Understanding Signal-Layer Bonding in 10 Layer PCBs
Signal-layer bonding is a crucial process in the manufacturing of high-density, multi-layer printed circuit boards (PCBs), especially in the case of 10 layer PCBs. The bonding process ensures that the signal layers are properly connected and can effectively transmit electrical signals throughout the board. In this article, we will explore the various methods and techniques used to bond the signal layers of a 10 layer PCB, along with their advantages and disadvantages.
What is a 10 Layer PCB?
A 10 layer PCB is a complex, multi-layer printed circuit board that consists of ten conductive layers separated by insulating materials. These layers are typically arranged in the following order:
Layer | Description |
---|---|
1 | Top Layer (Signal) |
2 | Ground Plane |
3 | Signal Layer |
4 | Power Plane |
5 | Signal Layer |
6 | Signal Layer |
7 | Power Plane |
8 | Signal Layer |
9 | Ground Plane |
10 | Bottom Layer (Signal) |
The signal layers are responsible for carrying electrical signals between components, while the power and ground planes provide a stable reference voltage and help to reduce electromagnetic interference (EMI).
Importance of Signal-Layer Bonding
Signal-layer bonding is essential for ensuring the proper functioning and reliability of a 10 layer PCB. Some of the key reasons why signal-layer bonding is crucial include:
-
Signal Integrity: Proper bonding of the signal layers helps to maintain signal integrity by reducing impedance mismatches, crosstalk, and signal reflections.
-
Mechanical Strength: Bonding the layers together increases the overall mechanical strength of the PCB, making it more resistant to vibration, shock, and other physical stresses.
-
Thermal Management: Effective bonding helps to dissipate heat more efficiently, preventing hot spots and thermal stress on the board.
-
Manufacturing Consistency: Consistent bonding processes ensure that each PCB is manufactured to the same high standards, reducing the likelihood of defects and failures.
Signal-Layer Bonding Methods
There are several methods used to bond the signal layers of a 10 layer PCB, each with its own advantages and disadvantages. The most common methods include:
1. Lamination
Lamination is the most widely used method for bonding the layers of a multi-layer PCB. In this process, the individual layers are stacked together with insulating materials (prepregs) between them. The stack is then subjected to high pressure and temperature in a lamination press, causing the prepregs to melt and bond the layers together.
Advantages:
– Well-established and reliable process
– Suitable for high-volume production
– Provides good mechanical strength
Disadvantages:
– Requires careful control of pressure and temperature
– Can be time-consuming
– May cause signal integrity issues if not performed correctly
2. Direct Bonding
Direct bonding, also known as oxide bonding or fusion bonding, involves directly bonding the copper layers together without the use of prepregs. In this method, the copper surfaces are cleaned and activated, then brought into contact under high pressure and temperature. The copper atoms diffuse across the interface, forming a strong metallic bond.
Advantages:
– Eliminates the need for prepregs, reducing material costs
– Provides excellent thermal and electrical conductivity
– Enables the creation of finer pitch features
Disadvantages:
– Requires extremely clean and flat copper surfaces
– Limited to certain copper types and thicknesses
– May be more expensive than lamination for low-volume production
3. Adhesive Bonding
Adhesive bonding involves using a conductive adhesive to bond the signal layers together. The adhesive is applied to the copper surfaces, and the layers are then pressed together under moderate pressure and temperature. The adhesive cures, forming a strong bond between the layers.
Advantages:
– Lower processing temperatures compared to lamination
– Suitable for bonding dissimilar materials
– Provides good mechanical strength and flexibility
Disadvantages:
– Adhesive may degrade over time, affecting long-term reliability
– May not provide as good electrical and thermal conductivity as direct bonding
– Requires careful control of adhesive application and curing process
4. Anisotropic Conductive Film (ACF) Bonding
ACF bonding uses a thin film containing conductive particles suspended in an insulating adhesive matrix. The film is placed between the signal layers, and pressure and heat are applied. The conductive particles create electrical connections between the layers, while the insulating adhesive provides mechanical bonding.
Advantages:
– Enables fine-pitch bonding
– Suitable for bonding flexible circuits to rigid boards
– Low processing temperatures
Disadvantages:
– Limited current-carrying capacity due to small particle size
– May be more expensive than other bonding methods
– Requires precise alignment and pressure control
Factors Affecting Signal-Layer Bonding
Several factors can influence the success and quality of signal-layer bonding in a 10 layer PCB. These include:
-
Surface Preparation: The copper surfaces must be clean, flat, and free of oxides or contaminants to ensure good bonding. Various cleaning methods, such as chemical etching, plasma treatment, or mechanical abrasion, may be used depending on the bonding method employed.
-
Pressure and Temperature: The applied pressure and temperature during the bonding process must be carefully controlled to ensure uniform bonding across the entire board. Insufficient pressure or temperature can result in weak bonds, while excessive pressure or temperature can cause damage to the layers or components.
-
Alignment: Proper alignment of the layers is crucial for maintaining signal integrity and preventing short circuits or open connections. Advanced alignment systems, such as optical or laser alignment, are often used to ensure precise layer registration.
