Introduction to Solder Paste Testing
Solder paste printing is a critical process in the manufacturing of printed circuit boards (PCBs). It involves applying a precise amount of solder paste onto specific areas of the PCB, which will later be used to attach electronic components. The quality of the solder paste printing process directly affects the reliability and functionality of the final product. Therefore, it is essential to test the solder paste printing process to ensure that it meets the required standards.
Why is Solder Paste Testing Important?
Solder paste testing is important for several reasons:
-
Ensures Consistent Quality: Testing the solder paste printing process helps to ensure that the solder paste is applied consistently and accurately across the PCB. This consistency is crucial for the proper functioning of the electronic components.
-
Identifies Defects Early: By testing the solder paste printing process, defects such as insufficient solder paste, bridging, or misalignment can be identified early in the manufacturing process. This allows for corrective action to be taken before the defects lead to more serious problems down the line.
-
Reduces Rework and Scrap: Identifying and correcting defects early in the process reduces the need for rework and scrap, which can be costly and time-consuming.
-
Improves Reliability: Proper solder paste printing is essential for the reliability of the final product. Testing ensures that the solder joints are strong and reliable, reducing the risk of failures in the field.
Methods of Solder Paste Testing
There are several methods used to test solder paste printing, each with its own advantages and disadvantages. The most common methods are:
Visual Inspection
Visual inspection is the most basic form of solder paste testing. It involves visually examining the printed solder paste under magnification to check for defects such as insufficient solder paste, bridging, or misalignment.
Advantages:
– Simple and quick
– Does not require specialized equipment
– Can identify gross defects
Disadvantages:
– Subjective and dependent on the skill of the inspector
– Cannot detect subtle defects
– Time-consuming for large volumes
2D Automated Optical Inspection (AOI)
2D AOI uses cameras and image processing software to automatically inspect the printed solder paste. The system captures images of the PCB and compares them to a reference image to identify defects.
Advantages:
– Automated and objective
– Can inspect large volumes quickly
– Can detect subtle defects
Disadvantages:
– Requires specialized equipment
– Limited to 2D inspection
– Can be affected by variations in lighting or PCB Color
3D Solder Paste Inspection (SPI)
3D SPI uses laser triangulation or structured light to create a 3D profile of the printed solder paste. This allows for the measurement of solder paste volume, height, and shape.
Advantages:
– Provides detailed 3D measurements
– Can detect defects not visible in 2D inspection
– Highly accurate and repeatable
Disadvantages:
– Requires specialized equipment
– Slower than 2D AOI
– Can be affected by highly reflective surfaces
X-Ray Inspection
X-ray inspection uses x-rays to image the internal structure of the solder joints. This allows for the detection of defects such as voids, cracks, or insufficient solder.
Advantages:
– Can inspect hidden solder joints
– Provides detailed internal images
– Can detect defects not visible with other methods
Disadvantages:
– Requires specialized equipment
– Slower than other methods
– Potential safety concerns with x-ray exposure
Solder Paste Testing Parameters
When testing solder paste printing, there are several key parameters that need to be measured and evaluated. These include:
Solder Paste Volume
The volume of solder paste applied to each pad is critical for forming a reliable solder joint. Too little solder paste can result in weak or open joints, while too much solder paste can cause bridging or tombstoning.
Solder Paste Volume | Effect |
---|---|
Insufficient | Weak or open joints |
Excessive | Bridging, tombstoning, solder beading |
Solder Paste Height
The height of the solder paste deposit affects the final shape and strength of the solder joint. Solder paste that is too thin may not provide sufficient volume for a reliable joint, while solder paste that is too thick may cause component misalignment or bridging.
Solder Paste Height | Effect |
---|---|
Too thin | Insufficient volume for reliable joint |
Too thick | Component misalignment, bridging |
Solder Paste Area
The area of the solder paste deposit should match the size and shape of the pad. Solder paste that extends beyond the pad can cause bridging, while solder paste that does not cover the entire pad may result in a weak or open joint.
Solder Paste Area | Effect |
---|---|
Too small | Weak or open joint |
Too large | Bridging, solder beading |
Solder Paste Alignment
The alignment of the solder paste deposit with the pad is important for ensuring proper component placement. Misaligned solder paste can cause component skew or tombstoning.
Solder Paste Alignment | Effect |
---|---|
Misaligned | Component skew, tombstoning |
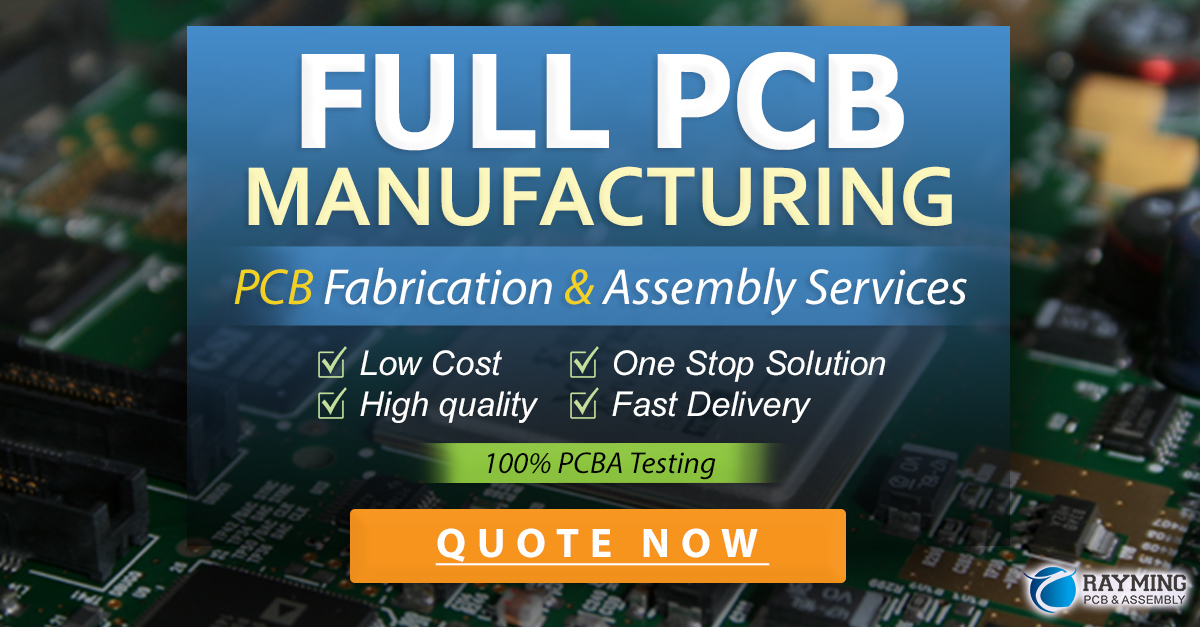
Solder Paste Testing Standards
There are several industry standards that provide guidelines for solder paste testing. These standards ensure consistency and reliability in the manufacturing process. Some of the most common standards are:
IPC-7527
IPC-7527 is a standard for solder paste printing inspection. It provides guidelines for the measurement and evaluation of solder paste deposits, including volume, height, area, and alignment.
