Overview of the MPU9250 sensor
The MPU9250 sensor is a product of InvenSense, a leading company in the MEMS sensor industry. This sensor integrates three distinct sensing elements into a single package, offering a compact and efficient solution for motion tracking.
Key Features of the MPU9250
- 9-Axis Sensing: The MPU9250 combines a 3-axis gyroscope, a 3-axis accelerometer, and a 3-axis magnetometer, providing a complete set of data for accurate motion tracking.
- High Performance: The sensor offers high sensitivity, low noise, and excellent stability, ensuring precise and reliable measurements.
- Digital Output: The sensor communicates with the host system using a digital interface, such as I2C or SPI, simplifying integration and data processing.
- Low Power Consumption: The MPU9250 is designed for low power consumption, making it suitable for battery-powered applications.
- Compact Size: The sensor comes in a small package, measuring only 3mm x 3mm x 1mm, allowing for easy integration into space-constrained devices.
Gyroscope
The gyroscope in the MPU9250 measures angular velocity, which is the rate of change of the sensor’s orientation. It provides data about the rotation of the sensor along the X, Y, and Z axes, commonly referred to as roll, pitch, and yaw.
Gyroscope Specifications
Parameter | Value |
---|---|
Range | ±250, ±500, ±1000, ±2000 °/s |
Sensitivity | 131 LSB/(°/s) |
Noise Performance | 0.1 °/s-rms |
Output Data Rate | 4 Hz to 8 kHz |
Accelerometer
The accelerometer in the MPU9250 measures linear acceleration, which includes both the acceleration due to motion and the acceleration due to gravity. It provides data about the sensor’s acceleration along the X, Y, and Z axes.
Accelerometer Specifications
Parameter | Value |
---|---|
Range | ±2g, ±4g, ±8g, ±16g |
Sensitivity | 16,384 LSB/g |
Noise Performance | 300 µg/√Hz |
Output Data Rate | 4 Hz to 4 kHz |
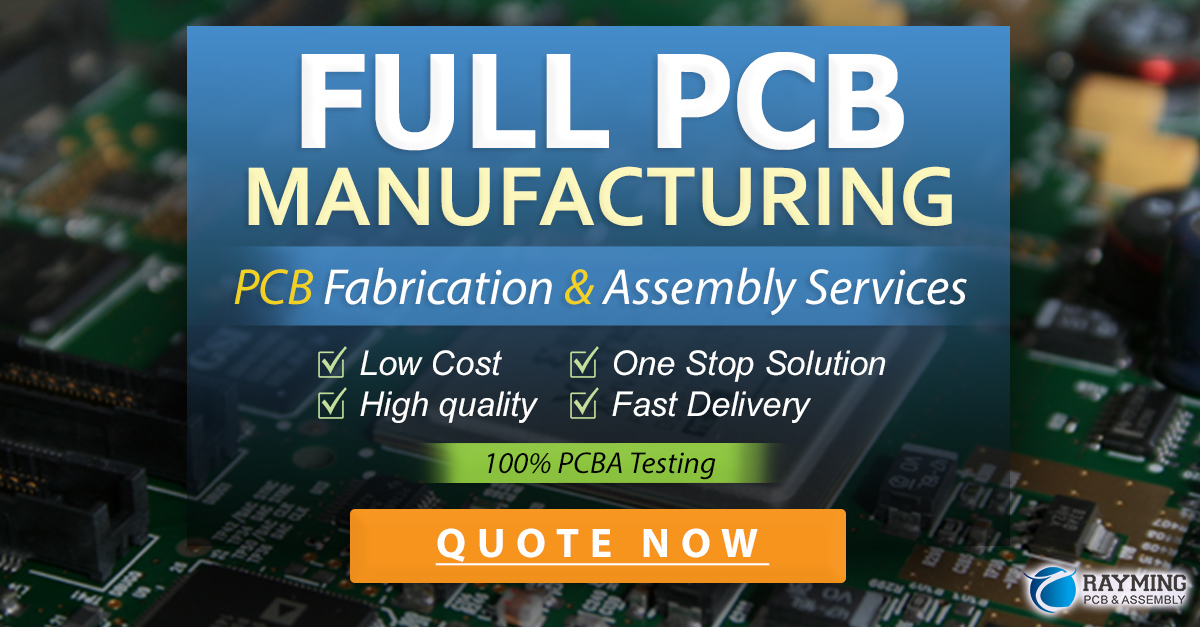
Magnetometer
The magnetometer in the MPU9250 measures the strength and direction of the Earth’s magnetic field. It provides data about the sensor’s orientation relative to the Earth’s magnetic north, which can be used for compass applications and to compensate for gyroscope drift.
