Introduction to Microwave PCB Laminates
Microwave PCB laminates are specialized materials designed to meet the unique requirements of high-frequency and high-power applications. These laminates play a crucial role in the fabrication of microwave circuit boards, which are used in various industries, including telecommunications, aerospace, defense, and automotive. The key characteristics of microwave PCB laminates include low dielectric constant (Dk), low dissipation factor (Df), and high thermal stability, which enable the reliable performance of microwave circuits in demanding environments.
The Importance of Low Dielectric Constant and Dissipation Factor
Low dielectric constant and dissipation factor are essential properties for microwave PCB laminates. A low dielectric constant minimizes signal propagation delay and reduces signal attenuation, while a low dissipation factor minimizes signal loss and heat generation. These properties are crucial for maintaining signal integrity and ensuring the efficient operation of microwave circuits.
The dielectric constant of a material is a measure of its ability to store electrical energy, and it is represented by the symbol Dk. The dissipation factor, also known as the loss tangent or tan δ, is a measure of the material’s ability to dissipate electrical energy as heat. The relationship between the dielectric constant and dissipation factor is given by the following equation:
tan δ = ε” / ε’
where:
– ε” is the imaginary part of the complex permittivity, representing the loss factor
– ε’ is the real part of the complex permittivity, representing the dielectric constant
A lower dissipation factor indicates a lower loss of electrical energy and, consequently, better performance in microwave applications.
Thermal Stability and Its Significance
Thermal stability is another critical property of microwave PCB laminates, as it ensures the consistent performance of microwave circuits under varying temperature conditions. Thermally stable laminates maintain their dielectric properties and mechanical integrity over a wide temperature range, minimizing the risk of circuit failure due to thermal stress.
The thermal stability of a laminate is often characterized by its glass transition temperature (Tg) and thermal expansion coefficient (CTE). A high Tg indicates that the material can withstand higher temperatures before its properties begin to degrade, while a low CTE ensures minimal dimensional changes due to temperature fluctuations.
Types of Microwave PCB Laminates
Several types of microwave PCB laminates are available, each with its unique set of properties and advantages. The most common types include:
PTFE (Polytetrafluoroethylene) Laminates
PTFE laminates, also known as Teflon laminates, are widely used in microwave applications due to their excellent dielectric properties and thermal stability. They offer a low dielectric constant (2.0-2.3) and a low dissipation factor (0.0002-0.0008), making them suitable for high-frequency applications. PTFE laminates also have a high thermal stability, with a Tg of around 327°C and a low CTE (50-100 ppm/°C).
Some common PTFE laminates include:
- Rogers RT/duroid® 5870-5880 series
- Rogers RT/duroid® 6002-6202 series
- Taconic TLY, TLY-5, and TLY-HP series
Ceramic-Filled PTFE Laminates
Ceramic-filled PTFE laminates combine the advantages of PTFE with the added benefits of ceramic fillers, such as improved thermal conductivity and mechanical stability. These laminates offer a slightly higher dielectric constant (2.4-3.0) and dissipation factor (0.0010-0.0030) compared to pure PTFE laminates, but they still provide excellent performance in microwave applications.
Examples of ceramic-filled PTFE laminates include:
- Rogers RO3000® series
- Taconic RF-35 and RF-30 series
Hydrocarbon-Based Laminates
Hydrocarbon-based laminates, such as those based on polyphenylene oxide (PPO) or polybutadiene (PBD), offer a lower-cost alternative to PTFE laminates. While their dielectric properties are not as exceptional as those of PTFE laminates, they still provide good performance in many microwave applications. Hydrocarbon-based laminates typically have a dielectric constant of 2.8-3.5 and a dissipation factor of 0.0020-0.0050.
Some examples of hydrocarbon-based laminates include:
- Rogers RO4000® series
- Isola I-Tera® MT series
Comparison of Microwave PCB Laminate Properties
The following table compares the key properties of the main types of microwave PCB laminates:
Laminate Type | Dielectric Constant (Dk) | Dissipation Factor (Df) | Thermal Stability (Tg) | CTE (ppm/°C) |
---|---|---|---|---|
PTFE | 2.0-2.3 | 0.0002-0.0008 | 327°C | 50-100 |
Ceramic-Filled PTFE | 2.4-3.0 | 0.0010-0.0030 | 327°C | 30-60 |
Hydrocarbon-Based | 2.8-3.5 | 0.0020-0.0050 | 150-180°C | 30-60 |
Selecting the Right Microwave PCB Laminate
Choosing the right microwave PCB laminate for a specific application involves considering several factors, including:
- Frequency range: The laminate should have a low dielectric constant and dissipation factor over the desired frequency range.
