Introduction
Flex circuits, also known as flexible printed circuits, are a critical component in modern electronics and enable compact, lightweight circuitry for everything from consumer devices to mission-critical aerospace systems. As flex circuits grow more complex and serve increasingly demanding applications, standards play a vital role by promoting design and manufacturing best practices.
The IPC (Association Connecting Electronics Industries) has developed a comprehensive set of flex circuit standards that are widely used across the electronics industry. These standards cover everything from design and layout, to materials and fabrication, to testing and inspection. This article provides an in-depth look at key IPC flex circuit standards, their scope, and how they benefit both designers and manufacturers.
IPC Standards for Flexible Circuits
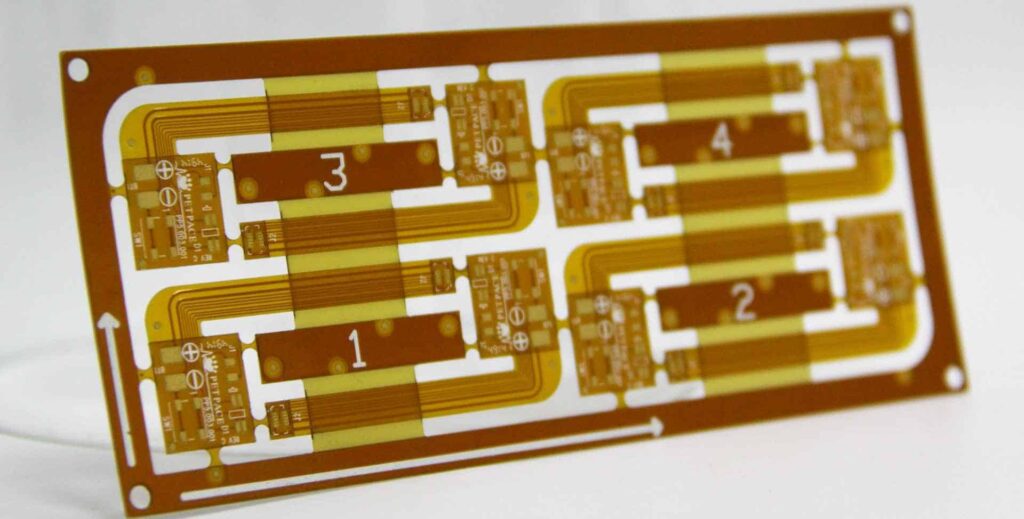
The IPC standards specific to flexible circuits are found in the following families of documents:
IPC-2220 Series
The IPC-2220 series covers generic requirements for the design, fabrication and assembly of flex circuits. This includes:
- IPC-2221 – Generic standard on printed board design
- IPC-2222 – Sectional requirements for flexible printed boards
- IPC-2223 – Sectional requirements for assemblies
- IPC-2224 – Sectional requirements for plated through holes
These documents establish baseline requirements for aspects like materials, handling, assembly, and testing. They are useful for both flex circuit designers and manufacturers.
IPC-6013 Series
The IPC-6013 series provides more detailed requirements and guidance focused on flex circuit design:
- IPC-6013D – Qualification and performance specification for flex materials
- IPC-6016 – Qualification and performance of adhesive coatings
- IPC-6018 – Recommended requirements for organic multichip modules and MCM-L assemblies
These standards help designers select suitable flex circuit materials, adhesives, and assembly techniques. They contain extensive performance test data on flex circuit properties.
IPC-A-600G
IPC-A-600G is the master acceptability standard for electronics assemblies. This wide-ranging document includes a section (section 10) dedicated to flex circuit and rigid-flex circuit assemblies. It provides acceptability requirements for aspects like:
- Conductor alignment
- Coverlayer application
- Adhesive voids
- Flex fold integrity
- Cut edge separation
- And more
This standard is indispensible for flex circuit manufacturers, allowing them to verify quality and detect defects.
IPC J-STD-001
IPC J-STD-001 provides general requirements for soldering on printed boards and assemblies, including flex circuits. The standard covers:
- Soldering processes
- Solder joint acceptance criteria
- Inspection methods
- Training and certification
Meeting these requirements helps ensure the reliability of solder joints on completed flex circuit assemblies.