Magnetometer Specifications
Parameter | Value |
---|---|
Range | ±4800 µT |
Sensitivity | 0.6 µT/LSB |
Noise Performance | 0.3 µT-rms |
Output Data Rate | 8 Hz to 100 Hz |
Sensor Fusion and Data Processing
To obtain meaningful motion tracking information from the MPU9250, the data from the gyroscope, accelerometer, and magnetometer must be combined and processed using sensor fusion algorithms. These algorithms, such as the Kalman filter or the Madgwick algorithm, estimate the sensor’s orientation by fusing the data from the three sensors and compensating for their individual limitations.
Sensor Fusion Algorithms
- Kalman Filter: The Kalman filter is a recursive algorithm that estimates the state of a system based on noisy measurements. It is widely used for sensor fusion in motion tracking applications.
- Madgwick Algorithm: The Madgwick algorithm is a computationally efficient orientation estimation algorithm that uses quaternions to represent the sensor’s orientation. It is well-suited for resource-constrained embedded systems.
- Mahony Filter: The Mahony filter is another popular orientation estimation algorithm that uses proportional-integral (PI) feedback control to correct for gyroscope drift using accelerometer and magnetometer measurements.
Data Processing Steps
- Calibration: Before using the MPU9250 for motion tracking, the sensor must be calibrated to compensate for offsets, scale factors, and misalignment errors. Calibration involves measuring the sensor’s output in known orientations and calculating the necessary correction factors.
- Preprocessing: The raw sensor data may need to be preprocessed to remove noise, outliers, and other artifacts. Common preprocessing techniques include low-pass filtering, median filtering, and outlier removal.
- Sensor Fusion: The preprocessed data from the gyroscope, accelerometer, and magnetometer is fused using a sensor fusion algorithm to estimate the sensor’s orientation. The choice of the algorithm depends on the specific application requirements, such as accuracy, computational complexity, and real-time performance.
- Post-processing: The estimated orientation may require further post-processing to obtain the desired output format, such as Euler angles (roll, pitch, yaw) or a rotation matrix. Additionally, the orientation data may be combined with other information, such as position or velocity, to provide a complete motion tracking solution.
Applications of the MPU9250 Sensor
The MPU9250 sensor finds applications in a wide range of domains, including:
- Robotics: The MPU9250 is commonly used in robotics for orientation estimation, stability control, and navigation. It enables robots to maintain balance, avoid obstacles, and perform precise movements.
- Wearable Devices: The small size and low power consumption of the MPU9250 make it suitable for wearable devices, such as fitness trackers, smartwatches, and virtual reality headsets. It allows these devices to track the user’s motion and orientation for various applications, such as activity monitoring, gesture recognition, and immersive experiences.
- Gaming: The MPU9250 is used in gaming controllers, such as motion-sensing joysticks and VR controllers, to provide intuitive and realistic user interaction. It enables precise tracking of the controller’s orientation and motion, enhancing the gaming experience.
- Virtual Reality and Augmented Reality: The MPU9250 is a key component in VR and AR systems, enabling accurate tracking of the user’s head orientation and motion. It allows for immersive and realistic experiences by synchronizing the virtual environment with the user’s movements.
- Drones and UAVs: The MPU9250 is used in drones and unmanned aerial vehicles (UAVs) for orientation estimation, stabilization, and navigation. It enables drones to maintain stable flight, perform autonomous maneuvers, and navigate in complex environments.
