What Are PCB Heat Sinks?
PCB (Printed Circuit Board) heat sinks are essential components used to dissipate excess heat generated by electronic components on a PCB. They are designed to prevent overheating, which can lead to component failure and reduced overall system performance. Heat sinks are typically made from materials with high thermal conductivity, such as aluminum or copper, and are attached to the heat-generating components using thermal adhesive or mechanical fasteners.
Types of PCB Heat Sinks
- Extruded Heat Sinks
- Manufactured through an extrusion process
- Consist of fins or pins to increase surface area
-
Commonly used for high-power applications
-
Stamped Heat Sinks
- Created by stamping a metal sheet
- Offer a cost-effective solution for low-power applications
-
Limited in terms of heat dissipation capacity
-
Bonded Fin Heat Sinks
- Constructed by bonding fins to a base plate
- Provide excellent heat dissipation performance
-
Suitable for high-power applications with limited space
-
Forged Heat Sinks
- Manufactured through a forging process
- Offer high strength and thermal conductivity
- Ideal for demanding applications with high mechanical stress
Factors Affecting PCB Heat Sink Performance
Several factors influence the effectiveness of a PCB heat sink in dissipating excess heat:
- Material Properties
- Thermal conductivity: Higher thermal conductivity allows for better heat transfer.
-
Specific heat capacity: Higher specific heat capacity enables the heat sink to absorb more heat before its temperature rises.
-
Surface Area
- Increased surface area allows for more efficient heat dissipation.
-
Fins, pins, or other protrusions can be added to increase the surface area.
-
Airflow
- Adequate airflow is crucial for effective heat dissipation.
-
Forced convection using fans can significantly improve heat sink performance.
-
Thermal Interface Material (TIM)
- TIM fills the gaps between the heat sink and the heat-generating component.
-
Proper application of TIM ensures efficient heat transfer from the component to the heat sink.
-
Mounting Pressure
- Sufficient mounting pressure ensures proper contact between the heat sink and the component.
- Inadequate pressure can result in air gaps, reducing heat transfer efficiency.
Calculating Required Heat Sink Size
To determine if a PCB heat sink is sufficient, you need to calculate the required heat sink size based on the following parameters:
- Power dissipation of the component (P)
- Maximum allowable component temperature (Tmax)
- Ambient temperature (Ta)
- Thermal resistance of the heat sink (Rhs)
The thermal resistance of the required heat sink can be calculated using the following formula:
Rhs = (Tmax – Ta) / P
Once you have calculated the required thermal resistance, you can select a heat sink with a thermal resistance value equal to or lower than the calculated value.
Example Calculation
Let’s consider an example where a component dissipates 10 watts of power, has a maximum allowable temperature of 80°C, and operates in an ambient temperature of 25°C.
Given:
– P = 10 W
– Tmax = 80°C
– Ta = 25°C
Step 1: Calculate the required thermal resistance of the heat sink.
Rhs = (Tmax – Ta) / P
Rhs = (80°C – 25°C) / 10 W
Rhs = 5.5°C/W
Step 2: Select a heat sink with a thermal resistance equal to or lower than 5.5°C/W.
