Introduction to Hall Effect Sensors
A Hall effect sensor is a type of transducer that converts magnetic fields into electrical signals. It is based on the Hall effect, which was discovered by Edwin Hall in 1879. The Hall effect occurs when a current-carrying conductor is placed in a magnetic field perpendicular to the current flow. This generates a voltage difference across the conductor, known as the Hall voltage, which is proportional to the strength of the magnetic field and the current density.
Hall effect sensors are widely used in various applications, such as position sensing, speed detection, current sensing, and proximity switching. They offer several advantages over other types of sensors, including:
- Non-contact sensing: Hall effect sensors can detect magnetic fields without physical contact with the target object, making them suitable for harsh environments and reducing wear and tear.
- High reliability: With no moving parts, Hall effect sensors are less prone to mechanical failures and have a longer lifespan compared to mechanical sensors.
- Wide operating temperature range: Hall effect sensors can function in a wide temperature range, typically from -40°C to +150°C, making them suitable for various industrial applications.
- Fast response time: Hall effect sensors can detect changes in magnetic fields quickly, enabling high-speed sensing applications.
- Small size: Hall effect sensors are available in compact packages, allowing for integration into space-constrained applications.
Types of Hall Effect Sensors
There are three main types of Hall effect sensors:
-
Analog Hall effect sensors: These sensors provide a continuous analog output voltage that is proportional to the strength of the magnetic field. They are suitable for applications that require precise position or speed measurements.
-
Digital Hall effect sensors: Also known as switch-type Hall effect sensors, these devices provide a digital output (ON/OFF) when the magnetic field strength exceeds a certain threshold. They are commonly used in proximity sensing, limit switches, and rotary encoding applications.
-
Ratiometric Hall effect sensors: These sensors provide an output voltage that is proportional to the supply voltage and the strength of the magnetic field. They offer improved accuracy and temperature stability compared to analog Hall effect sensors.
Hall Effect Sensor Pinout
The pinout of a Hall effect sensor depends on the specific device and package type. However, most Hall effect sensors share a common set of pins:
-
VCC (Power Supply): This pin is connected to the positive power supply, typically ranging from 3.3V to 5V.
-
GND (Ground): This pin is connected to the ground or negative power supply.
-
OUT (Output): This pin provides the sensor’s output signal, which can be analog, digital, or ratiometric, depending on the sensor type.
-
EN (Enable) or !SLEEP: Some Hall effect sensors have an enable or sleep pin that allows the user to control the sensor’s power state. When the enable pin is pulled high, the sensor is activated; when pulled low, the sensor enters a low-power sleep mode.
Here’s an example pinout for a typical 3-pin Hall effect sensor (e.g., AH3503):
Pin Number | Pin Name | Function |
---|---|---|
1 | VCC | Power Supply (3.3V to 5V) |
2 | GND | Ground |
3 | OUT | Output Signal |
For a 4-pin Hall effect sensor (e.g., DRV5053):
Pin Number | Pin Name | Function |
---|---|---|
1 | VCC | Power Supply (3.3V to 5V) |
2 | GND | Ground |
3 | OUT | Output Signal |
4 | EN | Enable (Active High) |
It’s essential to refer to the datasheet of the specific Hall effect sensor for accurate pinout information and electrical characteristics.
Features of Hall Effect Sensors
Hall effect sensors offer several key features that make them attractive for various applications:
-
Sensitivity: Hall effect sensors can detect magnetic fields as low as a few millitesla (mT) and up to several tesla (T). The sensitivity of a Hall effect sensor is determined by factors such as the sensor’s material, geometry, and operating conditions.
-
Linearity: Analog Hall effect sensors provide an output voltage that is linearly proportional to the applied magnetic field strength. This linearity allows for accurate position and speed measurements.
-
Temperature stability: Modern Hall effect sensors are designed to maintain stable performance over a wide temperature range. Some sensors incorporate temperature compensation techniques to minimize the effect of temperature variations on the output signal.
-
Programmable switching points: Digital Hall effect sensors often feature programmable switching points, allowing users to adjust the magnetic field threshold at which the sensor’s output changes state. This flexibility enables the sensor to be adapted to different application requirements.
-
Integrated signal conditioning: Some Hall effect sensors include built-in signal conditioning circuitry, such as amplifiers, filters, and hysteresis control. This integration simplifies the overall system design and improves signal quality.
