What is PCB Contamination?
Printed circuit board (PCB) contamination refers to the presence of unwanted substances or impurities on the surface of a PCB. These contaminants can come from various sources, such as:
- Dust and dirt particles
- Oils and greases from handling or manufacturing processes
- Flux residues from soldering
- Chemical residues from cleaning agents
- Moisture or humidity
PCB contamination can have significant impacts on the performance, reliability, and lifespan of electronic systems. It is essential for manufacturers and designers to understand the types of contaminants, their effects, and prevention methods to ensure optimal system performance.
Types of PCB Contaminants
PCB contaminants can be categorized into three main types:
-
Particulate Contamination: This type includes dust, dirt, fibers, and other small particles that settle on the PCB surface. These particles can cause short circuits, interfere with electrical connections, and hinder heat dissipation.
-
Chemical Contamination: Chemical contaminants include flux residues, cleaning agent residues, and other chemical substances that can react with the PCB materials or components. These contaminants can cause corrosion, delamination, and degradation of the PCB.
-
Moisture Contamination: Moisture or humidity can lead to the formation of dendrites, which are metallic growths that can cause short circuits. Moisture can also promote the growth of mold or other microorganisms that can damage the PCB.
Effects of PCB Contamination on System Performance
PCB contamination can have various negative effects on system performance, including:
-
Decreased Reliability: Contaminants can cause intermittent or permanent failures in electronic components, leading to reduced system reliability. Short circuits, open circuits, and other issues caused by contamination can result in unexpected system behavior or complete failure.
-
Reduced Lifespan: Contamination can accelerate the degradation of PCB materials and components, shortening the overall lifespan of the electronic system. Chemical contaminants, in particular, can cause corrosion and weaken the structural integrity of the PCB.
-
Impaired Electrical Performance: Contaminants can interfere with electrical connections, causing increased resistance, capacitance, or inductance. This can lead to signal integrity issues, such as crosstalk, signal reflections, and electromagnetic interference (EMI).
-
Thermal Management Issues: Particulate contamination can hinder heat dissipation by blocking air flow or insulating heat-generating components. This can lead to overheating, which can cause component failure or reduce the overall efficiency of the system.
-
Manufacturing and Assembly Challenges: Contamination can cause issues during the manufacturing and assembly process, such as poor solder joint formation, inaccurate component placement, and difficulties in inspection and testing.
Preventing PCB Contamination
To minimize the risks associated with PCB contamination, manufacturers and designers can implement various prevention strategies:
Cleanliness in Manufacturing
Maintaining a clean manufacturing environment is crucial for preventing particulate and chemical contamination. This can be achieved through:
- Implementing proper air filtration systems to remove dust and other particles
- Using clean room protocols, such as gowning, gloves, and shoe covers
- Regularly cleaning and maintaining production equipment
- Properly storing and handling PCB materials and components
Proper Handling and Storage
Proper handling and storage practices can help prevent contamination during the manufacturing process and in the field. Some best practices include:
- Using ESD-safe gloves when handling PCBs to prevent oils and greases from contaminating the surface
- Storing PCBs in sealed, moisture-barrier bags with desiccants to prevent moisture contamination
- Avoiding exposure to extreme temperatures or humidity during storage and transportation
Flux Management
Flux residues from soldering can be a significant source of chemical contamination. To minimize flux-related issues:
- Use no-clean or low-residue flux whenever possible
- Ensure proper flux application and avoid excessive amounts
- Implement effective cleaning processes to remove flux residues, such as using appropriate solvents or aqueous cleaning systems
Cleaning and Inspection
Regular cleaning and inspection of PCBs can help identify and remove contaminants before they cause significant damage. Some cleaning and inspection methods include:
- Visual inspection using microscopes or automated optical inspection (AOI) systems
- X-ray inspection for identifying internal contamination or defects
- Ionic contamination testing to measure the level of ionic residues on the PCB surface
- Cleaning with solvents, aqueous systems, or plasma cleaning technologies
Design Considerations
PCB designers can also take steps to minimize the impact of contamination by:
- Selecting materials and components that are resistant to contamination and corrosion
- Designing adequate spacing between components to prevent short circuits caused by particulate contamination
- Incorporating conformal coatings or encapsulation to protect the PCB from moisture and other environmental contaminants
- Designing for manufacturability and testability to facilitate cleaning and inspection processes
Case Studies
To illustrate the impact of PCB contamination on system performance, let’s look at two case studies:
Case Study 1: Automotive Electronics
An automotive electronics manufacturer experienced a high rate of field failures in one of their engine control modules (ECMs). Upon investigation, it was discovered that the failures were caused by particulate contamination on the PCBs. The contaminants, which included dust and small fibers, had caused short circuits and intermittent connections, leading to erratic engine performance and complete ECM failure.
To address the issue, the manufacturer implemented several changes in their production process, including:
- Upgrading their air filtration system to achieve a higher level of cleanliness in the manufacturing environment
- Implementing strict clean room protocols for all personnel involved in PCB handling and assembly
- Improving their inspection process to include automated optical inspection (AOI) for detecting particulate contamination
After implementing these changes, the field failure rate for the ECMs dropped significantly, resulting in improved customer satisfaction and reduced warranty costs.
