Understanding Flexible-heater Technology
Before diving into optimization techniques, it’s crucial to understand the basics of flexible-heater technology. Flexible-heaters are thin, lightweight, and can conform to various shapes and sizes. They typically consist of a heating element, such as a resistive wire or conductive ink, sandwiched between layers of insulation and protective materials.
Types of Flexible-heaters
There are several types of flexible-heaters, each with its own unique characteristics and applications:
- Silicone Rubber Heaters
- Polyimide Film Heaters
- Kapton Heaters
- Mica Heaters
- Carbon Fiber Heaters
Type | Characteristics | Applications |
---|---|---|
Silicone Rubber | High flexibility, moisture-resistant | Aerospace, medical devices |
Polyimide Film | Thin, lightweight, high-temperature resistance | Electronics, battery heating |
Kapton | Excellent insulation, high-temperature resistance | Aerospace, semiconductor processing |
Mica | High-temperature resistance, good thermal conductivity | Industrial heating, cooking appliances |
Carbon Fiber | Lightweight, high strength-to-weight ratio | Aerospace, automotive, sports equipment |
Factors Affecting Flexible-heater Performance
Several factors can impact the performance of flexible-heaters:
- Material selection
- Heating element design
- Insulation and protective layers
- Power density and wattage
- Temperature control and regulation
Optimizing Flexible-heater Design
Proper design is crucial for maximizing the value of flexible-heaters. Consider the following aspects when optimizing flexible-heater design:
Heating Element Configuration
The configuration of the heating element can significantly impact the heater’s performance. Some common configurations include:
- Serpentine pattern
- Etched foil
- Printed ink
- Wire-wound
Choose the configuration that best suits your application, considering factors such as heat distribution, flexibility, and power requirements.
Material Selection
Select materials that are compatible with your application’s requirements, such as temperature range, chemical resistance, and mechanical properties. Common materials include:
- Silicone rubber
- Polyimide film
- Mica
- Kapton
- Carbon fiber
Consider the trade-offs between cost, performance, and durability when selecting materials.
Insulation and Protective Layers
Proper insulation and protective layers are essential for ensuring the safety and longevity of flexible-heaters. Consider the following:
- Electrical insulation
- Thermal insulation
- Moisture resistance
- Abrasion and puncture resistance
Choose materials and thicknesses that provide adequate protection without compromising flexibility or heat transfer.
Enhancing Flexible-heater Efficiency
Improving the efficiency of flexible-heaters can lead to energy savings, longer lifespan, and better overall performance. Consider the following strategies:
Power Density Optimization
Power density refers to the amount of power (wattage) per unit area of the heater. Optimizing power density involves finding the right balance between heat output and heater size. Too high a power density can lead to hotspots and premature failure, while too low a power density may result in insufficient heating.
Temperature Control and Regulation
Accurate temperature control and regulation are essential for maintaining consistent performance and preventing overheating. Consider implementing the following:
- Thermostats
- Temperature sensors
- PID controllers
- Feedback loops
Choose control methods that are appropriate for your application’s requirements and budget.
Thermal Interface Materials
Thermal interface materials (TIMs) are used to enhance heat transfer between the heater and the object being heated. TIMs can help improve efficiency by reducing thermal resistance and ensuring uniform heat distribution. Common TIMs include:
- Thermal greases
- Thermal pads
- Phase change materials
- Thermal adhesives
Select TIMs based on their thermal conductivity, ease of application, and compatibility with your heater materials.
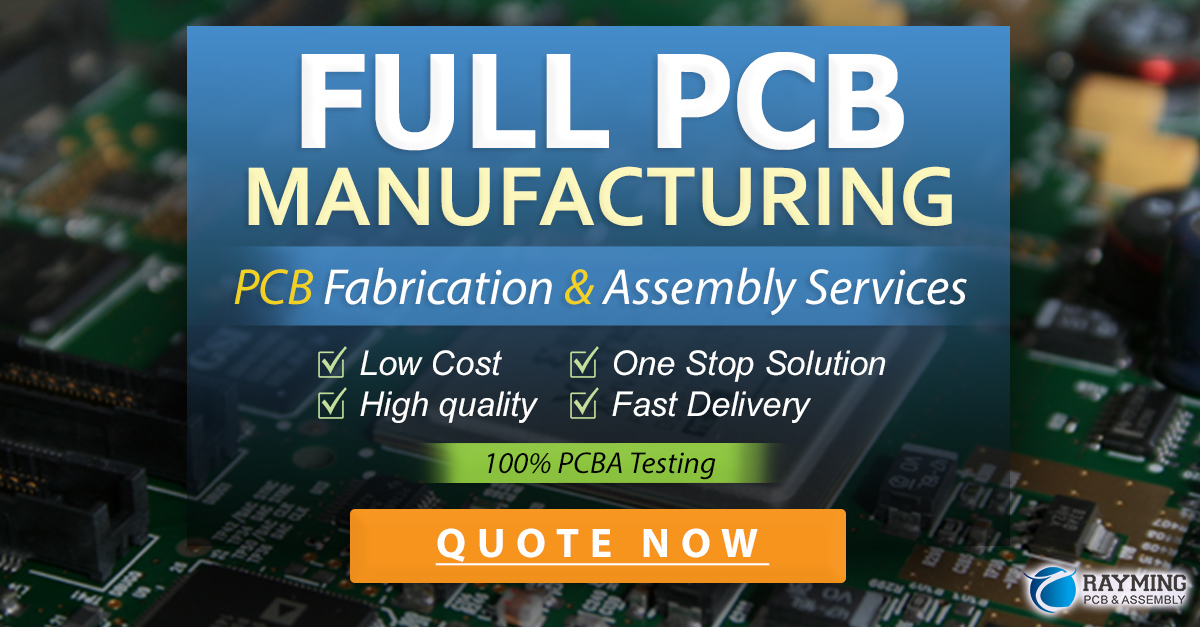
Integration and Assembly Considerations
Proper integration and assembly of flexible-heaters are crucial for ensuring optimal performance and reliability. Consider the following:
Mechanical Attachment
Choose an attachment method that is secure, yet allows for the necessary flexibility and movement. Common methods include:
- Adhesives
- Mechanical fasteners
- Snap-fits
- Overmolding
Consider the environmental conditions and mechanical stresses the heater will be subjected to when selecting an attachment method.
