Understanding Lead-free Soldering Temperatures
Lead-free soldering is a process that involves using solder alloys that do not contain lead. This shift towards lead-free soldering is driven by environmental and health concerns associated with lead exposure. However, lead-free soldering typically requires higher temperatures compared to traditional lead-based soldering.
The table below shows the melting points of common lead-free solder alloys:
Solder Alloy | Melting Point (°C) |
---|---|
Tin-Silver-Copper (SAC) | 217-220 |
Tin-Copper (SnCu) | 227 |
Tin-Silver (SnAg) | 221 |
Tin-Bismuth (SnBi) | 138 |
As evident from the table, lead-free solder alloys have melting points ranging from 138°C to 227°C, with SAC being the most widely used alloy.
Impact of High Soldering Temperatures on PCBs
Exposing a PCB to high soldering temperatures repeatedly can have several detrimental effects on its performance and longevity. Let’s explore some of these effects in detail.
Thermal Stress
When a PCB is subjected to high temperatures during soldering, it experiences thermal stress. The repeated heating and cooling cycles can cause the PCB substrate to expand and contract, leading to warping, twisting, or even cracking. This thermal stress can be particularly severe when the temperature change is rapid or when there is a significant mismatch in the thermal expansion coefficients of the PCB materials.
Delamination
Delamination is another common issue that can arise from repeated exposure to high soldering temperatures. It occurs when the layers of the PCB separate due to the weakening of the adhesive bond between them. Delamination can lead to poor electrical connections, reduced mechanical strength, and even complete failure of the PCB.
Copper Dissolution
At high soldering temperatures, the copper traces on the PCB can dissolve into the molten solder. This phenomenon, known as copper dissolution, can cause thinning of the copper traces and alter their electrical properties. Excessive copper dissolution can result in open circuits or increased resistance, affecting the overall performance of the PCB.
Intermetallic Compound (IMC) Growth
When the PCB is exposed to high soldering temperatures, intermetallic compounds (IMCs) can form at the interface between the solder and the copper pads. While a thin layer of IMCs is necessary for a strong solder joint, excessive IMC growth can lead to brittle and weak joints. Repeated exposure to high temperatures accelerates the growth of IMCs, compromising the reliability of the solder connections.
Factors Affecting PCB’s Ability to Withstand High Temperatures
Several factors influence a PCB’s ability to withstand repeated exposure to high soldering temperatures. These factors include:
PCB Material
The choice of PCB material plays a crucial role in its thermal stability. Some commonly used PCB materials and their maximum operating temperatures are listed below:
PCB Material | Maximum Operating Temperature (°C) |
---|---|
FR-4 | 130 |
High Tg FR-4 | 170 |
Polyimide | 260 |
Teflon | 260 |
PCBs made from materials with higher maximum operating temperatures, such as polyimide or Teflon, can withstand repeated exposure to lead-free soldering temperatures better than standard FR-4 PCBs.
PCB Thickness
The thickness of the PCB also influences its ability to dissipate heat and withstand thermal stress. Thicker PCBs have better thermal conductivity and are less prone to warping or deformation compared to thinner ones. However, increasing the PCB thickness also increases the overall cost and weight of the board.
Copper Thickness
The thickness of the copper traces on the PCB affects its current-carrying capacity and heat dissipation properties. Thicker copper traces can handle higher currents and distribute heat more effectively, reducing the risk of thermal damage during soldering. The table below shows the standard copper thicknesses used in PCBs:
Copper Weight (oz) | Thickness (μm) |
---|---|
0.5 | 17.5 |
1 | 35 |
2 | 70 |
3 | 105 |
Using thicker copper traces can help improve the PCB’s thermal performance and durability.
Soldering Profile
The soldering profile, which defines the temperature curve and duration of the soldering process, also plays a significant role in determining how often a PCB can be raised to lead-free soldering temperatures. An optimized soldering profile minimizes the time spent at peak temperatures and ensures a gradual ramp-up and cool-down to reduce thermal shock.
