Introduction to IPC-A-600 Standards
IPC-A-600 is the industry standard for establishing acceptability requirements for printed circuit boards (PCBs). Developed by the Association Connecting Electronics Industries (IPC), this standard provides visual quality acceptability requirements and illustrations for PCBs. It covers various aspects of PCB manufacturing, including materials, workmanship, solderability, and surface mount and through-hole component mounting.
The IPC-A-600 standard is widely used by PCB manufacturers, assemblers, and end-users to ensure consistent quality and reliability of printed circuit boards. It helps in reducing ambiguity and provides a common language for all stakeholders involved in the PCB industry.
Understanding IPC-A-600 Classes
IPC-A-600 defines three classes of printed circuit boards based on their intended end-use applications and the level of quality required. These classes are:
- Class 1 – General Electronic Products
- Class 2 – Dedicated Service Electronic Products
- Class 3 – High-Performance Electronic Products
Let’s explore each class in detail.
Class 1 – General Electronic Products
Class 1 PCBs are used in general electronic products where the main requirement is the function of the completed assembly. These products are suitable for applications where cosmetic imperfections are not important, and the end-use environment is not overly harsh.
Key characteristics of Class 1 PCBs:
– Lowest cost
– Least stringent acceptability criteria
– Suitable for consumer electronics, toys, and low-end appliances
Examples of Class 1 products:
– Alarm clocks
– Low-end computer peripherals
– Toys with electronic components
Class 2 – Dedicated Service Electronic Products
Class 2 PCBs are used in dedicated service electronic products where continued performance and extended life are required. These products are suitable for applications where uninterrupted service is desired but not critical, and the end-use environment is not excessively severe.
Key characteristics of Class 2 PCBs:
– Moderate cost
– Increased quality requirements compared to Class 1
– Suitable for telecommunications equipment, industrial controls, and automotive electronics
Examples of Class 2 products:
– ATMs
– Automotive engine controls
– Industrial automation systems
Class 3 – High-Performance Electronic Products
Class 3 PCBs are used in high-performance electronic products where continued high performance or performance-on-demand is critical, equipment downtime cannot be tolerated, end-use environment may be exceptionally harsh, and the equipment must function when required.
Key characteristics of Class 3 PCBs:
– Highest cost
– Most stringent acceptability criteria
– Suitable for aerospace, military, and medical life-support systems
Examples of Class 3 products:
– Aerospace control systems
– Medical implantable devices
– Military communication equipment
IPC-A-600 Acceptability Criteria
IPC-A-600 provides detailed acceptability criteria for various aspects of PCB manufacturing. These criteria are based on the class of the PCB and are used to determine if a board meets the required quality standards. The main categories covered by IPC-A-600 include:
- Printed Board Edges
- Conductors
- Solder Mask
- Marking
- Solder Coatings and Fused Tin Lead
- Holes (Plated-Through Holes, Unsupported Holes, Solder Mask Tenting)
- Printed Board Surface and Cleaning
- Flexible and Rigid-Flex Printed Boards
For each category, IPC-A-600 provides visual examples and acceptability criteria for the three classes of PCBs. These criteria are presented in a tabular format for easy reference.
Here’s an example table for the acceptability of conductor width and spacing:
Characteristic | Class 1 | Class 2 | Class 3 |
---|---|---|---|
Conductor Width | -20% to +50% | -10% to +20% | -5% to +10% |
Conductor Spacing | -20% to +50% | -10% to +20% | -5% to +10% |
This table indicates that for Class 1 PCBs, the conductor width and spacing can vary from -20% to +50% of the specified dimensions. For Class 2, the allowable variation is -10% to +20%, and for Class 3, it is -5% to +10%.
