Introduction
In the world of printed circuit board (PCB) design, ensuring reliable and efficient power delivery is of paramount importance. Traces on a PCB act as conductors, carrying electrical current from one component to another. However, as current flows through these traces, it generates heat due to the inherent resistance of the conductor material. Excessive heating can lead to various issues, such as increased resistance, degradation of insulation materials, and even catastrophic failure of the PCB.
To mitigate these risks, it is essential to properly design and size the traces according to industry standards. One widely accepted standard is IPC-2221, which provides guidelines for calculating the current-carrying capacity and temperature rise of PCB traces based on various factors, including trace dimensions, copper weight, and environmental conditions.
In this article, we will delve into the IPC-2221 calculator, a powerful tool that assists PCB designers in determining the maximum allowable current and temperature rise for PCB traces. We will explore the underlying principles, formulas, and factors involved in these calculations, as well as the practical applications and considerations for ensuring reliable and efficient power distribution on PCBs.
Understanding IPC-2221
IPC-2221 is a widely recognized standard developed by the Association Connecting Electronics Industries (IPC). It provides comprehensive guidelines for the design and manufacturing of printed circuit boards, including specifications for trace currents and temperature rise.
The standard takes into account various factors that influence the current-carrying capacity and temperature rise of PCB traces, such as trace width, thickness, copper weight, and the presence of external cooling mechanisms. By considering these factors, IPC-2221 enables PCB designers to determine the maximum allowable current that can safely flow through a trace without exceeding specified temperature limits.
Trace Current Calculation
The IPC-2221 calculator allows designers to determine the maximum allowable current for a given trace based on several parameters. The formula used for this calculation is as follows:Copy code
I = k * A * (ΔT)^B
Where:
I
is the maximum allowable current in amperes (A)k
is a constant based on the trace cross-sectional area and the presence of external coolingA
is the cross-sectional area of the trace in square milsΔT
is the temperature rise above the ambient temperature in degrees Celsius (°C)B
is a constant based on the trace cross-sectional area and the presence of external cooling
The values of k
and B
are determined based on lookup tables provided in the IPC-2221 standard, which take into account the trace cross-sectional area and the presence of external cooling mechanisms, such as air flow or heatsinks.
Example Calculation
Let’s consider an example to illustrate the trace current calculation using the IPC-2221 calculator.
Suppose we have a PCB trace with the following parameters:
- Trace width: 10 mils (0.254 mm)
- Trace thickness: 1 oz copper (0.0347 mm)
- Ambient temperature: 25°C
- Maximum allowable temperature rise: 30°C
To calculate the maximum allowable current, we first need to determine the cross-sectional area of the trace:Copy code
Cross-sectional area = Trace width × Trace thickness Cross-sectional area = 10 mils × 1 oz copper Cross-sectional area = 1000 square mils
Next, we need to find the values of k
and B
from the IPC-2221 standard based on the cross-sectional area and the presence of external cooling. Assuming no external cooling, we can look up the values in the appropriate table:
k
= 0.048B
= 0.44
Now, we can substitute these values into the formula:Copy code
I = k * A * (ΔT)^B I = 0.048 * 1000 * (30)^0.44 I = 8.93 amperes
Therefore, according to the IPC-2221 calculator, the maximum allowable current for this trace is approximately 8.93 amperes, considering the specified temperature rise limit of 30°C above the ambient temperature of 25°C.
