Introduction to ESD in SMT Assembly
Electrostatic discharge (ESD) is a common phenomenon that can cause significant damage to electronic components during the surface mount technology (SMT) assembly process. ESD occurs when there is a sudden transfer of electrostatic charge between two objects with different electrical potentials. In the context of SMT assembly, ESD can damage sensitive electronic components, leading to reduced reliability, performance issues, and even complete failure of the assembled products.
To prevent ESD damage in SMT assembly, it is essential to understand the causes, effects, and preventive measures. This article will provide a comprehensive guide on how to prevent ESD damage in the SMT assembly process, covering various aspects such as ESD-safe workstations, personnel grounding, material handling, and more.
Understanding the Causes of ESD in SMT Assembly
Triboelectric Charging
Triboelectric charging is one of the primary causes of ESD in SMT assembly. It occurs when two materials come into contact and then separate, resulting in a transfer of electrons from one material to the other. The material that loses electrons becomes positively charged, while the material that gains electrons becomes negatively charged. Common sources of triboelectric charging in SMT assembly include:
- Walking across a floor
- Handling components or PCBs
- Using non-ESD-safe packaging materials
- Rubbing of clothing against the skin
Induction Charging
Induction charging occurs when an electrically charged object is brought near a conductive object, causing a redistribution of charges on the conductive object’s surface. In SMT assembly, induction charging can occur when:
- Charged operators handle conductive components or PCBs
- Charged objects, such as tools or equipment, are brought near conductive components or PCBs
Conductive Charging
Conductive charging occurs when a charged object comes into direct contact with a conductive object, resulting in a transfer of charge. In SMT assembly, conductive charging can occur when:
- Charged operators touch conductive components or PCBs
- Charged tools or equipment come into contact with conductive components or PCBs
Effects of ESD on Electronic Components in SMT Assembly
ESD can cause various types of damage to electronic components in SMT assembly, ranging from subtle performance degradation to complete failure. The severity of the damage depends on factors such as the level of charge, the sensitivity of the component, and the duration of the discharge.
Latent Defects
Latent defects are a type of ESD damage that may not be immediately apparent but can lead to premature failure of the component. Examples of latent defects include:
- Increased leakage current
- Reduced insulation resistance
- Altered device parameters
Catastrophic Failures
Catastrophic failures are a type of ESD damage that result in immediate and permanent damage to the component. Examples of catastrophic failures include:
- Dielectric breakdown
- Melted or vaporized metallization
- Thermal damage
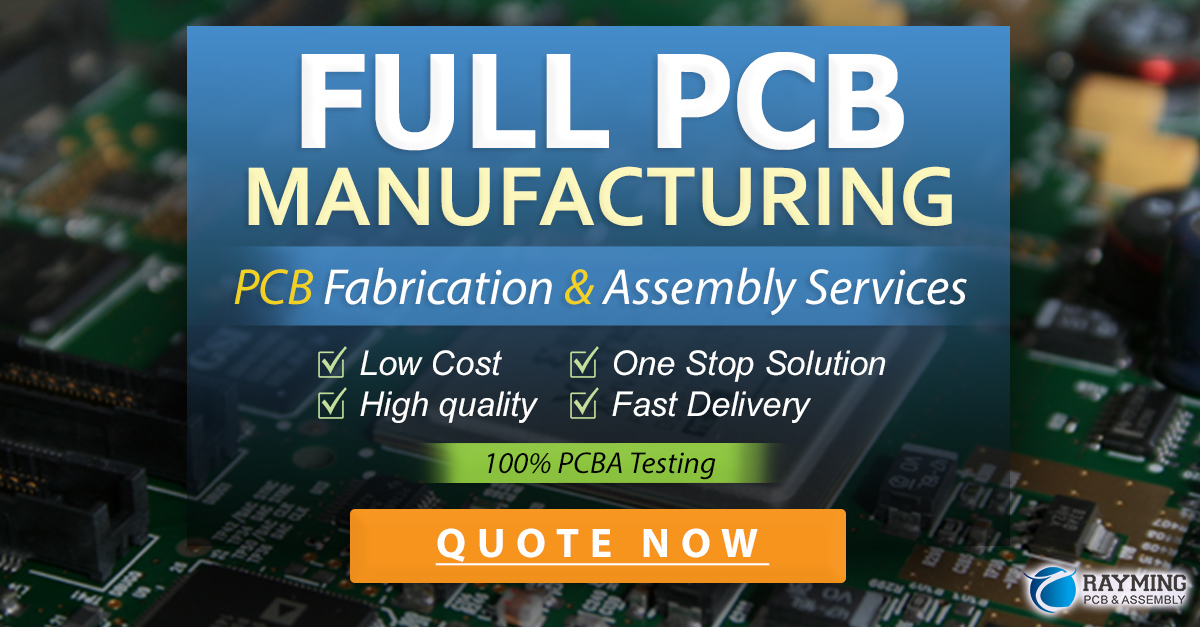
ESD Sensitivity of Common Electronic Components
Different electronic components have varying levels of sensitivity to ESD. Understanding the sensitivity of the components used in your SMT assembly process is crucial for implementing effective ESD Prevention measures.