- Automotive: The MPU9250 finds applications in automotive systems, such as electronic stability control, rollover detection, and inertial navigation. It helps improve vehicle safety, handling, and performance by providing accurate motion and orientation data.
Interfacing the MPU9250 with Microcontrollers
To utilize the MPU9250 sensor in a project, it needs to be interfaced with a microcontroller or a processing unit. The sensor communicates using a digital interface, typically I2C or SPI, which allows for easy integration with various microcontroller platforms.
I2C Interface
The MPU9250 supports I2C communication, which is a two-wire serial interface. The I2C interface consists of two lines: SCL (Serial Clock) and SDA (Serial Data). Multiple devices can be connected to the same I2C bus, with each device having a unique address.
To interface the MPU9250 with a microcontroller using I2C, the following steps are typically involved:
- Connect the SCL and SDA lines of the MPU9250 to the corresponding SCL and SDA pins of the microcontroller.
- Connect the VCC and GND pins of the MPU9250 to the power supply and ground of the microcontroller, respectively.
- Configure the microcontroller’s I2C peripheral to communicate with the MPU9250 using its default I2C address (0x68 or 0x69, depending on the state of the AD0 pin).
- Initialize the MPU9250 by writing appropriate configuration values to its registers using I2C commands.
- Read the sensor data from the MPU9250 registers using I2C commands and process the data as required.
SPI Interface
The MPU9250 also supports SPI communication, which is a four-wire serial interface. The SPI interface consists of four lines: MOSI (Master Out Slave In), MISO (Master In Slave Out), SCK (Serial Clock), and CS (Chip Select).
To interface the MPU9250 with a microcontroller using SPI, the following steps are typically involved:
- Connect the MOSI, MISO, SCK, and CS lines of the MPU9250 to the corresponding SPI pins of the microcontroller.
- Connect the VCC and GND pins of the MPU9250 to the power supply and ground of the microcontroller, respectively.
- Configure the microcontroller’s SPI peripheral to communicate with the MPU9250 using the desired SPI mode and clock speed.
- Initialize the MPU9250 by writing appropriate configuration values to its registers using SPI commands.
- Read the sensor data from the MPU9250 registers using SPI commands and process the data as required.
Example Code
Here’s an example code snippet in C++ for interfacing the MPU9250 with an Arduino board using the I2C interface:
#include <Wire.h>
const int MPU9250_ADDRESS = 0x68; // MPU9250 I2C address
void setup() {
Wire.begin(); // Initialize I2C communication
// Initialize MPU9250
Wire.beginTransmission(MPU9250_ADDRESS);
Wire.write(0x6B); // PWR_MGMT_1 register
Wire.write(0x00); // Set to zero to wake up the MPU9250
Wire.endTransmission(true);
}
void loop() {
// Read accelerometer data
Wire.beginTransmission(MPU9250_ADDRESS);
Wire.write(0x3B); // Starting register for accelerometer data
Wire.endTransmission(false);
Wire.requestFrom(MPU9250_ADDRESS, 6, true); // Read 6 bytes (2 bytes per axis)
int16_t ax = Wire.read() << 8 | Wire.read();
int16_t ay = Wire.read() << 8 | Wire.read();
int16_t az = Wire.read() << 8 | Wire.read();
// Process accelerometer data
// ...
delay(100); // Delay between readings
}
This example code initializes the I2C communication, wakes up the MPU9250, and reads the accelerometer data in a loop. The data can be further processed and used for motion tracking applications.
Challenges and Limitations
While the MPU9250 is a powerful and versatile sensor, there are certain challenges and limitations to consider when using it for motion tracking applications:
- Gyroscope Drift: The gyroscope in the MPU9250 is subject to drift over time, which can lead to cumulative errors in orientation estimation. This drift needs to be compensated for using sensor fusion algorithms that incorporate data from the accelerometer and magnetometer.
- Magnetic Interference: The magnetometer in the MPU9250 is sensitive to magnetic interference from nearby objects, such as metal structures or electronic devices. This interference can cause errors in the heading estimation and needs to be accounted for through calibration and filtering techniques.
