Introduction to LGA packaging
Land Grid Array (LGA) is a surface-mount packaging technology used for integrated circuits (ICs) that offers a reliable and flexible solution for various electronic applications. LGA packages consist of a rectangular or square housing with an array of exposed metal pads on the bottom surface, which directly connect to the printed circuit board (PCB) through a socket or soldering process. This packaging technology has gained popularity due to its advantages over other packaging methods, such as Ball Grid Array (BGA) and Pin Grid Array (PGA).
Advantages of LGA Packaging
- Lower profile: LGA packages have a lower profile compared to other packaging technologies, making them suitable for space-constrained applications.
- Better thermal performance: The exposed metal pads on the bottom surface of the LGA package allow for better heat dissipation, enhancing the thermal performance of the IC.
- Improved electrical performance: LGA packages offer shorter signal paths and reduced inductance, resulting in better electrical performance and higher signal integrity.
- Increased reliability: The absence of fragile pins or balls in LGA packages makes them more resistant to mechanical stress and vibration, improving overall reliability.
- Cost-effective: LGA packages are generally more cost-effective than other packaging technologies due to their simpler manufacturing process and reduced material usage.
LGA Package Structure and Materials
Package Structure
An LGA package typically consists of the following components:
- IC die: The semiconductor chip that contains the integrated circuit.
- Substrate: A thin, multi-layered platform that provides electrical connectivity and mechanical support for the IC die.
- Solder mask: A protective layer applied to the substrate to prevent short circuits and improve solderability.
- Metal pads: Exposed metal contacts on the bottom surface of the package that connect to the PCB.
- Encapsulant: A molding compound that protects the IC die and wire bonds from environmental factors.
Package Materials
The materials used in LGA packages are carefully selected to ensure optimal performance, reliability, and cost-effectiveness. Some common materials include:
- Substrate materials:
- FR-4: A glass-reinforced epoxy laminate material widely used for PCBs and IC package substrates.
- BT (Bismaleimide-Triazine): A high-performance thermoset material with excellent thermal and electrical properties.
- Solder mask materials:
- LPI (Liquid Photoimageable) solder mask: A photosensitive polymer coating that offers high resolution and excellent adhesion.
- Dry film solder mask: A thin, pre-manufactured film that is laminated onto the substrate surface.
- Pad materials:
- Copper (Cu): The most common material for metal pads due to its excellent electrical conductivity and solderability.
- Nickel/Gold (Ni/Au) plating: A surface finish applied to copper pads to improve oxidation resistance and enhance solderability.
- Encapsulant materials:
- Epoxy molding compounds (EMC): Thermosetting polymers filled with silica or other inorganic particles for enhanced mechanical and thermal properties.
LGA Socket and Soldering Technologies
LGA Socket Technology
LGA sockets provide a removable and replaceable interface between the LGA package and the PCB. They consist of a housing with a grid of contacts that mate with the metal pads on the bottom surface of the LGA package. LGA sockets offer several advantages, such as:
- Ease of assembly and disassembly: LGA sockets allow for quick and easy installation and removal of LGA packages without soldering.
- Improved serviceability: Faulty or upgraded ICs can be easily replaced by simply removing the LGA package from the socket.
- Enhanced thermal management: Some LGA sockets incorporate heat spreaders or heat sinks to improve heat dissipation from the IC.
LGA Soldering Technology
When a permanent connection between the LGA package and the PCB is required, soldering is used. The most common soldering methods for LGA packages include:
- Reflow soldering: A process where solder paste is applied to the PCB pads, and the LGA package is placed on top. The assembly is then heated in a reflow oven, melting the solder and forming a permanent connection.
- Wave soldering: A method where the PCB with the LGA package is passed over a molten solder wave, which selectively wets the exposed metal pads and creates a solder joint.
Soldering LGA packages requires careful process control to ensure reliable and consistent solder joints. Factors such as solder paste composition, stencil design, and reflow temperature profile must be optimized for the specific LGA package and PCB design.
