Introduction to FR PCBs
Printed Circuit Boards (PCBs) are the backbone of modern electronics. They provide a platform for electrical components to be mounted and connected, enabling the creation of complex circuits that power our devices. Among the various types of PCBs, FR (Flame Retardant) PCBs are widely used due to their excellent fire-resistant properties. In this article, we will focus on FR1 PCBs and how they differ from FR2, FR3, and FR4 PCBs.
What are FR PCBs?
FR PCBs are a type of printed circuit board that is manufactured using flame-retardant materials. These materials are designed to resist ignition and slow down the spread of flames in case of a fire. FR PCBs are classified based on their flame retardancy level, with FR1 being the least flame-resistant and FR4 being the most flame-resistant.
Why are FR PCBs Important?
FR PCBs are essential in applications where fire safety is a critical concern. They are commonly used in industries such as aerospace, automotive, medical, and industrial equipment, where the risk of fire is high, and the consequences of a fire can be catastrophic. By using FR PCBs, manufacturers can reduce the risk of fire and ensure the safety of their products and users.
FR1 PCBs
What are FR1 PCBs?
FR1 PCBs are the most basic type of flame-retardant PCBs. They are made using a paper-based substrate that is impregnated with a flame-retardant resin. FR1 PCBs have the lowest flame retardancy rating among all FR PCBs, making them suitable for low-cost, low-performance applications.
Characteristics of FR1 PCBs
- Substrate material: Paper-based
- Flame retardancy rating: UL 94V-0
- Dielectric constant: 4.5 at 1 MHz
- Dissipation factor: 0.035 at 1 MHz
- Thermal conductivity: 0.3 W/mK
- Moisture absorption: 0.8%
- Temperature resistance: 105°C
Applications of FR1 PCBs
FR1 PCBs are commonly used in low-cost, low-performance applications such as:
- Consumer electronics (e.g., toys, calculators)
- Low-power LED lighting
- Simple control circuits
- Educational kits and projects
FR2 PCBs
What are FR2 PCBs?
FR2 PCBs are a step up from FR1 PCBs in terms of flame retardancy and performance. They are made using a paper-based substrate that is impregnated with a higher-grade flame-retardant resin. FR2 PCBs offer better electrical and mechanical properties than FR1 PCBs, making them suitable for a wider range of applications.
Characteristics of FR2 PCBs
- Substrate material: Paper-based
- Flame retardancy rating: UL 94V-0
- Dielectric constant: 4.2 at 1 MHz
- Dissipation factor: 0.02 at 1 MHz
- Thermal conductivity: 0.4 W/mK
- Moisture absorption: 0.6%
- Temperature resistance: 130°C
Applications of FR2 PCBs
FR2 PCBs are commonly used in applications that require better performance than FR1 PCBs, such as:
- Automotive electronics (e.g., dashboard controls, lighting systems)
