Understanding Relay Connections
A relay is an electromagnetic switch that allows you to control a high-current circuit with a low-current signal. It is a crucial component in many electrical and electronic systems, including automotive, industrial, and home automation applications. To ensure that your relay functions efficiently and reliably, it is essential to understand the proper way to connect it.
Types of Relays
There are several types of relays available, each with its own specific characteristics and applications. Some common types include:
- Electromechanical Relays (EMRs)
- Solid-State Relays (SSRs)
- Reed Relays
- Time-Delay Relays
- Latching Relays
Relay Type | Switching Mechanism | Typical Applications |
---|---|---|
Electromechanical (EMR) | Mechanical contacts | General-purpose, automotive, industrial |
Solid-State (SSR) | Semiconductor | High-speed switching, power control |
Reed | Magnetic contacts | Low-current, high-speed switching |
Time-Delay | Mechanical/Electronic | Delayed switching, timing control |
Latching | Mechanical contacts | Bi-stable switching, power conservation |
Relay Terminology
To properly connect a relay, it is important to understand the basic terminology associated with its components and functions:
- Coil: The electromagnet that actuates the relay when energized
- Contacts: The conductive elements that open or close the controlled circuit
- Normally Open (NO): Contacts that are open when the relay is de-energized
- Normally Closed (NC): Contacts that are closed when the relay is de-energized
- Common (COM): The shared terminal for both NO and NC contacts
- Voltage Rating: The nominal coil voltage required to energize the relay
- Current Rating: The maximum current the relay contacts can handle safely
- Switching Capacity: The maximum power (voltage × current) the relay can switch
Relay Connection Basics
Identifying Relay Terminals
The first step in connecting a relay is to identify its terminals. Most relays have the following terminal designations:
- Coil terminals: Usually labeled as “+” and “-” or “A1” and “A2”
- Contact terminals: Labeled as “NO” (Normally Open), “NC” (Normally Closed), and “COM” (Common)
Refer to the relay’s datasheet or markings on the relay itself to identify the correct terminals.
Connecting the Relay Coil
To energize the relay, you need to connect the coil terminals to a suitable power source. Follow these steps:
- Determine the voltage rating of the relay coil (e.g., 5V, 12V, 24V).
- Connect the positive (+) terminal of the power source to the positive coil terminal.
- Connect the negative (-) terminal of the power source to the negative coil terminal.
It is important to ensure that the power source voltage matches the relay coil voltage rating to avoid damaging the relay or causing malfunction.
Connecting the Relay Contacts
The relay contacts are used to switch the controlled circuit. Follow these steps to connect the contacts:
- Identify the type of contact you need for your application (NO, NC, or both).
- Connect the common (COM) terminal to one side of the controlled circuit.
- For a normally open (NO) connection, connect the other side of the controlled circuit to the NO terminal.
- For a normally closed (NC) connection, connect the other side of the controlled circuit to the NC terminal.
Remember that the relay contacts are electrically isolated from the coil, allowing you to switch a high-voltage or high-current circuit with a low-voltage control signal.
Protection and Safety Considerations
Coil Suppression
When a relay coil is de-energized, the collapsing magnetic field can induce a high-voltage spike across the coil terminals. This voltage spike can damage the controlling device or cause electromagnetic interference (EMI). To protect the circuit, it is recommended to use a coil suppression method:
-
Diode Suppression: Connect a diode (e.g., 1N4001) across the coil terminals, with the cathode to the positive terminal and the anode to the negative terminal. This allows the induced current to flow through the diode, suppressing the voltage spike.
-
RC Snubber: Connect a resistor and capacitor in series across the coil terminals. The resistor limits the current, while the capacitor absorbs the energy of the voltage spike. Typical values are 100Ω to 1kΩ for the resistor and 0.1μF to 0.47μF for the capacitor.
Contact Protection
In some cases, the relay contacts may need protection from inductive loads, such as motors or solenoids. When these loads are switched off, they can produce a high-voltage arc across the relay contacts, causing premature wear and failure. To protect the contacts, consider using these methods:
-
Snubber Circuit: Connect a resistor and capacitor in series across the relay contacts. The resistor limits the current, while the capacitor suppresses the voltage spike. Typical values are 10Ω to 100Ω for the resistor and 0.1μF to 1μF for the capacitor.
-
Varistor: Connect a metal oxide varistor (MOV) across the relay contacts. A varistor is a voltage-dependent resistor that offers a low resistance at high voltages, effectively suppressing voltage spikes.
Fuse Protection
To protect the relay contacts and the controlled circuit from overcurrent conditions, it is advisable to use a fuse in series with the common (COM) terminal. The fuse should be rated slightly higher than the maximum expected load current to allow for transient currents while still providing protection against short circuits or overloads.
