Introduction
Printed circuit boards (PCBs) form the foundation of all modern electronics products. From relatively simple consumer devices to highly complex industrial systems, PCBs provide the interconnect platform to mount and connect electronic components. With the growth of the electronics hardware industry in India, there is increasing demand for domestic PCB fabrication and assembly services.
PCB manufacturing involves multiple steps – design, fabrication, assembly, and testing. Traditionally, a majority of global PCB production has been centered in China due to their expansive infrastructure and low costs. However, geopolitical factors and supply chain risks have compelled companies to explore alternate locations for sourcing PCBs.
This has created significant opportunities for PCB manufacturing in India to grow. In this guide, we will examine the capabilities for PCB fabrication and assembly available domestically and the key factors influencing electronics hardware companies to source boards from India.
Overview of the PCB Manufacturing Process
To better understand manufacturing capabilities for PCBs in India, let’s first review the typical workflow for taking a board from design through volume production:
PCB Design
The PCB layout is created and all required documentation like schematics, bill of materials, assembly drawings, fabrication/assembly files are generated.
Prototyping
A small number of boards are built to validate the design. This may involve producing the bare boards externally but hand assembling components.
Fabrication
The bare PCB without components is fabricated in bulk. This involves processes like imaging, lamination, etching, drilling.
Assembly
Components are mounted and soldered to the fabricated boards. This may be done manually or using automated pick-and-place assembly lines.
Testing
Each fully assembled board undergoes electrical testing and functional validation. Debugging identifies any issues.
Volume Production
Once the design is validated, full-scale manufacturing with high-volume fabrication, assembly, and testing is launched.
Different providers in India offer capabilities spanning various parts of this workflow. Understanding where in the process they can add value is key.
PCB Fabrication Capabilities in India
For actually fabricating the raw PCB without components, India has developed advanced technological capabilities:
Manufacturers
There are over 100 PCB fabricators in India with combined capacity of over $2 billion. Key manufacturers include Viking Electronics, Xindium Technologies, Hi-Q Electronics, Advanced Circuits, AT&S, and Shogini Tech.
They utilize cutting-edge equipment for fabrication processes and can produce boards at large scale – from a few prototypes to tens of thousands per month.
Capabilities
These manufacturers can deliver a wide range of board complexities and features:
- Layer counts up to 36 layers
- Line/space down to 3/3 mil
- Via hole size down to 0.3 mm
- HDI technology
- High speed materials like FR-4, Rogers, Arlon
- Thick copper up to 20 oz.
- Gold plating
- Flex and rigid-flex PCBs
- Heavy copper, sequential lamination
- Solder mask and silkscreen
This allows them to fabricate even the most demanding designs for sectors like defense, aerospace, telecom infrastructure, consumer electronics etc.
Certifications
Many manufacturers are certified to stringent international quality standards:
- ISO 9001
- IPC Class 2 or Class 3
- UL certification
- RoHS compliance
They utilize advanced QA and inspection tools at every fabrication step using AOI and x-ray to meet reliability requirements.
This level of fabrication expertise domestically provides electronics hardware companies in India the opportunity to significantly shorten supply chains for PCB sourcing instead of importing from other countries.
PCB Assembly Capabilities in India
In addition to bare board fabrication, assembly of components is essential for producing finished PCBs ready for integration into products. India has assembly infrastructure through:
EMS Companies
Contract electronics manufacturing services (EMS) providers like Flex, Kimball Electronics, Dixon, and Centum assemble PCBs for customers.
They have automated SMT lines from leading manufacturers like Fuji, Panasonic, Assembleon, Yamaha, and Juki which allow high-speed precision assembly.
Capabilities
Key assembly capabilities include:
- High-speed chip shooters for SMT components up to 01005 size
- Automatic optical inspection (AOI)
- Conformal coating
- Selective soldering
- Through-hole component insertion
- Box build assembly
- Functional testing
Volume Production
Companies can scale from prototype runs to full production capacity of over 1 million boards per month.
