Introduction to Frequency-Voltage Converters
A frequency-voltage converter, also known as an F/V converter or a frequency to voltage converter, is an electronic device that converts a frequency signal into a proportional voltage signal. This conversion is essential in various applications, such as sensor interfacing, motor speed control, and audio signal processing. The frequency-voltage converter plays a crucial role in translating mechanical or temporal information into an electrical signal that can be easily processed, analyzed, and integrated into larger systems.
Key Features of Frequency-Voltage Converters
-
Linearity: A good frequency-voltage converter should exhibit a linear relationship between the input frequency and the output voltage. This linearity ensures that the output voltage accurately represents the changes in the input frequency, making it easier to interpret and process the signal.
-
Wide frequency range: Frequency-voltage converters should be capable of handling a wide range of input frequencies, depending on the application. Some converters are designed for low-frequency signals (e.g., below 1 kHz), while others can handle high-frequency signals (e.g., up to several MHz).
-
Adjustable sensitivity: The sensitivity of a frequency-voltage converter determines the output voltage range for a given input frequency range. Having an adjustable sensitivity allows users to fine-tune the converter to match the requirements of their specific application.
-
Low noise and high accuracy: To ensure reliable signal conversion, frequency-voltage converters should have low noise characteristics and high accuracy. This minimizes the introduction of unwanted artifacts or distortions in the output voltage signal.
Working Principle of Frequency-Voltage Converters
The core component of a frequency-voltage converter is a charge pump circuit, which typically consists of a capacitor, a current source, and a reset switch. The working principle of a frequency-voltage converter can be summarized in the following steps:
-
Charging: When the input frequency signal is high, the current source charges the capacitor, causing the voltage across the capacitor to increase linearly with time.
-
Resetting: When the input frequency signal goes low, the reset switch is activated, discharging the capacitor and resetting its voltage to zero.
-
Averaging: The voltage across the capacitor is then passed through a low-pass filter, which averages the voltage over time. The resulting output voltage is proportional to the input frequency.
The output voltage of a frequency-voltage converter can be expressed as:
V_out = K_f × f_in
Where:
– V_out is the output voltage
– K_f is the frequency-to-voltage conversion factor (sensitivity)
– f_in is the input frequency
Charge Pump Circuit Diagram
Here’s a simplified schematic diagram of a charge pump circuit used in a frequency-voltage converter:
+--------+
+----| Reset |----+
| +--------+ |
| |
+----+----+ +----+----+
| Current| | |
| Source |--------|Capacitor|
+----+----+ +----+----+
| |
+------------------+
|
|
+-+-+
| |
|R_L|
| |
+-+-+
|
GND
In this diagram:
– The current source charges the capacitor when the reset switch is open.
– The reset switch discharges the capacitor when closed.
– R_L represents the load resistance, which determines the output voltage range.
Applications of Frequency-Voltage Converters
Frequency-voltage converters find applications in various fields, including:
1. Tachometers and Speed Sensors
In motor speed control applications, frequency-voltage converters are used to convert the frequency of a tachometer or speed sensor output into a proportional voltage signal. This voltage signal can then be used as feedback for closed-loop speed control or monitoring purposes.
Example: Motor Speed Control
Motor Speed (RPM) | Tachometer Output Frequency (Hz) | F/V Converter Output Voltage (V) |
---|---|---|
500 | 250 | 1.25 |
1000 | 500 | 2.50 |
1500 | 750 | 3.75 |
2000 | 1000 | 5.00 |
In this example, the tachometer generates a frequency proportional to the motor speed. The frequency-voltage converter translates this frequency into a voltage signal, which can be used by a motor controller to maintain the desired speed.
2. Flow Meters
Frequency-voltage converters are used in flow measurement applications, where the flow rate is determined by the frequency of pulses generated by a flow meter. The converter translates the pulse frequency into a voltage signal, which can be easily processed by a data acquisition system or a controller.
