Introduction to PCB Design and Manufacturing
Printed Circuit Boards (PCBs) are the backbone of modern electronics. They are used in almost every electronic device, from smartphones and laptops to industrial equipment and medical devices. PCBs provide a way to mechanically support and electrically connect electronic components using conductive pathways, tracks, or signal traces etched from copper sheets laminated onto a non-conductive substrate.
Designing and manufacturing a custom PCB can be a complex process, but with the right tools and knowledge, anyone can create their own custom PCB. In this guide, we will cover everything you need to know about designing and manufacturing a custom PCB.
Understanding PCB Basics
What is a PCB?
A PCB is a printed circuit board that is used to mechanically support and electrically connect electronic components. It consists of a non-conductive substrate, typically made of fiberglass or other composite materials, and conductive pathways, tracks, or signal traces etched from copper sheets laminated onto the substrate.
Types of PCBs
There are several types of PCBs, each with its own unique characteristics and applications:
PCB Type | Description | Applications |
---|---|---|
Single-sided PCB | Has conductive traces on one side of the substrate | Simple, low-cost projects |
Double-sided PCB | Has conductive traces on both sides of the substrate | More complex projects that require higher density |
Multi-layer PCB | Has multiple layers of conductive traces separated by insulating layers | High-density, complex projects |
Flexible PCB | Uses a flexible substrate that can be bent or folded | Wearable electronics, medical devices |
Rigid-Flex PCB | Combines rigid and flexible sections | High-reliability applications, such as aerospace and military |
PCB Materials
The choice of materials for a PCB is critical to its performance and reliability. The most common materials used in PCBs are:
Material | Description | Properties |
---|---|---|
FR-4 | Fiberglass-reinforced epoxy laminate | High strength, good insulation, low cost |
Polyimide | High-temperature polymer | Excellent thermal stability, high flexibility |
PTFE | Polytetrafluoroethylene (Teflon) | Low dielectric constant, low loss at high frequencies |
Aluminum | Metal substrate | Excellent thermal conductivity, high strength |
PCB Design Process
Schematic Design
The first step in designing a custom PCB is to create a schematic diagram. A schematic is a graphical representation of the electronic circuit, showing the components and their interconnections. There are several software tools available for creating schematic diagrams, such as Eagle, KiCad, and Altium Designer.
PCB Layout
Once the schematic is complete, the next step is to create the PCB layout. The layout determines the physical placement of the components on the PCB and the routing of the conductive traces between them. PCB layout software, such as Eagle, KiCad, and Altium Designer, can be used to create the layout.
Design Considerations
When designing a custom PCB, there are several important considerations to keep in mind:
- Component placement: Components should be placed in a way that minimizes the length of the conductive traces and reduces the risk of electromagnetic interference (EMI).
- Trace width and spacing: The width and spacing of the conductive traces should be chosen based on the current and voltage requirements of the circuit, as well as the manufacturing capabilities of the PCB fabricator.
- Via placement: Vias are used to connect traces on different layers of the PCB. They should be placed in a way that minimizes the length of the conductive traces and reduces the risk of signal integrity issues.
- Grounding and shielding: Proper grounding and shielding techniques should be used to reduce EMI and ensure signal integrity.
Design Rules Check (DRC)
Before sending the PCB design to a fabricator, it is important to run a Design Rules Check (DRC) to ensure that the design meets the manufacturing capabilities of the fabricator. The DRC checks for issues such as minimum trace width and spacing, minimum drill size, and maximum aspect ratio.
