Understanding QFP Solder Bridging
What is QFP Solder Bridging?
QFP solder bridging is an unwanted connection of solder between two or more adjacent pins on a QFP package. This connection creates a short circuit, which can lead to device malfunction or failure. Solder bridging is a common issue in surface-mount soldering, especially with fine-pitch components like QFPs.
Causes of QFP Solder Bridging
Several factors can contribute to the formation of solder bridges on QFP packages:
- Excessive solder: Applying too much solder can cause it to flow between adjacent pins, creating bridges.
- Improper solder paste stencil design: An incorrectly designed solder paste stencil can result in excessive solder paste deposition.
- Incorrect reflow profile: An improper reflow profile can cause the solder to flow uncontrollably, leading to bridging.
- Component misalignment: Misaligned components can cause solder to flow between pins during the reflow process.
- Contamination: Flux residue, dirt, or other contaminants on the PCB or component can contribute to solder bridging.
Prevention Techniques for QFP Solder Bridging
Proper Solder Paste Stencil Design
A well-designed solder paste stencil is crucial for preventing QFP solder bridging. Consider the following factors when designing your stencil:
- Aperture size: Ensure that the aperture size is appropriate for the component’s pitch and size. Consult the component manufacturer’s recommendations for optimal aperture dimensions.
- Aperture shape: Use aperture shapes that promote proper solder paste release, such as rounded corners or tapered walls.
- Stencil thickness: Choose an appropriate stencil thickness based on the solder paste’s viscosity and the component’s pitch. Thinner stencils are generally better for fine-pitch components.
Component Pitch | Recommended Stencil Thickness |
---|---|
0.5mm | 0.100mm – 0.125mm |
0.4mm | 0.100mm – 0.115mm |
0.3mm | 0.075mm – 0.100mm |
Optimizing Reflow Profile
An optimal reflow profile is essential for achieving proper solder joint formation and minimizing the risk of solder bridging. Consider the following guidelines:
- Preheat stage: Ensure a gradual and controlled ramp-up to the desired preheat temperature to evaporate solvents and activate the flux.
- Soak stage: Maintain a stable temperature to allow the PCB and components to reach thermal equilibrium before entering the reflow stage.
- Reflow stage: Choose a peak temperature and time above liquidus that allows for proper solder joint formation without causing excessive solder flow or intermetallic growth.
- Cooling stage: Ensure a controlled cool-down rate to minimize thermal stress and prevent solder joint defects.
Reflow Stage | Typical Temperature Range | Duration |
---|---|---|
Preheat | 150°C – 180°C | 60-90 sec |
Soak | 180°C – 200°C | 60-120 sec |
Reflow | 220°C – 250°C (peak) | 30-90 sec |
Cooling | < 6°C/sec | As required |
Ensuring Proper Component Alignment
Proper component alignment is crucial for preventing solder bridging. Use the following techniques to ensure accurate placement:
- Vision systems: Employ machine vision systems to verify component alignment before and after placement.
- Placement accuracy: Ensure that your pick-and-place machine is calibrated and capable of placing components with high accuracy.
- Fiducial Markers: Use fiducial markers on the PCB to provide reference points for accurate component placement.
- Tooling holes: Incorporate tooling holes in the PCB design to ensure precise alignment during the assembly process.
Maintaining Cleanliness
Contamination on the PCB or components can contribute to solder bridging. Implement the following cleanliness practices:
- Handling: Use clean gloves when handling PCBs and components to avoid introducing contaminants.
- Cleaning: Regularly clean and maintain your soldering equipment, including stencils, squeegees, and pick-and-place nozzles.
- Flux selection: Choose a flux that is compatible with your cleaning process and leaves minimal residue.
- Cleaning process: Implement an appropriate cleaning process, such as ultrasonic cleaning or spray cleaning, to remove flux residue and other contaminants after soldering.
Inspection and Rework Techniques
Despite implementing prevention techniques, solder bridging may still occur. Regularly inspect your assemblies and employ the following rework techniques when necessary:
Visual Inspection
Perform visual inspections of the soldered QFP packages using magnification tools, such as microscopes or high-resolution cameras. Look for signs of solder bridging, including:
- Excessive solder between adjacent pins
- Uneven or bulging solder joints
- Solder splatter or balls
Automated Optical Inspection (AOI)
Implement automated optical inspection systems to detect solder bridging and other defects. AOI systems use advanced imaging techniques and algorithms to compare the soldered assembly to a reference image, identifying any deviations or anomalies.
X-Ray Inspection
For complex assemblies or devices with hidden solder joints, use X-ray inspection to detect solder bridging. X-ray systems allow you to view the internal structure of the solder joints, identifying any bridging or voids that may not be visible through visual inspection.
Manual Rework
If solder bridging is detected, manual rework may be necessary. Use the following tools and techniques for effective rework:
- Soldering iron: Use a fine-tipped soldering iron with adjustable temperature control to remove excess solder and separate bridged pins.
- Solder wick: Employ solder wick, also known as desoldering braid, to absorb excess solder from the bridged area.
