Introduction
When designing a motion control system, selecting the right motor drive and motor controller is crucial for achieving optimal performance, efficiency, and reliability. The choice of motor drive and controller depends on various factors such as the type of motor being used, the application requirements, and the overall system architecture. In this article, we will discuss the key considerations for choosing a motor drive and motor controller, focusing on the importance of proper Motor Selection.
Understanding Motor Types
Before delving into the selection of motor drives and controllers, it is essential to understand the different types of motors commonly used in industrial applications.
DC Motors
DC motors are widely used in applications that require precise speed control and high torque at low speeds. They are classified into two main categories:
-
Brushed DC Motors: These motors use mechanical commutation with brushes and a commutator to control the current flow. They are simple, low-cost, and easy to control but require regular maintenance due to brush wear.
-
Brushless DC (BLDC) Motors: BLDC motors use electronic commutation, eliminating the need for brushes. They offer higher efficiency, longer lifespan, and reduced maintenance compared to brushed DC motors.
AC Motors
AC motors are popular in industrial applications due to their robustness, reliability, and low maintenance requirements. The two main types of AC motors are:
-
Induction Motors: Induction motors are the most common type of AC motor. They are simple, reliable, and can operate directly from the AC power supply without the need for complex control electronics.
-
Synchronous Motors: Synchronous motors operate at a constant speed determined by the frequency of the AC power supply. They offer precise speed control and high efficiency but require more complex control electronics.
Stepper Motors
Stepper motors are used in applications that require precise positioning and repeatability. They operate by dividing a full rotation into a series of discrete steps, allowing for accurate position control without the need for closed-loop feedback.
Factors to Consider When Selecting a Motor Drive
Voltage and Current Ratings
The voltage and current ratings of the motor drive must match the requirements of the selected motor. The drive should be capable of supplying the necessary voltage and current to the motor under all operating conditions, including peak loads and transient conditions.
Power Output
The power output of the motor drive should be sufficient to meet the power requirements of the motor and the application. It is important to consider the continuous power rating as well as the peak power rating to ensure that the drive can handle both steady-state and transient loads.
Control Features
The motor drive should offer the necessary control features for the specific application. Some common control features include:
- Speed control: The ability to adjust the motor speed according to the application requirements.
- Torque control: The capability to regulate the motor torque for precise force control.
- Position control: The ability to accurately control the motor position for applications that require precise positioning.
- Programmability: The flexibility to customize the drive’s behavior through programming or parameter settings.
Communication Interfaces
Consider the communication interfaces supported by the motor drive. Common communication protocols used in industrial applications include:
- RS-232/RS-485: Serial communication protocols for point-to-point or multi-drop configurations.
- Ethernet: High-speed, networked communication for data exchange and remote monitoring.
- Fieldbus: Industrial communication protocols such as Profibus, DeviceNet, or CANopen for real-time control and data acquisition.
Environmental Factors
The motor drive should be suitable for the intended operating environment. Consider factors such as:
- Temperature range: Ensure that the drive can operate reliably within the expected temperature range.
- Humidity: Consider the humidity level in the operating environment and choose a drive with appropriate protection.
- Vibration and shock: If the drive will be subjected to vibration or shock, select a model with suitable mechanical design and ratings.
Integration and Compatibility
Ensure that the motor drive is compatible with the rest of the system components, including the motor, controller, power supply, and any auxiliary devices. Consider factors such as:
- Mounting options: Verify that the drive can be mounted in the desired location and orientation.
- Wiring and connectors: Check that the drive has the appropriate wiring and connectors for seamless integration with the system.
- Software compatibility: Ensure that the drive’s software and programming tools are compatible with the overall system architecture.
