Introduction to Laser Diodes and Driver Circuits
Laser diodes are a type of semiconductor device that produces coherent light through stimulated emission. Unlike regular LEDs that emit incoherent light over a wide range of wavelengths, laser diodes generate a narrow beam of light at a specific wavelength. This property makes laser diodes useful for various applications, including fiber-optic communication, barcode scanners, laser pointers, and optical storage devices.
To operate a laser diode effectively, you need a specialized driver circuit that can provide the appropriate current and voltage levels while ensuring stable operation and protecting the diode from damage. In this article, we’ll explore the basics of Laser Diode Driver circuits and guide you through the process of designing and building your own.
Key Characteristics of Laser Diodes
Before diving into the details of driver circuits, let’s review some key characteristics of laser diodes that influence their operation and design requirements:
-
Threshold Current: Laser diodes require a minimum current, known as the threshold current, to begin lasing. Below this current, the diode behaves like a regular LED, emitting incoherent light.
-
Forward Voltage Drop: Like other diodes, laser diodes have a forward voltage drop that varies depending on the material and wavelength. Typical values range from 1.5V to 4V.
-
Optical Output Power: The optical output power of a laser diode increases linearly with the driving current once the threshold current is reached. However, exceeding the maximum rated current can cause permanent damage to the diode.
-
Temperature Sensitivity: Laser diodes are sensitive to temperature changes, which can affect their threshold current, wavelength, and output power. Proper thermal management is crucial for stable operation.
Basic Laser Diode Driver Circuit
A basic laser diode driver circuit consists of the following components:
-
Current Limiter: A resistor or a constant current source limits the current flowing through the laser diode to prevent damage.
-
Voltage Regulator: A voltage regulator ensures a stable supply voltage for the laser diode, minimizing the impact of power supply fluctuations.
-
Protection Diode: A reverse-biased protection diode across the laser diode helps prevent reverse current flow and protects the diode from voltage spikes.
-
Switching Transistor: A transistor is used to switch the laser diode on and off rapidly, enabling pulsed operation for applications like data transmission or laser ranging.
Here’s a simple schematic of a basic laser diode driver circuit:
+VCC
|
|
+-+
| |
| | Current Limiter
| |
+-+
|
+-----+------+
| |
+-+-+ +-+-+
| | | |
| Voltage | |
| Regulator | |
| | | Laser Diode
+-+-+ | |
| +-+-+
| |
+-+ |
| | |
| Protection |
| Diode |
| | |
+-+ |
| |
+++ +++
| | | |
| Switching | |
| Transistor | |
| | | |
+++ +++
| |
GND GND
Designing a Laser Diode Driver Circuit
Now that we understand the basic components of a laser diode driver circuit let’s explore the design process in more detail.
Step 1: Determine Laser Diode Specifications
The first step in designing a laser diode driver is to gather the relevant specifications of the laser diode you’ll be using. These include:
- Wavelength
- Threshold Current
- Maximum Continuous Current
- Forward Voltage Drop
- Optical Output Power
You can find these specifications in the laser diode’s datasheet provided by the manufacturer.
Step 2: Select Current Limiting Method
There are two primary methods for limiting the current in a laser diode driver circuit:
-
Resistive Current Limiting: A series resistor is used to limit the current based on Ohm’s law. This method is simple but has some drawbacks, such as power dissipation in the resistor and sensitivity to supply voltage fluctuations.
-
Constant Current Source: A constant current source, such as a transistor-based circuit or a dedicated IC, maintains a stable current regardless of supply voltage variations. This method provides better control and efficiency but is more complex to implement.
The choice between these methods depends on the specific requirements of your application, such as power efficiency, stability, and cost.
Step 3: Calculate Component Values
Once you’ve selected the current limiting method, you can calculate the values of the components in your driver circuit.
