What is a Land Pattern?
A land pattern, also known as a footprint or pad layout, is the arrangement of copper pads and traces on a printed circuit board (PCB) that allows the mounting and soldering of surface-mount components. The land pattern is critical in ensuring proper electrical connections, mechanical stability, and thermal management of the components on the PCB.
Land patterns are designed according to industry standards and guidelines, which take into account factors such as component dimensions, tolerances, soldering requirements, and manufacturing capabilities. Adhering to these standards ensures compatibility, reliability, and manufacturability of the PCB assembly.
Importance of Land Pattern Design
Proper land pattern design is essential for several reasons:
-
Electrical Connectivity: The land pattern must provide adequate contact area for the component leads or terminals to ensure reliable electrical connections. Insufficient or poorly designed land patterns can lead to open circuits, shorts, or intermittent connections.
-
Mechanical Stability: The land pattern should provide sufficient support and anchorage for the component to withstand mechanical stresses during assembly, handling, and operation. Improper land patterns can result in component misalignment, tombstoning (lifting of components during soldering), or mechanical failure.
-
Thermal Management: The land pattern plays a role in dissipating heat generated by the component. Adequate thermal relief and copper area help transfer heat away from the component, preventing overheating and ensuring reliable operation.
-
Manufacturing Feasibility: The land pattern must be designed with consideration for manufacturing processes, such as solder paste application, component placement, and soldering. Overly complex or tightly spaced land patterns can pose challenges for manufacturing and lead to defects or reduced yield.
Industry Standards for Land Pattern Design
Several industry standards and guidelines are available for land pattern design, providing recommendations for dimensions, tolerances, and best practices. Some of the widely recognized standards include:
IPC-7351B: Generic Requirements for Surface Mount Design and Land Pattern Standard
IPC-7351B is a comprehensive standard that provides guidelines for the design and creation of land patterns for surface-mount components. It covers a wide range of component types, including chip components, QFPs, BGAs, and more. The standard specifies recommended land pattern dimensions, tolerances, and courtyard requirements based on component size and package type.
Component Type | Pitch (mm) | Land Width (mm) | Land Length (mm) |
---|---|---|---|
Chip Resistor | 0.5 | 0.6 | 1.0 |
Chip Capacitor | 0.5 | 0.6 | 1.0 |
SOIC | 1.27 | 0.6 | 2.2 |
QFP | 0.5 | 0.3 | 1.5 |
Table 1: Example land pattern dimensions from IPC-7351B
IPC-SM-782A: Surface Mount Design and Land Pattern Standard
IPC-SM-782A is another standard that focuses on land pattern design for surface-mount components. It provides guidelines for creating land patterns that ensure reliable solder joints and minimize assembly defects. The standard covers aspects such as solder joint formation, thermal relief design, and solder mask considerations.
Manufacturer-Specific Guidelines
In addition to industry standards, component manufacturers often provide their own recommended land patterns for their specific components. These guidelines take into account the unique characteristics and requirements of the component and should be followed when designing the land pattern.
It’s important to refer to the manufacturer’s datasheet or application notes for the specific component being used, as they may have specific recommendations or variations from the general industry standards.
