested for inductance, resistance, and other relevant parameters to ensure it meets the specified requirements.
Applications of PCB Coils
PCB coils find applications in a wide range of electronic devices and systems:
-
Wireless Charging: PCB coils are used as the transmitting and receiving coils in wireless charging systems for smartphones, wearables, and other devices.
-
Radio Frequency (RF) Circuits: PCB coils are employed in RF filters, matching networks, and antennas for wireless communication devices.
-
Power Electronics: PCB coils are used in switching power supplies, DC-DC converters, and voltage regulators for efficient power management.
-
Sensors: PCB coils can be used as sensing elements in proximity sensors, metal detectors, and position encoders.
-
Electromagnetic Interference (EMI) Suppression: PCB coils can be designed to act as EMI filters, reducing electromagnetic noise in electronic systems.
Troubleshooting and Common Issues
When working with PCB coils, several common issues may arise:
-
Inaccurate Inductance: If the measured inductance differs significantly from the designed value, possible causes include incorrect coil dimensions, manufacturing tolerances, or the presence of nearby conductive materials.
-
High Resistance: Excessive coil resistance can be caused by thin copper traces, narrow trace widths, or poor-quality PCB materials. Increasing the copper thickness or trace width can help reduce resistance.
-
Electromagnetic Interference (EMI): PCB coils can generate or pick up EMI, causing noise and signal integrity issues. Proper shielding, grounding, and layout techniques can mitigate EMI problems.
-
Overheating: If the coil is subjected to high currents or operates at high frequencies, it may overheat due to copper losses and dielectric losses. Adequate cooling measures, such as heatsinks or forced air cooling, may be necessary.
Future Trends and Advancements
The field of PCB coils is continually evolving, driven by the demand for smaller, more efficient, and high-performance electronic devices. Some of the future trends and advancements include:
-
3D Printing: The use of 3D printing technologies, such as selective laser sintering (SLS) or fused deposition modeling (FDM), to create PCB coils with complex geometries and embedded components.
-
High-Frequency Materials: The development of advanced PCB materials with low dielectric losses and stable properties at high frequencies, enabling the design of high-performance PCB coils for 5G and beyond.
-
Integrated Passive Components: The integration of PCB coils with other passive components, such as capacitors and resistors, to create compact and multifunctional modules.
-
Wireless Power Transfer: The continued advancement of PCB coil designs for efficient and long-range wireless power transfer, enabling the charging of devices over greater distances.
FAQ
- What is the difference between a PCB coil and a wire-wound inductor?
A PCB coil is constructed directly on a printed circuit board using copper traces, while a wire-wound inductor is made by winding a wire around a core. PCB coils offer space savings, cost-effectiveness, and ease of manufacturing compared to wire-wound inductors.
- Can I design a PCB coil with any inductance value?
While PCB coils can be designed to achieve a wide range of inductance values, there are practical limitations based on the available PCB space, copper thickness, and manufacturing capabilities. Very high inductance values may require specialized techniques or larger PCB sizes.
- How do I choose the right PCB material for my coil?
The choice of PCB material depends on the operating frequency, power handling requirements, and environmental conditions. For general-purpose applications, FR-4 is a common choice. For high-frequency or RF applications, low-loss materials like Rogers laminates are preferred. Alumina substrates are suitable for high-power and high-temperature applications.
- What is the maximum current a PCB coil can handle?
The maximum current a PCB coil can handle depends on the copper thickness, trace width, and the coil’s ability to dissipate heat. Thicker copper and wider traces can handle higher currents. It is essential to consider the coil’s power dissipation and provide adequate cooling to prevent overheating and damage.
- Can PCB coils be used for wireless charging?
Yes, PCB coils are widely used in wireless charging applications. They serve as the transmitting and receiving coils in inductive power transfer systems, enabling the charging of devices such as smartphones, wearables, and other electronics without the need for physical connectors.
Conclusion
PCB coils are essential components in modern electronic devices, offering a compact, cost-effective, and customizable solution for inductor design. By understanding the basics of PCB coils, their design considerations, and construction techniques, engineers and enthusiasts can harness their potential in a wide range of applications.
From wireless charging to RF circuits and power electronics, PCB coils play a crucial role in enabling efficient and reliable operation. As technology continues to advance, the demand for innovative PCB coil designs will only grow, driving the development of new materials, manufacturing processes, and applications.
By mastering the art of PCB coil design and construction, you can unlock new possibilities in your electronic projects and contribute to the ever-evolving world of electronics.
Comparison of PCB Coil Types
Coil Type | Inductance | Size | Ease of Manufacturing |
---|---|---|---|
Spiral Coil | High | Compact | Easy |
Square Coil | Moderate | Compact | Easy |
Toroidal Coil | High | Larger | Moderate |
Solenoid Coil | Moderate to High | Larger | Moderate |
Common PCB Materials for Coils
Material | Dielectric Constant | Loss Tangent | Thermal Conductivity (W/mK) |
---|---|---|---|
FR-4 | 4.3 – 4.7 | 0.02 | 0.3 |
Rogers RO4003C | 3.38 | 0.0027 | 0.64 |
Alumina | 9.8 | 0.0001 | 30 |
Leave a Reply