Introduction to PCB Assembly
Printed Circuit Board (PCB) assembly is the process of soldering or mounting electronic components onto a printed circuit board. It is a crucial step in the manufacturing of electronic devices, as it determines the functionality, reliability, and quality of the final product. PCB assembly services have become increasingly important in today’s fast-paced and technology-driven world, where electronic devices are ubiquitous and essential in various industries such as consumer electronics, automotive, aerospace, medical, and telecommunications.
One-stop PCB assembly services refer to a comprehensive solution that covers all aspects of the PCB assembly process, from design and prototyping to fabrication, component sourcing, assembly, testing, and even packaging and shipping. These services are provided by specialized companies that have the expertise, equipment, and resources to handle the entire PCB assembly workflow efficiently and cost-effectively.
Benefits of One-stop PCB Assembly Services
1. Time and Cost Savings
One of the primary advantages of using one-stop PCB assembly services is the potential for significant time and cost savings. By outsourcing the entire PCB assembly process to a single provider, companies can eliminate the need to coordinate with multiple vendors and suppliers, which can be time-consuming and costly. One-stop services also allow for better coordination and communication between the different stages of the assembly process, reducing the risk of errors and delays.
Moreover, one-stop PCB assembly providers often have established relationships with component suppliers and can negotiate better prices due to their large volume orders. They can also optimize the assembly process through automated equipment and lean manufacturing techniques, resulting in faster turnaround times and lower production costs.
2. Expertise and Quality Assurance
Another benefit of using one-stop PCB assembly services is access to specialized expertise and quality assurance. PCB assembly requires a high level of technical knowledge and skill, as well as strict adherence to industry standards and regulations. One-stop service providers typically have a team of experienced engineers, technicians, and quality control specialists who are well-versed in the latest PCB assembly technologies and best practices.
These experts can provide valuable guidance and support throughout the assembly process, from design optimization and component selection to testing and inspection. They can also implement rigorous quality control measures, such as automated optical inspection (AOI), X-ray inspection, and functional testing, to ensure that the assembled PCBs meet the required specifications and performance criteria.
3. Scalability and Flexibility
One-stop PCB assembly services also offer scalability and flexibility to accommodate different production volumes and requirements. Whether a company needs a small batch of prototypes or a large-scale production run, one-stop service providers can adapt their processes and resources accordingly. They can also handle a wide range of PCB types and complexities, from simple single-layer boards to complex multi-layer boards with high-density interconnects.
Furthermore, one-stop PCB assembly providers can offer flexibility in terms of customization and value-added services. They can work closely with their clients to understand their specific needs and preferences, and provide tailored solutions such as custom packaging, labeling, and shipping options. Some providers also offer additional services such as PCB design, component kitting, and inventory management to further streamline the assembly process.
Key Considerations for Choosing a One-stop PCB Assembly Provider
1. Technical Capabilities and Equipment
When selecting a one-stop PCB assembly provider, it is important to evaluate their technical capabilities and equipment. The provider should have state-of-the-art facilities and equipment that can handle the specific requirements of the project, such as:
- Surface mount technology (SMT) lines for placing and soldering small components
- Through-hole technology (THT) lines for placing and soldering larger components
- Automated optical inspection (AOI) machines for detecting assembly defects
- X-ray inspection machines for inspecting hidden solder joints and connections
- Functional testing equipment for verifying the electrical and mechanical performance of the assembled PCBs
The provider should also have experience and expertise in assembling the specific type of PCBs required, whether they are rigid, flexible, or rigid-flex boards, and whether they involve special materials or components such as high-frequency laminates or ball grid arrays (BGAs).
Assembly Technology | Equipment | Capabilities |
---|---|---|
SMT | Pick-and-place machines, reflow ovens, wave soldering machines | Placing and soldering small components (resistors, capacitors, ICs) |
THT | Insertion machines, wave soldering machines, selective soldering machines | Placing and soldering larger components (connectors, switches, through-hole ICs) |
AOI | 2D or 3D optical inspection machines | Detecting assembly defects (missing/misaligned components, solder bridges, insufficient solder) |
X-ray | 2D or 3D X-ray inspection machines | Inspecting hidden solder joints and connections, detecting voids and cracks |
Functional Testing | In-circuit testers, flying probe testers, boundary scan testers | Verifying electrical and mechanical performance, detecting functional defects |
2. Quality Management System
Another key consideration is the provider’s quality management system (QMS). A robust QMS ensures that the PCB assembly process is consistently controlled and monitored, and that the assembled PCBs meet the required quality standards. The provider should have a well-documented QMS that includes:
- Quality policies and objectives
- Procedures and work instructions for each stage of the assembly process
- Inspection and testing plans and criteria
- Calibration and maintenance schedules for equipment
- Training and certification programs for personnel
- Corrective and preventive action procedures for addressing quality issues
Ideally, the provider should be certified to relevant quality management standards such as ISO 9001 (general QMS), ISO 13485 (medical devices), or AS9100 (aerospace). These certifications demonstrate the provider’s commitment to quality and continuous improvement, and provide assurance to clients that their PCBs will be assembled in accordance with industry best practices.