Benefits of Using IPC Flex Circuit Standards
IPC standards offer a range of benefits for both designers and manufacturers:
For designers:
- Ensure designs meet industry best practices
- Access detailed material property data
- Qualify materials, adhesives, and assembly methods
- Aid communication with manufacturers
For manufacturers:
- Consistency in customer requirements
- Acceptance criteria for quality control
- Assurance that materials and processes meet needs
- Operator training and certification
- Legal protection in case of disputes
Essentially, following IPC standards reduces errors, improves quality, and facilitates collaboration between the designer and producer. The standards accumulate decades of industry knowledge into an organized framework.
Challenges of Implementing IPC Standards
While adoption of IPC standards is almost universal, effective implementation presents some challenges:
- Initial cost – Developing compliant processes requires investment in inspection tools, training, auditing, etc.
- Ongoing compliance – Continual monitoring and auditing is necessary to prove standards are followed.
- Customer conflicts – Some customers have unique or conflicting requirements that override IPC standards.
- New applications – Novel products may not fit neatly into existing standards. Flex circuit technology evolves rapidly.
- Amendments – Keeping up with revisions and amendments to standards requires significant effort.
The benefits outweigh these challenges in most cases. Fortunately, IPC provides extensive training and certification programs to aid in adopting their standards. Most inspection equipment suppliers also offer solutions tailored to IPC requirements.
Key Specifications in IPC-6013D
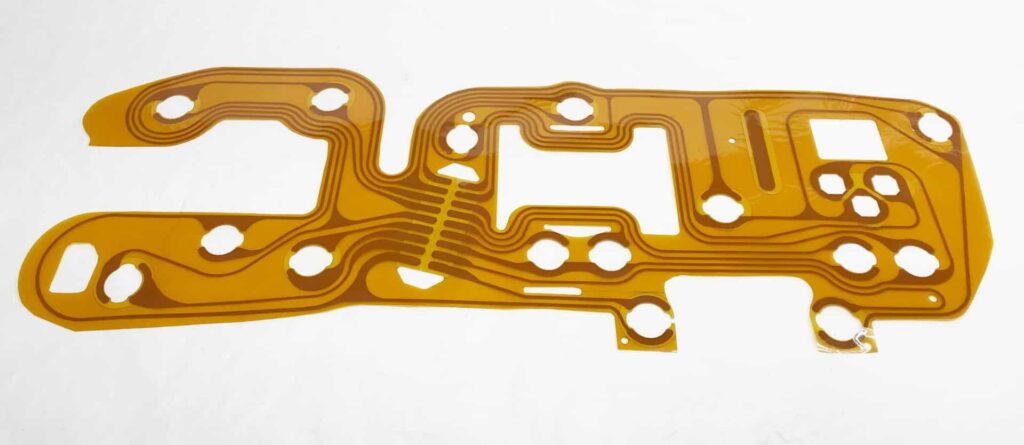
To give a more detailed look at IPC flex circuit standards, here is an overview of key specifications contained in IPC-6013D:
Materials
IPC-6013D specifies requirements for:
- Base Materials – Polyimide, polyester films
- Bonding Adhesives – Epoxy, acrylic, polyimide
- Cover layers – Liquid photoimageable, dry film
It provides minimum performance requirements and test methods for properties like:
- Thermal capabilities
- Flexibility
- Dielectric strength
- Adhesion
- Chemical resistance
Construction
IPC-6013D defines:
- Conductor thickness – 1/2 oz (18um) copper typical
- Minimum spacing between conductors
- Bend radius limits
- Adhesive application methods
- Coverlayer requirements
- Soldermask characteristics
Acceptance Testing
Acceptance testing in IPC-6013D covers:
Test | Description |
---|---|
Net dimensional stability | Exposure to high temperature and humidity |
Conductor adhesiveness | 90 degree peel strength |
Insulation resistance | Dielectric breakdown voltage |
Flammability | Resistance to burning |
Flexibility | Dynamic bend cycles without failure |
IPC-2221 Flex Circuit Design Standard
To understand how IPC standards guide flex circuit designers, it helps to explore IPC-2221 in more detail. This document governs the generic design of flexible printed circuit boards and assemblies.