-
Material Selection: The choice of bonding materials, such as prepregs, adhesives, or ACF, can significantly impact the performance and reliability of the bonded layers. Factors such as dielectric constant, glass transition temperature, and thermal expansion coefficient must be considered when selecting materials.
-
Design Considerations: The PCB layout and design can also affect the success of signal-layer bonding. Factors such as trace width and spacing, via size and placement, and copper thickness must be carefully optimized to ensure good bonding and signal integrity.
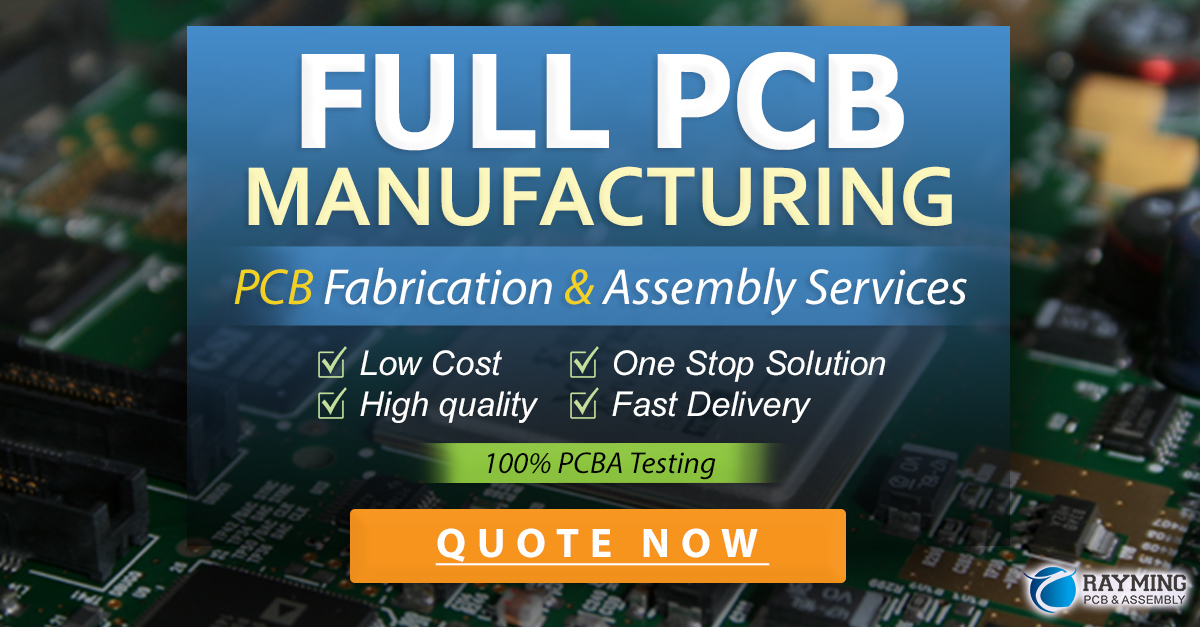
Quality Control and Testing
To ensure the reliability and performance of the bonded signal layers, various quality control measures and testing methods are employed during and after the bonding process. These include:
-
Visual Inspection: Optical microscopy or automated optical inspection (AOI) systems are used to visually inspect the bonded layers for defects such as voids, delamination, or misalignment.
-
Electrical Testing: Continuity and isolation testing are performed to verify the electrical integrity of the bonded layers. Methods such as flying probe testing or bed-of-nails testing may be used depending on the PCB design and test requirements.
-
Cross-Sectional Analysis: Destructive cross-sectional analysis may be performed on sample boards to assess the quality of the bonding interface and identify any internal defects or anomalies.
-
Thermal Cycling: The bonded PCB may be subjected to thermal cycling tests to evaluate its performance and reliability under varying temperature conditions. This helps to identify any potential issues related to thermal expansion mismatches or bond degradation.
-
Mechanical Testing: Peel strength tests or shear strength tests may be conducted to assess the mechanical integrity of the bonded layers and their ability to withstand physical stresses.
Troubleshooting Common Bonding Issues
Despite careful process control and quality assurance measures, various issues can arise during the signal-layer bonding process. Some common problems and their potential solutions include:
-
Delamination: Delamination occurs when the bonded layers separate due to weak adhesion or stress. This can be caused by improper surface preparation, insufficient bonding pressure or temperature, or material incompatibility. To prevent delamination, ensure proper surface cleaning, optimize bonding parameters, and select compatible materials.
-
Voids: Voids are air pockets or gaps that form between the bonded layers, which can affect signal integrity and mechanical strength. Voids can be caused by uneven pressure distribution, outgassing of materials, or contamination. To minimize voids, use vacuum lamination processes, control material moisture content, and maintain a clean bonding environment.
-
Misalignment: Misalignment of the layers can lead to signal integrity issues and manufacturing defects. This can be caused by improper layer registration, mechanical handling errors, or equipment malfunctions. To prevent misalignment, use precise alignment systems, implement robust handling procedures, and regularly maintain and calibrate bonding equipment.
