Introduction to PCB Quality
Printed Circuit Boards (PCBs) are the backbone of modern electronics. They are used in almost every electronic device, from smartphones and laptops to medical equipment and aerospace systems. The quality of a PCB directly impacts the performance, reliability, and longevity of the electronic device it powers. Therefore, ensuring the highest quality of PCBs is crucial for any electronics manufacturer.
In this article, we will explore the various aspects of PCB quality and how we can guarantee the quality of your PCB. We will discuss the importance of PCB quality, the factors that affect it, and the measures we take to ensure that every PCB we manufacture meets the highest quality standards.
Why is PCB Quality Important?
PCB quality is essential for several reasons:
-
Reliability: A high-quality PCB ensures that the electronic device it powers functions reliably without any issues. Poor quality PCBs can lead to device failures, malfunctions, and even safety hazards.
-
Performance: The quality of a PCB directly impacts the performance of the electronic device. A well-designed and manufactured PCB ensures optimal signal integrity, power distribution, and heat dissipation, resulting in better device performance.
-
Longevity: High-quality PCBs have a longer lifespan compared to poor quality ones. They can withstand harsh environmental conditions, such as high temperatures, humidity, and vibrations, without deteriorating over time.
-
Cost-effectiveness: Investing in high-quality PCBs can save costs in the long run. Poor quality PCBs are more likely to fail, leading to costly repairs, replacements, and product recalls.
Factors Affecting PCB Quality
Several factors can affect the quality of a PCB. These include:
1. Design
The design of a PCB is crucial for its quality. A well-designed PCB takes into account various factors such as signal integrity, power distribution, thermal management, and manufacturability. Poor design choices can lead to issues such as signal interference, power fluctuations, and manufacturing defects.
2. Material Selection
The choice of materials used in a PCB can significantly impact its quality. High-quality PCB materials, such as FR-4, ensure better insulation, thermal stability, and mechanical strength. Cheaper, low-quality materials can lead to issues such as delamination, warping, and poor signal integrity.
3. Manufacturing Process
The manufacturing process used to fabricate a PCB plays a vital role in its quality. A well-controlled and optimized manufacturing process ensures consistent quality across all PCBs. Poor manufacturing practices, such as improper etching, drilling, or soldering, can lead to defects and reliability issues.
4. Testing and Inspection
Thorough testing and inspection are essential to ensure the quality of a PCB. Various tests, such as electrical testing, visual inspection, and environmental testing, help identify any defects or issues before the PCB is assembled into the final product. Skipping or inadequate testing can lead to quality issues going unnoticed.
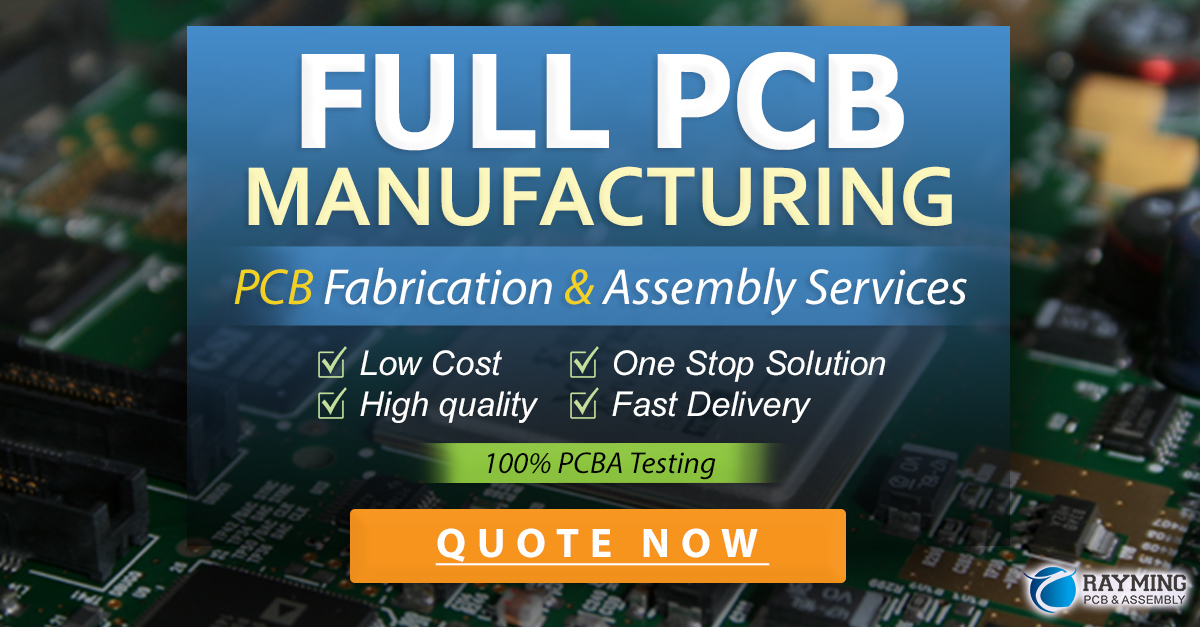
Measures to Guarantee PCB Quality
At our company, we take several measures to guarantee the quality of every PCB we manufacture:
1. Robust Design Process
Our experienced design team follows a robust design process to ensure that every PCB is designed for optimal performance, reliability, and manufacturability. We use state-of-the-art design tools and techniques, such as signal integrity analysis and thermal simulation, to validate the design before manufacturing.