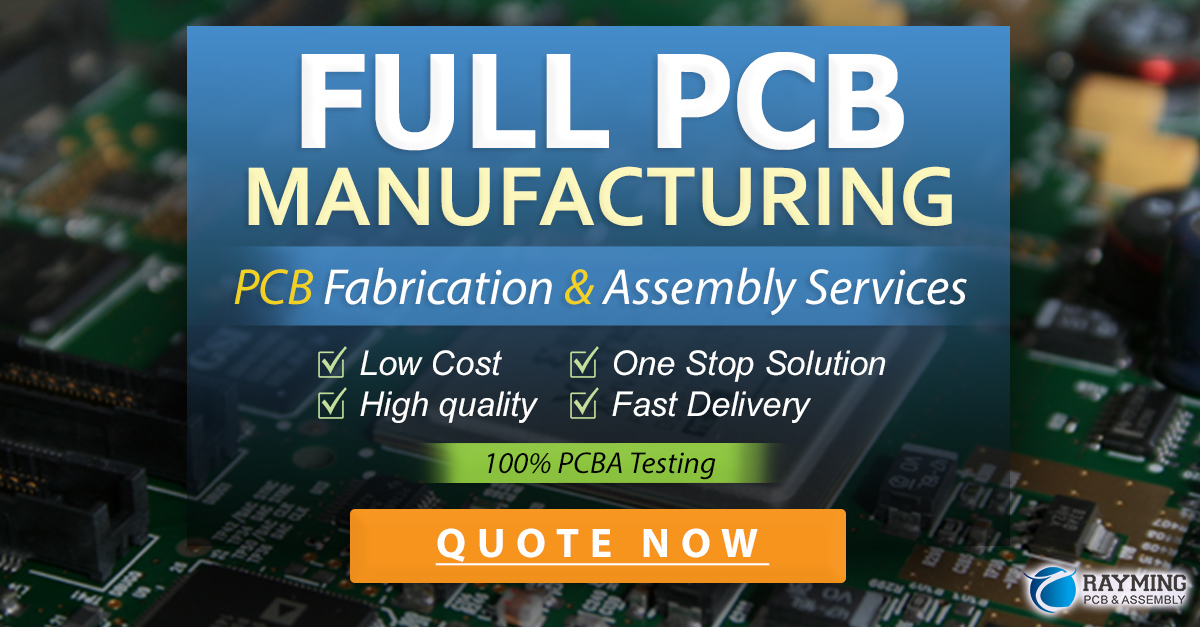
Design Considerations for Land Patterns
When designing land patterns, several key factors should be considered to ensure optimal performance and manufacturability:
Pad Size and Shape
The size and shape of the pads in the land pattern should be based on the component’s lead or terminal dimensions, as well as the soldering requirements. The pads should be large enough to provide sufficient contact area for reliable electrical and mechanical connections, but not so large that they introduce excessive capacitance or interfere with adjacent components.
Rectangular pads are commonly used for leaded components, while rounded or circular pads are often used for leadless components like BGAs. The pad shape should also consider the soldering process, such as providing adequate space for solder fillets.
Pitch and Spacing
The pitch, or distance between the centers of adjacent pads, should match the pitch of the component’s leads or terminals. Adequate spacing between pads is necessary to prevent shorts and ensure proper solder joint formation. The spacing should also consider the manufacturing capabilities, such as the minimum achievable spacing for solder paste printing and component placement.
Solder Mask Openings
Solder mask is a protective layer applied over the copper traces on the PCB, leaving openings for the pads where soldering occurs. The solder mask openings should be designed to ensure proper solder joint formation and prevent solder bridging. The openings should be slightly larger than the pads to allow for solder wetting and fillets.
Thermal Relief
For components that generate significant heat, such as power transistors or voltage regulators, thermal relief patterns should be incorporated into the land pattern. Thermal relief consists of spokes or vias that connect the pad to the surrounding copper pour, allowing heat to dissipate more efficiently. The thermal relief pattern should be designed to balance thermal conductivity with electrical conductivity and mechanical strength.
Courtyard and Assembly Clearance
The land pattern should include a courtyard, which is an area around the component that defines the minimum clearance required for assembly and inspection. The courtyard ensures that adjacent components and features do not interfere with the component placement and soldering. The size of the courtyard depends on the component dimensions, package type, and assembly process tolerances.
Solderable Finish
The land pattern should have a solderable finish to ensure good solderability and reliable solder joint formation. Common solderable finishes include Hot Air Solder Leveling (HASL), Organic Solderability Preservative (OSP), and Electroless Nickel Immersion Gold (ENIG). The choice of finish depends on factors such as component compatibility, shelf life, and cost.