Case Study 2: Telecommunications Equipment
A telecommunications equipment manufacturer experienced a series of failures in their optical transceiver modules. The failures were characterized by increased bit error rates and signal degradation. Upon analysis, it was found that the failures were caused by chemical contamination on the PCBs, specifically flux residues from the soldering process.
To resolve the issue, the manufacturer took the following actions:
- Switched to a low-residue, no-clean flux for their soldering process
- Implemented a more rigorous cleaning process using an aqueous cleaning system to remove any remaining flux residues
- Conducted ionic contamination testing on a sample of PCBs to ensure that the cleaning process was effective
By addressing the chemical contamination issue, the manufacturer was able to improve the reliability and performance of their optical transceiver modules, reducing field failures and customer complaints.
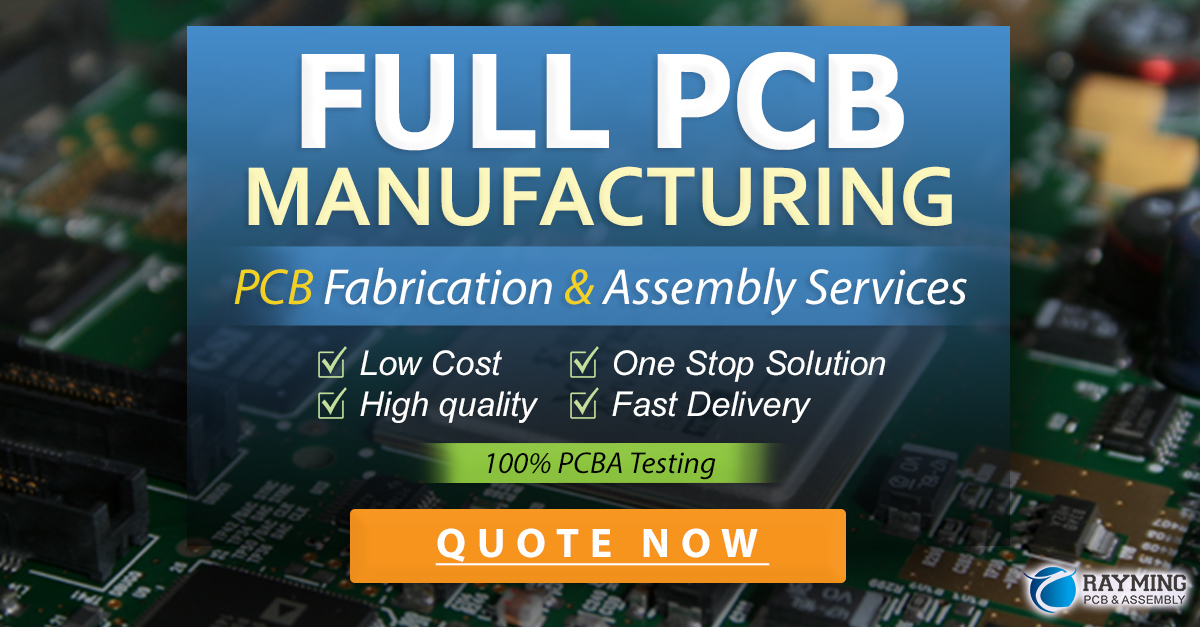
FAQ
-
Q: What are the most common types of PCB contaminants?
A: The most common types of PCB contaminants are particulate contamination (dust, dirt, fibers), chemical contamination (flux residues, cleaning agent residues), and moisture contamination. -
Q: How can PCB contamination affect system reliability?
A: PCB contamination can cause intermittent or permanent failures in electronic components, leading to reduced system reliability. Short circuits, open circuits, and other issues caused by contamination can result in unexpected system behavior or complete failure. -
Q: What are some best practices for preventing PCB contamination during manufacturing?
A: Best practices for preventing PCB contamination during manufacturing include maintaining a clean production environment, implementing proper handling and storage procedures, managing flux usage, and conducting regular cleaning and inspection. -
Q: Can PCB designers help minimize the impact of contamination?
A: Yes, PCB designers can help minimize the impact of contamination by selecting materials and components that are resistant to contamination and corrosion, designing adequate spacing between components, incorporating conformal coatings or encapsulation, and designing for manufacturability and testability. -
Q: How can ionic contamination testing help in ensuring PCB cleanliness?
A: Ionic contamination testing measures the level of ionic residues on the PCB surface. By conducting this testing, manufacturers can verify the effectiveness of their cleaning processes and ensure that the PCBs meet the required cleanliness standards, reducing the risk of contamination-related failures.
In conclusion, PCB contamination is a critical issue that can significantly impact the performance, reliability, and lifespan of electronic systems. By understanding the types of contaminants, their effects, and implementing proper prevention and mitigation strategies, manufacturers and designers can ensure optimal system performance and customer satisfaction.
Leave a Reply