What is Micro-Sectioning?
Micro-sectioning is the process of cutting a small, representative section from a larger material sample for microscopic examination. The goal is to create a thin, flat, and polished surface that reveals the material’s internal structure and characteristics. This technique is essential for analyzing a wide range of materials, including metals, alloys, ceramics, composites, and even biological specimens.
Applications of Micro-Sectioning
Micro-sectioning is used in various fields for different purposes, such as:
- Materials Science and Engineering:
- Studying the microstructure of materials
- Identifying defects, inclusions, or anomalies
- Evaluating the effects of heat treatment, welding, or other processes
-
Investigating failure mechanisms and conducting failure analysis
-
Metallurgy:
- Examining the grain structure, phase distribution, and segregation in metals and alloys
- Assessing the quality of castings, forgings, or welds
-
Studying the effects of alloying elements, heat treatment, or mechanical processing
-
Quality Control and Failure Analysis:
- Verifying the conformance of materials to specifications
- Investigating the causes of component failures or malfunctions
-
Identifying manufacturing defects or material flaws
-
Research and Development:
- Developing new materials or improving existing ones
- Studying the structure-property relationships of materials
- Evaluating the performance of coatings, surface treatments, or corrosion protection measures
The Micro-Sectioning Process
The micro-sectioning process involves several steps to prepare a sample for microscopic examination. The following is a general outline of the process:
1. Sample Selection and Cutting
The first step is to select a representative sample from the material of interest. The sample should be small enough to fit into the mounting medium and the microscope stage. Typically, a sample size of 10-20 mm in diameter and 5-10 mm in thickness is suitable for most applications.
The sample is then cut using a precision cutting tool, such as a low-speed diamond saw or a wire EDM (Electrical Discharge Machining) machine. The cutting process should minimize damage to the sample and produce a flat surface for further preparation.
2. Mounting
After cutting, the sample is mounted in a suitable medium to provide support and facilitate handling during the subsequent grinding and polishing steps. The most common mounting materials are:
- Cold-setting resins (e.g., epoxy, acrylic)
- Hot-setting resins (e.g., phenolic, diallyl phthalate)
- Low-melting-point alloys (e.g., Wood’s metal, Bi-Sn alloys)
The choice of mounting material depends on the sample properties, the required edge retention, and the compatibility with the etching or staining reagents used for microstructural analysis.
3. Grinding
The mounted sample is then subjected to a series of grinding steps to remove the damage introduced during cutting and to create a flat surface for polishing. Grinding is typically performed using abrasive papers or discs with progressively finer grit sizes, such as:
Grit Size | Abrasive Type |
---|---|
120-240 | Silicon Carbide (SiC) |
320-600 | Silicon Carbide (SiC) |
800-1200 | Silicon Carbide (SiC) |
The sample is ground using water as a lubricant and coolant to minimize heat generation and damage. Between each grinding step, the sample is cleaned and rotated 90° to remove the scratches from the previous step.
4. Polishing
After grinding, the sample is polished to remove the fine scratches and produce a smooth, mirror-like surface suitable for microscopic examination. Polishing is performed using soft cloth pads and abrasive suspensions containing fine particles, such as:
Abrasive | Particle Size |
---|---|
Diamond | 3-6 µm |
Diamond | 1-3 µm |
Alumina (Al2O3) | 0.3-1 µm |
Silica (SiO2) | 0.05-0.1 µm |
The sample is polished using a compatible lubricant, such as water, alcohol, or oil, depending on the abrasive type and the sample properties. The polishing pressure, speed, and time are adjusted to achieve the desired surface finish and to minimize artifacts, such as edge rounding or relief.
5. Etching or Staining
In some cases, the polished sample may require etching or staining to reveal the microstructural features of interest. Etching involves the selective chemical or electrochemical attack of the sample surface to highlight the grain boundaries, phases, or defects. Common etching reagents for metals include:
Material | Etching Reagent |
---|---|
Steels | Nital (HNO3 + Ethanol) |
Stainless Steels | Vilella’s Reagent (HCl + Picric Acid + Ethanol) |
Aluminum Alloys | Keller’s Reagent (HF + HCl + HNO3 + Water) |
Copper Alloys | Ferric Chloride (FeCl3) Solution |
Staining, on the other hand, involves the selective coloration of specific phases or constituents to enhance their contrast under the microscope. Staining techniques are commonly used for polymers, ceramics, and biological samples.
6. Microscopic Examination
The final step is to examine the prepared sample under an optical or electron microscope. The choice of microscope depends on the required magnification, resolution, and depth of field. Optical microscopes are suitable for magnifications up to 1000x, while scanning electron microscopes (SEM) can provide higher magnifications and greater depth of field.
