What is Design for Manufacturing (DFM)?
Design for Manufacturing (DFM) is a design approach that focuses on creating products that are easy to manufacture, assemble, and maintain. The goal of DFM is to reduce manufacturing costs, improve product quality, and shorten time-to-market by considering manufacturing constraints and requirements early in the design process.
DFM involves several key principles:
- Simplify the design: Reduce the number of parts, minimize complex geometries, and standardize components wherever possible.
- Design for ease of fabrication: Consider the limitations and capabilities of the manufacturing processes to be used, such as tolerances, material properties, and machine capabilities.
- Design for ease of assembly: Optimize the design for efficient assembly, reducing the number of steps and minimizing the need for specialized tools or skilled labor.
- Select appropriate materials: Choose materials that are easily sourced, cost-effective, and compatible with the intended manufacturing processes.
- Collaborate with manufacturing experts: Involve manufacturing engineers and other stakeholders early in the design process to identify potential issues and optimize the design for manufacturing.
By applying DFM principles, companies can reduce manufacturing costs, improve product quality, and accelerate time-to-market.
Types of DFM Tools
There are several types of DFM tools available to support designers and engineers in implementing DFM principles:
1. CAD-Integrated DFM Tools
Many modern Computer-Aided Design (CAD) software packages include built-in DFM tools that allow designers to analyze their designs for manufacturability. These tools often provide real-time feedback on potential manufacturing issues, such as thin walls, undercuts, or draft angles. Examples of CAD software with integrated DFM tools include:
- Autodesk Fusion 360
- SolidWorks DFMXpress
- Siemens NX DFM Advisor
- PTC Creo DFM Adviser
CAD-integrated DFM tools offer the advantage of seamless integration with the design environment, allowing designers to make changes and receive feedback without switching between different software applications.
2. Standalone DFM Software
Standalone DFM software packages are dedicated tools that focus specifically on analyzing designs for manufacturability. These tools often provide more advanced features and in-depth analysis compared to CAD-integrated DFM tools. Some popular standalone DFM software include:
- DFMPro by HCL Technologies
- DFMA by Boothroyd Dewhurst, Inc.
- Geometric DFMPro
- Siemens Tecnomatix DFM
Standalone DFM software typically requires designers to export their CAD models in a compatible format, such as STEP or IGES, for analysis. The software then generates reports highlighting potential manufacturing issues and suggests improvements to optimize the design for manufacturing.
3. Manufacturing Process-Specific DFM Tools
Some DFM tools are designed to analyze designs for specific manufacturing processes, such as injection molding, Sheet Metal Fabrication, or 3D printing. These tools provide specialized analysis and guidance based on the unique constraints and requirements of each manufacturing process. Examples of process-specific DFM tools include:
- Moldflow by Autodesk (for injection molding)
- SolidWorks Plastics (for injection molding)
- AutoForm (for sheet metal forming)
- Materialise Magics (for 3D printing)
Process-specific DFM tools enable designers to optimize their designs for a particular manufacturing process, taking into account factors such as material flow, cooling, warpage, and support structures.
4. Knowledge-Based DFM Tools
Knowledge-based DFM tools leverage artificial intelligence and machine learning algorithms to analyze designs and provide recommendations based on a vast database of manufacturing knowledge. These tools can identify potential manufacturing issues and suggest design improvements based on best practices and historical data. Examples of knowledge-based DFM tools include:
- DFMA by Boothroyd Dewhurst, Inc.
- Siemens NX DFM Advisor
- DFMPro by HCL Technologies
Knowledge-based DFM tools continuously learn and improve their recommendations as more data is fed into the system, making them increasingly valuable for optimizing designs for manufacturing.
Key Features of DFM Tools
While the specific features of DFM tools vary depending on the type and vendor, most tools share some common capabilities:
-
Design Analysis: DFM tools analyze CAD models for potential manufacturing issues, such as thin walls, undercuts, draft angles, and part complexity. The tools highlight these issues and provide recommendations for improvement.
-
Manufacturing Process Simulation: Some DFM tools can simulate the manufacturing process, such as injection molding or sheet metal forming, to predict potential issues like material flow, cooling, warpage, or springback. This allows designers to optimize their designs before committing to production.
-
Design Optimization: DFM tools often provide suggestions for design optimization, such as simplifying geometry, reducing part count, or standardizing components. These suggestions aim to reduce manufacturing costs and improve product quality.
-
Cost Estimation: Many DFM tools include cost estimation features that help designers understand the manufacturing costs associated with their designs. This enables designers to make informed decisions and trade-offs to meet cost targets.