Electrical Connections
Reliable electrical connections are essential for the proper functioning of flexible-heaters. Consider the following:
- Wire gauge and material
- Connector type and rating
- Strain relief
- Insulation and shielding
Ensure that electrical connections are secure, protected from environmental factors, and able to withstand the expected mechanical stresses.
Testing and Quality Control
Thorough testing and quality control are essential for ensuring the performance and reliability of flexible-heaters. Consider the following:
- Resistance and continuity testing
- Insulation resistance testing
- Thermal imaging
- Lifecycle testing
- Environmental testing
Implement a robust quality control process to identify and address any issues before the heaters are put into service.
Maintenance and Troubleshooting
Proper maintenance and troubleshooting can help extend the lifespan of flexible-heaters and ensure optimal performance. Consider the following:
Regular Inspections
Conduct regular visual inspections of flexible-heaters to identify any signs of damage, wear, or contamination. Look for:
- Cracks or tears in insulation
- Discoloration or charring
- Loose or damaged connections
- Foreign debris or contaminants
Address any issues promptly to prevent further damage or performance degradation.
Cleaning and Care
Proper cleaning and care can help maintain the performance and longevity of flexible-heaters. Follow the manufacturer’s recommendations for cleaning methods and frequency. Generally, consider the following:
- Use mild detergents and soft cloths
- Avoid abrasive or corrosive cleaners
- Protect heaters from moisture and contaminants
- Store heaters in a clean, dry environment when not in use
Regular cleaning and care can help prevent build-up of contaminants that can degrade heater performance over time.
Troubleshooting Common Issues
If a flexible-heater is not performing as expected, consider the following troubleshooting steps:
- Check for visible damage or contamination
- Verify proper electrical connections and continuity
- Ensure proper power supply and control settings
- Check for any changes in environmental conditions
- Consult the manufacturer’s troubleshooting guide or support resources
By systematically addressing potential issues, you can often identify and resolve problems with flexible-heaters quickly and efficiently.
Frequently Asked Questions (FAQ)
-
What is the typical lifespan of a flexible-heater?
The lifespan of a flexible-heater can vary depending on factors such as material quality, power density, and environmental conditions. With proper design, integration, and maintenance, flexible-heaters can last for several years or even decades in some applications. -
Can flexible-heaters be custom-designed for specific applications?
Yes, flexible-heaters can be custom-designed to meet the specific requirements of an application. Factors such as size, shape, power density, and temperature range can be tailored to optimize performance for a particular use case. -
How do I select the right flexible-heater for my application?
When selecting a flexible-heater, consider factors such as the required temperature range, power density, environmental conditions, and mechanical requirements. Consult with a reputable manufacturer or supplier to discuss your specific needs and get recommendations for the most suitable heater type and configuration. -
What safety considerations should I keep in mind when working with flexible-heaters?
Safety is paramount when working with flexible-heaters. Always follow the manufacturer’s guidelines for installation, operation, and maintenance. Ensure proper electrical insulation and grounding, use appropriate personal protective equipment, and monitor heaters for any signs of damage or malfunction. Comply with all relevant industry standards and regulations. -
How can I optimize the energy efficiency of my flexible-heater system?
To optimize energy efficiency, consider strategies such as power density optimization, accurate temperature control, and the use of thermal interface materials. Regular maintenance and inspection can also help identify and address any issues that may be impacting efficiency. Work with a qualified engineer or supplier to develop a comprehensive efficiency optimization plan.
Conclusion
Flexible-heaters are a versatile and valuable component in many industries, offering a wide range of benefits such as compact size, lightweight design, and conformability. By understanding the key principles of flexible-heater technology, optimizing design and efficiency, and implementing proper integration, maintenance, and troubleshooting practices, you can maximize the value of flexible-heaters in your applications.
Remember to consider factors such as material selection, heating element configuration, insulation and protection, power density, temperature control, and thermal interface materials when designing and optimizing flexible-heaters. Regular inspections, cleaning, and care can help extend the lifespan and maintain the performance of these essential components.
By following the strategies and best practices outlined in this article, you can unlock the full potential of flexible-heaters and make them a most valuable asset in your industry or application.
Leave a Reply