For resistive current limiting, use Ohm’s law to determine the value of the series resistor:
R = (V_supply - V_diode) / I_max
Where:
– R is the resistor value in ohms
– V_supply is the supply voltage in volts
– V_diode is the laser diode’s forward voltage drop in volts
– I_max is the maximum continuous current rating of the laser diode in amperes
For constant current sources, refer to the specific design guidelines for the chosen circuit or IC.
Step 4: Select Appropriate Components
Based on the calculated values and the laser diode specifications, select appropriate components for your driver circuit. Consider factors such as power rating, tolerance, and temperature stability when choosing resistors, capacitors, and semiconductor devices.
For the protection diode, choose a diode with a reverse breakdown voltage higher than the maximum expected voltage across the laser diode. Schottky diodes are often used due to their fast switching speed and low forward voltage drop.
Step 5: Design PCB Layout
A well-designed PCB layout is crucial for the proper operation and stability of your laser diode driver circuit. Consider the following guidelines:
- Keep the traces carrying high currents short and wide to minimize resistance and inductance.
- Use ground planes to provide a low-impedance return path and minimize noise.
- Place the current limiting and protection components close to the laser diode to minimize the effects of parasitic inductance and capacitance.
- Use appropriate thermal management techniques, such as heat sinks and thermal vias, to dissipate heat from power-dissipating components.
Step 6: Test and Characterize
After assembling your laser diode driver circuit, it’s essential to test and characterize its performance. Use a current probe or a sense resistor to measure the actual current flowing through the laser diode. Verify that the current remains within the safe operating limits specified in the datasheet.
Also, monitor the optical output power of the laser diode using a calibrated photodetector or power meter. Ensure that the output power is stable and free from significant fluctuations or noise.
Advanced Laser Diode Driver Techniques
While the basic laser diode driver circuit discussed above is sufficient for many applications, some situations may require more advanced techniques to achieve optimal performance. Let’s explore a few of these techniques.
Constant Power Control
In some applications, such as fiber-optic communication, it’s desirable to maintain a constant optical output power from the laser diode despite variations in temperature or aging effects. This can be achieved using a constant power control loop.
A typical constant power control loop consists of a photodetector that monitors the laser diode’s output power, an error amplifier that compares the detected power with a reference level, and a feedback circuit that adjusts the laser diode current accordingly. By continuously adjusting the current, the control loop maintains a stable optical output power.
Temperature Compensation
As mentioned earlier, laser diodes are sensitive to temperature changes, which can affect their threshold current and output power. To maintain stable operation over a wide temperature range, you can implement temperature compensation techniques in your driver circuit.
One common method is to use a temperature sensor, such as a thermistor or a semiconductor temperature sensor, to monitor the laser diode’s temperature. The sensor’s output is used to adjust the current limit or the reference level in the constant power control loop, compensating for temperature-induced variations.
Another approach is to use a thermoelectric cooler (TEC) to actively control the laser diode’s temperature. A TEC is a solid-state device that can heat or cool a laser diode depending on the direction of the current flowing through it. By integrating a TEC and a temperature controller into your driver circuit, you can maintain the laser diode at a constant temperature, ensuring stable operation.
Modulation Techniques
In applications like fiber-optic communication or laser ranging, it’s often necessary to modulate the laser diode’s output to transmit data or measure distances. There are several modulation techniques you can use, depending on your specific requirements:
-
Direct Modulation: In this technique, the laser diode current is directly modulated by the data signal. This method is simple and cost-effective but has limitations in terms of modulation bandwidth and signal integrity.
-
External Modulation: An external modulator, such as an electro-optic modulator (EOM) or an acousto-optic modulator (AOM), is used to modulate the laser diode’s output. This technique offers higher modulation bandwidth and better signal quality but is more complex and expensive.
-
Pulsed Operation: By rapidly switching the laser diode on and off, you can generate short optical pulses for applications like time-of-flight ranging or pulsed laser deposition. Pulsed operation requires careful design of the driver circuit to ensure fast rise and fall times while avoiding overshoot or ringing.