-
Robust packaging: Hall effect sensors are available in various package types, including through-hole, surface-mount, and IP-rated packages. These packaging options enable the sensors to be used in harsh environments and withstand mechanical stress.
-
Magnetic field polarity detection: Hall effect sensors can detect both the presence and polarity of magnetic fields. This capability is useful in applications such as rotary encoding, where the direction of rotation needs to be determined.
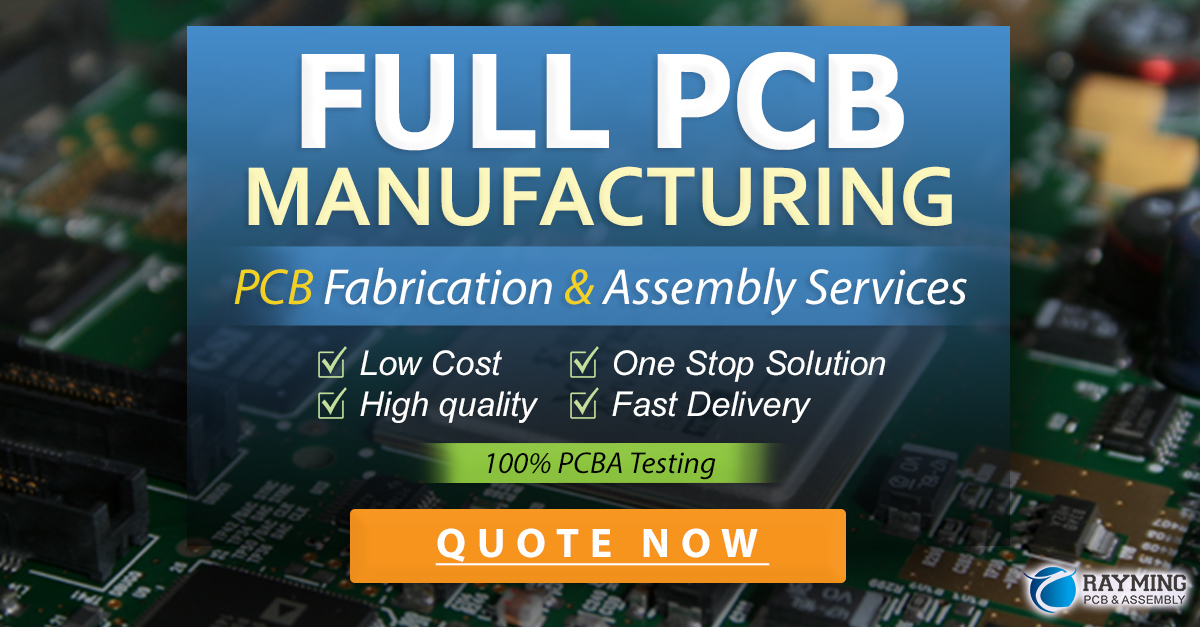
Alternatives to Hall Effect Sensors
While Hall effect sensors are widely used, there are several alternative technologies for magnetic field sensing and position detection:
-
Reed switches: Reed switches are mechanical switches that consist of two ferromagnetic contacts sealed in a glass envelope. When a magnetic field is applied, the contacts close, creating an electrical connection. Reed switches are simple and low-cost but have a shorter lifespan compared to Hall effect sensors due to their mechanical nature.
-
Magnetoresistive sensors: Magnetoresistive sensors, such as anisotropic magnetoresistive (AMR) and giant magnetoresistive (GMR) sensors, change their electrical resistance in the presence of a magnetic field. They offer higher sensitivity and smaller size compared to Hall effect sensors but are more expensive and require more complex signal conditioning.
-
Inductive sensors: Inductive sensors detect the presence of metallic objects by measuring changes in the sensor’s magnetic field caused by eddy currents induced in the target object. They are robust and can detect both ferrous and non-ferrous metals but have a shorter sensing range compared to Hall effect sensors.
-
Optical encoders: Optical encoders use a light source, a photodetector, and a patterned disk or strip to detect position or speed. They offer high resolution and accuracy but are more susceptible to dust, dirt, and misalignment compared to Hall effect sensors.
-
Capacitive sensors: Capacitive sensors detect the presence of objects by measuring changes in the sensor’s capacitance caused by the proximity of the target object. They can detect both conductive and non-conductive materials but are sensitive to environmental factors such as humidity and temperature.
The choice between a Hall effect sensor and an alternative technology depends on the specific application requirements, such as sensing range, accuracy, environmental conditions, and cost.