During the microscopic examination, the sample is observed under different lighting conditions (bright field, dark field, polarized light) and magnifications to characterize the microstructural features, such as:
- Grain size and morphology
- Phase distribution and volume fraction
- Inclusions, porosity, or defects
- Surface topography and roughness
The microscopic images are then analyzed and interpreted to derive quantitative or qualitative information about the material’s properties and performance.
Frequently Asked Questions (FAQ)
- What is the purpose of mounting the sample before grinding and polishing?
-
Mounting provides support and protection to the sample during the grinding and polishing steps. It also ensures a uniform and consistent surface finish by minimizing edge rounding and relief.
-
Can micro-sectioning be used for non-metallic materials?
-
Yes, micro-sectioning can be used for a wide range of materials, including polymers, ceramics, composites, and even biological specimens. However, the sample preparation techniques may vary depending on the material properties and the desired analysis.
-
How do I choose the appropriate etching reagent for my sample?
-
The choice of etching reagent depends on the material type, composition, and the microstructural features of interest. Refer to standard metallographic references or consult with experts in the field to select the most suitable etching reagent for your specific application.
-
What are the common artifacts or problems encountered during micro-sectioning?
-
Some common artifacts or problems encountered during micro-sectioning include:
- Edge rounding or relief due to improper mounting or polishing
- Scratches, smearing, or deformation introduced during grinding or polishing
- Contamination or staining from improper cleaning or storage
- Inconsistent or uneven etching due to variations in reagent concentration, temperature, or time
-
Can micro-sectioning be automated for high-throughput sample preparation?
- Yes, there are automated systems available for micro-sectioning that can handle multiple samples simultaneously and provide consistent results. These systems often include features such as programmable grinding and polishing cycles, automatic sample cleaning and drying, and integrated microscopy for rapid analysis.
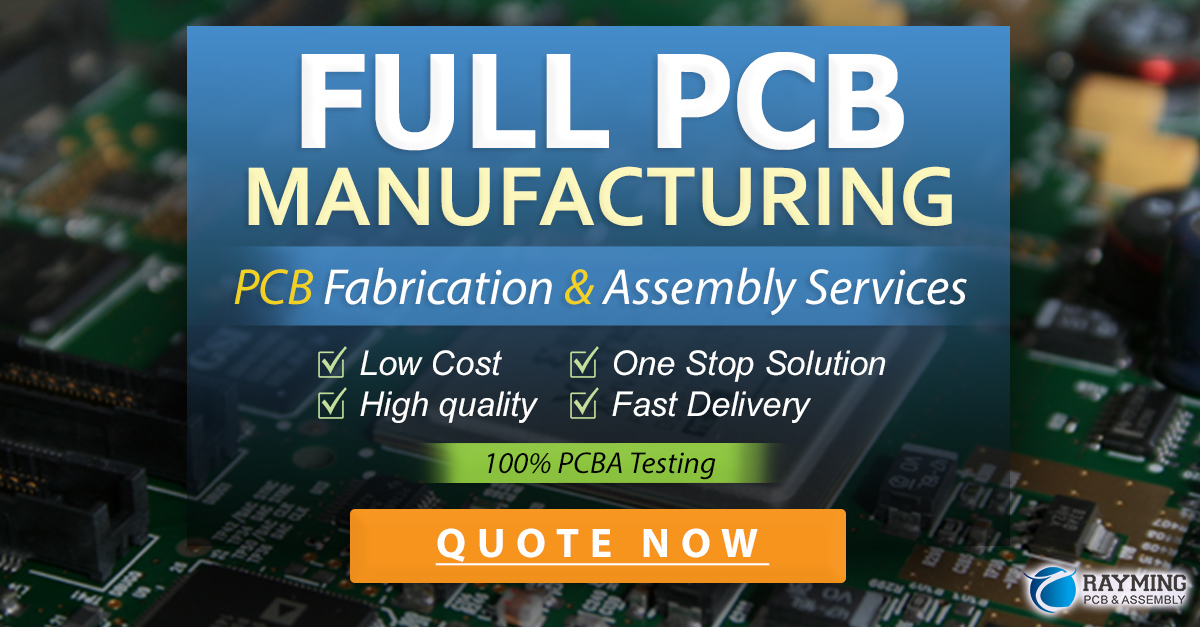
Conclusion
Micro-sectioning is a powerful technique for preparing samples for microscopic examination and analysis. By following a systematic process of cutting, mounting, grinding, polishing, and etching, researchers can obtain high-quality samples that reveal the microstructural features and properties of a wide range of materials. Whether used for materials development, quality control, failure analysis, or research, micro-sectioning remains an essential tool in the field of materials science and engineering.
Leave a Reply