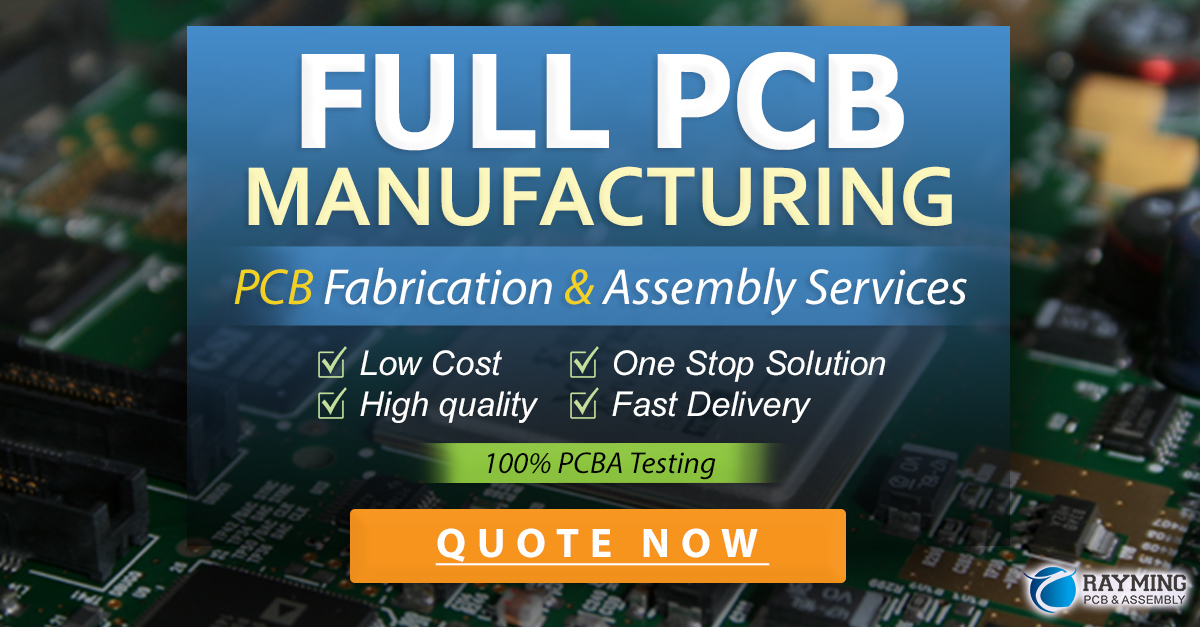
LGA Package Design Considerations
Designing an LGA package involves several key considerations to ensure optimal performance, reliability, and manufacturability. Some of these considerations include:
Pad Layout and Pitch
The layout and pitch of the metal pads on the bottom surface of the LGA package are critical factors in determining the package’s electrical performance and manufacturability. A smaller pitch allows for higher I/O density but may increase manufacturing complexity and cost. The pad layout should also be optimized to minimize signal integrity issues, such as crosstalk and impedance mismatch.
Substrate Design
The substrate design plays a crucial role in the electrical and thermal performance of the LGA package. The number of layers, layer thickness, and material properties must be carefully selected to ensure adequate signal routing, power delivery, and heat dissipation. Additionally, the substrate design should consider the coefficient of thermal expansion (CTE) mismatch between the package and the PCB to minimize stress-induced failures.
Thermal Management
Effective thermal management is essential for LGA packages to ensure reliable operation and long-term durability. The package design should incorporate features that promote efficient heat dissipation, such as:
- Thermal vias: Conductive pathways that transfer heat from the IC die to the metal pads on the bottom surface of the package.
- Heat spreaders: Thin, high-conductivity materials (e.g., copper or aluminum) attached to the top surface of the package to spread heat evenly.
- Thermal interface materials (TIMs): Materials that fill the gaps between the IC die, heat spreader, and heat sink to enhance thermal conductivity.
Electrical Performance
To achieve optimal electrical performance, LGA package designers must consider factors such as:
- Signal integrity: Minimizing signal distortion, crosstalk, and impedance mismatch through proper pad layout, substrate design, and routing techniques.
- Power integrity: Ensuring stable and efficient power delivery to the IC die by optimizing the power distribution network (PDN) and minimizing voltage drop.
- Electromagnetic compatibility (EMC): Reducing electromagnetic interference (EMI) and ensuring compliance with relevant EMC standards through proper grounding, shielding, and filtering techniques.
LGA Package Manufacturing Process
The manufacturing process for LGA packages involves several key steps, including:
- Substrate fabrication: The multi-layered substrate is manufactured using processes such as lamination, drilling, and plating.
- IC die attachment: The semiconductor die is bonded to the substrate using adhesives or soldering techniques.
- Wire bonding: Thin metal wires (e.g., gold or copper) are used to establish electrical connections between the IC die and the substrate.
- Encapsulation: The IC die and wire bonds are protected by a molding compound, which is applied using transfer molding or compression molding techniques.
- Solder mask application: A solder mask layer is applied to the substrate to protect the circuitry and define the metal pad areas.
- Pad finishing: The exposed metal pads are plated with a surface finish (e.g., Ni/Au) to improve solderability and protect against oxidation.
- Singulation: The substrate panel is cut into individual LGA packages using methods such as sawing or laser cutting.
Throughout the manufacturing process, strict quality control measures are implemented to ensure consistent and reliable LGA packages. These measures include visual inspections, electrical testing, and environmental testing (e.g., temperature cycling and humidity exposure) to verify the package’s performance and durability.
Applications of LGA Packaging
LGA packaging technology is widely used in various electronic applications, ranging from consumer devices to industrial and automotive systems. Some notable applications include:
- Mobile devices: LGA packages are commonly used in smartphones, tablets, and wearables for processors, memory, and other ICs due to their low profile and high I/O density.
- Computing: Desktop and laptop computers employ LGA packages for CPUs, GPUs, and chipsets, benefiting from their excellent thermal performance and socket compatibility.
