Introduction to Gold PCBs
Gold PCBs, also known as gold-plated printed circuit boards, are a type of PCB that features a thin layer of gold coating on the surface of the copper traces and pads. This gold finishing is applied through either an immersion or electroplating process, which provides enhanced protection and improved performance for the circuit board.
The use of gold in PCB manufacturing has become increasingly popular due to its excellent electrical conductivity, corrosion resistance, and durability. Gold PCBs are widely used in various industries, including aerospace, military, medical, and high-end consumer electronics, where reliability and longevity are critical factors.
Advantages of Gold PCBs
-
Enhanced Corrosion Resistance: Gold is highly resistant to oxidation and corrosion, providing long-term protection for the copper traces and pads on the PCB. This is particularly important in harsh environments or applications where the PCB may be exposed to moisture, chemicals, or extreme temperatures.
-
Improved Electrical Conductivity: Gold has excellent electrical conductivity, which helps to minimize signal loss and improve the overall performance of the circuit board. This is especially crucial in high-frequency applications or designs with fine-pitch components.
-
Better Solderability: Gold-plated surfaces offer superior solderability compared to bare copper or other surface finishes. The gold layer prevents the formation of oxide layers on the copper, ensuring a reliable and consistent solder joint during the assembly process.
-
Extended Shelf Life: Gold PCBs have a longer shelf life compared to other surface finishes. The gold layer prevents the copper from tarnishing or oxidizing over time, allowing the PCBs to be stored for extended periods without compromising their quality or performance.
-
Compatibility with Wire Bonding: Gold is the preferred surface finish for wire bonding, a process commonly used in semiconductor packaging and high-density interconnect (HDI) PCBs. The gold layer provides a stable and reliable surface for the bonding of gold or aluminum wires.
Gold Immersion Process
Gold immersion, also known as immersion gold or electroless nickel immersion gold (ENIG), is a chemical process that deposits a thin layer of gold onto the surface of the copper traces and pads. The process involves several steps:
-
Cleaning: The PCB surface is thoroughly cleaned to remove any contaminants or oxides that may interfere with the plating process.
-
Microetching: A mild etching solution is applied to the copper surface to create a slightly roughened profile, which improves the adhesion of the subsequent layers.
-
Nickel Plating: A thin layer of electroless nickel is deposited onto the copper surface. This nickel layer acts as a barrier between the copper and the gold, preventing the formation of intermetallic compounds that can cause brittleness and reduced solderability.
-
Gold Immersion: The PCB is immersed in a gold solution, where the gold ions displace the nickel ions on the surface, resulting in a thin, uniform layer of gold.
The typical thickness of the gold layer in the immersion process ranges from 0.05 to 0.2 microns (2 to 8 microinches). This thin layer is sufficient to provide the necessary protection and enhanced properties without significantly adding to the cost of the PCB.
Advantages of Gold Immersion
-
Cost-effective: Gold immersion is a relatively inexpensive process compared to electroplating, as it requires less gold and has a simpler setup.
-
Uniform Coverage: The immersion process results in a uniform gold layer across the entire PCB surface, ensuring consistent protection and performance.
-
Suitable for Fine-Pitch Components: The thin gold layer produced by immersion is well-suited for PCBs with fine-pitch components or high-density designs.
Disadvantages of Gold Immersion
-
Limited Wear Resistance: The thin gold layer provided by immersion may not be sufficient for applications that require high wear resistance or frequent mating cycles.
-
Potential for Black Pad: In some cases, the immersion process can lead to the formation of “black pad,” a defect characterized by a dark, brittle nickel layer beneath the gold. This can cause solderability issues and reduced reliability.
Gold Electroplating Process
Gold electroplating, also known as electrolytic gold plating, is an electrochemical process that deposits a thicker layer of gold onto the surface of the copper traces and pads. The process involves the following steps:
-
Cleaning: As with the immersion process, the PCB surface is cleaned to remove contaminants and oxides.
-
Activation: The copper surface is activated using a mild acid solution to improve the adhesion of the subsequent layers.
-
Nickel Plating: A layer of electroplated nickel is deposited onto the copper surface. This nickel layer serves as a barrier and provides a smooth, uniform surface for the gold plating.
-
Gold Electroplating: The PCB is placed in a gold plating bath, where an electric current is applied. The gold ions in the solution are attracted to the nickel surface, resulting in the deposition of a gold layer.
The thickness of the gold layer in the electroplating process can range from 0.5 to 2.5 microns (20 to 100 microinches), depending on the specific requirements of the application.
Advantages of Gold Electroplating
-
Thicker Gold Layer: Electroplating produces a thicker gold layer compared to immersion, providing better wear resistance and durability.
-
Improved Wear Resistance: The thicker gold layer offers superior wear resistance, making it suitable for applications with frequent mating cycles or exposure to abrasive conditions.
-
Enhanced Wire Bonding: The thicker gold layer provided by electroplating is ideal for wire bonding applications, ensuring a reliable and stable connection between the PCB and the bonded wires.
Disadvantages of Gold Electroplating
-
Higher Cost: Gold electroplating is more expensive than immersion due to the thicker gold layer and the more complex setup required for the plating process.
-
Potential for Overplating: If not carefully controlled, the electroplating process can lead to overplating, resulting in excessive gold thickness that can cause issues with solderability and component fitment.
