Introduction to PCB Architectures
Printed Circuit Boards (PCBs) are the backbone of modern electronics, providing a platform for interconnecting electronic components and enabling complex circuitry in a compact form factor. As technology advances and the demand for smaller, faster, and more powerful devices increases, PCB architectures must evolve to keep pace. High-density PCB construction is a critical aspect of this evolution, enabling the creation of smaller, more complex boards with improved performance and reliability.
What is High Density PCB Construction?
High-density PCB construction refers to the design and manufacturing techniques used to create PCBs with a high component density and fine feature sizes. This involves the use of advanced materials, manufacturing processes, and design tools to create boards with smaller trace widths, tighter spacing, and more layers than traditional PCBs.
Benefits of High Density PCB Construction
High-density PCB construction offers several benefits over traditional PCB design and manufacturing:
- Smaller form factor: High-density PCBs can accommodate more components in a smaller space, enabling the creation of smaller, more compact devices.
- Improved performance: With smaller trace widths and tighter spacing, high-density PCBs can achieve higher signal speeds and reduced noise and interference.
- Increased reliability: Advanced manufacturing processes and materials used in high-density PCB construction can improve the reliability and durability of the final product.
- Cost reduction: Although the initial design and manufacturing costs may be higher, high-density PCBs can ultimately lead to cost savings by reducing the overall size and complexity of the device.
Advanced PCB Architectures
To meet the demands of high-density PCB construction, several advanced PCB architectures have emerged. These architectures employ innovative design techniques and materials to push the boundaries of what is possible with PCB technology.
HDI (High Density Interconnect) PCBs
HDI PCBs are designed with fine lines and spaces, small vias, and high layer counts to achieve a high component density. They typically feature:
- Trace widths and spaces of 3 mil (75 μm) or less
- Microvias with diameters of 6 mil (150 μm) or less
- Multiple layers (8 or more) with thin dielectrics
HDI PCBs are commonly used in smartphones, tablets, and other compact electronic devices that require high functionality in a small form factor.
Rigid-Flex PCBs
Rigid-flex PCBs combine rigid and flexible substrates in a single board, allowing for three-dimensional packaging and improved reliability in applications with limited space or requiring movement. They offer several advantages:
- Reduced size and weight compared to separate rigid and flexible boards
- Improved reliability by eliminating connectors between rigid and flexible sections
- Enhanced design flexibility for complex, space-constrained applications
Rigid-flex PCBs are often used in aerospace, military, and medical devices where reliability and space savings are critical.
Embedded Component PCBs
Embedded component PCBs incorporate passive components, such as resistors and capacitors, directly into the PCB substrate. This is achieved by placing the components into cavities within the board and laminating them with the other layers. Embedded component PCBs offer several benefits:
- Reduced board size and thickness
- Improved electrical performance by reducing parasitic inductance and capacitance
- Enhanced reliability by eliminating solder joints
Embedded component PCBs are used in applications requiring high component density and improved electrical performance, such as high-speed digital systems and RF circuits.
Design Considerations for High Density PCBs
Designing high-density PCBs requires careful consideration of several factors to ensure optimal performance, reliability, and manufacturability.
Signal Integrity
As trace widths and spaces decrease and signal speeds increase, maintaining signal integrity becomes increasingly challenging. Designers must consider factors such as impedance control, crosstalk, and electromagnetic interference (EMI) when routing high-speed signals. Techniques such as differential pair routing, ground planes, and proper termination can help mitigate these issues.
Thermal Management
With higher component density comes increased heat generation, which can lead to reliability issues if not properly managed. Designers must consider the thermal characteristics of components and materials, as well as the use of thermal vias, heat sinks, and other cooling methods to ensure adequate heat dissipation.
DFM (Design for Manufacturability)
High-density PCBs require advanced manufacturing processes and tight tolerances, making DFM a critical consideration. Designers must work closely with manufacturers to ensure that their designs are compatible with the available manufacturing capabilities and can be produced reliably and cost-effectively. This may involve adjusting trace widths, via sizes, and other design parameters to meet manufacturing constraints.
