What is temperature correction?
Temperature correction is a method used to compensate for the influence of temperature variations on the measurement of a parameter. It involves adjusting the measured value of a parameter to account for the deviation caused by temperature changes. By applying temperature correction, the true value of the parameter can be determined, regardless of the ambient temperature conditions.
The need for temperature correction arises from the fact that many materials and devices exhibit temperature-dependent behavior. For example, the resistance of an electrical conductor, the output of a sensor, or the dimensions of a mechanical component can all vary with temperature. Without proper correction, these temperature-induced variations can lead to erroneous measurements and compromised system performance.
Importance of Temperature Correction
Temperature correction plays a vital role in ensuring the accuracy and reliability of parameter measurements across various fields. Some of the key reasons why temperature correction is important include:
-
Improved Accuracy: By compensating for temperature-induced variations, temperature correction enables more precise measurements of parameters. This enhanced accuracy is essential in applications where even small deviations can have significant consequences, such as in scientific research, quality control, and process optimization.
-
Consistency and Reproducibility: Temperature correction ensures that measurements remain consistent and reproducible, regardless of the ambient temperature conditions. This is particularly important when comparing measurements taken at different times or locations, as it eliminates the influence of temperature variations on the results.
-
Compliance with Standards: Many industries have specific standards and regulations that require temperature correction to be applied to parameter measurements. Adhering to these standards ensures that the measurements meet the necessary accuracy and reliability requirements, thereby maintaining product quality and safety.
-
Cost Savings: Inaccurate measurements due to temperature variations can lead to inefficiencies, product defects, and increased costs. By implementing temperature correction, businesses can minimize these issues and optimize their processes, resulting in cost savings and improved profitability.
Techniques for Temperature Correction
There are several techniques used for temperature correction, each with its own advantages and limitations. The choice of technique depends on factors such as the parameter being measured, the temperature range of interest, and the required level of accuracy. Some common techniques for temperature correction include:
1. Linear Temperature Correction
Linear temperature correction assumes a linear relationship between the measured parameter and temperature. It involves applying a correction factor that is proportional to the temperature deviation from a reference temperature. The corrected value of the parameter is calculated using the following equation:
Corrected Value = Measured Value + Correction Factor × (Measured Temperature – Reference Temperature)
The correction factor is typically determined through calibration, where the parameter is measured at different known temperatures, and the relationship between the measured value and temperature is established.
2. Polynomial Temperature Correction
Polynomial temperature correction is used when the relationship between the parameter and temperature is non-linear. It involves fitting a polynomial function to the calibration data, which describes the parameter’s behavior over a range of temperatures. The corrected value is then calculated using the polynomial equation.
For example, a second-order polynomial correction equation would be:
Corrected Value = a₀ + a₁ × (Measured Temperature) + a₂ × (Measured Temperature)²
The coefficients a₀, a₁, and a₂ are determined through regression analysis of the calibration data.
3. Look-up Table Correction
Look-up table correction involves creating a table that maps the measured temperature to the corresponding correction factor or corrected value. During measurement, the correction factor or corrected value is retrieved from the table based on the measured temperature.
This technique is particularly useful when the relationship between the parameter and temperature is complex or when high accuracy is required over a wide temperature range. The look-up table is typically generated through extensive calibration and interpolation of the calibration data.
4. Sensor Fusion
Sensor fusion is a technique that combines measurements from multiple sensors to improve the accuracy and reliability of the parameter measurement. In the context of temperature correction, sensor fusion can involve using a dedicated temperature sensor alongside the primary parameter sensor.
By measuring the temperature independently and applying the appropriate correction algorithm, the influence of temperature variations on the parameter measurement can be effectively compensated for. Sensor fusion can provide enhanced accuracy and robustness compared to relying on a single sensor.