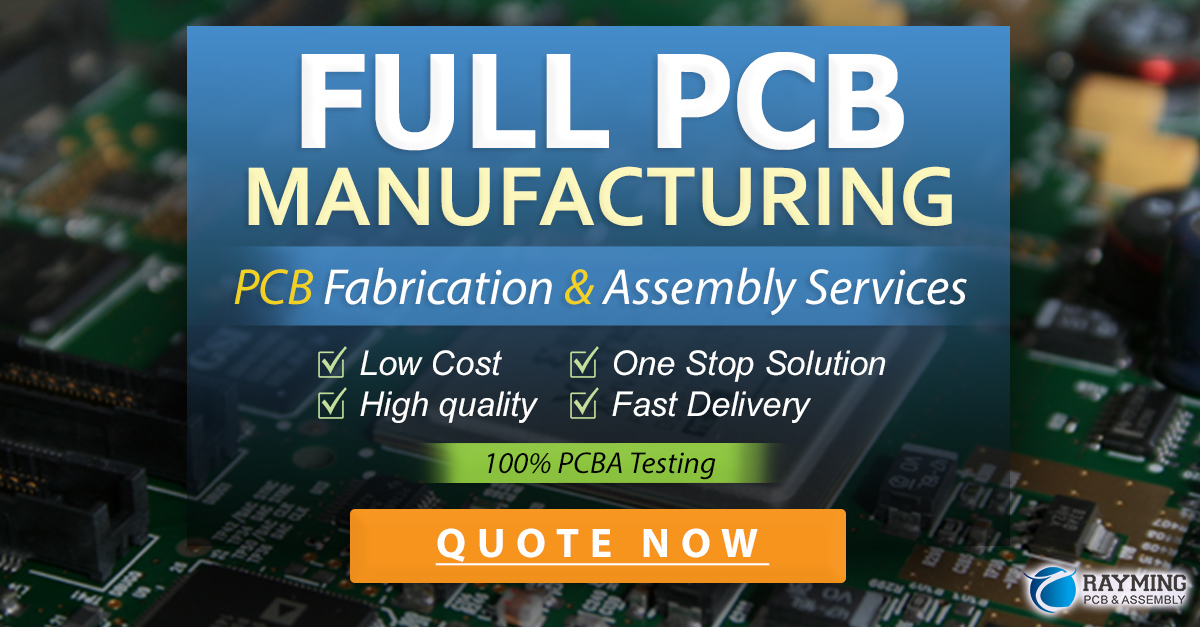
Relay Connection Examples
Example 1: Controlling a Light with a Relay
In this example, we will use a relay to control a 120V AC light using a 5V DC control signal.
- Connect the positive (+) terminal of the 5V DC power source to one of the coil terminals.
- Connect the negative (-) terminal of the 5V DC power source to the other coil terminal.
- Connect the common (COM) terminal of the relay to one side of the 120V AC power source.
- Connect the normally open (NO) terminal of the relay to one terminal of the light.
- Connect the other terminal of the light to the other side of the 120V AC power source.
When the 5V DC control signal is applied to the coil, the relay will energize, closing the NO contact and turning on the light. When the control signal is removed, the relay will de-energize, and the light will turn off.
Example 2: Controlling a Motor with a Relay
In this example, we will use a relay to control a 12V DC motor using a 3.3V DC control signal from a microcontroller.
- Connect the positive (+) terminal of the 3.3V DC control signal to one of the coil terminals.
- Connect the negative (-) terminal of the 3.3V DC control signal to the other coil terminal.
- Connect the common (COM) terminal of the relay to the positive (+) terminal of the 12V DC power source.
- Connect the normally open (NO) terminal of the relay to one terminal of the motor.
- Connect the other terminal of the motor to the negative (-) terminal of the 12V DC power source.
When the 3.3V DC control signal is applied to the coil, the relay will energize, closing the NO contact and supplying power to the motor. When the control signal is removed, the relay will de-energize, and the motor will stop.
Frequently Asked Questions (FAQ)
-
Can I use a relay to switch AC and DC loads?
Yes, relays can switch both AC and DC loads. However, make sure to choose a relay with an appropriate voltage and current rating for your specific application. -
How do I determine the right relay for my project?
To select the appropriate relay, consider the following factors: - Coil voltage and current
- Contact voltage and current ratings
- Switching capacity
- Contact arrangement (SPST, SPDT, DPDT, etc.)
-
Mechanical and electrical life expectancy
-
Can I use a relay to control multiple loads simultaneously?
Yes, you can use a relay with multiple sets of contacts (e.g., DPDT or 3PDT) to control multiple loads simultaneously. Each set of contacts can switch a separate load. -
How do I protect my relay from voltage spikes?
To protect your relay from voltage spikes, use coil suppression methods such as diode suppression or RC snubbers. These methods help to dissipate the energy of the voltage spike and protect the controlling device. -
What is the difference between a relay and a contactor?
Relays and contactors are both electromechanical switches, but contactors are designed for higher current and voltage applications. Contactors typically have larger contacts and are used in high-power industrial settings, while relays are used in lower-power applications.
Conclusion
Connecting a relay efficiently requires understanding the basics of relay terminology, identifying the correct terminals, and following proper connection procedures. By adhering to protection and safety considerations, such as coil suppression, contact protection, and fuse protection, you can ensure that your relay-controlled circuits operate reliably and safely. Always refer to the relay’s datasheet and application notes for specific guidelines and recommendations. With this knowledge, you can confidently integrate relays into your electrical and electronic projects, enabling efficient and effective control of high-current loads with low-current control signals.
Leave a Reply