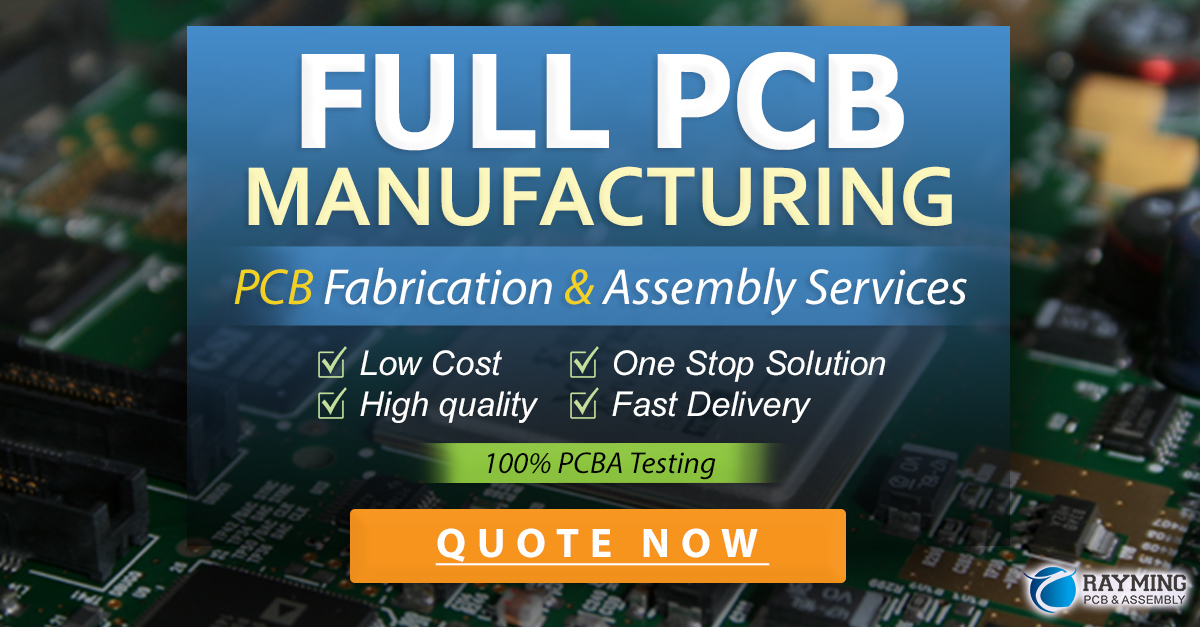
Laser Diode Driver Circuit Examples
To help you understand the practical implementation of laser diode driver circuits, let’s look at a few examples.
Example 1: Simple Resistive Current Limiting Circuit
This example demonstrates a basic laser diode driver circuit using resistive current limiting.
+5V
|
+-+
| |
| 100Ω
| |
+-+
|
+-----+------+
| |
+-+-+ +-+-+
| | | |
| LM317 | Laser Diode
| Voltage | (3V, 20mA)
| Regulator | |
+-+-+ +-+-+
| |
| |
+++ |
| NPN +-+
| Transistor | |
| 2N2222 | Schottky
| | | Diode
+++ | 1N5817
| |
GND GND
In this circuit, a 100Ω resistor limits the current to approximately 20mA, assuming a 3V forward voltage drop across the laser diode. The LM317 voltage regulator provides a stable 5V supply, while the 2N2222 NPN transistor allows the laser diode to be switched on and off. The 1N5817 Schottky diode protects the laser diode from reverse voltage spikes.
Example 2: Constant Current Source with LM317
This example shows how to use an LM317 adjustable voltage regulator as a constant current source for driving a laser diode.