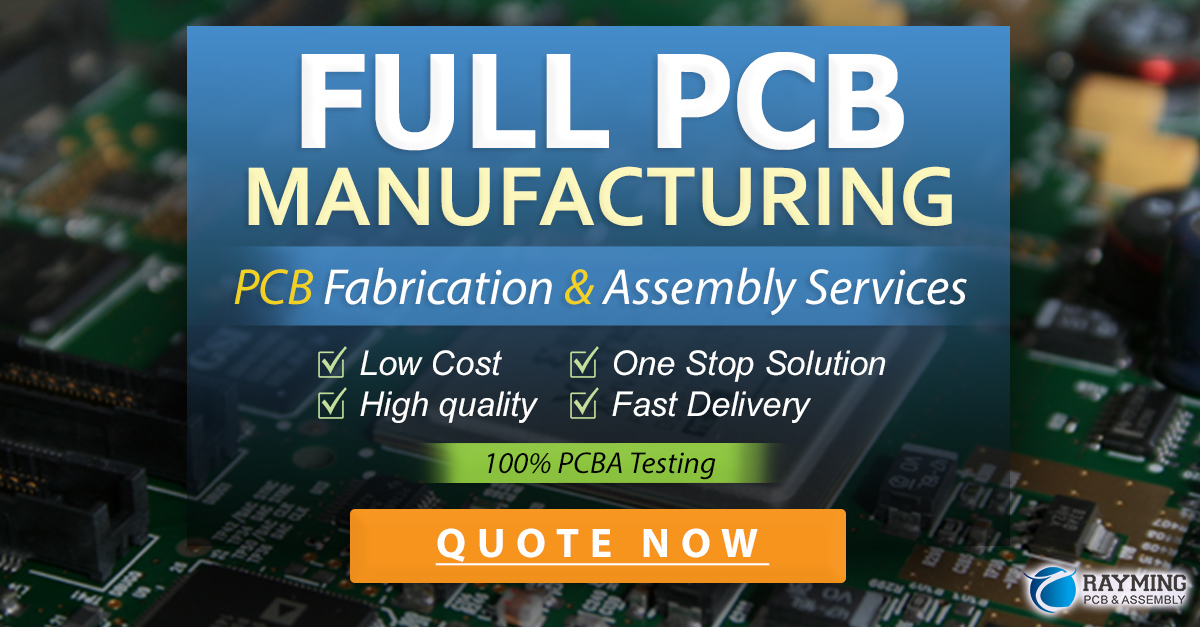
Best Practices for Maximizing PCB Durability
To maximize the durability of PCBs subjected to repeated lead-free soldering, consider the following best practices:
-
Choose appropriate PCB materials: Select PCB materials with high glass transition temperatures (Tg) and good thermal stability, such as high Tg FR-4, polyimide, or Teflon, depending on the application requirements.
-
Optimize PCB design: Design the PCB with adequate copper thickness, proper trace routing, and sufficient spacing between components to facilitate heat dissipation and minimize thermal stress.
-
Use conformal coatings: Apply conformal coatings to the PCB to provide an additional layer of protection against thermal and mechanical stresses.
-
Implement thermal management techniques: Incorporate thermal management techniques, such as using heatsinks, thermal vias, or heat-spreading layers, to dissipate heat effectively and reduce the impact of high temperatures on the PCB.
-
Follow recommended soldering profiles: Adhere to the recommended soldering profiles provided by the solder alloy manufacturer to ensure optimal soldering conditions and minimize thermal stress on the PCB.
FAQ
-
Q: What is the typical maximum temperature for lead-free soldering?
A: The typical maximum temperature for lead-free soldering is around 260°C, depending on the specific solder alloy used. -
Q: How many times can a PCB be safely raised to lead-free soldering temperatures?
A: The number of times a PCB can be safely raised to lead-free soldering temperatures depends on various factors such as the PCB material, thickness, copper thickness, and soldering profile. Generally, a well-designed PCB can withstand several soldering cycles without significant degradation. -
Q: Can repeated exposure to high soldering temperatures cause permanent damage to a PCB?
A: Yes, repeated exposure to high soldering temperatures can cause permanent damage to a PCB, such as delamination, copper dissolution, and excessive intermetallic compound growth, which can affect its performance and reliability. -
Q: What can be done to minimize the impact of high soldering temperatures on PCBs?
A: To minimize the impact of high soldering temperatures on PCBs, use appropriate PCB materials with high thermal stability, optimize the PCB design for heat dissipation, use conformal coatings, implement thermal management techniques, and follow recommended soldering profiles. -
Q: Are there any alternative soldering methods that can reduce the thermal stress on PCBs?
A: Alternative soldering methods, such as vapor phase soldering or laser soldering, can potentially reduce the thermal stress on PCBs by providing more localized heating or a more controlled temperature profile. However, these methods may have their own limitations and may not be suitable for all applications.
Conclusion
In conclusion, the frequency at which a PCB can be raised to lead-free soldering temperatures depends on several factors, including the PCB material, thickness, copper thickness, and soldering profile. Repeated exposure to high temperatures can cause thermal stress, delamination, copper dissolution, and excessive intermetallic compound growth, compromising the PCB’s performance and reliability.
To maximize the durability of PCBs subjected to lead-free soldering, it is essential to choose appropriate PCB materials, optimize the PCB design, use conformal coatings, implement thermal management techniques, and follow recommended soldering profiles. By adopting these best practices, manufacturers can ensure that their PCBs can withstand multiple lead-free soldering cycles without significant degradation.
As the electronics industry continues to evolve and the demand for lead-free soldering grows, understanding the impact of high soldering temperatures on PCBs becomes increasingly important. By staying informed about the latest developments in PCB materials, design techniques, and soldering processes, manufacturers can make informed decisions to produce high-quality, reliable, and durable PCBs that meet the requirements of modern electronic devices.
Leave a Reply