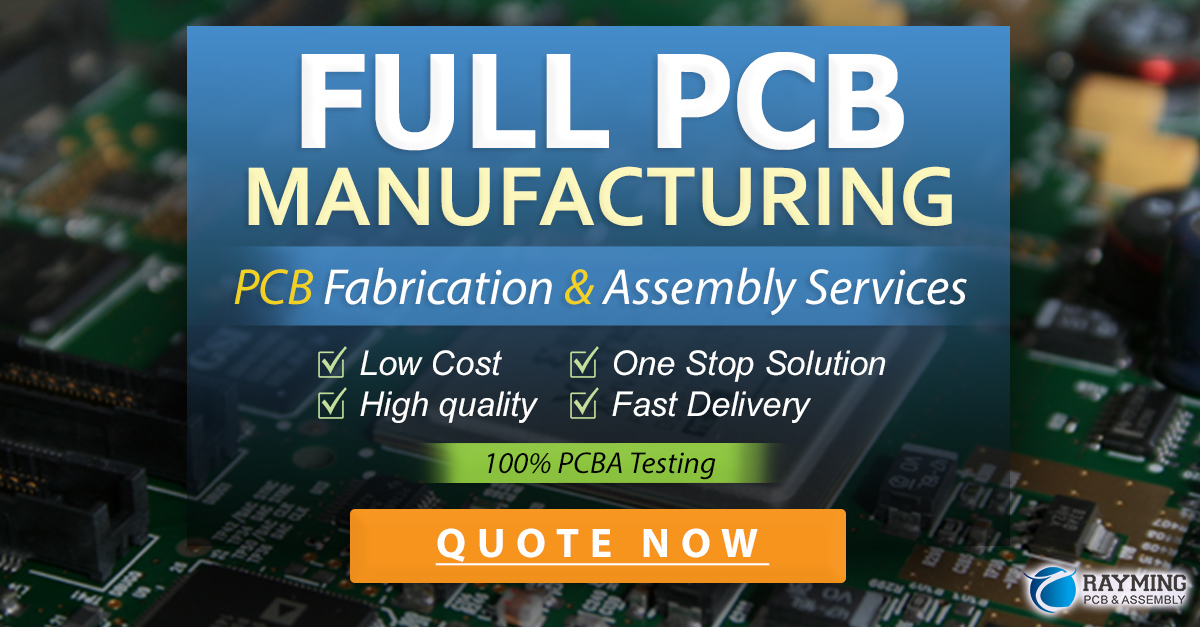
Factors to Consider When Selecting a Motor Controller
Control Architecture
The choice of motor controller depends on the control architecture of the system. Common control architectures include:
- Centralized control: A single controller manages multiple motor drives and coordinates their operation.
- Distributed control: Each motor drive has its own dedicated controller, allowing for modular and scalable system design.
Processing Power
The motor controller should have sufficient processing power to handle the required control algorithms, data processing, and communication tasks. Consider factors such as:
- Processor type and speed: Select a controller with a processor that can handle the computational demands of the application.
- Memory capacity: Ensure that the controller has enough memory to store program code, data, and any required parameters.
I/O Capabilities
The motor controller should have the necessary input/output (I/O) capabilities to interface with sensors, actuators, and other system components. Consider the number and type of I/O channels required, such as:
- Digital inputs and outputs: For discrete control signals and status monitoring.
- Analog inputs and outputs: For reading sensors and controlling analog devices.
- Encoder interfaces: For position and speed feedback from the motor.
Programming and Software
The motor controller should be programmable and offer software tools for application development and configuration. Consider factors such as:
- Programming language: Choose a controller that supports a programming language suitable for the application, such as ladder logic, structured text, or function block diagram.
- Integrated development environment (IDE): Look for a controller with a user-friendly IDE that simplifies program development, debugging, and deployment.
- Libraries and resources: Consider the availability of pre-built libraries, function blocks, and resources that can accelerate application development.
Scalability and Expandability
Consider the scalability and expandability of the motor controller to accommodate future system growth or modifications. Look for controllers that offer:
- Modular design: A modular controller architecture allows for easy expansion by adding additional I/O modules or communication interfaces.
- Networking capabilities: Controllers with built-in networking capabilities enable seamless integration with other system components and facilitate data exchange.
Motor Selection Considerations
Proper motor selection is crucial for achieving optimal performance and efficiency in a motion control system. When selecting a motor, consider the following factors:
Torque and Speed Requirements
Determine the torque and speed requirements of the application. Consider both the continuous torque and peak torque needed, as well as the required speed range. Select a motor that can deliver the necessary torque and speed while operating within its rated specifications.
Power Rating
Evaluate the power rating of the motor based on the application demands. The motor should have sufficient power to handle the required load and acceleration/deceleration profiles. Consider both the continuous power rating and the peak power rating.
Efficiency
Motor efficiency directly impacts the overall system efficiency and energy consumption. Choose a motor with high efficiency to minimize power losses and reduce operating costs. Consider factors such as the motor’s design, materials, and operating point.
Size and Weight
The size and weight of the motor should be compatible with the available space and mounting requirements of the application. Consider the motor’s dimensions, shaft size, and mounting options to ensure proper fitment.
Environmental Factors
Select a motor that can withstand the environmental conditions of the application. Consider factors such as:
- Temperature range: Ensure that the motor can operate reliably within the expected temperature range.
