Introduction to Induction Heating
Induction heating is a fast, efficient, and non-contact method of heating electrically conductive materials. It relies on the principle of electromagnetic induction to generate heat within the target material. Induction heating has found widespread applications in various industries, including metallurgy, manufacturing, and even in household appliances.
At the heart of an induction heating system is the Induction Heater Circuit, which consists of a power source, a work coil, and the workpiece to be heated. The work coil plays a crucial role in the efficiency and effectiveness of the heating process.
In this article, we will delve into the working principle of induction heater circuits, the design considerations for work coils, and the diverse applications of induction heating technology.
Working Principle of Induction Heater Circuits
Electromagnetic Induction
Induction heating relies on the principle of electromagnetic induction, discovered by Michael Faraday in 1831. When an alternating current (AC) flows through a conductor, it generates a magnetic field around it. If another electrically conductive material is placed within this magnetic field, the fluctuating magnetic field induces eddy currents within the material.
These eddy currents, which are essentially circulating electrical currents, flow through the resistance of the material, generating heat due to Joule heating. The amount of heat generated depends on factors such as the intensity of the magnetic field, the frequency of the alternating current, and the electrical and magnetic properties of the workpiece.
Skin Effect and Penetration Depth
In induction heating, the induced eddy currents tend to concentrate near the surface of the workpiece, a phenomenon known as the skin effect. The depth to which the eddy currents penetrate the material is called the penetration depth or skin depth.
The penetration depth depends on the frequency of the alternating current and the electrical and magnetic properties of the workpiece. Higher frequencies result in shallower penetration depths, while lower frequencies allow for deeper penetration. The penetration depth δ can be calculated using the following formula:
δ = √(ρ / (πfμ))
where:
– ρ is the electrical resistivity of the workpiece material
– f is the frequency of the alternating current
– μ is the magnetic permeability of the workpiece material
The skin effect has important implications for the design of work coils and the selection of operating frequencies for different applications.
Design of Induction Heater Work Coils
Types of Work Coils
Work coils come in various shapes and configurations, depending on the specific application and the geometry of the workpiece. Some common types of work coils include:
-
Solenoid Coils: These are the most basic and widely used type of work coils. They consist of a helical winding of copper tubing or wire around a cylindrical former. Solenoid coils are suitable for heating cylindrical workpieces such as bars, tubes, and rods.
-
Pancake Coils: Pancake coils are flat, spiral-wound coils that are used for heating flat surfaces or thin workpieces. They provide uniform heating over a large area and are commonly used in applications such as hardening, brazing, and bonding.
-
Channel Coils: Channel coils are used for heating specific regions or patterns on a workpiece. They consist of a shaped copper channel that conforms to the desired heating pattern. Channel coils are often used in selective hardening applications.
-
Split Coils: Split coils are designed to facilitate easy loading and unloading of the workpiece. They consist of two or more segments that can be opened and closed around the workpiece. Split coils are commonly used in high-volume production applications.
-
Hairpin Coils: Hairpin coils are used for heating specific areas or edges of a workpiece. They consist of a U-shaped copper tube or bar that concentrates the magnetic field in a localized region. Hairpin coils are often used in edge hardening applications.
The choice of work coil depends on factors such as the shape and size of the workpiece, the desired heating pattern, and the production requirements.
Coil Design Considerations
When designing work coils for induction heating, several key factors must be considered to ensure optimal performance and efficiency:
-
Coil Geometry: The geometry of the work coil should be designed to match the shape and size of the workpiece. The coil should provide uniform heating coverage and minimize any gaps or variations in the magnetic field.
-
Number of Turns: The number of turns in the work coil determines the intensity of the magnetic field generated. Increasing the number of turns increases the field strength but also increases the coil impedance. The optimal number of turns depends on the desired heating rate, the power supply capabilities, and the workpiece properties.
-
Coil Diameter: The diameter of the work coil affects the coupling efficiency between the coil and the workpiece. A smaller coil diameter provides better coupling but may limit the size of the workpiece that can be heated. A larger coil diameter allows for heating larger workpieces but may reduce the coupling efficiency.
-
Coil Pitch: The pitch of the work coil, which is the distance between adjacent turns, influences the uniformity of the magnetic field. A tighter pitch provides more uniform heating but increases the coil impedance. A looser pitch reduces the coil impedance but may result in less uniform heating.
-
Coil Material: The work coil is typically made of copper due to its high electrical conductivity and resistance to oxidation. However, in high-temperature applications, other materials such as tungsten or molybdenum may be used.
-
Cooling: Work coils generate significant heat during operation due to resistive losses. Adequate cooling is essential to prevent overheating and ensure the longevity of the coil. Cooling can be achieved through the use of water-cooled coils, air cooling, or other cooling methods.
-
Insulation: The work coil must be properly insulated to prevent electrical short circuits and to protect the coil from damage. High-temperature insulation materials such as ceramic or silicone are commonly used.
