Introduction to Glass PCB
Glass PCB, also known as glass printed circuit board, is a revolutionary technology that has gained significant attention in the electronics industry. Unlike traditional PCBs that use copper and other metals as conductive materials, glass PCBs utilize a special type of glass substrate with embedded conductive traces. This innovative approach offers several advantages over conventional PCB manufacturing techniques, making glass PCBs an attractive option for various applications.
In this comprehensive article, we will delve into the world of glass PCBs, explaining their construction, benefits, applications, and addressing common questions that beginners may have. By the end of this article, you will have a solid understanding of glass PCBs and their potential in the electronics industry.
What is a Glass PCB?
A glass PCB is a printed circuit board that uses a glass substrate instead of the traditional FR-4 or other materials. The glass substrate is typically made from borosilicate glass, which is known for its excellent thermal and electrical properties. The conductive traces on a glass PCB are created using a process called thin-film deposition, where a thin layer of conductive material, such as copper or gold, is deposited onto the glass surface.
The resulting glass PCB offers several advantages over traditional PCBs, including:
- High thermal stability
- Low dielectric constant
- Excellent dimensional stability
- High transparency
- Resistance to harsh environments
These properties make glass PCBs suitable for a wide range of applications, from high-frequency electronics to aerospace and medical devices.
Construction of Glass PCBs
Glass Substrate
The foundation of a glass PCB is the glass substrate, which is typically made from borosilicate glass. Borosilicate glass is chosen for its excellent thermal and electrical properties, as well as its high resistance to thermal shock and chemical corrosion. The glass substrate is carefully selected based on the specific requirements of the application, such as thickness, transparency, and dielectric constant.
Thin-Film Deposition
To create the conductive traces on the glass substrate, a process called thin-film deposition is used. This process involves depositing a thin layer of conductive material, such as copper or gold, onto the glass surface. There are several methods for thin-film deposition, including:
- Sputtering
- Evaporation
- Chemical vapor deposition (CVD)
- Electroless plating
The choice of deposition method depends on factors such as the desired thickness of the conductive layer, the required adhesion strength, and the compatibility with the glass substrate.
Patterning and Etching
Once the conductive layer has been deposited onto the glass substrate, it needs to be patterned to create the desired circuit layout. This is typically done using photolithography, a process that involves:
- Applying a photoresist layer onto the conductive layer
- Exposing the photoresist to UV light through a mask that contains the circuit pattern
- Developing the photoresist to remove the exposed areas
- Etching away the unwanted conductive material using a chemical or physical process
- Removing the remaining photoresist
The result is a glass PCB with precisely patterned conductive traces that form the desired circuit layout.
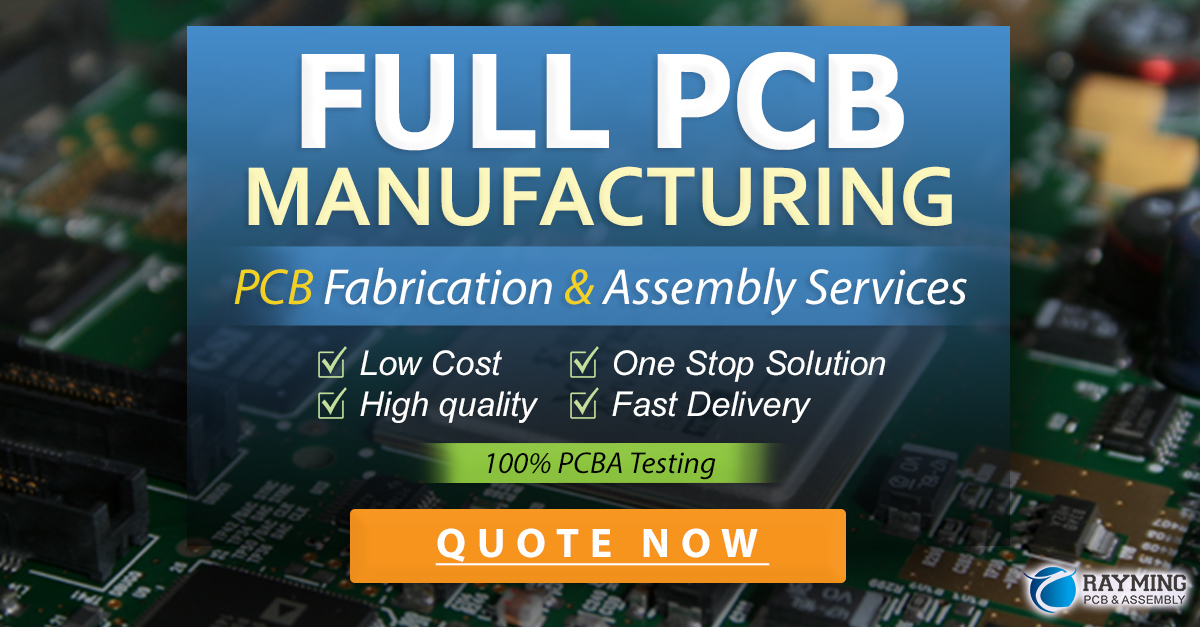
Benefits of Glass PCBs
