What is Solder?
Solder is a metal alloy used to create a permanent bond between electronic components and printed circuit boards (PCBs). It is typically composed of two or more metals, such as tin, lead, silver, or copper. The most common types of solder are lead-based and lead-free.
Lead Solder
Lead solder, also known as tin-lead solder, has been the standard in the electronics industry for many years. It typically consists of 60% tin and 40% lead (Sn60/Pb40) or 63% tin and 37% lead (Sn63/Pb37). Lead solder has a relatively low melting point, excellent wetting properties, and good electrical conductivity.
Lead-Free Solder
Lead-free solder, as the name suggests, does not contain lead. Instead, it is composed of various combinations of tin, silver, copper, and other metals. The most common lead-free solder alloys are:
- Tin-Silver-Copper (SAC): Typically contains 95.5% tin, 3.8% silver, and 0.7% copper (SAC305).
- Tin-Copper (SnCu): Contains 99.3% tin and 0.7% copper.
- Tin-Silver (SnAg): Contains 96.5% tin and 3.5% silver.
Lead-free solder was introduced to address the environmental and health concerns associated with lead exposure.
Advantages and Disadvantages of Lead Solder
Advantages
- Lower melting point: Lead solder has a lower melting point compared to most lead-free alternatives, making it easier to work with and reducing the risk of thermal damage to components.
- Better wetting properties: Lead solder has excellent wetting properties, which means it flows and adheres to surfaces more easily, resulting in stronger and more reliable solder joints.
- Low cost: Lead solder is generally less expensive than lead-free alternatives due to its simpler composition and well-established manufacturing processes.
Disadvantages
- Environmental concerns: Lead is a toxic substance that can harm the environment if not disposed of properly. When lead solder ends up in landfills, it can leach into the soil and groundwater, causing contamination.
- Health risks: Exposure to lead can have serious health consequences, particularly for children and pregnant women. Lead exposure can cause developmental delays, learning difficulties, and other neurological problems.
- Regulatory restrictions: Many countries have implemented regulations restricting the use of lead in electronics, such as the European Union’s Restriction of Hazardous Substances (RoHS) directive.
Advantages and Disadvantages of Lead-Free Solder
Advantages
- Environmental friendliness: Lead-free solder eliminates the environmental concerns associated with lead, as it does not pose the same risks of contamination and toxicity.
- Compliance with regulations: Using lead-free solder ensures compliance with international regulations, such as RoHS, which is essential for companies selling products in regulated markets.
- Improved mechanical strength: Some lead-free solder alloys, particularly those containing silver, have higher mechanical strength compared to lead solder, resulting in more durable solder joints.
Disadvantages
- Higher melting point: Lead-free solder typically has a higher melting point than lead solder, requiring higher processing temperatures. This can lead to increased energy consumption and potential thermal damage to components.
- Reduced wetting properties: Lead-free solder often has inferior wetting properties compared to lead solder, which can result in less reliable solder joints and increased risk of defects.
- Higher cost: Lead-free solder alloys are generally more expensive than lead solder due to the added cost of the constituent metals, such as silver and copper.
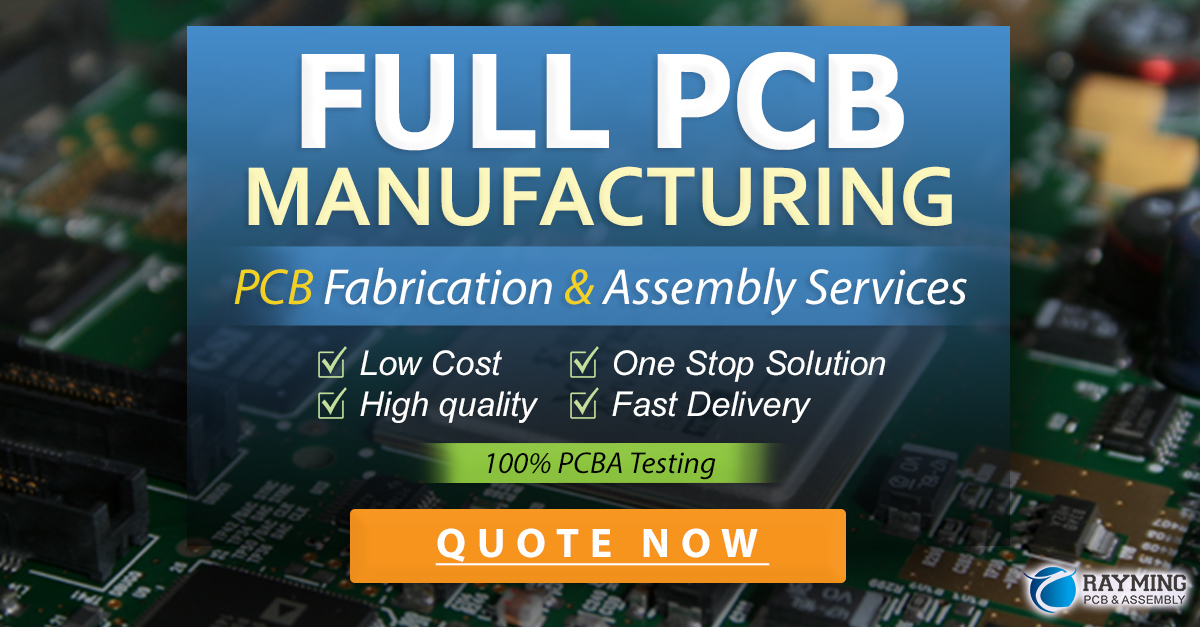
Comparison of Lead and Lead-Free Solder Properties
To better understand the differences between lead and lead-free solder, let’s compare their key properties:
Property | Lead Solder (Sn63/Pb37) | Lead-Free Solder (SAC305) |
---|---|---|
Melting Point | 183°C | 217-220°C |
Tensile Strength | 40-50 MPa | 50-60 MPa |
Electrical Conductivity | 11.9 × 10^6 S/m | 7.5 × 10^6 S/m |
Wetting Angle | 10-30° | 30-45° |
Shelf Life | 2-3 years | 1-2 years |
As seen in the table, lead-free solder (SAC305) has a higher melting point, increased tensile strength, and reduced electrical conductivity compared to lead solder (Sn63/Pb37). The wetting angle, which indicates the solder’s ability to flow and adhere to surfaces, is also higher for lead-free solder, suggesting inferior wetting properties.
