Introduction to Innerlayer Imaging
Innerlayer imaging is a critical step in the manufacturing process of multilayer printed circuit boards (PCBs). It involves transferring the circuit pattern onto the copper surface of the inner layers of the PCB Stack-Up. The accuracy and precision of the innerlayer imaging process directly impact the functionality, reliability, and performance of the final PCB product.
In this article, we will delve into the details of innerlayer imaging for multilayer PCBs, covering the various methods, materials, and best practices involved. We will also discuss common challenges and solutions, as well as emerging trends and technologies in this field.
The Importance of Innerlayer Imaging in Multilayer PCBs
Multilayer PCBs have become increasingly popular in the electronics industry due to their ability to accommodate complex circuitry in a compact form factor. By stacking multiple layers of copper traces and insulating dielectric materials, designers can achieve higher component density, improved signal integrity, and better thermal management.
However, the success of a multilayer PCB heavily relies on the accuracy of the innerlayer imaging process. Any misalignment, distortion, or defects in the circuit pattern can lead to:
- Short circuits or open circuits
- Impedance mismatches
- Signal integrity issues
- Reduced manufacturing yield
- Increased production costs
Therefore, it is crucial to understand and optimize the innerlayer imaging process to ensure the quality and reliability of multilayer PCBs.
Methods of Innerlayer Imaging
There are several methods used for innerlayer imaging in Multilayer PCB Manufacturing. The choice of method depends on various factors such as the required resolution, throughput, cost, and available equipment. Let’s explore some of the most common methods:
1. Photolithography
Photolithography is the most widely used method for innerlayer imaging in the PCB industry. It involves the following steps:
- Applying a light-sensitive photoresist coating on the copper surface of the innerlayer.
- Exposing the photoresist to UV light through a photomask or phototool that contains the circuit pattern.
- Developing the photoresist to remove the exposed (or unexposed) areas, depending on the type of photoresist used (positive or negative).
- Etching away the exposed copper areas using a chemical etching process.
- Stripping off the remaining photoresist to reveal the final circuit pattern.
Photolithography offers several advantages, such as:
- High resolution (down to a few microns)
- Good repeatability and consistency
- Compatibility with a wide range of substrate materials
- Scalability for high-volume production
However, it also has some limitations, such as:
- High cost of photomasks and equipment
- Sensitivity to environmental factors (e.g., humidity, temperature)
- Waste generation from the use of chemicals
2. Direct Imaging (DI)
Direct imaging is a maskless alternative to photolithography that has gained popularity in recent years. Instead of using a physical photomask, DI systems use a digital image file to directly expose the photoresist on the innerlayer surface. This is typically achieved using a laser or LED light source that is controlled by a computer.
The main advantages of direct imaging include:
- Elimination of photomasks, reducing cost and lead time
- Flexibility to make quick design changes without needing new masks
- Higher resolution and finer feature sizes compared to photolithography
- Reduced environmental impact due to less chemical usage
However, direct imaging systems can be more expensive than traditional photolithography equipment, and they may require specialized software and operator training.
3. Inkjet Printing
Inkjet printing is an emerging technology for innerlayer imaging that uses a modified inkjet printer to deposit conductive ink directly onto the substrate surface. The ink contains metal nanoparticles (e.g., silver, copper) that can form the desired circuit pattern when sintered at high temperatures.