High Thermal Stability
Glass PCBs offer excellent thermal stability compared to traditional PCBs. The glass substrate has a low coefficient of thermal expansion (CTE), which means it experiences minimal dimensional changes when exposed to temperature fluctuations. This property is particularly important in applications where thermal management is critical, such as high-power electronics or devices operating in extreme temperature environments.
Low Dielectric Constant
The glass substrate used in glass PCBs has a low dielectric constant, typically around 4.6 at 1 MHz. This low dielectric constant results in reduced signal propagation delay and lower power loss, making glass PCBs suitable for high-frequency applications. The low dielectric constant also enables the design of high-density circuit layouts with improved signal integrity.
Excellent Dimensional Stability
Glass PCBs exhibit excellent dimensional stability, thanks to the inherent properties of the glass substrate. Unlike traditional PCB materials, such as FR-4, glass does not absorb moisture and is not prone to warping or twisting. This dimensional stability is crucial for applications that require precise alignment and consistent performance over time, such as in optical devices or sensors.
High Transparency
One of the unique features of glass PCBs is their high transparency. The glass substrate can be made optically clear, allowing light to pass through the PCB. This property opens up new possibilities for applications that require light transmission, such as displays, optical sensors, or solar cells. The transparency of glass PCBs also enables visual inspection of the circuit layout, facilitating quality control and troubleshooting.
Resistance to Harsh Environments
Glass PCBs are highly resistant to harsh environments, including extreme temperatures, chemicals, and radiation. The glass substrate is chemically inert and does not react with most solvents or corrosive substances. Additionally, glass PCBs can withstand high levels of radiation, making them suitable for applications in aerospace, medical imaging, or nuclear facilities.
Applications of Glass PCBs
High-Frequency Electronics
Glass PCBs are particularly well-suited for high-frequency electronics, such as radio frequency (RF) circuits, millimeter-wave devices, and 5G applications. The low dielectric constant and excellent dimensional stability of glass PCBs enable the design of high-performance, low-loss circuits that can operate at higher frequencies compared to traditional PCBs.
Aerospace and Defense
The aerospace and defense industries have stringent requirements for electronic components, including resistance to extreme temperatures, vibrations, and radiation. Glass PCBs meet these requirements, thanks to their high thermal stability, dimensional stability, and resistance to harsh environments. Glass PCBs are used in various aerospace and defense applications, such as satellite communication systems, radar equipment, and avionics.
Medical Devices
Glass PCBs find applications in medical devices, particularly in implantable electronics and diagnostic equipment. The biocompatibility and chemical resistance of glass make it suitable for use in medical implants, such as pacemakers or neural stimulators. Additionally, the transparency of glass PCBs enables the design of optical sensors or imaging devices used in medical diagnostics.