- Power handling: The laminate should be able to withstand the expected power levels without excessive heating or degradation.
- Thermal requirements: The laminate should have a high Tg and low CTE to ensure thermal stability under the expected operating conditions.
- Mechanical requirements: The laminate should have sufficient mechanical strength and dimensional stability to withstand the manufacturing process and the intended application.
- Cost: The laminate should be cost-effective for the specific application, considering the balance between performance and budget.
By carefully evaluating these factors and consulting with PCB manufacturers and laminate suppliers, designers can select the most suitable microwave PCB laminate for their high-power applications.
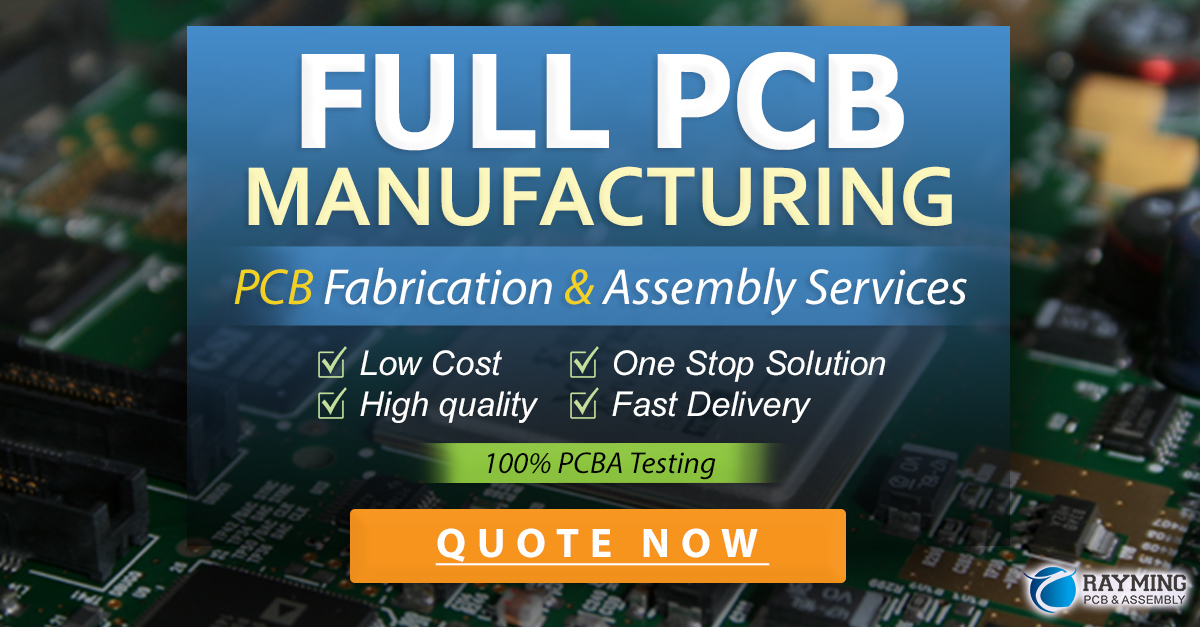
Manufacturing Considerations for Microwave PCB Laminates
When working with microwave PCB laminates, several manufacturing considerations should be taken into account to ensure the best possible performance and reliability of the final product.
Material Handling and Storage
Microwave PCB laminates, particularly PTFE-based materials, require special handling and storage procedures to maintain their properties and prevent contamination. Some key considerations include:
- Storing laminates in a clean, dry, and temperature-controlled environment.
- Handling laminates with clean gloves to avoid contamination from skin oils and dirt.
- Avoiding exposure to UV light, which can degrade the material properties.
- Following the manufacturer’s recommended shelf life and storage conditions.