Example: Flow Measurement
Flow Rate (L/min) | Flow Meter Output Frequency (Hz) | F/V Converter Output Voltage (V) |
---|---|---|
2 | 100 | 1.00 |
4 | 200 | 2.00 |
6 | 300 | 3.00 |
8 | 400 | 4.00 |
In this example, the flow meter generates a frequency proportional to the flow rate. The frequency-voltage converter translates this frequency into a voltage signal, which can be used to monitor and control the flow rate in a process.
3. Audio Signal Processing
Frequency-voltage converters are used in audio signal processing applications, such as pitch detection and audio frequency analysis. The converter translates the frequency components of an audio signal into corresponding voltage levels, enabling further processing and analysis.
Example: Audio Pitch Detection
Musical Note | Frequency (Hz) | F/V Converter Output Voltage (V) |
---|---|---|
A4 | 440 | 2.20 |
C5 | 523 | 2.62 |
E5 | 659 | 3.30 |
G5 | 784 | 3.92 |
In this example, the frequency-voltage converter translates the frequencies of musical notes into corresponding voltage levels. This information can be used in pitch detection algorithms or audio analysis applications.
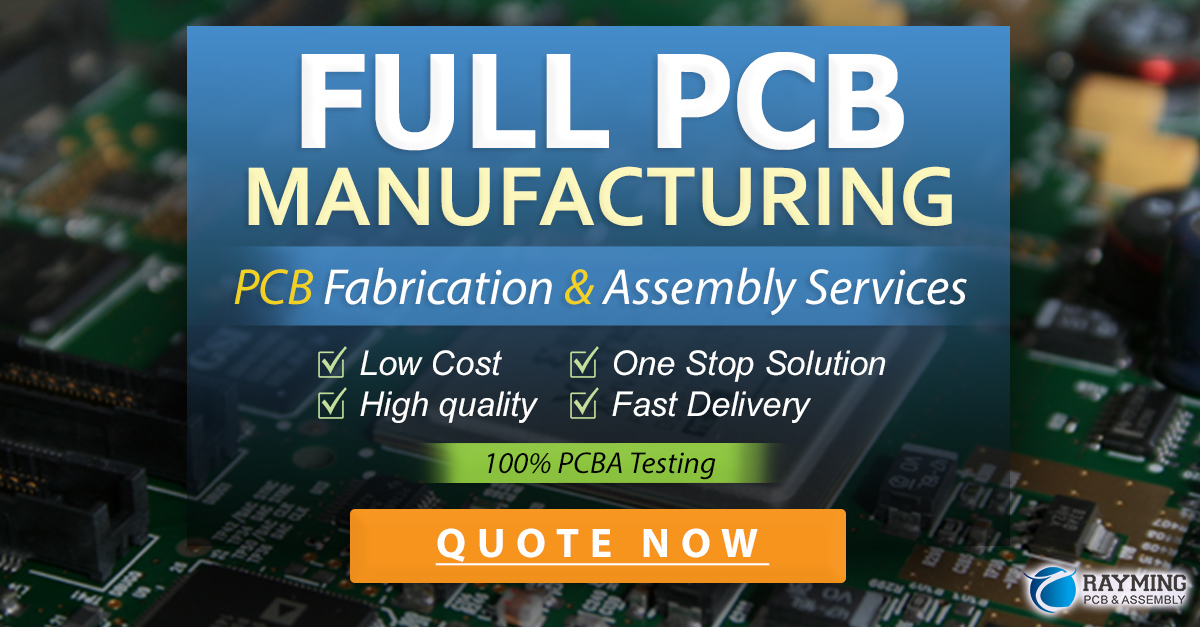
Designing a Frequency-Voltage Converter
When designing a frequency-voltage converter, several key factors must be considered:
1. Input Frequency Range
Determine the expected range of input frequencies based on the application requirements. This will help in selecting the appropriate components and designing the charge pump circuit.
2. Output Voltage Range
Define the desired output voltage range for the given input frequency range. This will determine the sensitivity of the converter and the value of the load resistance.