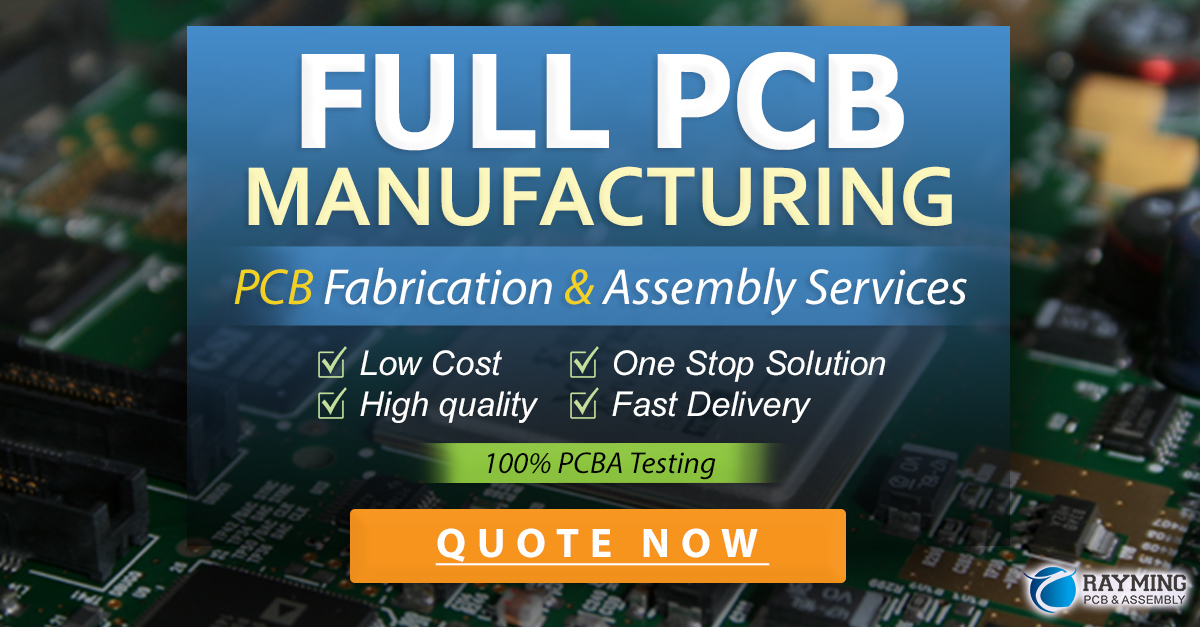
Importance of Adhering to IPC-A-600 Standards
Adhering to IPC-A-600 standards is crucial for ensuring the quality, reliability, and consistency of printed circuit boards. By following these standards, PCB manufacturers can:
- Reduce ambiguity and misinterpretation of acceptability criteria
- Ensure that PCBs meet the required quality standards for their intended end-use applications
- Facilitate communication between PCB manufacturers, assemblers, and end-users
- Minimize the risk of PCB failures and associated costs
- Improve customer satisfaction and brand reputation
PCB manufacturers should familiarize themselves with IPC-A-600 standards and implement appropriate quality control processes to ensure compliance. Regular training and audits can help maintain a high level of quality and consistency in PCB production.
Frequently Asked Questions (FAQ)
-
What is the difference between Class 2 and Class 3 PCBs?
Class 2 PCBs are suitable for dedicated service electronic products where continued performance and extended life are required, but uninterrupted service is not critical. Class 3 PCBs, on the other hand, are used in high-performance electronic products where continued high performance or performance-on-demand is critical, equipment downtime cannot be tolerated, and the end-use environment may be exceptionally harsh. -
Can a PCB be classified as both Class 1 and Class 2?
No, a PCB cannot be classified as both Class 1 and Class 2. Each PCB is classified into one of the three classes based on its intended end-use application and the level of quality required. -
How often should IPC-A-600 standards be updated?
IPC-A-600 standards are periodically reviewed and updated to keep pace with advancements in PCB manufacturing technologies and changing industry requirements. The frequency of updates may vary, but it is essential to refer to the latest version of the standard to ensure compliance. -
Are IPC-A-600 standards mandatory for PCB manufacturers?
While IPC-A-600 standards are not legally mandatory, they are widely accepted and followed by the PCB industry. Adhering to these standards is often a requirement from customers and helps PCB manufacturers demonstrate their commitment to quality and reliability. -
How can PCB manufacturers ensure compliance with IPC-A-600 standards?
PCB manufacturers can ensure compliance with IPC-A-600 standards by implementing a robust quality management system, conducting regular training for employees, and performing internal audits. Engaging with third-party certification bodies can also help validate compliance and provide additional assurance to customers.
Conclusion
IPC-A-600 is a crucial standard for the PCB industry, providing a framework for establishing acceptability requirements for printed circuit boards. By defining three classes of PCBs based on their intended end-use applications and quality requirements, IPC-A-600 helps reduce ambiguity and ensures consistent quality across the industry.
PCB manufacturers should make every effort to understand and adhere to IPC-A-600 standards to produce high-quality, reliable PCBs that meet the needs of their customers. By doing so, they can enhance their reputation, reduce the risk of failures, and contribute to the overall advancement of the electronics industry.
Leave a Reply