- Ingress protection: Choose a motor with appropriate ingress protection (IP) rating for resistance against dust, moisture, and other contaminants.
- Vibration and shock: If the motor will be subjected to vibration or shock, select a model with suitable mechanical design and ratings.
Feedback Options
Determine the feedback requirements of the application and choose a motor with appropriate feedback options. Common feedback options include:
- Encoder: Provides precise position and speed feedback for closed-loop control.
- Resolver: Offers robust position feedback in harsh environments.
- Tachometer: Provides speed feedback for velocity control.
Integration and System Considerations
When integrating the motor drive and motor controller into the overall system, consider the following aspects:
Wiring and Cabling
Proper wiring and cabling are essential for reliable operation and noise immunity. Use shielded cables for motor power and feedback signals to minimize electromagnetic interference (EMI). Follow the manufacturer’s guidelines for cable routing and grounding practices.
Grounding and Shielding
Implement proper grounding and shielding techniques to reduce EMI and ensure signal integrity. Use dedicated grounding points for the motor drive, controller, and other system components. Follow best practices for cable shielding and termination.
Power Supply
Ensure that the power supply is adequately sized to meet the requirements of the motor drive and controller. Consider the voltage and current ratings, as well as any transient or peak power demands. Use appropriate power conditioning and filtering techniques to maintain power quality.
Safety Considerations
Implement necessary safety features and protocols to protect personnel and equipment. Consider factors such as:
- Emergency stop (E-stop) functionality: Provide a means to quickly stop the motor in case of an emergency.
- Overcurrent and short-circuit protection: Implement protection mechanisms to prevent damage due to excessive current or short-circuit conditions.
- Isolation and disconnection: Use appropriate isolation and disconnection devices to ensure safe maintenance and troubleshooting.
Conclusion
Selecting the right motor drive and motor controller is essential for achieving optimal performance, efficiency, and reliability in a motion control system. By considering factors such as voltage and current ratings, control features, communication interfaces, and environmental factors, you can choose a motor drive that meets the specific requirements of your application.
Similarly, when selecting a motor controller, evaluate the control architecture, processing power, I/O capabilities, and programming options to ensure compatibility with your system needs.
Proper motor selection is equally important, taking into account torque and speed requirements, power rating, efficiency, size and weight, environmental factors, and feedback options.
By carefully considering these factors and following best practices for integration and system design, you can build a robust and efficient motion control system that meets your application requirements.
Frequently Asked Questions (FAQ)
-
Q: What is the difference between a motor drive and a motor controller?
A: A motor drive is responsible for supplying power to the motor and controlling its speed, torque, or position. A motor controller, on the other hand, is a higher-level device that sends commands to the motor drive and coordinates the overall operation of the motion control system. -
Q: Can I use a motor drive with any type of motor?
A: No, the motor drive must be compatible with the specific type of motor being used. Different motor types, such as DC motors, AC motors, and stepper motors, require different drive technologies and control methods. It is important to select a motor drive that matches the characteristics and requirements of the selected motor. -
Q: How do I determine the power rating of the motor drive?
A: The power rating of the motor drive should be based on the power requirements of the motor and the application. Consider the continuous power rating and peak power rating of the motor, as well as any additional power demands from the system. The drive should be capable of supplying the necessary power under all operating conditions. -
Q: What communication interfaces are commonly used with motor controllers?
A: Common communication interfaces used with motor controllers include serial protocols like RS-232 and RS-485, Ethernet for networked communication, and industrial fieldbus protocols such as Profibus, DeviceNet, or CANopen. The choice of communication interface depends on the specific requirements of the application and the overall system architecture. -
Q: How important is motor efficiency in the selection process?
A: Motor efficiency is a critical factor to consider when selecting a motor. Higher efficiency motors consume less energy, generate less heat, and offer better overall system efficiency. Choosing a motor with high efficiency can result in reduced operating costs, improved reliability, and a smaller environmental footprint.
Factor | Motor Drive | Motor Controller |
---|---|---|
Voltage and Current | Must match motor requirements | – |
Power Output | Sufficient for motor and application demands | – |
Control Features | Speed, torque, position control, programmability | – |
Communication | RS-232/RS-485, Ethernet, Fieldbus | – |
Environment | Temperature, humidity, vibration, shock | – |
Integration | Mounting, wiring, connectors, software | – |
Control Architecture | – | Centralized or distributed |
Processing Power | – | Processor type, speed, memory |
I/O Capabilities | – | Digital, analog, encoder interfaces |
Programming and Software | – | Language, IDE, libraries |
Scalability | – | Modular design, networking |
Leave a Reply