IPC-A-610
IPC-A-610 is a standard for the acceptability of electronic assemblies. It includes guidelines for solder joint inspection, including visual criteria for acceptable solder joints.
J-STD-001
J-STD-001 is a standard for soldered electrical and electronic assemblies. It includes requirements for solder paste printing, including solder paste volume, height, and alignment.
Solder Paste Testing Equipment
There are several types of equipment used for solder paste testing, each with its own capabilities and limitations. Some of the most common types of equipment are:
Solder Paste Inspection (SPI) Systems
SPI systems are automated systems that use 3D measurement techniques to inspect solder paste deposits. They can measure solder paste volume, height, area, and alignment, and compare these measurements to predefined criteria.
Advantages:
– Highly accurate and repeatable
– Can inspect large volumes quickly
– Provides detailed 3D measurements
Disadvantages:
– Expensive
– Requires specialized training to operate
– Can be affected by highly reflective surfaces
Automated Optical Inspection (AOI) Systems
AOI systems use cameras and image processing software to automatically inspect solder paste deposits. They can detect defects such as insufficient solder paste, bridging, or misalignment.
Advantages:
– Automated and objective
– Can inspect large volumes quickly
– Can detect subtle defects
Disadvantages:
– Limited to 2D inspection
– Can be affected by variations in lighting or PCB color
– May require specialized programming for each PCB design
X-Ray Inspection Systems
X-ray inspection systems use x-rays to image the internal structure of solder joints. They can detect defects such as voids, cracks, or insufficient solder.
Advantages:
– Can inspect hidden solder joints
– Provides detailed internal images
– Can detect defects not visible with other methods
Disadvantages:
– Expensive
– Slower than other methods
– Potential safety concerns with x-ray exposure
Best Practices for Solder Paste Testing
To ensure the effectiveness of solder paste testing, there are several best practices that should be followed:
-
Establish Clear Criteria: Clearly define the acceptable ranges for solder paste volume, height, area, and alignment based on industry standards and the specific requirements of the PCB design.
-
Use Appropriate Equipment: Select the appropriate testing equipment based on the specific needs of the manufacturing process. Consider factors such as accuracy, speed, and cost.
-
Calibrate Equipment Regularly: Regularly calibrate testing equipment to ensure accurate and reliable measurements.
-
Train Operators: Provide thorough training to operators on the use of testing equipment and the interpretation of results.
-
Implement Statistical Process Control: Use statistical process control (SPC) techniques to monitor the solder paste printing process over time. This can help to identify trends and potential issues before they lead to defects.
-
Take Corrective Action: When defects are identified, take prompt corrective action to address the root cause of the problem. This may involve adjusting the solder paste printing process, replacing components, or modifying the PCB design.
Frequently Asked Questions (FAQ)
-
What is solder paste testing?
Solder paste testing is the process of inspecting and evaluating the quality of solder paste deposits on a printed circuit board (PCB). It involves measuring parameters such as solder paste volume, height, area, and alignment to ensure that they meet the required standards. -
Why is solder paste testing important?
Solder paste testing is important because the quality of the solder paste printing process directly affects the reliability and functionality of the final product. Testing helps to identify defects early in the manufacturing process, reduce rework and scrap, and ensure consistent quality. -
What are the common methods of solder paste testing?
The common methods of solder paste testing include visual inspection, 2D automated optical inspection (AOI), 3D solder paste inspection (SPI), and x-ray inspection. Each method has its own advantages and disadvantages in terms of accuracy, speed, and cost. -
What parameters are measured in solder paste testing?
The key parameters measured in solder paste testing are solder paste volume, height, area, and alignment. These parameters are critical for forming reliable solder joints and ensuring proper component placement. -
What are some best practices for solder paste testing?
Some best practices for solder paste testing include establishing clear criteria, using appropriate equipment, calibrating equipment regularly, training operators, implementing statistical process control, and taking prompt corrective action when defects are identified.
Conclusion
Solder paste testing is a critical process in the manufacturing of printed circuit boards. It helps to ensure the quality and reliability of the final product by identifying defects early in the manufacturing process. There are several methods and equipment used for solder paste testing, each with its own advantages and disadvantages. By following best practices and industry standards, manufacturers can optimize their solder paste printing process and produce high-quality products consistently.
Leave a Reply