- Flux: Apply additional flux to the rework area to promote proper solder flow and prevent re-bridging.
- Magnification: Use magnification tools to ensure precise rework and avoid damaging adjacent pins or components.
Automated Rework Systems
For high-volume production or complex rework tasks, consider using automated rework systems. These systems use advanced technology, such as laser or hot-air, to remove excess solder and perform precise rework operations. Automated rework systems can improve efficiency, consistency, and quality compared to manual rework methods.
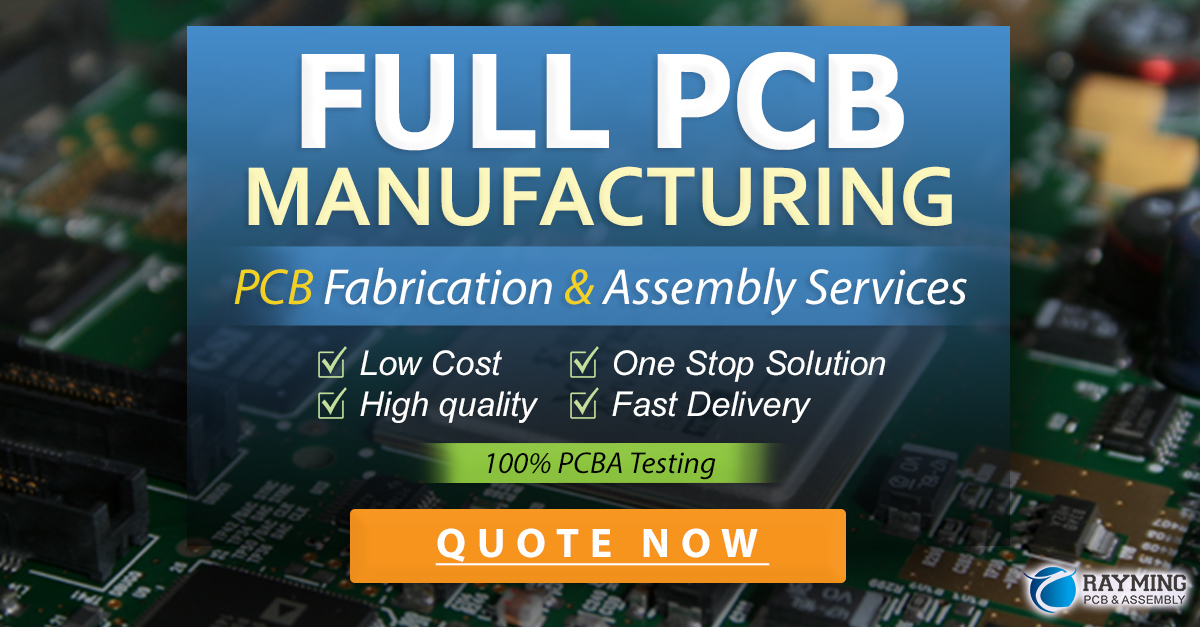
Frequently Asked Questions (FAQ)
-
Q: What is the main cause of QFP solder bridging?
A: The main cause of QFP solder bridging is excessive solder applied to the pins, which can be due to improper solder paste stencil design, incorrect reflow profile, or component misalignment. -
Q: How can I prevent QFP solder bridging during the assembly process?
A: To prevent QFP solder bridging, ensure proper solder paste stencil design, optimize the reflow profile, maintain cleanliness, and use techniques to ensure accurate component alignment, such as vision systems and fiducial markers. -
Q: What are some methods for inspecting QFP packages for solder bridging?
A: Visual inspection using magnification tools, automated optical inspection (AOI), and X-ray inspection are common methods for detecting solder bridging in QFP packages. -
Q: How can I rework QFP packages with solder bridging?
A: Manual rework using a fine-tipped soldering iron, solder wick, flux, and magnification tools can be effective for resolving solder bridging. For high-volume production or complex rework tasks, automated rework systems using laser or hot-air technology may be more suitable. -
Q: Can solder bridging cause permanent damage to the QFP package or the PCB?
A: Yes, solder bridging can cause permanent damage to the QFP package or the PCB if left unresolved. Short circuits created by solder bridges can lead to device malfunction, overheating, or even component failure. It is crucial to detect and rework solder bridging promptly to avoid potential damage.
Conclusion
QFP solder bridging is a common issue in surface-mount soldering that can lead to device malfunction and potential damage. By understanding the causes of solder bridging and implementing appropriate prevention techniques, such as proper solder paste stencil design, optimized reflow profile, component alignment, and cleanliness, you can minimize the occurrence of solder bridging in your assembly process.
Regular inspection using visual, automated optical, or X-ray methods is essential for detecting solder bridging. When necessary, employ manual or automated rework techniques to remove excess solder and resolve bridging issues.
By following the guidelines and techniques discussed in this article, you can effectively solve the problem of QFP solder bridging, improve the quality and reliability of your assemblies, and reduce the risk of device failure.
Leave a Reply