Inkjet printing offers several potential benefits, such as:
- Low cost and simplicity of the process
- Ability to print on a variety of substrate materials
- Reduced waste and environmental impact
- Possibility of printing multiple layers in a single pass
However, inkjet printing is still in the early stages of development for PCB Applications, and it faces challenges such as:
- Limited resolution and feature sizes compared to photolithography
- Need for specialized inks and substrates
- Difficulty in achieving consistent and reliable results
- Long sintering times and high temperatures required
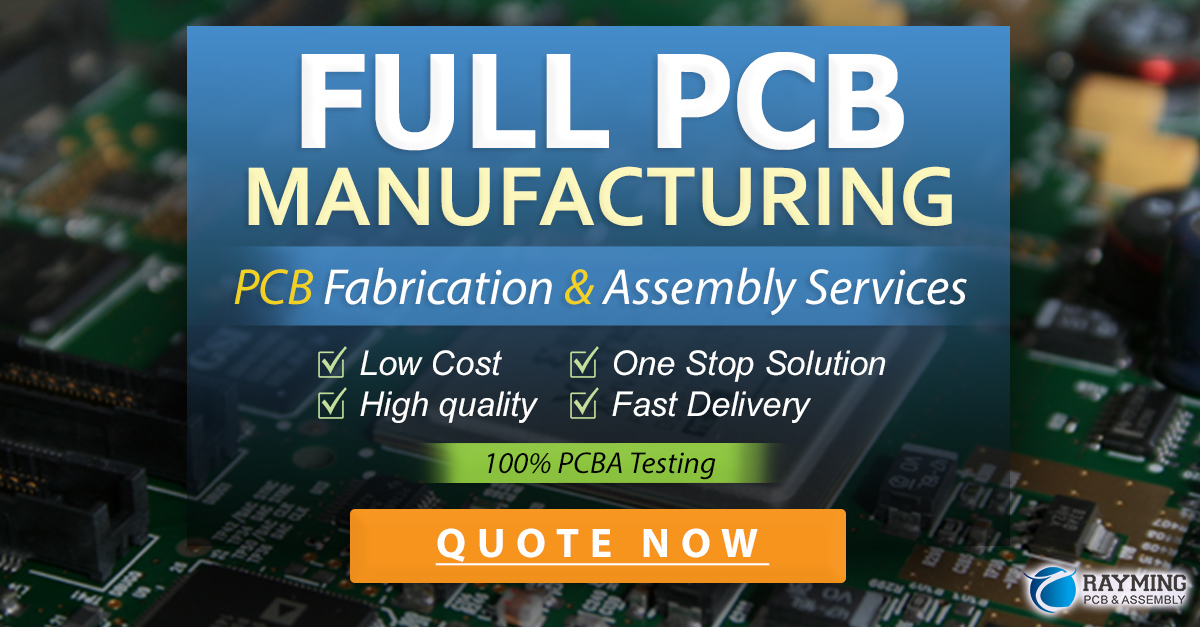
Materials Used in Innerlayer Imaging
The materials used in innerlayer imaging play a crucial role in determining the quality and performance of the final PCB product. Let’s take a closer look at some of the key materials involved:
1. Copper Foil
Copper foil is the starting material for the innerlayer circuits. It is typically laminated onto the dielectric substrate using heat and pressure. The thickness of the copper foil can vary depending on the application, but common values are 1/2 oz (18 µm), 1 oz (35 µm), and 2 oz (70 µm).
The quality of the copper foil is important for achieving good innerlayer imaging results. Factors to consider include:
- Surface roughness and cleanliness
- Mechanical properties (e.g., tensile strength, elongation)
- Electrical conductivity
- Compatibility with the lamination process
2. Photoresist
Photoresist is a light-sensitive polymer that is applied onto the copper surface before the imaging process. It acts as a temporary mask that protects the desired copper areas from being etched away.
There are two main types of photoresists used in PCB manufacturing:
- Dry film photoresist: This comes in the form of a solid film that is laminated onto the copper surface using heat and pressure. It is the most common type used for innerlayer imaging.
- Liquid photoresist: This is applied as a liquid coating using spin coating or screen printing methods. It is less common but can offer higher resolution and conformality.
The choice of photoresist depends on factors such as the required resolution, aspect ratio, and compatibility with the exposure and development processes.
3. Dielectric Substrate
The dielectric substrate is the insulating material that separates the copper layers in a multilayer PCB. It provides mechanical support and electrical isolation between the layers.
Common dielectric materials used in PCBs include:
- FR-4: A composite material made of woven fiberglass and epoxy resin. It is the most widely used substrate material due to its good mechanical and electrical properties, as well as its low cost.
- Polyimide: A high-performance polymer that offers excellent thermal stability, chemical resistance, and flexibility. It is often used in flexible and Rigid-flex PCBs.
- High-frequency laminates: These are specialty materials designed for high-speed and high-frequency applications, such as RF and microwave circuits. Examples include PTFE (Teflon), Rogers, and Isola materials.
The choice of dielectric substrate depends on the specific requirements of the PCB, such as the operating temperature, frequency, and environment.