-
Shielding: In some cases, magnetic shielding may be necessary to prevent the magnetic field from interfering with nearby electronic devices or to focus the field on specific areas of the workpiece.
The design of work coils is a complex process that requires careful consideration of these factors and may involve computational modeling and experimental validation to optimize performance.
Impedance Matching
Impedance matching is a critical aspect of induction heater circuit design. The work coil and the power source should be matched in terms of impedance to ensure maximum power transfer and efficiency.
The impedance of the work coil depends on its geometry, the number of turns, and the operating frequency. The power source, typically a high-frequency inverter, has a certain output impedance that must be matched to the coil impedance.
Impedance matching can be achieved through the use of matching networks, such as capacitor banks or transformers. These components are designed to transform the coil impedance to match the output impedance of the power source.
Proper impedance matching ensures that the maximum power is delivered to the work coil and minimizes reflections and losses in the system. It also helps to protect the power source from damage due to impedance mismatches.
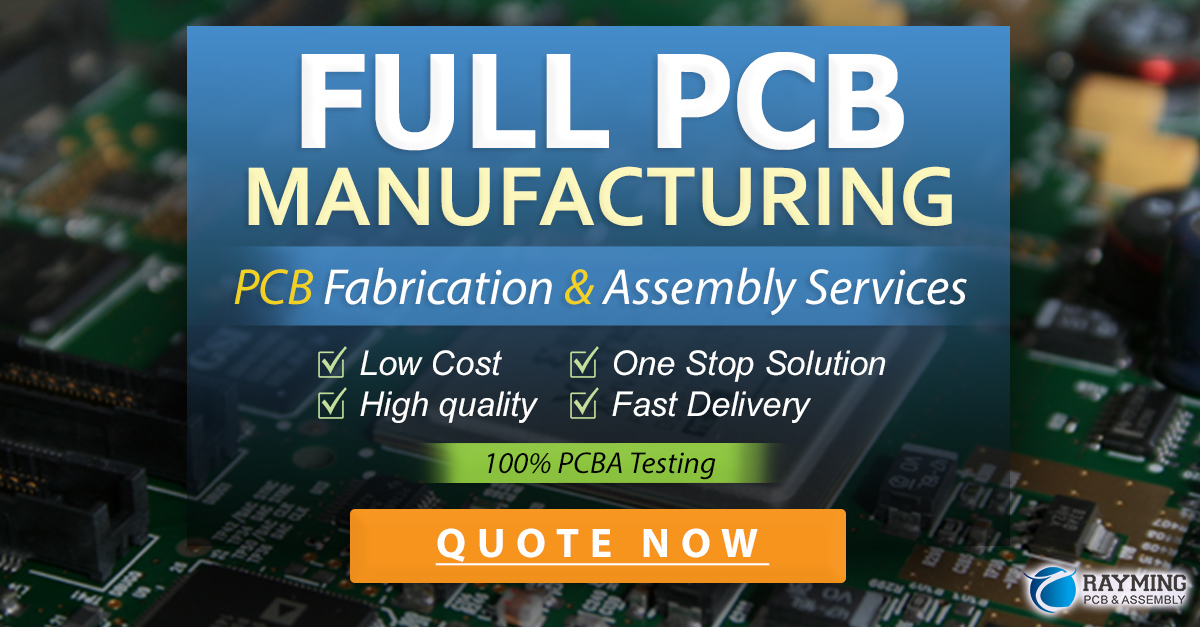
Applications of Induction Heating
Induction heating finds applications in a wide range of industries and processes. Some common applications include:
-
Metal Hardening: Induction heating is extensively used for surface hardening of steel components. By rapidly heating the surface layer of the workpiece followed by quenching, a hard and wear-resistant surface can be achieved while maintaining a ductile core. Induction hardening is commonly used for gears, shafts, and other machine parts.
-
Brazing and Soldering: Induction heating provides a fast and controlled method for brazing and soldering. The localized heating capability of induction allows for precise control over the joint area, minimizing thermal distortion and improving the quality of the joint.
-
Forging and Forming: Induction heating is used in forging and forming processes to preheat the workpiece before shaping. Induction preheating helps to reduce forging forces, improve material flow, and minimize die wear.
-
Shrink Fitting: Induction heating is employed in shrink fitting applications, where a component is heated to expand its diameter and then shrunk onto another component for a tight fit. This technique is commonly used for assembling bearings, gears, and other interference fit components.
-
Annealing and Stress Relieving: Induction heating is used for annealing and stress relieving of metal components. By heating the workpiece to a specific temperature and then allowing it to cool slowly, residual stresses can be relieved, and the material properties can be improved.
-
Heating of Non-Metals: While induction heating is primarily used for heating metals, it can also be applied to heating non-metallic materials such as plastics, ceramics, and composites. In these cases, susceptors or induction-friendly additives are often used to enable heating.