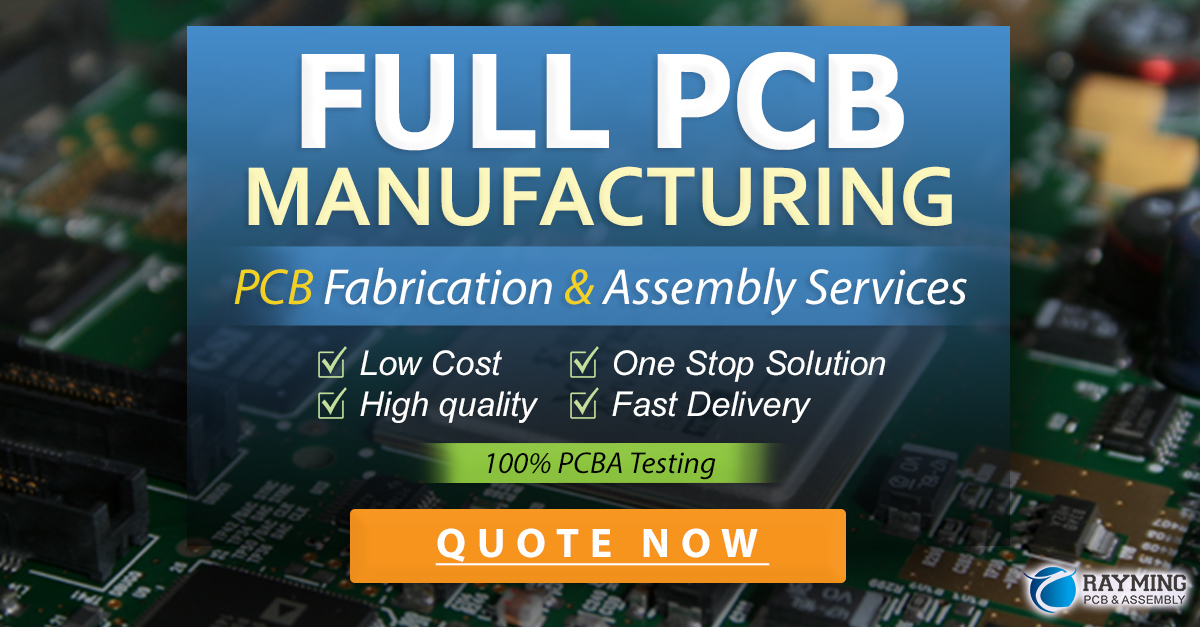
Choosing Between Gold Immersion and Electroplating
When deciding between gold immersion and electroplating for your PCB, consider the following factors:
-
Application Requirements: Evaluate the specific requirements of your application, such as the level of corrosion resistance, wear resistance, and electrical performance needed.
-
Cost Considerations: Compare the cost of immersion and electroplating processes, taking into account the gold thickness, PCB complexity, and production volume.
-
Component Compatibility: Consider the types of components used in your design and their compatibility with the gold thickness provided by each process.
-
Manufacturing Capabilities: Assess the capabilities of your PCB manufacturer and their experience with gold immersion and electroplating processes.
Factor | Gold Immersion | Gold Electroplating |
---|---|---|
Gold Thickness | 0.05 – 0.2 microns | 0.5 – 2.5 microns |
Cost | Lower | Higher |
Wear Resistance | Limited | Superior |
Corrosion Resistance | Good | Excellent |
Wire Bonding Suitability | Limited | Excellent |
Fine-Pitch Compatibility | Excellent | Good |
FAQ
-
Q: What is the difference between gold immersion and gold electroplating?
A: Gold immersion is a chemical process that deposits a thin layer of gold (0.05 – 0.2 microns) onto the PCB surface, while gold electroplating is an electrochemical process that deposits a thicker layer of gold (0.5 – 2.5 microns) using an electric current. -
Q: Which process is more cost-effective, gold immersion or electroplating?
A: Gold immersion is generally more cost-effective than electroplating, as it requires less gold and has a simpler setup. However, the total cost will depend on factors such as PCB complexity, production volume, and specific application requirements. -
Q: Can gold immersion provide sufficient wear resistance for high-use applications?
A: Gold immersion provides limited wear resistance due to the thin gold layer. For applications that require high wear resistance or frequent mating cycles, gold electroplating may be a more suitable choice. -
Q: Is gold immersion suitable for wire bonding applications?
A: While gold immersion can be used for wire bonding, the thin gold layer may not provide the optimal surface for reliable and stable bonding. Gold electroplating, with its thicker gold layer, is generally preferred for wire bonding applications. -
Q: Can gold electroplating cause issues with solderability?
A: If not properly controlled, gold electroplating can lead to overplating, resulting in an excessively thick gold layer that can cause issues with solderability and component fitment. Proper process control and monitoring are essential to ensure the desired gold thickness is achieved.
Conclusion
Gold PCBs offer numerous benefits, including enhanced corrosion resistance, improved electrical conductivity, better solderability, extended shelf life, and compatibility with wire bonding. The choice between gold immersion and electroplating depends on the specific requirements of the application, cost considerations, component compatibility, and manufacturing capabilities.
By understanding the advantages and disadvantages of each process and carefully evaluating your project needs, you can select the most suitable gold finishing method for your PCB. Working closely with an experienced PCB manufacturer can help ensure that your gold PCBs meet the highest standards of quality and reliability.
Leave a Reply