Applications of Hall Effect Sensors
Hall effect sensors find applications in a wide range of industries and products, including:
- Automotive: In the automotive industry, Hall effect sensors are used for various purposes, such as:
- Wheel speed sensing for anti-lock braking systems (ABS) and traction control systems (TCS)
- Throttle position sensing for electronic throttle control (ETC)
- Crankshaft and camshaft position sensing for engine management systems
- Gear position sensing for transmission control
-
Pedal position sensing for electronic throttle and brake systems
-
Industrial: Hall effect sensors are used in industrial applications for:
- Rotary encoding for position and speed monitoring of motors, gears, and shafts
- Limit switch detection for machine safeguarding and position control
- Proximity sensing for conveyor systems and material handling equipment
-
Current sensing for motor protection and power monitoring
-
Consumer electronics: Hall effect sensors are found in various consumer products, such as:
- Smartphones and tablets for detecting the presence of a magnetic case or cover
- Laptops for detecting the closure of the lid
- Gaming controllers for detecting the position of joysticks and triggers
-
Electronic compasses for determining the orientation of the device
-
Medical equipment: Hall effect sensors are used in medical applications, including:
- Position sensing for robotic surgery systems
- Fluid level detection for infusion pumps and dialysis machines
-
Rotation sensing for centrifuges and blood separators
-
Aerospace and defense: Hall effect sensors are employed in aerospace and defense applications, such as:
- Position sensing for flight control surfaces and actuators
- Gear position sensing for landing gear systems
-
Current sensing for power distribution and protection systems
-
Home automation: Hall effect sensors are used in smart home applications, including:
- Door and window sensors for security systems
- Appliance position sensing for washing machines and refrigerators
-
Water flow sensing for smart irrigation systems
-
Robotics: Hall effect sensors are used in robotic applications for:
- Joint position sensing for robotic arms and legs
- Wheel speed sensing for mobile robots and autonomous vehicles
- End-effector position sensing for robotic grippers and tools
These are just a few examples of the many applications where Hall effect sensors are employed. As technology advances and new use cases emerge, the importance and versatility of Hall effect sensors continue to grow.
FAQs
-
What is the difference between analog and digital Hall effect sensors?
Analog Hall effect sensors provide a continuous output voltage proportional to the strength of the magnetic field, while digital Hall effect sensors provide a discrete ON/OFF output when the magnetic field exceeds a certain threshold. -
Can Hall effect sensors detect the polarity of a magnetic field?
Yes, Hall effect sensors can detect both the presence and polarity of magnetic fields. This capability is useful in applications such as rotary encoding, where the direction of rotation needs to be determined. -
What is the typical operating temperature range for Hall effect sensors?
Hall effect sensors can function in a wide temperature range, typically from -40°C to +150°C. However, the specific operating temperature range may vary depending on the sensor model and manufacturer. -
How do I choose the right Hall effect sensor for my application?
When selecting a Hall effect sensor, consider factors such as the required sensing range, accuracy, output type (analog, digital, or ratiometric), operating temperature range, package type, and cost. Consult the sensor’s datasheet and application notes to ensure it meets your specific requirements. -
Can Hall effect sensors be used in harsh environments?
Yes, Hall effect sensors are well-suited for use in harsh environments. They have no moving parts, making them resistant to vibration and shock. Many Hall effect sensors are available in robust, IP-rated packages that protect against dust, moisture, and other environmental factors.
Conclusion
Hall effect sensors are versatile and reliable devices that convert magnetic fields into electrical signals. They offer numerous advantages, such as non-contact sensing, high reliability, wide operating temperature range, fast response time, and small size. With a variety of output types and programmable features, Hall effect sensors can be adapted to suit a wide range of applications across industries, including automotive, industrial, consumer electronics, medical equipment, aerospace, defense, home automation, and robotics.
When selecting a Hall effect sensor, it is essential to consider the specific requirements of the application, such as sensing range, accuracy, output type, and environmental conditions. By understanding the features and alternatives to Hall effect sensors, engineers and designers can make informed decisions when implementing magnetic field sensing solutions in their projects.
As technology continues to advance, Hall effect sensors will likely find new applications and play an increasingly important role in the development of smart, connected, and autonomous systems. With their robust performance and adaptability, Hall effect sensors are poised to remain a key component in the sensor landscape for years to come.
Leave a Reply