Designing Land Patterns in CAD Tools
Land patterns are typically designed using PCB design software or CAD tools. These tools provide libraries and templates for common component packages and allow customization of land patterns based on specific requirements.
When designing land patterns in CAD tools, consider the following steps:
-
Select the appropriate component package: Choose the component package that matches the specific component being used, such as QFP, BGA, or chip component.
-
Set the component dimensions: Enter the component dimensions, such as pitch, lead width, and overall size, based on the manufacturer’s datasheet or industry standards.
-
Define pad size and shape: Specify the pad size and shape based on the component requirements and soldering considerations. Adjust the pad dimensions as needed to ensure adequate contact area and clearance.
-
Configure solder mask and paste settings: Set the solder mask and paste openings around the pads. The solder mask opening should be slightly larger than the pad, while the paste opening should match the pad size or be slightly smaller.
-
Add thermal relief and vias: For components that require thermal management, add thermal relief spokes or vias to the land pattern. Ensure proper spacing and size of the thermal relief features.
-
Define courtyard and assembly clearance: Create a courtyard around the land pattern to define the minimum clearance required for assembly. Set the courtyard dimensions based on the component size and assembly process tolerances.
-
Verify and validate the land pattern: Check the land pattern against industry standards, manufacturer guidelines, and design rules. Perform a design rule check (DRC) to ensure the land pattern meets the specified constraints and requirements.
Frequently Asked Questions (FAQ)
1. What happens if the land pattern is not designed correctly?
If the land pattern is not designed correctly, it can lead to various issues during assembly and operation, such as:
– Poor solderability and weak solder joints
– Component misalignment or tombstoning
– Shorts or open circuits due to insufficient pad spacing
– Inadequate thermal dissipation, leading to component overheating
– Difficulty in manufacturing, resulting in defects or reduced yield
2. Can I use the same land pattern for different components with the same package?
While components with the same package type may have similar land pattern requirements, it’s important to refer to the specific manufacturer’s datasheet or guidelines for each component. Some components may have unique requirements or variations in pad size, spacing, or thermal relief that need to be considered.
3. What are the most common industry standards for land pattern design?
The most common industry standards for land pattern design include:
– IPC-7351B: Generic Requirements for Surface Mount Design and Land Pattern Standard
– IPC-SM-782A: Surface Mount Design and Land Pattern Standard
– Manufacturer-specific guidelines provided in component datasheets or application notes
4. How do I ensure proper thermal management in the land pattern design?
To ensure proper thermal management in the land pattern design, consider the following:
– Provide adequate copper area around the component to dissipate heat
– Use thermal relief spokes or vias to connect the pad to the surrounding copper pour
– Follow the manufacturer’s recommendations for thermal pad size and design
– Consider the use of thermal interface materials (TIM) if necessary
5. What are the common solderable finishes used for land patterns?
Common solderable finishes used for land patterns include:
– Hot Air Solder Leveling (HASL)
– Organic Solderability Preservative (OSP)
– Electroless Nickel Immersion Gold (ENIG)
– Immersion Silver (ImAg)
– Immersion Tin (ImSn)
The choice of finish depends on factors such as component compatibility, shelf life, solderability requirements, and cost.
Conclusion
Land pattern design is a critical aspect of PCB design that directly impacts the reliability, manufacturability, and performance of the assembled product. Following industry standards and guidelines, such as IPC-7351B and IPC-SM-782A, ensures that land patterns are designed to meet the required specifications and minimize assembly issues.
When designing land patterns, consider factors such as pad size and shape, pitch and spacing, solder mask openings, thermal relief, courtyard, and solderable finish. Use CAD tools and libraries to create land patterns efficiently and accurately, and always refer to the component manufacturer’s datasheet or application notes for specific requirements.
By adhering to best practices and industry standards in land pattern design, designers can ensure robust and reliable PCB assemblies that meet the desired functionality and quality.
Leave a Reply