Best Practices for Innerlayer Imaging
To achieve the best results in innerlayer imaging, it is important to follow some best practices and guidelines. Here are some key considerations:
1. Design for Manufacturability (DFM)
DFM involves designing the PCB layout in a way that is compatible with the manufacturing processes and capabilities. Some DFM guidelines for innerlayer imaging include:
- Ensuring adequate clearance and spacing between features
- Avoiding sharp corners and angles in the trace geometry
- Using standard via sizes and pad shapes
- Providing sufficient copper balancing and thieving to prevent warpage and distortion
2. Process Control
Maintaining tight control over the innerlayer imaging process parameters is critical for achieving consistent and reliable results. Some important factors to monitor and control include:
- Exposure dose and time
- Development time and temperature
- Etching rate and uniformity
- Resist thickness and adhesion
- Environmental conditions (e.g., humidity, air flow)
Implementing statistical process control (SPC) methods and regular quality checks can help identify and correct any deviations or issues in the process.
3. Equipment Maintenance and Calibration
Proper maintenance and calibration of the innerlayer imaging equipment are essential for ensuring optimal performance and repeatability. This includes:
- Regular cleaning and inspection of the exposure and development systems
- Calibration of the light source intensity and uniformity
- Monitoring and replacing consumables (e.g., filters, lamps)
- Preventive maintenance and servicing as recommended by the equipment manufacturer
4. Material Selection and Handling
Choosing the right materials and handling them properly can significantly impact the quality of the innerlayer imaging. Some best practices include:
- Using high-quality copper foil and dielectric substrates from reputable suppliers
- Storing materials in a controlled environment (e.g., temperature, humidity)
- Following the manufacturer’s recommendations for handling and processing
- Implementing strict contamination control measures (e.g., clean room, ESD protection)
5. Documentation and Traceability
Maintaining accurate and up-to-date documentation of the innerlayer imaging process is important for traceability and continuous improvement. This includes:
- Documenting the process parameters and settings used for each job
- Recording any deviations, issues, or corrective actions taken
- Implementing a version control system for the design files and artwork
- Maintaining a database of material and equipment specifications and certifications
Common Challenges and Solutions
Despite the advancements in innerlayer imaging technology, there are still several challenges that PCB manufacturers face. Here are some common issues and potential solutions:
1. Misregistration and Misalignment
Misregistration refers to the misalignment between the innerlayer images and the drilled holes or other layers in the PCB stack-up. This can cause issues such as open or short circuits, impedance mismatches, and signal integrity problems.
Possible solutions include:
- Using advanced registration systems and fiducial marks for alignment
- Implementing tight tolerances and process controls
- Using pin-less registration methods (e.g., optical, X-ray)
- Performing regular calibration and maintenance of the equipment
2. Copper Etching Problems
Copper etching issues can arise due to various factors, such as:
- Incorrect etching time or temperature
- Uneven etching rates across the panel
- Undercut or overetching of the features
- Residual copper or resist on the surface
Potential solutions include:
- Optimizing the etching process parameters (e.g., etchant concentration, temperature, agitation)
- Using advanced etching methods (e.g., vertical continuous etching, spray etching)
- Implementing in-line monitoring and control systems
- Performing regular maintenance and calibration of the etching equipment
3. Photoresist Adhesion and Defects
Photoresist adhesion and defects can lead to issues such as:
- Lifting or peeling of the resist during development or etching
- Pinholes, bubbles, or cracks in the resist layer
- Incomplete or non-uniform coverage of the copper surface
Possible solutions include:
- Ensuring proper surface preparation and cleaning before resist application
- Using high-quality photoresists and following the manufacturer’s recommendations
- Optimizing the resist application and drying parameters
- Implementing strict contamination control measures
4. Artwork and Design Errors
Errors in the artwork or design files can cause significant problems in the innerlayer imaging process, such as:
- Missing or incorrect features
- Incorrect dimensions or tolerances
- Incompatible file formats or settings
Potential solutions include:
- Implementing a rigorous design review and verification process
- Using automated design rule checks (DRC) and layout vs. schematic (LVS) tools
- Collaborating closely with the customer or design team to ensure accuracy
- Maintaining version control and backup systems for the design files
Emerging Trends and Technologies
As the demand for higher density and performance in PCBs continues to grow, new trends and technologies are emerging in the field of innerlayer imaging. Some notable developments include:
1. Advanced Imaging Methods
New imaging methods are being developed to enable finer feature sizes, higher aspect ratios, and better resolution. Examples include:
- Extreme ultraviolet (EUV) lithography
- Nanoimprint lithography
- Directed self-assembly (DSA) of block copolymers
These methods offer the potential for sub-10 nm feature sizes and 3D structures, but they are still in the research and development stage for PCB applications.