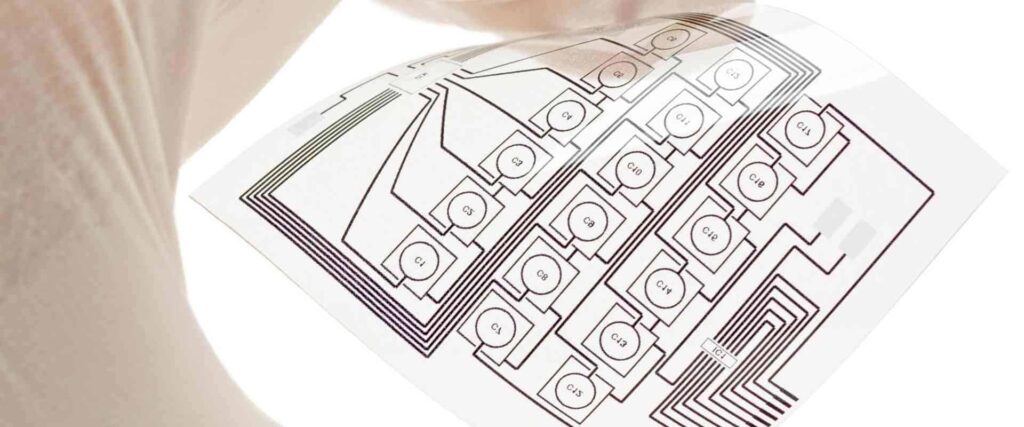
Temperature Rise Calculation
In addition to calculating the maximum allowable current, the IPC-2221 calculator can also be used to determine the temperature rise of a PCB trace for a given current. This calculation is particularly useful when designing power distribution systems or evaluating the thermal performance of existing PCB designs.
The formula used for calculating the temperature rise is a rearrangement of the previous equation:Copy code
ΔT = (I / (k * A))^(1/B)
Where:
ΔT
is the temperature rise above the ambient temperature in degrees Celsius (°C)I
is the current flowing through the trace in amperes (A)k
andB
are constants based on the trace cross-sectional area and the presence of external coolingA
is the cross-sectional area of the trace in square mils
Example Calculation
Let’s consider an example to illustrate the temperature rise calculation using the IPC-2221 calculator.
Suppose we have a PCB trace with the following parameters:
- Trace width: 12 mils (0.305 mm)
- Trace thickness: 1 oz copper (0.0347 mm)
- Current flowing through the trace: 5 amperes
- Ambient temperature: 25°C
To calculate the temperature rise, we first need to determine the cross-sectional area of the trace:Copy code
Cross-sectional area = Trace width × Trace thickness Cross-sectional area = 12 mils × 1 oz copper Cross-sectional area = 1200 square mils
Next, we need to find the values of k
and B
from the IPC-2221 standard based on the cross-sectional area and the presence of external cooling. Assuming no external cooling, we can look up the values in the appropriate table:
k
= 0.048B
= 0.44
Now, we can substitute these values into the formula:Copy code
ΔT = (I / (k * A))^(1/B) ΔT = (5 / (0.048 * 1200))^(1/0.44) ΔT = 21.37°C
Therefore, according to the IPC-2221 calculator, the temperature rise of this trace with a current of 5 amperes is approximately 21.37°C above the ambient temperature of 25°C, resulting in a total temperature of 46.37°C.
Factors Affecting Trace Current and Temperature Rise
While the IPC-2221 calculator provides a standardized method for determining trace currents and temperature rise, it is essential to consider various factors that can influence these calculations. Understanding these factors can help PCB designers make informed decisions and ensure reliable and efficient power distribution on their boards.
Trace Dimensions
The cross-sectional area of a PCB trace plays a crucial role in its current-carrying capacity and temperature rise. Wider and thicker traces have a larger cross-sectional area, allowing them to carry higher currents and dissipate heat more effectively. However, increasing trace dimensions also increases the required board space, which may conflict with design constraints or manufacturing capabilities.
Copper Weight
The copper weight, typically specified in ounces per square foot (oz/ft²), determines the thickness of the copper layer on the PCB. Heavier copper weights result in thicker traces, providing better current-carrying capacity and improved heat dissipation. However, increasing the copper weight can also increase manufacturing costs and affect the overall board thickness and weight.
External Cooling
The presence of external cooling mechanisms, such as forced air flow or heatsinks, can significantly improve the current-carrying capacity and temperature management of PCB traces. By facilitating heat dissipation, external cooling allows traces to carry higher currents without exceeding temperature limits. However, incorporating external cooling mechanisms may increase design complexity and cost.
Ambient Temperature
The ambient temperature of the operating environment plays a crucial role in the temperature rise calculation. Higher ambient temperatures leave less headroom for temperature rise, potentially limiting the maximum allowable current or requiring additional cooling measures.
Trace Routing and Spacing
The layout and routing of traces on a PCB can influence their thermal performance. Traces in close proximity to heat-generating components or other high-current traces may experience additional heating, potentially reducing their current-carrying capacity. Proper trace spacing and layout considerations are essential for efficient heat dissipation and electrical isolation.