2. Stringent Material Selection
We only use high-quality, industry-standard materials in our PCBs. Our material selection process involves rigorous testing and verification to ensure that the materials meet our strict quality standards. We also work closely with our suppliers to ensure a consistent supply of high-quality materials.
3. Advanced Manufacturing Facilities
Our manufacturing facilities are equipped with the latest equipment and technology to ensure consistent and high-quality PCB fabrication. We follow industry best practices and standards, such as IPC-A-600, to maintain tight process control and minimize defects.
4. Multi-stage Testing and Inspection
We employ a multi-stage testing and inspection process to catch any quality issues early in the manufacturing process. Our testing includes:
- Automated Optical Inspection (AOI) to detect surface defects
- In-Circuit Testing (ICT) to verify the electrical functionality of the PCB
- Flying Probe Testing (FPT) for high-precision electrical testing
- X-ray inspection to detect internal defects and voids
- Functional testing to validate the PCB’s performance in the final product
5. Continuous Improvement
We are committed to continuous improvement in our processes and quality management system. We regularly review our performance metrics, such as defect rates and customer feedback, to identify areas for improvement. We also invest in training and development of our employees to keep them updated with the latest industry trends and best practices.
FAQ
1. What certifications do you have for your PCB manufacturing process?
We are certified to ISO 9001:2015 for our quality management system and ISO 14001:2015 for our environmental management system. We also comply with various industry standards such as IPC-A-600, IPC-A-610, and IPC-6012.
2. Can you manufacture PCBs with special requirements, such as high-frequency or high-voltage applications?
Yes, we have experience in manufacturing PCBs for various specialized applications. Our design and manufacturing teams work closely with customers to understand their specific requirements and develop custom solutions.
3. What is your typical lead time for PCB manufacturing?
Our lead times depend on various factors such as the complexity of the design, the materials used, and the order quantity. Typically, our lead times range from 2-3 weeks for standard PCBs and 4-6 weeks for complex or customized PCBs.
4. How do you handle quality issues or customer complaints?
We have a dedicated quality assurance team that investigates any quality issues or customer complaints. We follow a structured problem-solving approach, such as 8D or PDCA, to identify the root cause of the issue and implement corrective and preventive actions. We also maintain open communication with our customers throughout the process to ensure their satisfaction.
5. Can you provide prototyping services for PCBs?
Yes, we offer prototyping services for PCBs. We understand the importance of prototyping in the product development process and offer quick-turn prototyping services with lead times as short as 24 hours.
Conclusion
PCB quality is a critical factor in the success of any electronic product. At our company, we are committed to delivering the highest quality PCBs to our customers. Through our robust design process, stringent material selection, advanced manufacturing facilities, multi-stage testing and inspection, and continuous improvement efforts, we ensure that every PCB we manufacture meets the highest quality standards.
In Part 2 of this article, we will delve deeper into some of the advanced techniques and technologies we use to guarantee PCB quality, such as signal integrity analysis, thermal management, and reliability testing. Stay tuned!
PCB Quality Aspect | Description |
---|---|
Design | A well-designed PCB takes into account signal integrity, power distribution, thermal management, and manufacturability |
Material Selection | High-quality PCB materials, such as FR-4, ensure better insulation, thermal stability, and mechanical strength |
Manufacturing Process | A well-controlled and optimized manufacturing process ensures consistent quality across all PCBs |
Testing and Inspection | Thorough testing and inspection, such as AOI, ICT, FPT, and X-ray, help identify any defects or issues before the PCB is assembled into the final product |
Leave a Reply