-
Domestic Applications: Induction heating is increasingly used in household appliances such as induction cooktops and water heaters. Induction cooktops provide fast, efficient, and safe cooking by directly heating the cookware through magnetic induction.
The selection of the appropriate induction heating system and work coil design depends on the specific application, material properties, and production requirements.
FAQ
1. What is the main advantage of induction heating over other heating methods?
Induction heating offers several advantages over other heating methods:
– Fast heating rates: Induction heating can heat workpieces very quickly due to the direct heating of the material.
– Energy efficiency: Induction heating is highly energy-efficient, as the heat is generated directly within the workpiece, minimizing losses.
– Precise control: Induction heating allows for precise control over the heating process, enabling selective heating of specific areas or patterns.
– Non-contact heating: Induction heating is a non-contact method, reducing the risk of contamination and allowing for heating of inaccessible or delicate parts.
2. Can induction heating be used for non-metallic materials?
While induction heating is primarily used for heating electrically conductive materials like metals, it can also be applied to non-metallic materials in certain cases. This is achieved by using susceptors or induction-friendly additives that are mixed with the non-metallic material. The susceptors absorb the electromagnetic energy and convert it into heat, which is then transferred to the surrounding non-metallic material.
3. How does the frequency of the alternating current affect induction heating?
The frequency of the alternating current has a significant impact on induction heating. Higher frequencies result in shallower penetration depths, concentrating the heating effect near the surface of the workpiece. This is useful for applications like surface hardening, where only the surface layer needs to be heated. Lower frequencies, on the other hand, allow for deeper penetration of the induced currents, heating the workpiece more uniformly throughout its thickness. The choice of frequency depends on the specific application, material properties, and the desired heating pattern.
4. What is the purpose of impedance matching in induction heater circuits?
Impedance matching is crucial in induction heater circuits to ensure maximum power transfer and efficiency. The work coil and the power source have their own impedances, and for optimal performance, these impedances should be matched. Impedance matching is achieved through the use of matching networks, such as capacitor banks or transformers, which transform the coil impedance to match the output impedance of the power source. Proper impedance matching minimizes reflections and losses in the system, protects the power source from damage, and ensures that the maximum power is delivered to the work coil for efficient heating.
5. What are some common cooling methods used for induction heater work coils?
Induction heater work coils generate significant heat during operation due to resistive losses, and adequate cooling is essential to prevent overheating and ensure the longevity of the coil. Some common cooling methods used for work coils include:
– Water cooling: The work coil is made from hollow copper tubing, and water is circulated through the coil to absorb the heat.
– Air cooling: Compressed air or fans are used to blow air over the work coil, removing the heat through convection.
– Oil cooling: The work coil is immersed in a cooling oil, which absorbs the heat and dissipates it through an external heat exchanger.
– Spray cooling: A cooling fluid is sprayed directly onto the work coil to remove the heat.
The choice of cooling method depends on factors such as the power level, the coil geometry, and the operating environment.
Conclusion
Induction heating is a versatile and efficient technology that has revolutionized various industries. The induction heater circuit, with its work coil, forms the core of this technology. Understanding the working principle of induction heating, the design considerations for work coils, and the diverse applications of induction heating is essential for engineers and professionals working in this field.
By carefully designing the work coil geometry, selecting the appropriate operating frequency, and ensuring proper impedance matching, optimal heating performance can be achieved. Induction heating offers numerous advantages, including fast heating rates, energy efficiency, precise control, and non-contact heating.
As technology advances, induction heating continues to find new applications and improvements. With ongoing research and development, the capabilities of induction heating are expanding, enabling more efficient and innovative heating solutions across various sectors.
In conclusion, induction heating and the design of work coils play a critical role in modern manufacturing and industrial processes. By leveraging the principles of electromagnetic induction and optimizing the induction heater circuit, industries can benefit from faster, more precise, and more efficient heating methods, leading to improved productivity and product quality.
Application | Frequency Range | Penetration Depth |
---|---|---|
Surface hardening | 10-500 kHz | 0.2-2 mm |
Through heating | 1-10 kHz | 2-20 mm |
Forging and forming | 1-10 kHz | 5-50 mm |
Brazing and soldering | 100-500 kHz | 0.2-2 mm |
Annealing and stress relieving | 1-10 kHz | 2-20 mm |
Table 1: Typical frequency ranges and penetration depths for different induction heating applications.
Coil Type | Application |
---|---|
Solenoid Coil | Cylindrical workpieces (bars, tubes, rods) |
Pancake Coil | Flat surfaces, thin workpieces |
Channel Coil | Specific regions or patterns |
Split Coil | High-volume production, easy loading/unloading |
Hairpin Coil | Specific areas or edges |
Table 2: Common types of work coils and their applications.
Leave a Reply