3. Supply Chain Management
Effective supply chain management is critical for ensuring the timely and cost-effective delivery of PCB assembly services. The one-stop provider should have a reliable and diversified network of component suppliers and distributors, as well as a robust system for managing inventory, lead times, and obsolescence risks.
The provider should also have experience and capabilities in sourcing hard-to-find or custom components, as well as managing the logistics of importing and exporting components and assembled PCBs across different regions and regulations. They should be able to provide real-time visibility and traceability of the supply chain, as well as proactively communicate any potential issues or delays to their clients.
Supply Chain Aspect | Best Practices |
---|---|
Supplier Selection | – Diversify supplier base to mitigate risks – Evaluate supplier performance and quality regularly – Establish long-term partnerships with key suppliers |
Inventory Management | – Implement just-in-time (JIT) or kanban system to minimize inventory costs – Use electronic data interchange (EDI) or web portals to share inventory data with suppliers – Monitor inventory levels and aging to avoid shortages or obsolescence |
Lead Time Management | – Collaborate with suppliers to optimize lead times and delivery schedules – Use expediting and safety stock strategies for critical components – Monitor and report lead time performance and variability |
Logistics Management | – Optimize shipping routes and modes to balance cost and speed – Use international commercial terms (Incoterms) to clarify responsibilities and risks – Comply with import/export regulations and documentation requirements |
4. Customer Service and Support
Finally, the level of customer service and support provided by the one-stop PCB assembly provider is an important factor to consider. The provider should have a dedicated team of account managers, project managers, and technical support specialists who can provide prompt and professional assistance throughout the assembly process and beyond.
The provider should have clear and transparent communication channels, such as email, phone, or web portals, for receiving and responding to customer inquiries, requests, and feedback. They should also have a formal process for handling customer complaints and escalations, as well as for measuring and reporting customer satisfaction.
In addition, the provider should offer value-added services and support that can help their clients optimize their PCB designs, reduce their costs, and improve their time-to-market. These services may include:
- Design for manufacturability (DFM) analysis and recommendations
- Bill of materials (BOM) optimization and component substitution
- Prototype and pre-production sampling and testing
- Failure analysis and root cause investigation
- Warranty and repair services
- Technical training and documentation
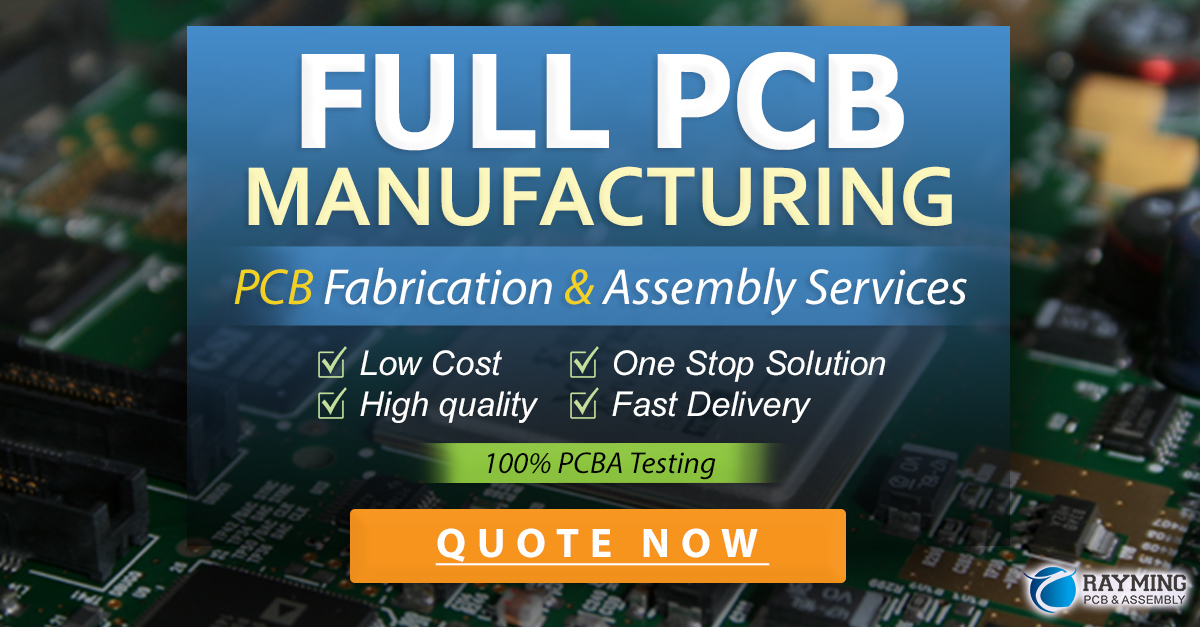
Conclusion
In conclusion, one-stop PCB assembly services provide a comprehensive and convenient solution for companies that need to outsource their PCB assembly needs. By leveraging the expertise, equipment, and resources of a single provider, companies can achieve significant time and cost savings, as well as improve the quality and reliability of their assembled PCBs.