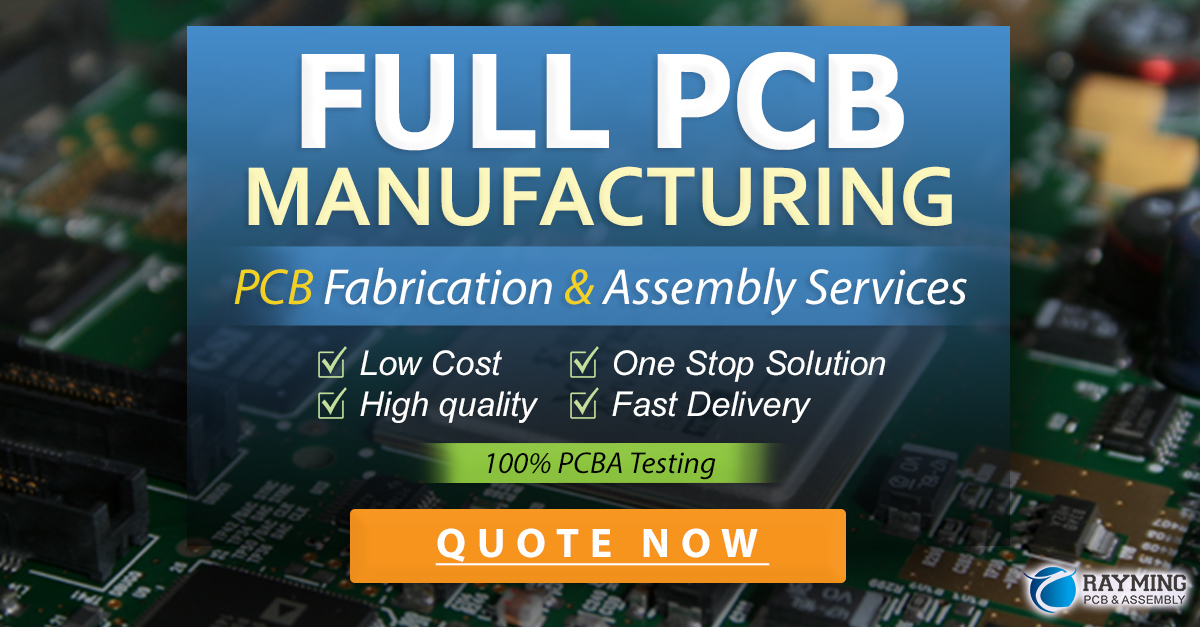
Manufacturing Processes for High Density PCBs
To achieve the fine feature sizes and tight tolerances required for high-density PCBs, advanced manufacturing processes are essential.
HDI Manufacturing
HDI PCBs are typically manufactured using a combination of standard and advanced processes, such as:
- Laser drilling for small, precise microvias
- Semi-additive process (SAP) for fine line patterning
- Thin film dielectrics for reduced layer thickness
- Copper filled microvias for improved thermal and electrical performance
These processes enable the creation of HDI PCBs with trace widths and spaces down to 1-2 mil (25-50 μm) and via diameters of 4-6 mil (100-150 μm).
Rigid-Flex Manufacturing
Rigid-flex PCBs are manufactured using a combination of rigid and flexible substrates, typically polyimide or polyester-based materials. The manufacturing process involves:
- Creating the rigid and flexible sub-laminates separately
- Laminating the sub-laminates together using adhesive layers
- Drilling and plating through-holes to interconnect the layers
- Patterning and etching the copper layers to create the circuit
Special care must be taken to ensure proper alignment and bonding of the rigid and flexible sections to avoid delamination and other reliability issues.