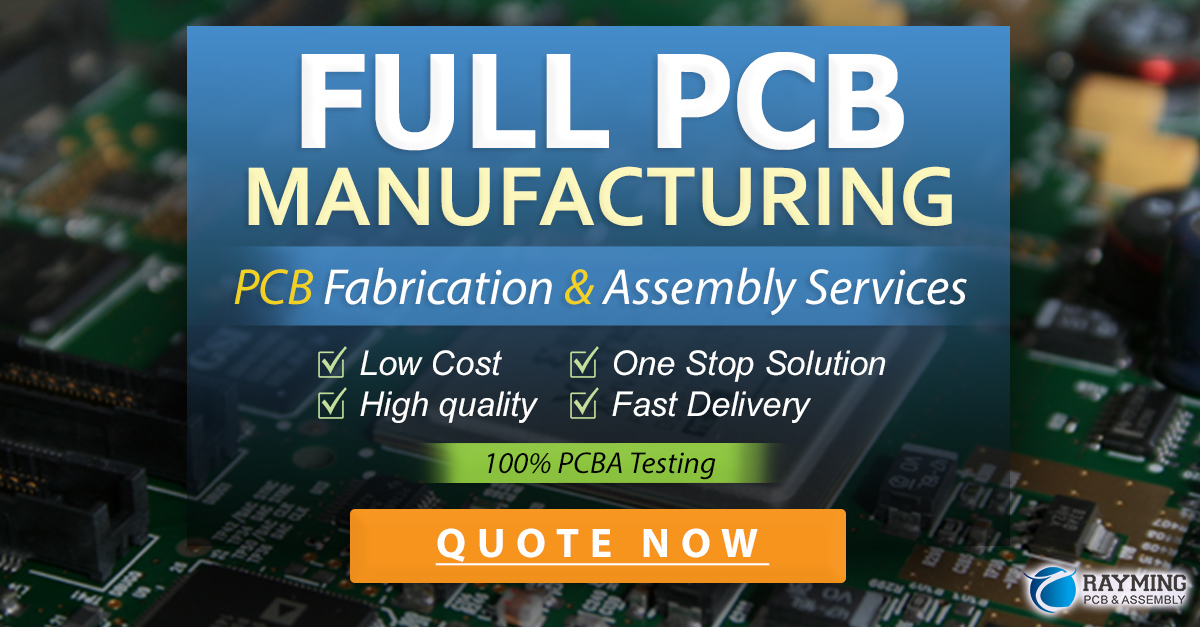
Implementation of Temperature Correction
The implementation of temperature correction involves several key steps:
-
Calibration: The first step in implementing temperature correction is calibrating the measurement system. This involves measuring the parameter at different known temperatures and establishing the relationship between the measured value and temperature. Calibration data is collected and used to determine the correction factors or polynomial coefficients.
-
Correction Algorithm: Based on the calibration data and the chosen correction technique, a correction algorithm is developed. The algorithm takes the measured temperature as an input and applies the appropriate correction to the measured parameter value. The algorithm can be implemented in software or hardware, depending on the specific requirements of the application.
-
Temperature Measurement: To apply temperature correction, accurate measurement of the ambient temperature is crucial. This can be achieved using various temperature sensors, such as thermocouples, resistance temperature detectors (RTDs), or thermistors. The temperature sensor should be placed in close proximity to the parameter sensor to ensure representative temperature measurements.
-
Real-time Correction: In real-time applications, temperature correction is applied continuously as measurements are taken. The correction algorithm is integrated into the measurement system, and the corrected parameter values are output in real-time. This ensures that the measurements remain accurate and reliable throughout the operation.
-
Validation and Monitoring: Regular validation and monitoring of the temperature correction system are essential to ensure its ongoing effectiveness. Periodic calibration checks and performance assessments should be conducted to verify the accuracy of the correction algorithm and identify any drift or degradation in the system. Monitoring temperature trends and parameter measurements can help detect anomalies and trigger maintenance or recalibration when necessary.
