Introduction to PCB Grounding
Printed Circuit Boards (PCBs) are the backbone of modern electronics, providing a platform for interconnecting electronic components and enabling the functioning of complex circuits. One critical aspect of PCB design is proper grounding, which ensures the stability, performance, and reliability of the electronic system. In this comprehensive article, we will delve into the fundamentals of PCB grounding, explore various grounding techniques, and discuss best practices for achieving optimal grounding in PCB designs.
What is PCB Grounding?
PCB grounding refers to the process of creating a low-impedance path for electrical currents to return to their source, typically the power supply or ground plane. The primary purpose of grounding is to establish a common reference point for all signals within the circuit, minimize noise and interference, and protect sensitive components from electrical disturbances.
Grounding plays a crucial role in several aspects of PCB design, including:
-
Signal integrity: Proper grounding helps maintain the quality and integrity of signals by providing a stable reference point and minimizing crosstalk and electromagnetic interference (EMI).
-
Power distribution: Grounding ensures efficient and uniform distribution of power throughout the PCB, reducing voltage drops and maintaining consistent supply voltages.
-
Electromagnetic compatibility (EMC): Effective grounding techniques help mitigate electromagnetic emissions and susceptibility, ensuring compliance with EMC regulations and preventing interference with other electronic devices.
-
Safety: Grounding protects users and equipment from electrical hazards by providing a safe path for fault currents to flow, preventing electric shock and fire hazards.
Types of Grounding in PCBs
There are several types of grounding techniques used in PCB design, each with its own characteristics and applications. Let’s explore the most common grounding methods:
1. Ground Plane
A ground plane is a large, continuous copper area on one or more layers of the PCB, typically connected to the ground (GND) pin of the power supply. The ground plane serves as a low-impedance return path for currents and helps maintain a stable reference voltage throughout the board.
Benefits of using a ground plane include:
- Reduced impedance: The large surface area of the ground plane minimizes the impedance of the return path, allowing currents to flow more easily and reducing voltage drops.
- Improved signal integrity: The ground plane provides a consistent reference voltage for signals, minimizing crosstalk and EMI.
- Enhanced EMI shielding: The ground plane acts as a shield, absorbing and attenuating electromagnetic emissions from the circuit.
2. Split Ground Plane
In some cases, it may be necessary to separate different sections of the ground plane to isolate noisy or sensitive circuits. This technique is known as split ground plane or partitioned ground plane.
A split ground plane involves dividing the ground plane into separate regions, each dedicated to a specific part of the circuit. The regions are connected through a single point, often referred to as a “star point” or “single point ground.”
Advantages of using a split ground plane include:
- Noise isolation: Separating noisy circuits from sensitive circuits helps prevent noise coupling and interference.
- Improved signal integrity: By isolating different sections of the circuit, a split ground plane minimizes crosstalk and maintains signal quality.
- Flexibility in design: Split ground planes allow designers to optimize the grounding for specific parts of the circuit, tailoring it to their unique requirements.
3. Chassis Ground
Chassis ground, also known as frame ground or earth ground, refers to the connection between the PCB’s ground and the metal chassis or enclosure of the electronic device. This connection is typically made through mounting holes or dedicated grounding points on the PCB.
The primary purposes of chassis ground are:
- Safety: Chassis ground provides a path for fault currents to flow, protecting users from electrical hazards.
- EMI shielding: Connecting the PCB’s ground to the chassis helps create a Faraday cage, reducing electromagnetic emissions and susceptibility.
It’s important to ensure a low-impedance connection between the PCB’s ground and the chassis to achieve effective grounding and shielding.
4. Hybrid Grounding
Hybrid grounding combines multiple grounding techniques to achieve the best balance between signal integrity, noise isolation, and EMI performance. This approach involves using a combination of ground planes, split ground planes, and chassis ground, depending on the specific requirements of the PCB design.
Hybrid grounding allows designers to optimize the grounding for different sections of the circuit while maintaining overall grounding integrity. It requires careful planning and analysis to ensure proper implementation and avoid potential issues such as ground loops or impedance mismatches.