Automotive Electronics
The automotive industry is increasingly adopting advanced electronic systems, such as advanced driver assistance systems (ADAS), autonomous driving, and electric vehicles. Glass PCBs can play a role in automotive electronics, offering high reliability, thermal stability, and resistance to harsh environments. Glass PCBs can be used in automotive sensors, control modules, or power electronics.
Consumer Electronics
Glass PCBs are finding their way into consumer electronics, particularly in applications that require high transparency or unique form factors. For example, glass PCBs can be used in touchscreens, displays, or wearable devices, where the transparency and flexibility of the glass substrate offer design advantages over traditional PCBs.
Frequently Asked Questions (FAQ)
1. Are glass PCBs more expensive than traditional PCBs?
Yes, glass PCBs are generally more expensive than traditional PCBs due to the specialized materials and manufacturing processes involved. However, the cost of glass PCBs is expected to decrease as the technology becomes more widely adopted and manufacturing processes are optimized.
2. Can glass PCBs be manufactured using the same equipment as traditional PCBs?
No, glass PCBs require specialized manufacturing equipment and processes, such as thin-film deposition and photolithography. Traditional PCB manufacturing equipment, such as through-hole drilling or surface-mount technology (SMT) assembly, may not be compatible with glass PCBs.
3. Are glass PCBs suitable for high-power applications?
Glass PCBs can be suitable for high-power applications, thanks to their high thermal stability and ability to dissipate heat effectively. However, the power handling capability of glass PCBs depends on factors such as the thickness of the conductive layer, the design of the circuit layout, and the thermal management techniques employed.
4. Can glass PCBs be flexible?
Yes, glass PCBs can be made flexible by using thin, flexible glass substrates. Flexible glass PCBs offer the benefits of glass, such as high transparency and chemical resistance, while providing the flexibility needed for certain applications, such as wearable devices or flexible displays.
5. Are there any limitations to the design of glass PCBs?
Glass PCBs have some design limitations compared to traditional PCBs. For example, the minimum feature size of conductive traces on glass PCBs is typically larger than that of copper traces on FR-4 PCBs. Additionally, the drilling and routing of glass PCBs can be more challenging due to the brittle nature of glass. However, advances in manufacturing technologies are continually pushing the boundaries of glass PCB design, enabling smaller feature sizes and more complex layouts.
Conclusion
Glass PCBs represent a significant advancement in printed circuit board technology, offering unique properties and benefits over traditional PCBs. With their high thermal stability, low dielectric constant, excellent dimensional stability, high transparency, and resistance to harsh environments, glass PCBs are well-suited for a wide range of applications, from high-frequency electronics to aerospace and medical devices.
As the demand for advanced electronic systems continues to grow, glass PCBs are poised to play an increasingly important role in the electronics industry. While the adoption of glass PCBs is still in its early stages, the technology shows great promise for enabling the next generation of high-performance, reliable, and innovative electronic devices.
As a beginner in the world of glass PCBs, it is essential to understand the fundamental concepts, benefits, and applications of this technology. By staying informed about the latest developments in glass PCB manufacturing and design, you can position yourself to take advantage of the opportunities that this innovative technology offers.
Property | Glass PCB | Traditional PCB (FR-4) |
---|---|---|
Thermal Stability | High (low CTE) | Moderate |
Dielectric Constant | Low (around 4.6 at 1 MHz) | Higher (around 4.5 at 1 MHz) |
Dimensional Stability | Excellent (minimal warping or twisting) | Good (prone to moisture absorption) |
Transparency | High (optically clear) | Opaque |
Environmental Resistance | High (resistant to chemicals, radiation) | Moderate |
Cost | Higher | Lower |
Manufacturing Process | Thin-film deposition, photolithography | Copper cladding, drilling, etching |
Design Limitations | Larger minimum feature size, brittle | Smaller minimum feature size, flexible |
Leave a Reply