Component Type | ESD Sensitivity |
---|---|
MOSFET | High |
CMOS | High |
Op-amp | Medium |
Resistor | Low |
Capacitor | Low to Medium |
ESD-Safe Workstations
An ESD-safe workstation is a crucial element in preventing ESD damage in SMT assembly. A well-designed ESD-safe workstation should include the following components:
ESD-Safe Work Surfaces
ESD-safe work surfaces are designed to dissipate electrostatic charges, preventing the buildup of charge on the components and PCBs being handled. Common types of ESD-safe work surfaces include:
- Dissipative mats
- Conductive mats
- Dissipative tabletops
Personnel Grounding
Personnel grounding is essential for preventing ESD damage caused by charged operators. Proper personnel grounding can be achieved through the use of:
- ESD-safe wrist straps
- ESD-safe foot straps
- ESD-safe shoes
Ionizers
Ionizers are devices that generate positive and negative ions, neutralizing electrostatic charges in the surrounding air. Ionizers can be used to reduce the risk of ESD damage caused by charged objects or materials in the work area.
ESD-Safe Material Handling
Proper handling of materials is essential for preventing ESD damage in SMT assembly. ESD-safe material handling practices include:
ESD-Safe Packaging
ESD-safe packaging is designed to protect sensitive components from ESD damage during storage and transportation. Common types of ESD-safe packaging include:
- Static shielding bags
- Conductive foam
- Dissipative trays
ESD-Safe Handling Tools
ESD-safe handling tools are designed to prevent the transfer of electrostatic charges between the operator and the components being handled. Examples of ESD-safe handling tools include:
- ESD-safe tweezers
- ESD-safe vacuum pens
- ESD-safe gloves
ESD Training and Awareness
Effective ESD prevention in SMT assembly requires a well-trained and aware workforce. ESD training should cover topics such as:
- Fundamentals of ESD
- ESD-safe workstation setup and maintenance
- ESD-safe material handling practices
- ESD-safe personal protective equipment (PPE)
Regular refresher training and audits should be conducted to ensure that ESD prevention practices are being followed consistently.
ESD Monitoring and Testing
To ensure the effectiveness of ESD prevention measures in SMT assembly, regular monitoring and testing should be performed. This can include:
- Workstation resistance testing
- Personnel grounding testing
- Ionizer performance testing
- ESD event monitoring
By regularly monitoring and testing ESD prevention measures, potential issues can be identified and addressed before they lead to ESD damage.
Frequently Asked Questions (FAQ)
-
What is the most common cause of ESD damage in SMT assembly?
The most common cause of ESD damage in SMT assembly is triboelectric charging, which occurs when two materials come into contact and then separate, resulting in a transfer of electrons. -
How can I tell if a component has been damaged by ESD?
ESD damage can be difficult to detect, as it may result in latent defects that are not immediately apparent. However, catastrophic failures, such as dielectric breakdown or thermal damage, can be visually identified. -
Are all electronic components equally sensitive to ESD?
No, different electronic components have varying levels of sensitivity to ESD. Components such as MOSFETs and CMOS devices are highly sensitive, while resistors and capacitors are generally less sensitive. -
Can ESD damage occur even if I can’t feel a static discharge?
Yes, ESD damage can occur even if the discharge is not perceptible to the human senses. Some components can be damaged by discharges as low as 20-30 volts. -
How often should ESD prevention measures be tested and monitored?
The frequency of ESD testing and monitoring depends on factors such as the sensitivity of the components being handled and the level of ESD risk in the work environment. As a general guideline, ESD prevention measures should be tested and monitored at least quarterly, with more frequent testing in high-risk environments.
Conclusion
Preventing ESD damage in SMT assembly is essential for ensuring the reliability and performance of electronic products. By understanding the causes and effects of ESD, implementing ESD-safe workstations and material handling practices, and providing regular training and monitoring, manufacturers can effectively minimize the risk of ESD damage in their assembly processes.
As electronic components continue to become smaller and more sensitive, the importance of effective ESD prevention will only continue to grow. By staying up-to-date with the latest ESD prevention technologies and best practices, manufacturers can stay ahead of the curve and deliver high-quality, reliable products to their customers.
Leave a Reply