Choosing Between Lead and Lead-Free Solder
When deciding between lead and lead-free solder, consider the following factors:
- Environmental and health regulations: If your products are sold in markets with strict regulations on lead use, such as the European Union, you must use lead-free solder to ensure compliance.
- Application requirements: Consider the specific requirements of your application, such as operating temperature, mechanical stress, and electrical performance. Some applications may benefit from the higher mechanical strength of lead-free solder, while others may require the superior wetting properties of lead solder.
- Manufacturing process: Evaluate your manufacturing process and equipment to determine if they are compatible with the higher melting point and processing temperatures required for lead-free solder.
- Cost: Consider the cost implications of using lead-free solder, as it is generally more expensive than lead solder. However, keep in mind that the long-term costs of non-compliance with regulations or potential environmental and health liabilities may outweigh the initial cost savings of using lead solder.
Best Practices for Soldering
Regardless of whether you choose lead or lead-free solder, following best practices for soldering can help ensure high-quality, reliable solder joints:
- Use appropriate soldering techniques: Select the appropriate soldering method (e.g., wave soldering, reflow soldering, hand soldering) based on your application and PCB design.
- Control temperature: Maintain precise control over soldering temperatures to avoid thermal damage to components and ensure proper solder flow.
- Ensure cleanliness: Keep the soldering area clean and free from contaminants, as impurities can weaken solder joints and cause defects.
- Use proper flux: Select the appropriate flux for your solder alloy and application to promote good wetting and prevent oxidation.
- Inspect solder joints: Regularly inspect solder joints for defects, such as bridging, cold joints, or insufficient solder coverage, and take corrective action as necessary.
Frequently Asked Questions (FAQ)
-
Is lead-free solder as reliable as lead solder?
While lead-free solder can produce reliable solder joints, it may require more precise process control and higher soldering temperatures to achieve the same level of reliability as lead solder. -
Can I mix lead and lead-free solder?
Mixing lead and lead-free solder is not recommended, as it can result in unpredictable solder joint properties and potential compatibility issues. It is best to use either lead or lead-free solder consistently throughout a project. -
How can I tell if my solder is lead-free?
Lead-free solder is often marked with “Pb-free” or “LF” on the packaging or spool. You can also refer to the solder’s technical datasheet or consult with the manufacturer to determine if a specific solder alloy is lead-free. -
Are there any health risks associated with using lead-free solder?
While lead-free solder eliminates the health risks associated with lead exposure, some lead-free solder alloys may contain other metals, such as silver or copper, which can pose their own health risks if not handled properly. Always follow proper safety guidelines and use appropriate personal protective equipment when working with any type of solder. -
Can I use lead-free solder for all applications?
Lead-free solder can be used for most electronics applications, but there may be some instances where lead solder is preferred or required, such as in certain high-reliability or military-grade applications. Always consider the specific requirements of your application when selecting a solder alloy.
Conclusion
The choice between lead and lead-free solder depends on various factors, including environmental and health regulations, application requirements, manufacturing processes, and cost considerations. While lead-free solder offers environmental and health benefits, it may present challenges in terms of higher melting points, reduced wetting properties, and increased costs. On the other hand, lead solder, despite its superior wetting properties and lower cost, poses environmental and health risks and may not comply with certain regulations.
Ultimately, the decision to use lead or lead-free solder should be based on a careful evaluation of your specific needs and constraints. By understanding the advantages and disadvantages of each type of solder and following best practices for soldering, you can ensure the production of high-quality, reliable electronic products while minimizing environmental impact and complying with relevant regulations.
Leave a Reply