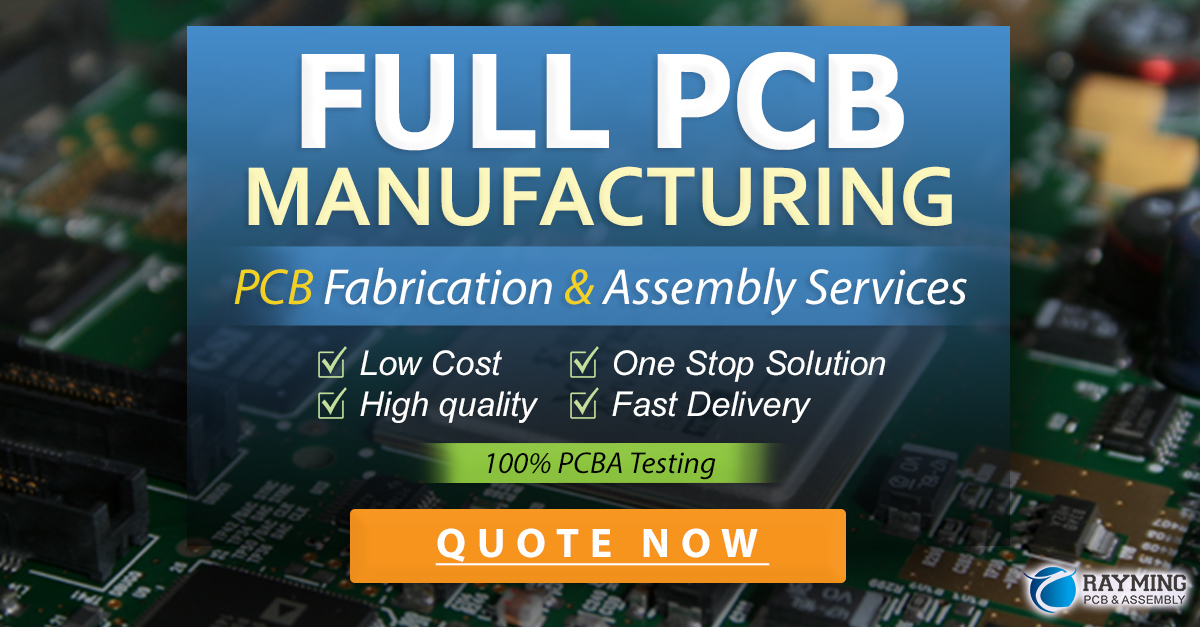
Experimental Verification
After selecting a heat sink based on the calculated thermal resistance, it is essential to verify its performance through experimental testing. This involves monitoring the component temperature under actual operating conditions to ensure that it remains within the specified limits.
Temperature Measurement Techniques
- Thermocouples
- Consist of two dissimilar metals joined together at one end
- Generate a voltage proportional to the temperature difference between the junction and the reference point
-
Offer accurate temperature measurements over a wide range
-
Resistance Temperature Detectors (RTDs)
- Utilize the change in electrical resistance of a material with temperature
- Provide high accuracy and stability
-
Commonly used in industrial applications
-
Infrared Thermography
- Non-contact temperature measurement technique
- Uses an infrared camera to detect the infrared energy emitted by an object
- Provides a visual representation of the temperature distribution
Test Setup and Procedure
- Attach the heat sink to the heat-generating component using the appropriate thermal interface material and mounting mechanism.
- Install temperature sensors (thermocouples, RTDs, or infrared camera) to monitor the component and heat sink temperatures.
- Apply power to the system and allow it to reach steady-state conditions.
- Record the temperature readings at regular intervals.
- Compare the measured temperatures with the maximum allowable component temperature.
If the measured temperatures remain below the maximum allowable limit, the selected heat sink is sufficient for the application. If the temperatures exceed the limit, a larger heat sink or additional cooling methods (e.g., forced air cooling) may be necessary.
FAQ
-
Q: What is the purpose of a PCB heat sink?
A: A PCB heat sink is used to dissipate excess heat generated by electronic components on a PCB, preventing overheating and ensuring optimal system performance. -
Q: What materials are commonly used for PCB heat sinks?
A: PCB heat sinks are typically made from materials with high thermal conductivity, such as aluminum or copper. -
Q: How do I calculate the required heat sink size for my application?
A: To calculate the required heat sink size, you need to know the power dissipation of the component, the maximum allowable component temperature, the ambient temperature, and the desired thermal resistance of the heat sink. Use the formula Rhs = (Tmax – Ta) / P to determine the required thermal resistance. -
Q: What is the importance of thermal interface material in heat sink installation?
A: Thermal interface material (TIM) fills the gaps between the heat sink and the heat-generating component, ensuring efficient heat transfer. Proper application of TIM is crucial for optimal heat sink performance. -
Q: How can I verify if a selected heat sink is sufficient for my application?
A: To verify the performance of a selected heat sink, conduct experimental testing by monitoring the component temperature under actual operating conditions. If the measured temperatures remain within the specified limits, the heat sink is sufficient for the application.
Leave a Reply