Introduction to PCB Assembly
Printed Circuit Board (PCB) assembly is the process of soldering electronic components onto a PCB to create a functional electronic device. PCB assembly can be done in high volumes for mass production or in low volumes for prototyping, small batch runs, or specialized applications. Low volume PCB assembly refers to the process of assembling a small number of PCBs, typically ranging from a few pieces to a few hundred pieces.
Advantages of Low Volume PCB Assembly
Low volume PCB assembly offers several advantages, including:
- Cost-effective for small batch runs
- Faster turnaround times compared to high volume production
- Flexibility to make design changes and iterations
- Ideal for prototyping and testing new designs
- Suitable for specialized or custom applications
Applications of Low Volume PCB Assembly
Low volume PCB assembly finds applications in various industries and sectors, such as:
- Research and development
- Medical devices
- Aerospace and defense
- Industrial automation
- IoT and wearable devices
- Automotive electronics
- Consumer electronics
PCB Assembly Process
The PCB assembly process consists of several steps, each of which is crucial for ensuring the quality and reliability of the final product.
PCB Design and Fabrication
The first step in the PCB assembly process is designing the PCB layout using specialized software such as Altium Designer, Eagle, or KiCad. The design includes the placement of components, routing of traces, and creation of solder pads. Once the design is finalized, the PCB is fabricated using a combination of chemical etching, drilling, and plating processes.
Component Sourcing and Preparation
The next step is to source the electronic components required for the assembly. This involves selecting the appropriate components based on the design specifications, such as package type, value, and tolerance. The components are then prepared for assembly by packaging them in reels, trays, or tubes, depending on their size and type.
Solder Paste Application
Solder paste, a mixture of tiny solder particles suspended in flux, is applied to the PCB’s solder pads using a stencil or syringe. The solder paste helps to temporarily hold the components in place during the reflow process and forms the electrical and mechanical connection between the components and the PCB.
Component Placement
The components are then placed onto the PCB using pick-and-place machines or manual placement techniques. Pick-and-place machines use vacuum nozzles to pick up components from their packaging and place them accurately on the PCB. Manual placement is often used for low volume assembly or for components that are too large or complex for machine placement.
Reflow Soldering
After component placement, the PCB undergoes reflow soldering, where it is heated in a reflow oven to melt the solder paste and form a permanent connection between the components and the PCB. The reflow process typically follows a temperature profile that gradually heats the PCB to the solder’s melting point, holds it at that temperature for a specified duration, and then cools it down gradually to avoid thermal stress.
Inspection and Testing
Once the reflow process is complete, the PCB undergoes visual inspection and electrical testing to ensure that all the components are properly soldered and functioning as intended. Visual inspection is done using microscopes or automated optical inspection (AOI) systems, while electrical testing is performed using various techniques such as in-circuit testing (ICT), flying probe testing, or functional testing.
Rework and Repair
If any defects or issues are identified during the inspection and testing phase, the PCB may require rework or repair. This involves removing the faulty component, cleaning the solder pads, and resoldering a new component in its place. Rework and repair require skilled technicians and specialized tools to ensure that the PCB is not damaged during the process.
Challenges in Low Volume PCB Assembly
While low volume PCB assembly offers several advantages, it also presents some unique challenges that need to be addressed to ensure a successful outcome.
Component Availability and Lead Times
One of the main challenges in low volume PCB assembly is the availability of components and their lead times. Many electronic components have minimum order quantities (MOQs) that are higher than the requirements for low volume assembly, making it difficult to source them in small quantities. Additionally, some components may have long lead times, which can impact the overall turnaround time for the assembly process.
To mitigate this challenge, it is essential to plan ahead and order components well in advance. Partnering with a reliable component distributor or a PCB assembly service provider with established supply chain relationships can also help in sourcing hard-to-find components.
Design for Manufacturing (DFM)
Design for Manufacturing (DFM) is the practice of designing PCBs in a way that makes them easier and more cost-effective to manufacture. In low volume PCB assembly, DFM is particularly important because the cost per unit is higher compared to high volume production.
Some key DFM considerations for low volume PCB assembly include:
- Choosing components with standard package sizes and pitches
- Avoiding tight tolerances and small feature sizes
- Providing adequate spacing between components for ease of assembly
- Using a single-sided or double-sided PCB design instead of multi-layer PCBs
- Minimizing the number of unique components to reduce inventory and setup costs
Process Control and Quality Assurance
Maintaining process control and quality assurance is another challenge in low volume PCB assembly. Unlike high volume production, where statistical process control (SPC) techniques can be used to monitor and control the process, low volume assembly relies more on manual inspection and testing.
To ensure consistent quality, it is important to have well-defined process standards and work instructions for each step of the assembly process. Operators should be trained on these standards and provided with the necessary tools and equipment to perform their tasks accurately. Regular quality audits and inspections should also be conducted to identify and correct any issues before they impact the final product.