However, selecting the right one-stop PCB assembly provider requires careful consideration of their technical capabilities, quality management system, supply chain management, and customer service and support. Companies should conduct thorough due diligence and evaluation of potential providers, and establish clear expectations and agreements regarding the scope, timeline, and deliverables of the assembly project.
By partnering with a reputable and experienced one-stop PCB assembly provider, companies can focus on their core competencies and innovation, while entrusting the critical task of PCB assembly to experts who can deliver high-quality and cost-effective results.
Frequently Asked Questions (FAQ)
1. What is the typical turnaround time for one-stop PCB assembly services?
The turnaround time for one-stop PCB assembly services varies depending on the complexity and volume of the project, as well as the specific provider’s capabilities and workload. In general, prototype or low-volume assembly can be completed within 1-2 weeks, while high-volume production may take 4-8 weeks or longer. However, some providers offer expedited services for urgent projects, with turnaround times as short as 24-48 hours.
2. What is the minimum order quantity (MOQ) for one-stop PCB assembly services?
The minimum order quantity (MOQ) for one-stop PCB assembly services also varies depending on the provider and the specific project requirements. Some providers may have no MOQ and can accommodate prototype or small-batch assembly, while others may require a minimum of 100 or 1,000 units per order. In general, higher MOQs may be required for projects that involve custom components, specialized equipment, or complex assembly processes.
3. What types of PCBs can be assembled using one-stop services?
One-stop PCB assembly services can typically handle a wide range of PCB types and technologies, including:
- Single-layer and double-layer PCBs
- Multi-layer PCBs (4, 6, 8, or more layers)
- High-density interconnect (HDI) PCBs
- Flexible and rigid-flex PCBs
- Metal core PCBs
- High-frequency and RF PCBs
- LED and MCPCB (metal core printed circuit board) PCBs
However, some providers may specialize in certain types of PCBs or have more experience and capabilities in specific industries or applications, such as automotive, aerospace, or medical devices.
4. How much do one-stop PCB assembly services cost?
The cost of one-stop PCB assembly services depends on various factors, such as:
- PCB complexity and layer count
- Component types and quantities
- Assembly technology and equipment required
- Order volume and repeatability
- Quality and testing requirements
- Shipping and logistics
In general, higher complexity, lower volume, and more stringent quality requirements will result in higher assembly costs. However, one-stop services can often provide more competitive pricing than using multiple providers, due to their economies of scale and streamlined processes. Many providers also offer online quoting tools or cost calculators to help estimate the assembly cost based on the specific project parameters.
5. How can I ensure the quality and reliability of the assembled PCBs?
To ensure the quality and reliability of the assembled PCBs, it is important to work closely with the one-stop PCB assembly provider and establish clear quality requirements and expectations from the outset. This may involve:
- Providing detailed and accurate design files, bill of materials, and assembly instructions
- Specifying the relevant industry standards and certifications (e.g., IPC, UL, RoHS)
- Defining the inspection and testing criteria and methods (e.g., AOI, X-ray, functional testing)
- Requesting first article inspection (FAI) or pre-production samples for approval
- Conducting regular audits and reviews of the provider’s quality management system and performance
- Establishing a robust feedback and corrective action process for addressing any quality issues
In addition, it is recommended to choose a provider that has a proven track record of quality and reliability, as evidenced by their certifications, references, and customer testimonials. Some providers may also offer warranties or guarantees for their assembled PCBs, which can provide additional assurance and protection for the customer.
Leave a Reply