Fabrication Processes
The fabrication of microwave PCBs using low-loss laminates requires specialized processes and equipment to ensure the best possible results. Some important aspects of the fabrication process include:
- Controlled impedance: Maintaining precise control over the impedance of transmission lines is crucial for microwave PCBs. This requires careful design and fabrication techniques, such as adjusting trace widths and dielectric thicknesses.
- Hole drilling: Microwave PCBs often require high-quality, small-diameter holes for vias and component mounting. Special drilling techniques, such as laser drilling or high-speed mechanical drilling, may be necessary to achieve the required hole quality.
- Plated through-holes (PTHs): The quality of PTHs is critical for microwave PCBs, as poor-quality PTHs can lead to signal reflections and losses. Special plating techniques, such as double-plating or filled-via technology, may be used to improve PTH performance.
- Surface finish: The choice of surface finish can impact the performance of microwave PCBs. Low-loss finishes, such as immersion silver or electroless nickel/immersion gold (ENIG), are often preferred for high-frequency applications.
Testing and Quality Control
Rigorous testing and quality control measures are essential to ensure the performance and reliability of microwave PCBs. Some key aspects of testing and quality control include:
- Visual inspection: Careful visual inspection of the PCB for defects, such as scratches, dents, or contamination, can help identify potential issues before they affect performance.
- Electrical testing: Electrical tests, such as time-domain reflectometry (TDR) and vector network analyzer (VNA) measurements, can verify the impedance, insertion loss, and return loss of the PCB.
- Environmental testing: Exposing the PCB to various environmental conditions, such as temperature cycling, humidity, and vibration, can help assess its reliability and durability.
- Dimensional verification: Measuring the critical dimensions of the PCB, such as trace widths and spacing, can ensure that the fabricated board meets the design specifications.
By carefully considering these manufacturing aspects and working closely with experienced PCB fabricators, designers can ensure that their microwave PCBs meet the desired performance and reliability requirements.
Conclusion
Microwave PCB laminates play a vital role in the performance and reliability of high-power, high-frequency applications. By understanding the key properties of these laminates, such as low dielectric constant, low dissipation factor, and high thermal stability, designers can select the most suitable material for their specific requirements. Additionally, considering the manufacturing aspects, such as material handling, fabrication processes, and testing, can help ensure the best possible results for microwave PCBs.
As the demand for high-performance microwave applications continues to grow, the development of advanced microwave PCB laminates with even better properties and more cost-effective solutions will remain a priority for the industry. By staying up-to-date with the latest advancements in laminate technology and working closely with PCB manufacturers and suppliers, designers can continue to push the boundaries of microwave circuit performance and reliability.
Frequently Asked Questions (FAQ)
- Q: What is the main difference between PTFE and hydrocarbon-based microwave PCB laminates?
A: PTFE laminates offer a lower dielectric constant and dissipation factor compared to hydrocarbon-based laminates, making them more suitable for high-frequency applications. However, hydrocarbon-based laminates are generally more cost-effective and may be sufficient for less demanding microwave applications.
- Q: How does the dielectric constant of a laminate affect the performance of a microwave PCB?
A: A lower dielectric constant results in faster signal propagation and reduced signal attenuation, which is desirable for high-frequency applications. It also allows for the design of transmission lines with wider traces, which can improve power handling and ease of manufacturing.
- Q: What are the main advantages of using ceramic-filled PTFE laminates compared to pure PTFE laminates?
A: Ceramic-filled PTFE laminates offer improved thermal conductivity and mechanical stability compared to pure PTFE laminates. This can help dissipate heat more effectively and reduce the risk of mechanical deformation, especially in high-power applications.
- Q: How can I select the right microwave PCB laminate for my application?
A: To select the right laminate, consider factors such as the frequency range, power handling requirements, thermal and mechanical requirements, and cost. Consult with PCB manufacturers and laminate suppliers to determine the most suitable material for your specific application.
- Q: What special manufacturing considerations should be taken into account when working with microwave PCB laminates?
A: Microwave PCB laminates require careful handling and storage to maintain their properties and prevent contamination. The fabrication process should also take into account factors such as controlled impedance, hole drilling, plated through-holes, and surface finish. Rigorous testing and quality control measures are essential to ensure the performance and reliability of the final product.
Leave a Reply