Cost Optimization
Cost optimization is a key consideration in low volume PCB assembly, as the fixed costs of setup and tooling are spread over a smaller number of units. Some strategies for optimizing costs in low volume assembly include:
- Minimizing the number of unique components and using standard components where possible
- Optimizing the PCB layout to reduce the size and complexity of the board
- Using a flexible manufacturing process that can accommodate design changes and iterations without incurring significant setup costs
- Partnering with a PCB assembly service provider that offers competitive pricing and volume discounts
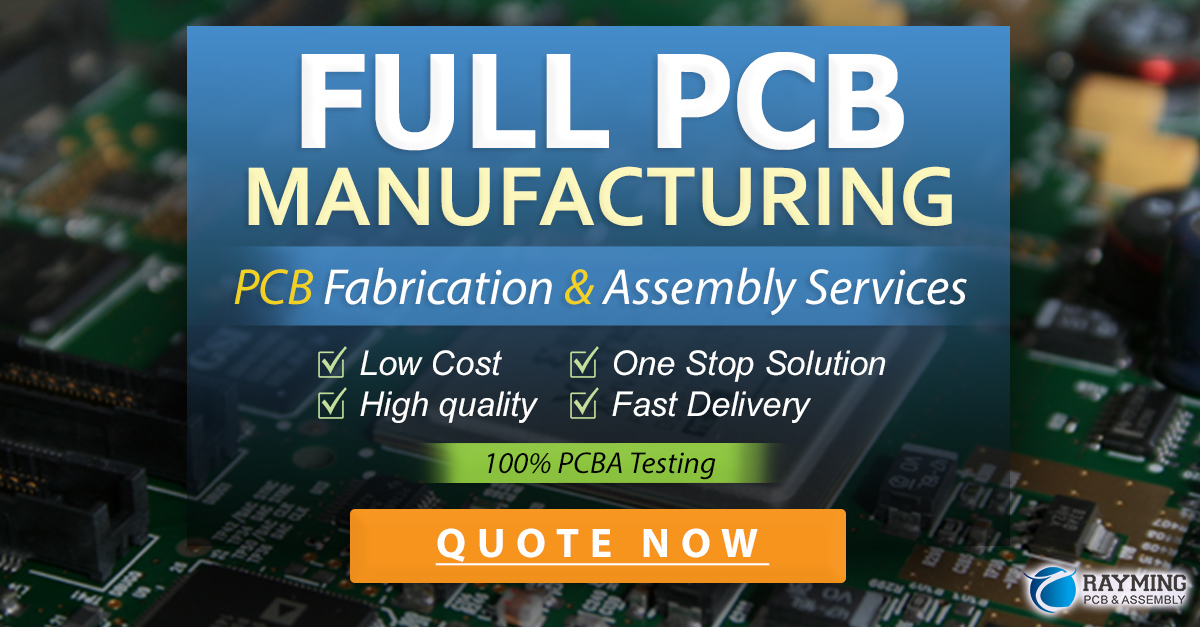
Choosing a Low Volume PCB Assembly Service Provider
Selecting the right PCB assembly service provider is crucial for the success of your low volume assembly project. Here are some factors to consider when choosing a service provider:
Technical Capabilities
The service provider should have the necessary technical capabilities and expertise to handle your specific assembly requirements. This includes experience with the type of components and PCB technology used in your design, as well as the ability to meet your quality and reliability standards.
Manufacturing Capacity and Turnaround Time
The service provider should have sufficient manufacturing capacity to meet your volume requirements and delivery schedule. They should also be able to provide fast turnaround times for prototyping and small batch runs.
Quality Management System
The service provider should have a robust quality management system in place to ensure consistent quality and reliability of the assembled PCBs. This includes documented processes, quality control checkpoints, and traceability of materials and components.
Customer Support and Communication
Good customer support and communication are essential for a successful low volume assembly project. The service provider should have a dedicated project manager or customer support team that can provide regular updates on the status of your project and address any issues or concerns in a timely manner.
Pricing and Value-Added Services
The service provider should offer competitive pricing for low volume assembly while also providing value-added services such as design support, component sourcing, and testing. It is important to get detailed quotes from multiple service providers and compare their pricing and services to find the best fit for your project.
Future Trends in Low Volume PCB Assembly
Low volume PCB assembly is constantly evolving, driven by advances in technology and changing market demands. Here are some future trends to watch out for:
Miniaturization and High-Density Packaging
As electronic devices become smaller and more complex, there is a growing demand for miniaturized PCBs with high-density packaging. This requires advanced assembly techniques such as 3D packaging, chip-on-board (COB), and system-in-package (SiP) that can accommodate a large number of components in a small footprint.