-
Collaboration and Communication: DFM tools facilitate collaboration between design and manufacturing teams by providing a common platform for sharing design data and feedback. Some tools also generate reports and visualizations that can be easily shared with stakeholders.
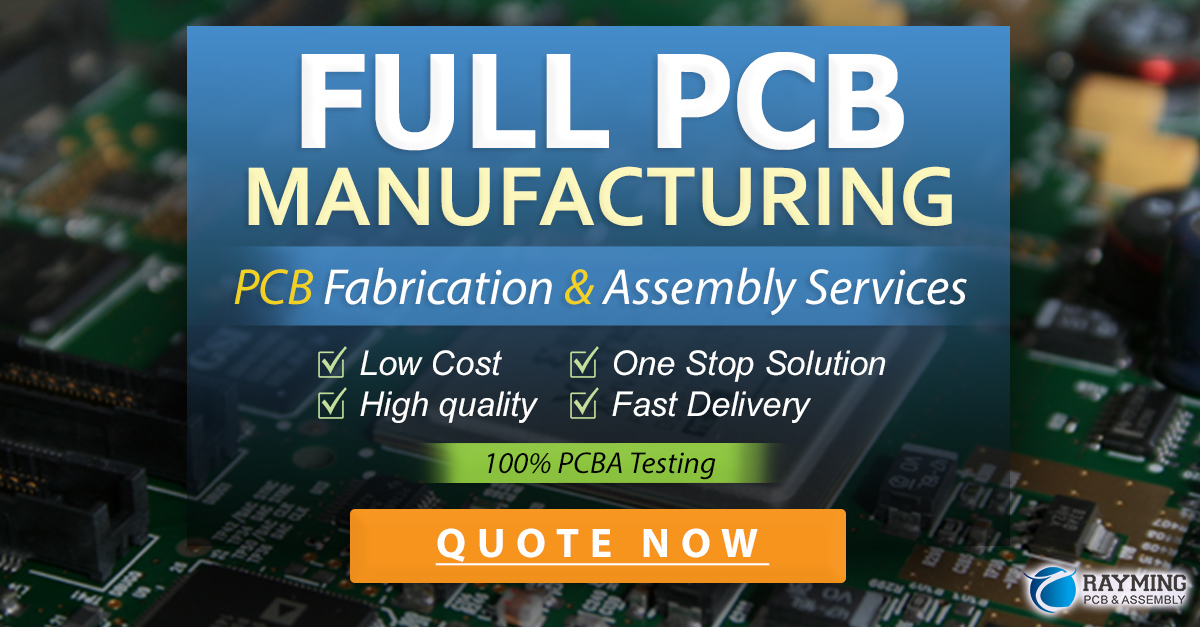
Choosing the Right DFM Tool
When selecting a DFM tool, consider the following factors:
-
Compatibility with existing CAD software: Ensure that the DFM tool is compatible with your current CAD system to avoid data translation issues and workflow disruptions.
-
Manufacturing process support: Choose a DFM tool that supports the specific manufacturing processes used by your company or suppliers.
-
Ease of use: Consider the learning curve and user-friendliness of the DFM tool, as well as the availability of training and support resources.
-
Integration with other tools: Look for DFM tools that can integrate with other software tools used in your product development process, such as Product Lifecycle Management (PLM) or Enterprise Resource Planning (ERP) systems.
-
Scalability: Ensure that the DFM tool can handle the complexity and scale of your product designs and can grow with your company’s needs.
Implementing DFM Tools in the Product Development Process
To effectively implement DFM tools in your product development process, consider the following best practices:
-
Involve manufacturing experts early: Engage manufacturing engineers and other stakeholders early in the design process to ensure that DFM considerations are addressed from the start.
-
Establish DFM guidelines and standards: Develop company-specific DFM guidelines and standards that align with your manufacturing processes and capabilities. Ensure that these guidelines are communicated to all relevant stakeholders and are consistently applied.
-
Provide training and support: Offer training and support resources to help designers and engineers effectively use DFM tools and apply DFM principles in their work.
-
Integrate DFM tools into the design workflow: Incorporate DFM tools into your standard design workflow to ensure that manufacturability analysis is performed consistently and at the appropriate stages of the design process.
-
Continuously improve: Regularly review and update your DFM practices and tools based on feedback from manufacturing, quality, and other stakeholders. Continuously seek opportunities to improve product designs and manufacturing processes.