3. Linearity and Accuracy
Ensure that the converter exhibits good linearity and accuracy over the specified input frequency range. This can be achieved by using precision components and implementing proper calibration techniques.
4. Noise Reduction
Minimize noise in the output voltage signal by using appropriate filtering techniques, such as low-pass filters or noise-reduction circuitry.
5. Component Selection
Choose components with suitable specifications, such as the capacitor value, current source, and reset switch. Consider factors like temperature stability, tolerance, and frequency response when selecting components.
Calibration and Testing
After designing and building a frequency-voltage converter, it is essential to calibrate and test the device to ensure its proper functioning and accuracy. The calibration process involves the following steps:
-
Apply known input frequencies to the converter and measure the corresponding output voltages.
-
Compare the measured output voltages with the expected values based on the designed sensitivity and linearity.
-
Adjust the converter’s parameters, such as the current source or load resistance, to minimize any deviations from the expected output voltages.
-
Repeat the calibration process for different input frequencies across the specified range to ensure consistent performance.
Once calibrated, the frequency-voltage converter should be tested under various operating conditions, including:
- Temperature variations
- Power supply fluctuations
- Presence of external noise sources
These tests help to validate the converter’s robustness and reliability in real-world applications.
Advantages and Limitations
Frequency-voltage converters offer several advantages:
- Simple and cost-effective solution for converting frequency signals to voltage signals
- Wide input frequency range and adjustable sensitivity
- Good linearity and accuracy when properly designed and calibrated
- Compatibility with various sensors and measurement devices
However, there are also some limitations to consider:
- Limited bandwidth due to the charge pump circuit’s response time
- Sensitivity to temperature variations and component tolerances
- Potential for noise introduction in the output voltage signal
- Need for periodic calibration to maintain accuracy over time
Despite these limitations, frequency-voltage converters remain a popular choice for many applications due to their simplicity, versatility, and cost-effectiveness.
Frequently Asked Questions
1. What is the difference between a frequency-voltage converter and a voltage-frequency converter?
A frequency-voltage converter converts a frequency signal into a proportional voltage signal, while a voltage-frequency converter does the opposite, converting a voltage signal into a proportional frequency signal.
2. Can a frequency-voltage converter handle non-sinusoidal input signals?
Yes, a frequency-voltage converter can handle non-sinusoidal input signals, such as square waves or pulse trains. The converter responds to the frequency of the input signal, regardless of its shape.
3. How does the capacitor value affect the performance of a frequency-voltage converter?
The capacitor value in a frequency-voltage converter determines the charge storage capacity and the response time of the charge pump circuit. A larger capacitor value results in a slower response time but better noise immunity, while a smaller capacitor value provides a faster response time but may be more susceptible to noise.
4. Can a frequency-voltage converter be used for measuring very low frequencies?
Yes, frequency-voltage converters can be designed to measure very low frequencies, such as those in the sub-Hz range. However, this requires the use of larger capacitor values and may result in slower response times.
5. How often should a frequency-voltage converter be calibrated?
The calibration frequency of a frequency-voltage converter depends on the application requirements and the operating conditions. In general, it is recommended to calibrate the converter at least once a year or whenever there are significant changes in the operating environment, such as temperature or power supply variations.
Conclusion
Frequency-voltage converters play a crucial role in converting mechanical or temporal information into electrical signals, enabling seamless integration with various control, monitoring, and analysis systems. By understanding the working principle, design considerations, and applications of frequency-voltage converters, engineers and technicians can effectively implement these devices in their projects.
When designing and using frequency-voltage converters, it is essential to consider factors such as input frequency range, output voltage range, linearity, accuracy, and noise reduction. Proper calibration and testing ensure that the converter performs optimally and reliably in the intended application.
As technology advances, frequency-voltage converters continue to evolve, with newer designs offering improved performance, higher bandwidth, and better noise immunity. By staying up-to-date with the latest developments and best practices, engineers can harness the full potential of frequency-voltage converters in a wide range of applications, from motor speed control to audio signal processing.
Leave a Reply