Supply Chain Management
EMS providers manage sourcing of components through distribution networks in India and globally. This alleviates the overhead for customers.
Design Support
Many provide design for manufacturing (DFM) reviews and component engineering to optimize designs for assembly.
So from PCB assembly and test to box build of complete products, the services needed are available domestically without relying exclusively on external sources.
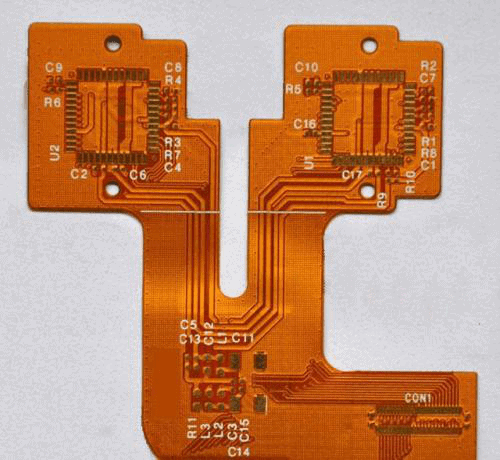
Trends Driving PCB Manufacturing Growth in India
Several trends are catalyzing growth for PCB fabrication and assembly infrastructure in India:
Import Substitution
Government initiatives like Make in India encourage local manufacturing and a reduction in electronics imports. Tax benefits also promote domestic sourcing.
Supply Chain Risk Mitigation
With disruptions to global supply chains, OEMs want to diversify PCB sourcing instead of heavy reliance on limited destinations.
Demand Forecast
India’s electronics manufacturing sector is projected to reach $300 billion by 2025-26 driven by high-volume mobile and consumer products. This requires commensurate PCB production and assembly capacity ramp-up.
Vertical Integration
As OEMs expand operations in India, they are developing capabilities across the product development lifecycle from design through manufacturing. This provides opportunities to integrate PCB fabrication and assembly rather than outsourcing.
Skill Development
Government and industry partnerships are promoting electronics manufacturing skills training programs to develop the technical workforce.
Policy Support
Special economic zones, export benefits, and electronics clusters provide incentives for companies to increase domestic PCB production.
With these drivers, PCB manufacturing in India is poised for robust long-term development.
Challenges Facing PCB Production in India
However, some challenges remain for India to truly achieve global competitiveness and scale in PCB fabrication and assembly:
Raw Material Sourcing
India lacks reliable access to key raw materials like high-end prepregs, copper clad laminates, speciality chemicals and metals. This increases import dependence.
Limited High-Density Interconnect
HDI technology needed for more advanced boards is only starting to emerge among a few leading manufacturers in India.
Equipment Investments
Significant capital expenditure is still required to acquire latest fabrication and assembly equipment to actualize higher capabilities.
Quality Perception
“Made in India” electronics manufacturing does not yet have the same reputation for quality as mature hubs like China, Taiwan, Korea.
Cost Competitiveness
Despite improvements, labor, infrastructure, power and compliance costs are still higher than established electronics manufacturing destinations.
Addressing these gaps through further policy support, R&D, and private investments will enable the PCB industry to overcome hurdles.
Key Applications Driving Demand
While consumer electronics generate high PCB volumes, India’s domestic design and production capabilities are strongest currently in strategic sectors:
Defense and Aerospace
State-owned and private companies manufacture PCBs for radar, avionics, guidance systems, drones, satellites, missiles etc requiring high reliability.
Telecommunications
Local engineering and network buildouts for cellular, broadband, and rural connectivity rely on PCBs sourced domestically.
Industrial Automation
‘Make in India’ initiatives in manufacturing spur demand for PCBs in programmable logic controllers, motor drives, sensors etc.
Automotive
As India emerges as an auto manufacturing hub, electronics content in vehicles is boosting PCB sourcing for telematics, infotainment and safety systems.