The Future of DFM Tools
As technology advances, DFM tools are expected to become increasingly sophisticated and integrated into the product development process. Some trends and future developments in DFM tools include:
-
Increased use of artificial intelligence and machine learning: DFM tools will leverage AI and ML algorithms to provide more accurate and personalized design recommendations based on vast amounts of manufacturing data.
-
Integration with additive manufacturing: As 3D printing and other additive manufacturing technologies become more prevalent, DFM tools will evolve to support the unique design constraints and opportunities associated with these processes.
-
Cloud-based collaboration: Cloud-based DFM tools will enable seamless collaboration between distributed design and manufacturing teams, allowing for real-time data sharing and feedback.
-
Virtual and augmented reality: VR and AR technologies will be incorporated into DFM tools, allowing designers to visualize and interact with their designs in a more immersive and intuitive manner.
-
Integration with the Internet of Things (IoT): DFM tools will integrate with IoT systems to collect real-time data from manufacturing processes, enabling continuous improvement and optimization of product designs.
Conclusion
DFM tools play a crucial role in optimizing product designs for manufacturing, reducing costs, improving quality, and accelerating time-to-market. With a wide range of DFM tools available, from CAD-integrated solutions to standalone software and process-specific tools, designers and engineers have access to powerful resources to support their DFM efforts.
By selecting the right DFM tools, establishing clear guidelines and standards, and integrating DFM into the product development process, companies can realize significant benefits in terms of manufacturing efficiency, product quality, and overall competitiveness.
As technology continues to advance, DFM tools will become even more sophisticated and integrated, enabling companies to push the boundaries of product design and manufacturing innovation.
Frequently Asked Questions (FAQ)
1. What are the benefits of using DFM tools?
DFM tools offer several key benefits, including:
- Reduced manufacturing costs by optimizing designs for efficient production
- Improved product quality by identifying and addressing potential manufacturing issues early in the design process
- Shortened time-to-market by streamlining the design and manufacturing process
- Enhanced collaboration between design and manufacturing teams
2. Can DFM tools be used for all types of manufacturing processes?
While some DFM tools are designed for specific manufacturing processes, such as injection molding or sheet metal fabrication, many tools offer a wide range of capabilities that can be applied to various manufacturing methods. When selecting a DFM tool, ensure that it supports the manufacturing processes used by your company or suppliers.
3. How do DFM tools integrate with existing CAD software?
Many DFM tools are designed to integrate seamlessly with popular CAD software packages, either as built-in features or as plug-ins. This integration allows designers to analyze their designs for manufacturability directly within their CAD environment, without the need to export and import data between different software applications.
4. What skills are required to use DFM tools effectively?
To use DFM tools effectively, designers and engineers should have a strong understanding of the manufacturing processes used by their company, as well as a solid foundation in design principles and CAD software. Familiarity with DFM principles and guidelines is also essential. Many DFM tool vendors offer training and support resources to help users develop the necessary skills and knowledge.
5. How can companies justify the investment in DFM tools?
Investing in DFM tools can be justified by the potential cost savings and quality improvements they offer. By optimizing designs for manufacturing, companies can reduce material waste, minimize production time, and avoid costly rework or redesign. DFM tools also help to improve product quality by identifying and addressing potential manufacturing issues early in the design process. These benefits can lead to significant long-term cost savings and a competitive advantage in the market.
DFM Tool Category | Examples | Key Features |
---|---|---|
CAD-Integrated DFM Tools | – Autodesk Fusion 360 – SolidWorks DFMXpress – Siemens NX DFM Advisor – PTC Creo DFM Adviser |
– Seamless integration with CAD software – Real-time feedback on manufacturing issues – Design optimization suggestions |
Standalone DFM Software | – DFMPro by HCL Technologies – DFMA by Boothroyd Dewhurst, Inc. – Geometric DFMPro – Siemens Tecnomatix DFM |
– Advanced features and in-depth analysis – Generates reports on manufacturing issues – Suggests design improvements for manufacturability |
Manufacturing Process-Specific DFM Tools | – Moldflow by Autodesk (injection molding) – SolidWorks Plastics (injection molding) – AutoForm (sheet metal forming) – Materialise Magics (3D printing) |
– Specialized analysis for specific manufacturing processes – Considers unique constraints and requirements – Optimizes designs for the chosen manufacturing method |
Knowledge-Based DFM Tools | – DFMA by Boothroyd Dewhurst, Inc. – Siemens NX DFM Advisor – DFMPro by HCL Technologies |
– Leverages AI and machine learning algorithms – Provides recommendations based on manufacturing knowledge – Continuously improves with increased data input |
Leave a Reply