Embedded Component Manufacturing
Embedded component PCBs are manufactured using a process similar to standard PCBs, with the addition of component embedding steps:
- Creating cavities in the PCB substrate for the embedded components
- Placing the components into the cavities and securing them with adhesive
- Laminating the layers together to embed the components
- Drilling and plating vias to interconnect the layers and components
- Patterning and etching the copper layers to create the circuit
Proper design and process control are critical to ensure the reliability and performance of embedded component PCBs.
Future Trends in PCB Architectures
As electronic devices continue to evolve and new technologies emerge, PCB architectures must adapt to meet new challenges and opportunities.
3D PCBs
3D PCBs take the concept of multi-layer boards to the next level by stacking and interconnecting multiple PCBs in a three-dimensional package. This allows for even greater component density and design flexibility, enabling the creation of highly integrated, compact devices. Challenges include thermal management, signal integrity, and manufacturing complexity.
Optical PCBs
Optical PCBs use optical waveguides instead of copper traces to transmit signals between components. This offers several potential advantages, such as higher bandwidth, reduced EMI, and lower power consumption. However, significant challenges remain in the manufacturing and integration of optical components into PCBs.
Flexible and Stretchable PCBs
Flexible and stretchable PCBs are designed to bend, twist, and stretch without losing functionality. This enables new applications in wearable electronics, medical devices, and soft robotics. Key challenges include materials selection, reliability, and manufacturing processes for these unconventional substrates.
Frequently Asked Questions
1. What is the difference between HDI and standard PCBs?
HDI PCBs have finer trace widths and spaces, smaller vias, and higher layer counts compared to standard PCBs. This allows for higher component density and improved electrical performance, but also requires more advanced manufacturing processes and design considerations.
2. Can rigid-flex PCBs be used in all applications?
Rigid-flex PCBs are best suited for applications that require a combination of rigid and flexible sections, such as devices with moving parts or space-constrained packaging. They may not be necessary or cost-effective for simpler, static applications.
3. What are the main challenges in designing high-density PCBs?
The main challenges in designing high-density PCBs include maintaining signal integrity, managing thermal dissipation, and ensuring manufacturability. Designers must carefully consider factors such as trace routing, impedance control, thermal management, and DFM to create reliable, high-performance boards.
4. How do embedded components differ from surface-mounted components?
Embedded components are placed inside the PCB substrate, while surface-mounted components are attached to the surface of the board. Embedded components offer advantages such as reduced board size and improved electrical performance, but require specialized manufacturing processes and design considerations.
5. What is the future outlook for PCB architectures?
The future of PCB architectures is likely to involve continued miniaturization, increased integration of advanced technologies (such as 3D packaging and optical interconnects), and the development of new materials and manufacturing processes to enable novel applications in wearable electronics, IoT devices, and beyond. However, these advancements will also bring new challenges in design, manufacturing, and reliability that will need to be addressed.
Conclusion
High-density PCB construction and advanced PCB architectures are essential for meeting the demands of modern electronic devices. By pushing the boundaries of trace widths, via sizes, and layer counts, these technologies enable the creation of smaller, faster, and more reliable products. However, they also introduce new challenges in design, manufacturing, and reliability that require careful consideration and collaboration between designers, manufacturers, and end-users.
As new technologies and applications emerge, PCB architectures will continue to evolve, incorporating novel materials, processes, and design techniques. From HDI and rigid-flex to embedded components and beyond, the future of PCBs is full of exciting possibilities and challenges. By staying at the forefront of these developments, designers and manufacturers can create the next generation of electronic devices that will shape our world.
PCB Architecture | Key Features | Typical Applications |
---|---|---|
HDI | – Fine traces and spaces (≤3 mil) – Small microvias (≤6 mil) – High layer count (≥8) |
– Smartphones – Tablets – Wearables |
Rigid-Flex | – Combination of rigid and flexible substrates – 3D packaging – Improved reliability |
– Aerospace – Military – Medical devices |
Embedded Component | – Passive components embedded in PCB substrate – Reduced board size and thickness – Improved electrical performance |
– High-speed digital systems – RF circuits – Miniaturized devices |
Leave a Reply