- Automotive electronics: LGA packages are used in automotive applications, such as infotainment systems, advanced driver assistance systems (ADAS), and engine control units (ECUs), thanks to their reliability and resistance to harsh environments.
- Industrial automation: Industrial control systems, sensors, and communication modules often rely on LGA packages for their robustness and ability to withstand extreme temperatures and vibrations.
- Medical devices: LGA packages are used in medical electronics, such as implantable devices and diagnostic equipment, due to their miniaturization capabilities and reliability.
As electronic devices continue to advance in terms of performance, functionality, and miniaturization, LGA packaging technology is expected to evolve and adapt to meet the ever-changing requirements of various industries.
Future Trends in LGA Packaging
The future of LGA packaging technology is driven by the increasing demands for higher performance, greater functionality, and improved reliability in electronic devices. Some key trends shaping the future of LGA packaging include:
- Advanced substrate materials: The development of new substrate materials with better electrical, thermal, and mechanical properties, such as low-loss dielectrics and high-conductivity metals, will enable LGA packages to support higher frequencies and power densities.
- 3D packaging: The integration of multiple ICs in a single LGA package using 3D stacking techniques, such as through-silicon vias (TSVs) and package-on-package (PoP), will allow for greater functionality and miniaturization.
- Heterogeneous integration: The combination of different IC technologies (e.g., digital, analog, and RF) in a single LGA package using advanced packaging techniques, such as fan-out wafer-level packaging (FOWLP) and embedded die packaging, will enable the development of highly integrated and multifunctional systems.
- Improved thermal management: The incorporation of advanced thermal management solutions, such as high-conductivity heat spreaders, advanced TIMs, and integrated heat sinks, will enable LGA packages to dissipate heat more efficiently and support higher power densities.
- Environmentally friendly materials: The adoption of eco-friendly and sustainable materials, such as halogen-free and recyclable substrates and encapsulants, will help reduce the environmental impact of LGA packaging and meet the growing demand for green electronics.
As LGA packaging technology continues to evolve, close collaboration between IC designers, package designers, and manufacturing experts will be essential to overcome challenges and develop innovative solutions that meet the future needs of the electronics industry.
Frequently Asked Questions (FAQ)
- What is the difference between LGA and BGA packaging?
-
LGA (Land Grid Array) packages have exposed metal pads on the bottom surface that directly connect to the PCB, while BGA (Ball Grid Array) packages have an array of solder balls that melt during the reflow process to establish a connection with the PCB. LGA packages generally have a lower profile and better thermal performance compared to BGA packages.
-
Can LGA packages be replaced or reworked?
-
Yes, LGA packages can be replaced or reworked using specialized tools and techniques. When LGA packages are mounted using sockets, they can be easily removed and replaced without soldering. For soldered LGA packages, rework processes such as hot air desoldering or localized heating can be used to remove the package without damaging the PCB.
-
How does the pitch of an LGA package affect its performance?
-
The pitch, or the distance between the centers of adjacent metal pads, affects the electrical performance and manufacturability of an LGA package. A smaller pitch allows for higher I/O density but may increase manufacturing complexity and cost. It also requires more precise alignment during assembly and can impact signal integrity due to increased crosstalk and impedance mismatch.
-
What are the challenges in designing an LGA package?
-
Some of the main challenges in designing an LGA package include optimizing the pad layout and pitch for electrical performance and manufacturability, selecting appropriate substrate materials and layer stack-up for signal and power integrity, managing thermal dissipation to ensure reliable operation, and minimizing stress-induced failures caused by CTE mismatch between the package and PCB.
-
How can the reliability of LGA packages be assessed?
- The reliability of LGA packages can be assessed through various testing methods, such as:
a. Temperature cycling: Exposing the package to alternating high and low temperatures to evaluate its resistance to thermal stress.
b. Humidity testing: Subjecting the package to high humidity conditions to assess its moisture resistance and potential for corrosion.
c. Mechanical shock and vibration testing: Evaluating the package’s ability to withstand sudden impacts and prolonged vibrations.
d. Electrical testing: Verifying the package’s signal integrity, power delivery, and electromagnetic compatibility under various operating conditions.
e. Accelerated life testing: Subjecting the package to elevated stress levels (e.g., higher temperatures or voltages) to predict its long-term reliability under normal operating conditions.
Conclusion
LGA packaging technology has emerged as a reliable and flexible solution for a wide range of electronic applications, offering advantages such as low profile, excellent thermal and electrical performance, and improved reliability compared to other packaging methods. As the demand for high-performance, compact, and cost-effective electronic devices continues to grow, LGA packaging is expected to play a crucial role in meeting the ever-evolving requirements of various industries.
To fully harness the potential of LGA packaging, designers and manufacturers must stay abreast of the latest advancements in materials, technologies, and processes. By collaborating closely and addressing challenges related to electrical performance, thermal management, and reliability, the electronics industry can continue to push the boundaries of what is possible with LGA packaging and develop innovative solutions that shape the future of electronic devices.
Leave a Reply