Flexible and Stretchable Electronics
Flexible and stretchable electronics are emerging as a new frontier in PCB technology, enabling the development of wearable devices, medical implants, and soft robotics. These electronics require specialized materials and assembly techniques that can withstand bending, stretching, and twisting without compromising performance.
Sustainable and Eco-Friendly Manufacturing
There is a growing focus on sustainable and eco-friendly manufacturing practices in the electronics industry, driven by consumer demand and regulatory requirements. This includes the use of lead-free solder, biodegradable materials, and energy-efficient manufacturing processes that minimize waste and environmental impact.
Industry 4.0 and Smart Manufacturing
Industry 4.0, also known as the fourth industrial revolution, is transforming the manufacturing landscape with the integration of advanced technologies such as artificial intelligence, robotics, and the Internet of Things (IoT). In low volume PCB assembly, this could lead to the development of smart manufacturing systems that can optimize the assembly process in real-time, reduce errors and defects, and improve overall efficiency.
Conclusion
Low volume PCB assembly is a critical process for bringing new electronic products to market quickly and cost-effectively. By understanding the assembly process, challenges, and best practices, designers and engineers can ensure the success of their low volume assembly projects. Partnering with a reliable PCB assembly service provider with the necessary technical capabilities and expertise is also essential for achieving the desired quality and reliability.
As the electronics industry continues to evolve, low volume PCB assembly will play an increasingly important role in enabling innovation and driving technological progress. By staying up-to-date with the latest trends and technologies in PCB assembly, designers and engineers can position themselves to take advantage of new opportunities and stay ahead of the competition.
FAQs
1. What is the typical turnaround time for low volume PCB assembly?
The turnaround time for low volume PCB assembly can vary depending on the complexity of the design, the availability of components, and the manufacturing process used. Typically, low volume assembly projects can be completed within 1-2 weeks, but some service providers may offer expedited services for faster turnaround times.
2. What is the minimum order quantity (MOQ) for low volume PCB assembly?
The minimum order quantity for low volume PCB assembly can vary depending on the service provider and the specific assembly requirements. Some service providers may offer assembly services for as few as 1-5 pieces, while others may have a minimum order quantity of 50-100 pieces. It is important to discuss your specific volume requirements with the service provider to determine their MOQ and pricing structure.
3. Can I use my own components for low volume PCB assembly?
Yes, most PCB assembly service providers offer consignment services where you can provide your own components for assembly. However, it is important to ensure that the components are properly packaged and labeled and that they meet the required specifications for the assembly process. The service provider may also require additional documentation such as component datasheets and certificates of conformity.
4. What types of testing and inspection services are available for low volume PCB assembly?
PCB assembly service providers offer a range of testing and inspection services to ensure the quality and reliability of the assembled PCBs. These services may include:
- Visual inspection using microscopes or automated optical inspection (AOI) systems
- X-ray inspection to detect hidden defects or voids in solder joints
- In-circuit testing (ICT) to verify the electrical connectivity and functionality of the PCB
- Functional testing to validate the performance of the assembled PCB under real-world conditions
- Environmental testing to ensure the PCB can withstand extreme temperatures, humidity, or vibration
The specific testing and inspection services required will depend on the complexity and criticality of the PCB and the end-use application.
5. How can I ensure the quality and reliability of my low volume PCB assembly?
To ensure the quality and reliability of your low volume PCB assembly, it is important to follow best practices in PCB design, component selection, and manufacturing. This includes:
- Designing the PCB with manufacturability in mind, using standard component sizes and pitches and providing adequate spacing between components
- Selecting high-quality components from reputable suppliers and ensuring they meet the required specifications
- Partnering with a PCB assembly service provider with a proven track record of quality and reliability and a robust quality management system
- Conducting thorough testing and inspection of the assembled PCBs to identify and correct any defects or issues
- Documenting the assembly process and maintaining traceability of materials and components throughout the supply chain
By following these best practices and working closely with your PCB assembly service provider, you can ensure the success of your low volume assembly project and deliver a high-quality product to your customers.
Factor | Consideration |
---|---|
Technical Capabilities | Experience with specific components and PCB technology, ability to meet quality and reliability standards |
Manufacturing Capacity and Turnaround Time | Sufficient capacity to meet volume requirements and delivery schedule, fast turnaround times for prototyping and small batch runs |
Quality Management System | Documented processes, quality control checkpoints, traceability of materials and components |
Customer Support and Communication | Dedicated project manager or customer support team, regular updates on project status, timely resolution of issues |
Pricing and Value-Added Services | Competitive pricing for low volume assembly, value-added services such as design support, component sourcing, and testing |
Table 1: Factors to consider when choosing a low volume PCB assembly service provider.
Leave a Reply