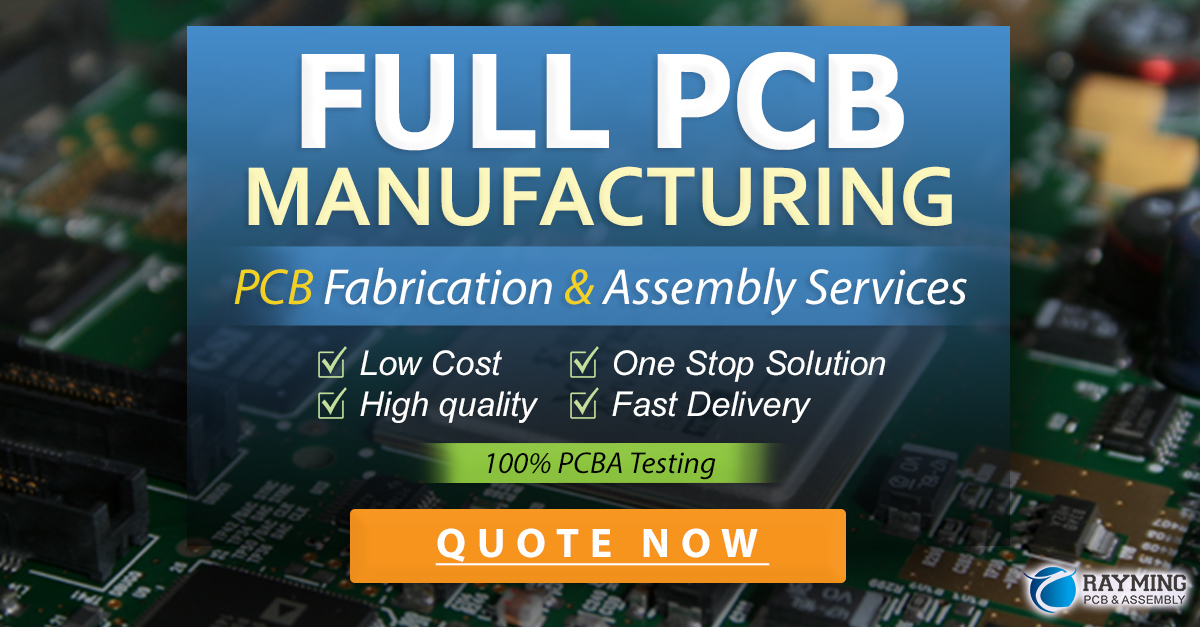
PCB Grounding Best Practices
To achieve optimal grounding in PCB designs, consider the following best practices:
-
Use a solid ground plane: Whenever possible, use a continuous ground plane on one or more layers of the PCB to provide a low-impedance return path and maintain a stable reference voltage.
-
Minimize ground impedance: Keep ground traces and connections as short and wide as possible to minimize impedance and ensure efficient current flow.
-
Avoid ground loops: Prevent the formation of ground loops by ensuring that there is only one path for ground currents to flow. Use star point grounding or split ground planes when necessary.
-
Separate noisy and sensitive circuits: Isolate noisy circuits, such as power supplies or high-speed digital circuits, from sensitive analog or RF circuits to prevent noise coupling and interference.
-
Use appropriate decoupling capacitors: Place decoupling capacitors close to the power pins of ICs to provide a local, low-impedance path for high-frequency noise and prevent it from spreading throughout the PCB.
-
Consider EMI shielding: Implement proper EMI shielding techniques, such as grounded shields or Faraday cages, to minimize electromagnetic emissions and susceptibility.
-
Follow layout guidelines: Adhere to recommended layout guidelines for grounding, such as maintaining appropriate clearances, avoiding sharp corners or long ground traces, and using ground vias strategically.
-
Simulate and test: Perform simulations and testing to validate the grounding design and identify potential issues early in the development process.
PCB Grounding Techniques Comparison
The following table provides a comparison of the different PCB grounding techniques discussed in this article:
Grounding Technique | Advantages | Disadvantages |
---|---|---|
Ground Plane | – Low impedance return path – Improved signal integrity – Enhanced EMI shielding |
– May increase PCB complexity and manufacturing cost |
Split Ground Plane | – Noise isolation – Improved signal integrity – Flexibility in design |
– Requires careful planning and implementation – Potential for ground loops |
Chassis Ground | – Safety – EMI shielding |
– Requires proper connection to chassis – Potential for ground loops |
Hybrid Grounding | – Optimized grounding for different circuit sections – Balanced performance |
– Requires careful planning and analysis – Increased complexity |
Frequently Asked Questions (FAQ)
-
Q: What is the purpose of grounding in PCB design?
A: The purpose of grounding in PCB design is to establish a common reference point for all signals, minimize noise and interference, ensure efficient power distribution, and protect users and equipment from electrical hazards. -
Q: What is the difference between a ground plane and a split ground plane?
A: A ground plane is a continuous copper area that serves as a low-impedance return path for currents, while a split ground plane involves dividing the ground plane into separate regions to isolate noisy or sensitive circuits. -
Q: How does chassis ground contribute to EMI shielding?
A: Connecting the PCB’s ground to the metal chassis or enclosure creates a Faraday cage, which helps absorb and attenuate electromagnetic emissions, reducing the device’s susceptibility to external EMI. -
Q: What are some best practices for achieving optimal grounding in PCB designs?
A: Best practices for optimal grounding include using a solid ground plane, minimizing ground impedance, avoiding ground loops, separating noisy and sensitive circuits, using appropriate decoupling capacitors, implementing EMI shielding, following layout guidelines, and performing simulations and testing. -
Q: What is the role of hybrid grounding in PCB design?
A: Hybrid grounding combines multiple grounding techniques to achieve the best balance between signal integrity, noise isolation, and EMI performance, allowing designers to optimize the grounding for different sections of the circuit while maintaining overall grounding integrity.
Conclusion
Proper grounding is essential for the optimal performance, reliability, and safety of PCBs. By understanding the fundamentals of PCB grounding, exploring various grounding techniques, and following best practices, designers can create robust and efficient electronic systems.
This article has provided a comprehensive overview of PCB grounding, covering topics such as ground planes, split ground planes, chassis ground, and hybrid grounding. By comparing the advantages and disadvantages of each technique and addressing frequently asked questions, we aim to equip readers with the knowledge necessary to make informed decisions when designing PCBs.
Remember, effective grounding requires careful planning, analysis, and implementation. By considering factors such as signal integrity, noise isolation, EMI performance, and safety, designers can optimize their PCB grounding strategies and ensure the success of their electronic projects.
Leave a Reply