Key aspects covered in IPC-2221 include:
Materials
- Specifies base material temp range, thickness, color
- Coverlayer requirements – photoimageable, thermal, adhesive
- Adhesive selections – acrylic, epoxy, silicone
Configuration
- Single, double, and multilayer constructions
- Rigid-flex requirements
- Rules for flexible “jumpers”
- Shielding types – conductive adhesive, metal foil
Layout Practices
- Conductor width/spacing based on voltage
- Insulation margins from edges
- Bend radius limits
- Bond pad geometries
- Mixed PTH/via hole sizes
Testing
- Generic qualification and lot acceptance tests
- Sampling rates
- Test coupons
- Failure analysis requirements
IPC-2221 provides hundreds of pages of details on all these aspects to create consistent, robust flex circuit designs.
Fabrication Requirements in IPC-6013D
For flex circuit manufacturers, IPC-6013D defines quality benchmarks through all stages of fabrication:
Materials Handling
- Storage temps, humidity levels
- Contamination control
- Lot traceability
Imaging
- Phototool calibration
- Exposure control
- Develop cycles
- Etch factor targets
Assembly
- Laminating pressures, temperatures
- Hole wall preparations
- Adhesive application
- Component lead trims
Testing
- First article inspection
- Electrical testing
- Visual accept/reject criteria
- Dimensional tolerances
By codifying industry best practices for fabrication, IPC-6013D helps manufacturers build reliability into their processes. Certification to the standard is a mark of quality.
Flex Circuit Inspection Criteria from IPC-A-600G
As the master acceptability document for electronics assemblies, IPC-A-600 provides invaluable visual inspection criteria for flex circuit manufacturers.
Some examples of flex circuit defect criteria in IPC-A-600G:
Defect | Acceptance Criteria |
---|---|
Conductor width variation | ±10% from specified width |
Registration of layers | Misalignment ≤ 10% of minimum spacing |
Adhesive voids | No voids > 2mm within 5mm of joint |
Coverlayer lifting | No lifted edges > 0.5mm |
Cut edge separation | No separation > 0.75mm |
With photo examples of each defect, IPC-A-600G gives clear guidance on identifying and controlling manufacturing issues. Certification to IPC-A-600 requires rigorous inspector training and examination.
Continual Improvement of Standards
A key advantage of the IPC standards is that they evolve over time along with the industry. IPC incorporates feedback from thousands of members to constantly enhance their standards.
For example, IPC-6013 is currently on Revision D, with over 70 updates from the C revision. Recent changes include:
- New acrylic adhesive material requirements
- Updated qualification test methods
- Increased flexibility cycle counts
- Reduced laminating pressures
- Clarified accept/reject criteria
By participating in the IPC standards development process, companies everywhere help improve manufacturing processes and product quality across the board.
Conclusion
IPC flex circuit standards represent a deep well of knowledge gathered from all facets of the electronics industry. They cover the entire product lifecycle from design, to fabrication, to inspection. For both designers and manufacturers, implementing IPC standards provides:
- A common language for requirements
- Best practice design and fabrication methods
- Acceptability requirements for quality control
- Reliability benchmarks for materials and processes
- A path for continual improvement
As flexible circuits increase in prominence, IPC standards will remain vital for driving quality, repeatability and innovation. Companies that embrace these industry standards gain a competitive advantage while contributing to the advancement of the larger electronics ecosystem.
Frequently Asked Questions
What are the main benefits of IPC standards for flex circuit designers?
For designers, the main benefits of following IPC standards are ensuring designs meet industry best practices, gaining access to detailed performance data for materials, qualifying fabrication methods up front, and facilitating clear communication with manufacturers.
What are the main challenges in implementing IPC standards?
Typical challenges include the initial cost of developing compliant processes, the ongoing cost of monitoring and auditing for compliance, dealing with customer requirements that conflict with IPC standards, and keeping up with revisions to standards.
Which IPC documents provide flex circuit fabrication requirements?
Key standards covering fabrication requirements are IPC-6013D for material selection, construction methods and acceptance testing and IPC-A-600G for detailed quality acceptance criteria and visual defect identification.
How do IPC standards for flex circuits improve over time?
IPC standards evolve through industry feedback on proposed revisions and amendments. Thousands of IPC member companies submit input to enhance the standards over time and reflect emerging technologies or lessons learned.
What role does IPC-2221 play for flex circuit designers?
IPC-2221 provides comprehensive requirements on materials, construction methods, layout practices, qualification testing and other aspects vital for robust flex circuit design. It covers the entire product life cycle.
Leave a Reply