Applications of Temperature Correction
Temperature correction finds applications in a wide range of fields, including:
-
Industrial Process Control: In industrial processes, accurate measurement of parameters such as pressure, flow, and level is essential for optimal control and efficiency. Temperature correction ensures that these measurements remain accurate despite variations in ambient temperature, enabling precise process control and optimization.
-
Automotive Industry: Temperature correction is widely used in the automotive industry, particularly in engine management systems. Parameters such as air intake temperature, coolant temperature, and exhaust gas temperature are measured and corrected to ensure accurate fuel injection, ignition timing, and emission control.
-
Aerospace and Defense: In aerospace and defense applications, temperature correction is critical for ensuring the reliability and performance of various systems. From avionics to propulsion systems, accurate measurement of parameters under varying temperature conditions is essential for safe and efficient operation.
-
Medical Devices: Medical devices, such as blood glucose meters and pulse oximeters, rely on accurate parameter measurements for proper diagnosis and treatment. Temperature correction is employed to compensate for the influence of body temperature on these measurements, ensuring reliable and consistent results.
-
Environmental Monitoring: Temperature correction is crucial in environmental monitoring applications, such as air and water quality monitoring. Accurate measurement of pollutants, gases, and other environmental parameters requires compensation for temperature variations to obtain reliable data for analysis and decision-making.
-
Scientific Research: In scientific research, temperature correction is essential for accurate data collection and analysis. From material characterization to biological experiments, correcting for temperature-induced variations ensures the integrity and reproducibility of research findings.
Frequently Asked Questions (FAQ)
-
What is the purpose of temperature correction?
Temperature correction aims to compensate for the influence of temperature variations on the measurement of a parameter. By applying temperature correction, the true value of the parameter can be determined, regardless of the ambient temperature conditions. -
Why is temperature correction important?
Temperature correction is important because it improves the accuracy and reliability of parameter measurements. It ensures consistency and reproducibility of measurements, enables compliance with industry standards, and can lead to cost savings by optimizing processes and reducing errors. -
What are some common techniques for temperature correction?
Common techniques for temperature correction include linear correction, polynomial correction, look-up table correction, and sensor fusion. The choice of technique depends on factors such as the parameter being measured, the temperature range of interest, and the required level of accuracy. -
How is temperature correction implemented?
The implementation of temperature correction involves calibrating the measurement system, developing a correction algorithm based on the calibration data, accurately measuring the ambient temperature, applying real-time correction to the parameter measurements, and regularly validating and monitoring the correction system. -
In which fields is temperature correction commonly applied?
Temperature correction finds applications in various fields, including industrial process control, automotive industry, aerospace and defense, medical devices, environmental monitoring, and scientific research. Accurate parameter measurements under varying temperature conditions are crucial in these domains for optimal performance, safety, and reliability.
Temperature Range (°C) | Correction Factor |
---|---|
-20 to 0 | 0.98 |
0 to 20 | 1.00 |
20 to 40 | 1.02 |
40 to 60 | 1.05 |
60 to 80 | 1.08 |
Table: Example of a look-up table for temperature correction factors
Conclusion
Temperature correction is a vital technique for ensuring the accuracy and reliability of parameter measurements in various scientific and industrial applications. By compensating for the influence of temperature variations, temperature correction enables precise measurements, consistency, and compliance with industry standards.
The choice of temperature correction technique depends on the specific requirements of the application, such as the parameter being measured, the temperature range of interest, and the desired level of accuracy. Implementing temperature correction involves calibration, algorithm development, accurate temperature measurement, real-time correction, and ongoing validation and monitoring.
As industries continue to demand higher accuracy and reliability in parameter measurements, the importance of temperature correction will only grow. Advancements in sensor technology, data analysis, and machine learning are expected to further enhance the capabilities of temperature correction systems, enabling more precise and robust measurements across a wide range of applications.
By understanding the principles and techniques of temperature correction, engineers, scientists, and technicians can effectively mitigate the impact of temperature variations on their measurements, leading to improved performance, efficiency, and decision-making in their respective fields.
Leave a Reply