+12V
|
+-+
| |
| 1kΩ
| |
+-+
|
+-----+------+
| |
+-+-+ +-+-+
| | | |
| LM317 | Laser Diode
| | | (5V, 50mA)
+-+-+ +-+-+
| |
+++ |
| 5Ω +-+
| | | |
+++ | Schottky
| | Diode
GND | 1N5817
|
GND
The LM317 is configured as a constant current source by connecting a 5Ω resistor between its adjustment pin and ground. The current through the laser diode is set by the voltage drop across the resistor, which is approximately 1.25V. In this case, the current is limited to 50mA (1.25V / 5Ω). The 1kΩ resistor ensures stable operation of the LM317.
Example 3: Constant Power Control with Photodiode Feedback
This example demonstrates a constant power control loop using a photodiode to monitor the laser diode’s output power.
+5V
|
+-+ +-------+
| | | |
| 100Ω | LM358 |
| | | Op-Amp|
+-+ +---+---+
| |
+-----+------+ |
| | |
+-+-+ +-+-++
| | | ||
| LM317 | Laser Diode
| Voltage | || (3V, 20mA)
| Regulator +-+-++
+-+-+ |
| |
+++ |
| NPN +---+---+
| 2N2222 | |
| | | Photo |
+++ | Diode |
| | |
GND +-------+
|
GND
In this circuit, a photodiode is placed near the laser diode to monitor its output power. The photodiode current, which is proportional to the received light intensity, is converted to a voltage by the LM358 op-amp configured as a transimpedance amplifier. This voltage is compared with a reference voltage (not shown) to generate an error signal, which controls the base current of the 2N2222 transistor. The transistor, in turn, adjusts the current through the laser diode to maintain a constant optical output power.
Frequently Asked Questions (FAQ)
1. What is the difference between a laser diode and an LED?
Laser diodes emit coherent, monochromatic light through stimulated emission, while LEDs produce incoherent light over a wider range of wavelengths. Laser diodes have a much narrower spectral width and higher directionality compared to LEDs.
2. Can I use a regular LED driver circuit to drive a laser diode?
No, laser diodes have specific current and voltage requirements that differ from LEDs. Using a regular LED driver circuit may cause damage to the laser diode or result in unstable operation. It’s essential to use a dedicated laser diode driver circuit that provides the necessary current limiting, voltage regulation, and protection features.
3. How do I determine the maximum current for my laser diode?
The maximum current rating for a laser diode is specified in its datasheet, usually under “Maximum Continuous Current” or “Absolute Maximum Ratings.” It’s crucial to stay within this limit to avoid damaging the laser diode. Always refer to the manufacturer’s datasheet for the specific laser diode you are using.
4. What is the purpose of the protection diode in a laser diode driver circuit?
The protection diode, typically a Schottky diode, is connected in reverse parallel with the laser diode to protect it from reverse voltage spikes that may occur during switching or due to electrostatic discharge (ESD). The protection diode conducts when the voltage across the laser diode becomes negative, preventing reverse current flow and potential damage.
5. Can I use a laser diode driver circuit for pulsed operation?
Yes, laser diode driver circuits can be designed for pulsed operation by incorporating a fast switching transistor and appropriate pulse generation circuitry. However, pulsed operation requires careful consideration of the laser diode’s peak current rating, rise and fall times, and duty cycle to ensure safe and reliable operation. Always consult the laser diode’s datasheet and application notes for guidance on pulsed mode operation.
Conclusion
Laser diode driver circuits play a crucial role in ensuring the stable, efficient, and safe operation of laser diodes in various applications. By understanding the key characteristics of laser diodes and the basic components of driver circuits, you can design and build your own laser diode driver tailored to your specific requirements.
Remember to always refer to the laser diode’s datasheet for the necessary specifications and ratings, and follow best practices for PCB layout and thermal management. When in doubt, consult application notes, reference designs, or seek guidance from experienced professionals.
As you explore more advanced techniques like constant power control, temperature compensation, and modulation, keep in mind the specific requirements and constraints of your application. With the right design approach and attention to detail, you can create reliable and high-performance laser diode driver circuits for a wide range of applications, from optical communication to sensing and material processing.
Leave a Reply