Material Properties
The properties of the PCB substrate material, such as thermal conductivity and dielectric constant, can affect the heat dissipation and electrical characteristics of the traces. Selecting appropriate materials based on the application requirements is crucial for ensuring reliable and efficient power distribution.
Applications and Considerations
The IPC-2221 calculator finds numerous applications in the PCB design process, including:
- Power Distribution Design: When designing power distribution networks, the calculator enables PCB designers to determine the appropriate trace widths and thicknesses to handle the required currents while adhering to temperature limits.
- Thermal Management: By calculating the temperature rise of traces under specific current loads, the IPC-2221 calculator aids in thermal management and the selection of appropriate cooling strategies.
- Design Verification: During the design review process, the calculator can be used to verify that the trace dimensions and currents comply with industry standards and meet the desired thermal performance requirements.
- Failure Analysis: In the event of PCB failures or thermal issues, the IPC-2221 calculator can assist in analyzing the root cause by evaluating the trace currents and temperature rise under various operating conditions.
When using the IPC-2221 calculator, it is essential to consider the following factors:
- Ensure accurate input parameters, such as trace dimensions, copper weight, and ambient temperature, for reliable calculations.
- Consider the impact of external cooling mechanisms, if present, on the trace current and temperature rise calculations.
- Validate the calculated values against real-world measurements or simulations to account for any deviations or additional factors not covered by the standard.
- Regularly review and update the calculations as design changes or operating conditions evolve to maintain optimal thermal performance.
Frequently Asked Questions (FAQ)
- What is the IPC-2221 standard? The IPC-2221 standard is a widely recognized set of guidelines developed by the Association Connecting Electronics Industries (IPC) for the design and manufacturing of printed circuit boards. It provides specifications and calculations for various aspects of PCB design, including trace currents and temperature rise.
- Why is it important to consider trace currents and temperature rise in PCB design? Excessive current flow or temperature rise in PCB traces can lead to various issues, such as increased resistance, degradation of insulation materials, and even catastrophic failure of the board. Properly sizing and designing traces according to industry standards like IPC-2221 is crucial for ensuring reliable and efficient power distribution on PCBs.
- How does the IPC-2221 calculator determine the maximum allowable current for a trace? The IPC-2221 calculator uses a formula that takes into account the trace cross-sectional area, temperature rise, and constants based on the presence of external cooling. By considering these factors, it calculates the maximum allowable current that can safely flow through the trace without exceeding specified temperature limits.
- Can the IPC-2221 calculator be used to calculate the temperature rise of a trace? Yes, the IPC-2221 calculator can also be used to determine the temperature rise of a PCB trace for a given current. This calculation is useful when designing power distribution systems or evaluating the thermal performance of existing PCB designs.
- What factors should be considered when using the IPC-2221 calculator? Several factors should be considered when using the IPC-2221 calculator, including trace dimensions, copper weight, external cooling mechanisms, ambient temperature, trace routing and spacing, and material properties. Accurately accounting for these factors is essential for reliable calculations and ensuring optimal thermal performance.
Conclusion
The IPC-2221 calculator is a powerful tool that assists PCB designers in determining the maximum allowable current and temperature rise for PCB traces based on industry standards. By considering factors such as trace dimensions, copper weight, and environmental conditions, the calculator ensures reliable and efficient power distribution on printed circuit boards.
Proper use of the IPC-2221 calculator, along with careful consideration of the various factors affecting trace current and temperature rise, can help mitigate risks associated with excessive heating, such as increased resistance, insulation degradation, and potential failure.
Whether designing power distribution networks, performing thermal management analyses, or verifying design compliance, the IPC-2221 calculator provides a standardized and comprehensive approach to ensuring the thermal integrity and reliability of PCB designs.
As the demand for high-performance and compact electronic systems continues to grow, the importance of accurate trace current and temperature rise calculations will become increasingly crucial. By embracing industry standards like IPC-2221 and leveraging tools like the calculator, PCB designers can stay ahead of the curve and deliver reliable and efficient power distribution solutions.
Leave a Reply