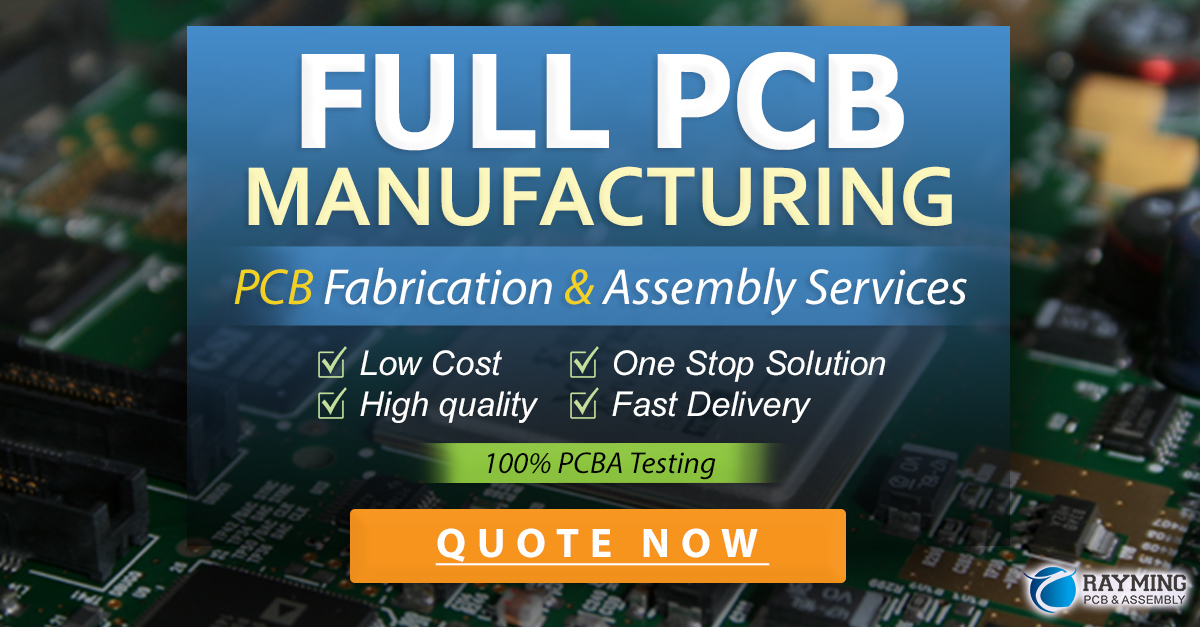
PCB Manufacturing Process
PCB Fabrication
Once the PCB design is complete and has passed the DRC, it can be sent to a PCB fabricator for manufacturing. The fabrication process typically involves the following steps:
- Printing the PCB layout onto a photoresist film
- Laminating the photoresist film onto the copper-clad substrate
- Exposing the photoresist to UV light through a photomask
- Developing the photoresist to remove the unexposed areas
- Etching away the exposed copper to create the conductive traces
- Drilling holes for through-hole components and vias
- Applying a solder mask to protect the copper traces
- Applying a silkscreen to add text and graphics to the PCB
PCB Assembly
After the PCB has been fabricated, the electronic components can be assembled onto the board. This can be done manually or using automated assembly machines. The assembly process typically involves the following steps:
- Applying solder paste to the PCB pads
- Placing the components onto the PCB
- Reflowing the solder paste to create a permanent connection between the components and the PCB
- Inspecting the assembled PCB for defects
PCB Testing
Once the PCB has been assembled, it should be tested to ensure that it functions as intended. There are several types of tests that can be performed, depending on the complexity of the PCB and the requirements of the application:
Test Type | Description |
---|---|
Visual inspection | Checking for obvious defects, such as missing or misaligned components |
Continuity test | Checking for open or short circuits between pins or pads |
Functional test | Checking that the PCB performs its intended function |
Boundary scan test | Using a special test fixture to test the interconnections between components |
In-circuit test | Using a bed-of-nails test fixture to test individual components and circuits |
PCB Design Tools
There are several software tools available for designing and manufacturing custom PCBs. Some of the most popular tools include:
Eagle
Eagle is a popular PCB design tool that is available in both free and paid versions. It includes a schematic editor, a PCB layout editor, and a autorouter. Eagle is known for its ease of use and extensive library of components.
KiCad
KiCad is a free and open-source PCB design tool that includes a schematic editor, a PCB layout editor, and a 3D viewer. It is known for its powerful features and active community of users.
Altium Designer
Altium Designer is a professional-grade PCB design tool that includes a schematic editor, a PCB layout editor, and a 3D viewer. It is known for its advanced features and integration with other design tools.
Frequently Asked Questions (FAQ)
What is the difference between a PCB and a breadboard?
A breadboard is a prototyping tool that allows you to quickly and easily create temporary circuits without soldering. A PCB, on the other hand, is a permanent circuit board that is used to mechanically support and electrically connect electronic components.
Can I design a PCB without using a software tool?
While it is possible to design a PCB by hand, it is much easier and more efficient to use a software tool. PCB design software allows you to create complex designs quickly and easily, and ensures that your design meets the manufacturing capabilities of the PCB fabricator.
How much does it cost to manufacture a custom PCB?
The cost of manufacturing a custom PCB depends on several factors, such as the size and complexity of the board, the number of layers, and the quantity ordered. In general, small, simple PCBs can cost as little as a few dollars each, while larger, more complex boards can cost hundreds or even thousands of dollars.
What is the turnaround time for manufacturing a custom PCB?
The turnaround time for manufacturing a custom PCB depends on the complexity of the board and the workload of the PCB fabricator. In general, small, simple PCBs can be manufactured in a few days, while larger, more complex boards may take several weeks.
Can I assemble my own PCB?
Yes, it is possible to assemble your own PCB, but it requires specialized equipment and skills. If you are new to PCB assembly, it may be easier and more cost-effective to have your PCB assembled by a professional assembly house.
Conclusion
Designing and manufacturing a custom PCB can be a complex process, but with the right tools and knowledge, anyone can create their own custom PCB. By understanding the basics of PCB design and manufacturing, and using the right software tools and fabrication services, you can bring your electronic projects to life.
Whether you are a hobbyist, a student, or a professional engineer, learning how to design and manufacture custom PCBs is a valuable skill that can open up new opportunities and possibilities. With this guide, you now have everything you need to know to get started on your own custom PCB project.
Leave a Reply