-
Copper Wrinkling: Copper wrinkling occurs when the copper foil buckles or deforms during the bonding process, which can cause signal integrity issues and reliability problems. This can be caused by excessive bonding pressure, rapid temperature changes, or copper foil thickness variations. To mitigate copper wrinkling, optimize bonding pressure and temperature ramp rates, use consistent copper foil thicknesses, and consider using alternative bonding methods, such as direct bonding.
-
Resin Starvation: Resin starvation occurs when there is insufficient resin flow between the layers during lamination, resulting in poor bonding and mechanical weakness. This can be caused by incorrect prepreg selection, insufficient prepreg quantity, or inadequate bonding pressure. To prevent resin starvation, select appropriate prepreg materials, use sufficient prepreg quantity, and optimize bonding pressure and temperature.
Future Trends in Signal-Layer Bonding
As the demand for higher-density, high-performance PCBs continues to grow, new bonding technologies and materials are being developed to meet these challenges. Some of the emerging trends in signal-layer bonding include:
-
Advanced Adhesives: The development of novel adhesive materials with improved electrical and thermal conductivity, as well as enhanced mechanical properties, is an ongoing area of research. These advanced adhesives aim to provide better bonding performance and reliability for high-density PCBs.
-
3D Printing: Additive manufacturing techniques, such as 3D printing, are being explored as potential methods for creating multi-layer PCBs with embedded components and interconnects. This approach could enable the creation of complex, three-dimensional PCB structures with improved signal integrity and reduced form factors.
-
Embedded Components: The integration of passive and active components within the PCB stack-up is becoming increasingly popular for high-density designs. Embedded component technologies, such as embedded capacitance materials or embedded die packaging, require advanced bonding techniques to ensure reliable connections between the components and the signal layers.
-
Flexible and Stretchable Electronics: The growing demand for flexible and stretchable electronic devices is driving the development of new bonding methods and materials that can accommodate the mechanical deformation of the PCB. Techniques such as anisotropic conductive film bonding and the use of stretchable conductive adhesives are being explored to enable the creation of flexible and stretchable multi-layer PCBs.
-
Sustainable Materials: As environmental concerns continue to drive the electronics industry towards more sustainable practices, the development of eco-friendly bonding materials and processes is gaining traction. This includes the use of bio-based resins, recyclable adhesives, and low-temperature bonding techniques that reduce energy consumption and carbon footprint.
Conclusion
Signal-layer bonding is a critical process in the manufacturing of 10 layer PCBs, ensuring the proper functioning, reliability, and performance of the board. Various bonding methods, such as lamination, direct bonding, adhesive bonding, and ACF bonding, are used depending on the specific requirements of the PCB design and the available resources.
To achieve successful signal-layer bonding, careful consideration must be given to factors such as surface preparation, pressure and temperature control, alignment, material selection, and design optimization. Quality control measures and testing methods, including visual inspection, electrical testing, cross-sectional analysis, thermal cycling, and mechanical testing, are employed to ensure the reliability and performance of the bonded PCB.
As PCB technology continues to advance, new trends in signal-layer bonding, such as advanced adhesives, 3D printing, embedded components, flexible and stretchable electronics, and sustainable materials, are emerging to meet the ever-increasing demands for high-density, high-performance, and environmentally-friendly electronic devices.
By understanding the principles, methods, and challenges of signal-layer bonding in 10 layer PCBs, engineers and manufacturers can optimize their designs and processes to create reliable, high-quality multi-layer PCBs that meet the needs of today’s complex electronic systems.
Frequently Asked Questions (FAQ)
-
What is the most common method for bonding the signal layers of a 10 layer PCB?
Lamination is the most widely used method for bonding the layers of a multi-layer PCB, including 10 layer PCBs. This process involves stacking the layers with insulating prepregs and subjecting the stack to high pressure and temperature in a lamination press. -
What are the advantages of direct bonding compared to lamination?
Direct bonding eliminates the need for prepregs, reducing material costs and enabling the creation of finer pitch features. It also provides excellent thermal and electrical conductivity between the bonded layers. -
How does adhesive bonding differ from lamination?
Adhesive bonding uses a conductive adhesive to bond the signal layers together, whereas lamination relies on the melting and bonding of insulating prepregs. Adhesive bonding typically requires lower processing temperatures compared to lamination. -
What factors can cause delamination in bonded signal layers?
Delamination can be caused by improper surface preparation, insufficient bonding pressure or temperature, or material incompatibility. Ensuring proper surface cleaning, optimizing bonding parameters, and selecting compatible materials can help prevent delamination. -
What are some emerging trends in signal-layer bonding for high-density PCBs?
Some emerging trends in signal-layer bonding include the development of advanced adhesives with improved electrical and thermal properties, the use of 3D printing for creating complex multi-layer structures, the integration of embedded components, and the adoption of flexible and stretchable bonding techniques for next-generation electronic devices.
Leave a Reply