- Temperature Sensitivity: The performance of the MPU9250 can be affected by temperature variations. The sensor’s offset and sensitivity may change with temperature, requiring compensation through calibration or real-time temperature correction.
- Integration Errors: When using the gyroscope and accelerometer data for position tracking, small errors in the sensor measurements can accumulate over time, leading to drift in the estimated position. This issue can be mitigated by incorporating additional sensors, such as GPS or visual odometry, to provide absolute position references.
- Limited Bandwidth: The MPU9250 has a limited bandwidth, which means that it may not be able to capture very high-frequency motions accurately. The maximum output data rate of the sensor is limited, and high-frequency vibrations or impacts may not be fully captured.
- Power Consumption: Although the MPU9250 is designed for low power consumption, continuous operation of the sensor can still drain the battery in portable devices. Power management techniques, such as duty cycling or low-power modes, may be necessary to extend battery life.
Frequently Asked Questions (FAQ)
-
What is the difference between the MPU9250 and the MPU6050 sensor?
The MPU9250 is an upgraded version of the MPU6050 sensor. While the MPU6050 only includes a 3-axis gyroscope and a 3-axis accelerometer, the MPU9250 adds a 3-axis magnetometer, providing a complete 9-axis solution for motion tracking. The MPU9250 also offers improved performance and additional features compared to the MPU6050. -
Can the MPU9250 be used for absolute position tracking?
The MPU9250 alone cannot provide absolute position tracking, as it measures angular velocity, acceleration, and magnetic field. To obtain absolute position, the data from the MPU9250 needs to be integrated over time, which can lead to accumulating errors. For accurate position tracking, the MPU9250 is often used in combination with other sensors, such as GPS or visual odometry systems. -
How do I calibrate the MPU9250 sensor?
Calibrating the MPU9250 involves determining the offset, scale factor, and misalignment errors for each sensing axis. This is typically done by measuring the sensor’s output in known orientations and comparing it with the expected values. The calibration process may involve placing the sensor on a level surface, rotating it in different orientations, and applying optimization algorithms to estimate the calibration parameters. -
What is the communication protocol used by the MPU9250?
The MPU9250 supports both I2C and SPI communication protocols. I2C is a two-wire serial interface that allows multiple devices to be connected to the same bus, while SPI is a four-wire serial interface that provides faster data transfer rates. The choice between I2C and SPI depends on the specific application requirements and the available interfaces on the host microcontroller. -
How do I fuse the data from the gyroscope, accelerometer, and magnetometer in the MPU9250?
Fusing the data from the gyroscope, accelerometer, and magnetometer involves using sensor fusion algorithms, such as the Kalman filter, Madgwick algorithm, or Mahony filter. These algorithms combine the sensor measurements in a complementary manner to estimate the sensor’s orientation while compensating for the individual limitations of each sensor. The choice of the sensor fusion algorithm depends on factors such as the desired accuracy, computational complexity, and real-time performance requirements of the application.
Conclusion
The MPU9250 is a powerful and versatile 9-axis MEMS sensor that offers a complete solution for motion tracking applications. With its integrated gyroscope, accelerometer, and magnetometer, the MPU9250 enables accurate and reliable sensing of angular velocity, acceleration, and magnetic field. Its compact size, low power consumption, and digital output make it suitable for a wide range of applications, including robotics, wearable devices, gaming, virtual reality, and more.
To effectively utilize the MPU9250 for motion tracking, it is essential to understand its specifications, interfacing methods, and data processing techniques. Sensor fusion algorithms play a crucial role in combining the data from the three sensing elements to estimate the sensor’s orientation accurately. However, challenges such as gyroscope drift, magnetic interference, and integration errors need to be addressed through appropriate calibration, filtering, and sensor fusion techniques.
By leveraging the capabilities of the MPU9250 and implementing robust data processing algorithms, developers and researchers can create innovative motion tracking solutions that push the boundaries of what is possible in various domains. As MEMS technology continues to advance, sensors like the MPU9250 will play an increasingly important role in enabling new applications and experiences that rely on accurate and reliable motion tracking.
Leave a Reply