Medical
Equipment like ventilators, scanners, diagnostics produced for domestic healthcare consume PCBs from local manufacturers.
By encouraging PCB manufacturing for both high-tech and high-volume segments, India can significantly expand output.
Key PCB Manufacturers in India
Some leading domestic PCB producers catering to the above applications include:
Company | Location | Capabilities |
---|---|---|
Viking Electronics | Bangalore | Rigid PCBs – up to 36 layers, 0.5 mm lines/spaces |
Xindium Technologies | Bengaluru | Rigid, flex, rigid-flex PCBs – 0.25 mm lines/spaces |
Hi-Q Electronics | Bangalore | 28 layer PCBs, 0.15mm lines/spaces, 0.15mm microvias |
Advanced Circuits | Noida | 24 layer rigid boards, 12-16 layer flex/rigid-flex PCBs |
AT&S | Nanjangud | High density PCBs – 16 layers, 0.1mm lines/spaces |
Shogini Tech | Noida | Multilayer, HDI, Flex and Rigid-Flex PCBs |
With their expertise in fabricating advanced technology boards, these leading Indian companies are enabling domestic sourcing for strategic and high-growth product segments.
Outlook for PCB Manufacturing in India
The electronics hardware ecosystem in India has made rapid strides, but sustaining growth requires continued development of PCB fabrication and assembly capabilities:
Expanding Capacity
Leading manufacturers are investing in larger facilities and acquiring latest equipment to substantially boost output.
Import Substitution
Programs to substitute PCB imports across defense, telecom, industrial, and consumer categories with domestic sourcing will help scale manufacturing.
Technology Upgrades
Introducing cutting-edge PCB technology like mSAP, AOI, HDI, and high-density packaging will improve technical proficiency.
Quality Improvement
Process enhancements through automation, ISO certifications and quality benchmarking against global peers will upgrade standards.
Cost Optimization
Economies of scale, better infrastructure, and a trained workforce can help lower manufacturing costs.
Export Focus
The PCB industry is identifying export opportunities to offset domestic demand fluctuations and make India a global electronics manufacturing hub.
With the right policy impetus and private sector participation, PCB manufacturing in India is poised for robust growth in this decade to transform from an import dependent nation to a self-sufficient, quality-focused electronics hardware exporter.
Conclusion
In summary, India has made significant progress developing PCB fabrication and assembly capabilities locally using advanced manufacturing technologies and equipment. While gaps remain to match larger electronics manufacturing hubs, trends like import substitution, supply chain optimization, government support and skill building provide opportunities.
Key domestic manufacturers are already supplying PCBs with high complexity and reliability to strategic sectors. Further investments to expand capacity, upgrade technology, and improve quality can establish India as a prominent destination in the global electronics hardware supply chain.
Frequently Asked Questions
What are some of the latest PCB technologies being adopted in India?
HDI, mSAP, high-speed materials, 0.3mm microvias, AOI, controlled impedance, and higher layer counts up to 36 layers are some of the latest PCB technologies now being manufactured in India.
What certification standards are Indian PCB manufacturers adopting?
Leading manufacturers are implementing stringent quality certifications like ISO 9001, IATF 16949, AS 9100D, and environmental compliance certifications like ISO 14001 and RoHS.
What are some key application areas driving PCB demand in India?
Defense, aerospace, telecom infrastructure, industrial automation, automotive electronics, and medical equipment are key application segments fueling PCB manufacturing growth in India.
How can India build cost competitiveness in PCB manufacturing?
Economies of scale, clustering through electronics manufacturing zones, skill development, automation, and establishing raw material supply chains locally can help optimize costs.
What policy initiatives support PCB manufacturing in India?
Favorable corporate tax structures, PLI incentives, phased manufacturing programs, and favorable export policies are government initiatives encouraging growth of PCB production in India.
Leave a Reply