2. Additive Manufacturing
Additive manufacturing, also known as 3D printing, is gaining attention as a potential alternative to traditional subtractive methods for PCB fabrication. Some advantages of additive manufacturing include:
- Ability to create complex 3D structures and non-planar circuits
- Reduced waste and environmental impact
- Faster prototyping and customization
However, additive manufacturing still faces challenges in terms of material compatibility, resolution, and throughput for PCB applications.
3. Automation and Industry 4.0
The trend towards automation and digitalization, known as Industry 4.0, is transforming the PCB manufacturing landscape. Some examples of how this is impacting innerlayer imaging include:
- Implementation of robotic systems for material handling and transport
- Integration of sensors and data analytics for real-time process monitoring and control
- Use of artificial intelligence (AI) and machine learning (ML) for defect detection and yield optimization
These technologies can help improve efficiency, quality, and flexibility in the innerlayer imaging process.
FAQ
1. What is the minimum feature size achievable with photolithography for innerlayer imaging?
The minimum feature size achievable with photolithography depends on various factors, such as the wavelength of the light source, the type of photoresist, and the exposure and development conditions. In general, modern PCB photolithography systems can achieve feature sizes down to around 50-100 µm. Advanced systems using laser direct imaging (LDI) or multiple patterning techniques can push this limit down to around 10-20 µm.
2. How does the choice of dielectric material affect the innerlayer imaging process?
The choice of dielectric material can affect the innerlayer imaging process in several ways. First, the surface roughness and adhesion properties of the dielectric can impact the copper foil lamination and photoresist application. Second, the thermal and mechanical properties of the dielectric can affect the dimensional stability and registration accuracy during the imaging and etching processes. Finally, the electrical properties of the dielectric, such as the dielectric constant and loss tangent, can impact the signal integrity and impedance control of the final PCB.
3. What are some common defects that can occur during innerlayer imaging, and how can they be prevented?
Some common defects that can occur during innerlayer imaging include:
- Misregistration or misalignment of the layers
- Undercut or overetching of the copper features
- Pinholes, cracks, or residues in the photoresist
- Incomplete or non-uniform etching
- Contamination or oxidation of the copper surface
To prevent these defects, it is important to:
- Implement strict process controls and monitoring
- Use high-quality materials and equipment
- Follow best practices for design, handling, and storage
- Perform regular maintenance, calibration, and cleaning
- Implement advanced inspection and testing methods
4. How does direct imaging differ from traditional photolithography for innerlayer imaging?
Direct imaging differs from traditional photolithography in several ways. In photolithography, the circuit pattern is transferred onto the photoresist using a physical photomask or phototool. This requires the creation of a separate mask for each layer and design change, which can be time-consuming and costly. In contrast, direct imaging uses a digital image file to directly expose the photoresist, eliminating the need for physical masks. This allows for faster and more flexible design changes, as well as higher resolution and finer feature sizes. However, direct imaging systems can be more expensive and complex than traditional photolithography equipment.
5. What are some emerging technologies that could impact the future of innerlayer imaging for PCBs?
Some emerging technologies that could impact the future of innerlayer imaging for PCBs include:
- Advanced imaging methods, such as extreme ultraviolet (EUV) lithography, nanoimprint lithography, and directed self-assembly (DSA) of block copolymers, which could enable sub-10 nm feature sizes and 3D structures.
- Additive manufacturing, or 3D printing, which could allow for the creation of complex 3D circuits and non-planar structures, as well as reduced waste and faster prototyping.
- Automation and digitalization, or Industry 4.0, which could enable real-time process monitoring and control, defect detection and yield optimization, and flexible and agile manufacturing.
However, these technologies are still in the early stages of development and face challenges in terms of cost, scalability, and reliability for PCB applications.
Conclusion
Innerlayer imaging is a critical step in the manufacturing of multilayer PCBs, directly impacting the quality, reliability, and performance of the final product. By understanding the various methods, materials, and best practices involved in innerlayer imaging, PCB manufacturers can optimize their processes and overcome common challenges.
As the demand for higher density and performance in PCBs continues to grow, new trends and technologies are emerging that could transform the field of innerlayer imaging. From advanced imaging methods to additive manufacturing and automation, these developments offer the potential for
Leave a Reply