- Industrial control systems
- Power supplies and converters
- Household appliances (e.g., washing machines, refrigerators)
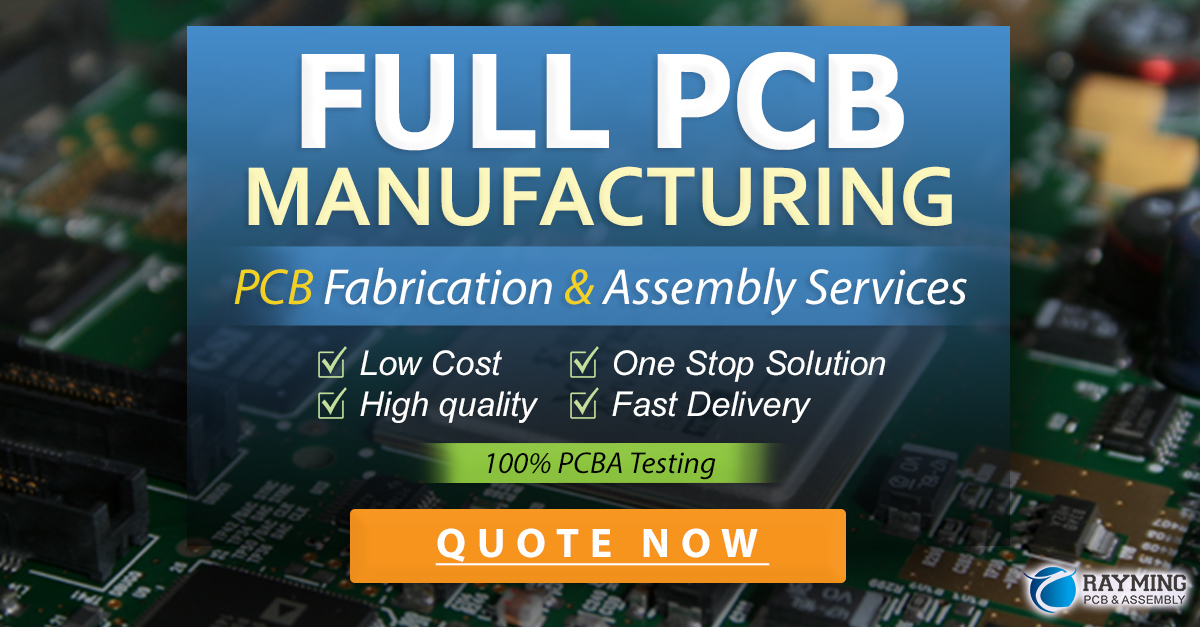
FR3 PCBs
What are FR3 PCBs?
FR3 PCBs are a higher-grade version of FR2 PCBs, offering even better flame retardancy and performance. They are made using a glass-reinforced epoxy substrate that provides excellent mechanical strength and dimensional stability. FR3 PCBs are suitable for applications that require high reliability and durability.
Characteristics of FR3 PCBs
- Substrate material: Glass-reinforced epoxy
- Flame retardancy rating: UL 94V-0
- Dielectric constant: 4.0 at 1 MHz
- Dissipation factor: 0.015 at 1 MHz
- Thermal conductivity: 0.6 W/mK
- Moisture absorption: 0.3%
- Temperature resistance: 150°C
Applications of FR3 PCBs
FR3 PCBs are commonly used in applications that require high reliability and durability, such as:
- Aerospace and defense electronics
- Medical equipment (e.g., patient monitors, diagnostic devices)
- Industrial automation and control systems
- Telecommunications infrastructure (e.g., base stations, routers)
FR4 PCBs
What are FR4 PCBs?
FR4 PCBs are the most advanced and widely used type of flame-retardant PCBs. They are made using a glass-reinforced epoxy substrate that offers the highest level of flame retardancy, mechanical strength, and electrical performance among all FR PCBs. FR4 PCBs are suitable for a wide range of applications, from consumer electronics to high-end industrial and aerospace systems.
Characteristics of FR4 PCBs
- Substrate material: Glass-reinforced epoxy
- Flame retardancy rating: UL 94V-0
- Dielectric constant: 4.3 at 1 MHz
- Dissipation factor: 0.02 at 1 MHz
- Thermal conductivity: 0.8 W/mK
- Moisture absorption: 0.15%
- Temperature resistance: 170°C
Applications of FR4 PCBs
FR4 PCBs are used in a vast array of applications, including:
- Consumer electronics (e.g., smartphones, laptops, gaming consoles)
- Automotive electronics (e.g., engine control units, infotainment systems)
- Medical devices (e.g., imaging equipment, surgical instruments)
- Industrial automation and robotics
- Aerospace and defense systems (e.g., avionics, radar, communication equipment)
Comparison of FR PCBs
To better understand the differences between FR1, FR2, FR3, and FR4 PCBs, let’s compare their key characteristics in a table:
Characteristic | FR1 | FR2 | FR3 | FR4 |
---|---|---|---|---|
Substrate Material | Paper | Paper | Glass-Epoxy | Glass-Epoxy |
Flame Retardancy Rating | UL 94V-0 | UL 94V-0 | UL 94V-0 | UL 94V-0 |
Dielectric Constant | 4.5 | 4.2 | 4.0 | 4.3 |
Dissipation Factor | 0.035 | 0.02 | 0.015 | 0.02 |
Thermal Conductivity | 0.3 W/mK | 0.4 W/mK | 0.6 W/mK | 0.8 W/mK |
Moisture Absorption | 0.8% | 0.6% | 0.3% | 0.15% |
Temperature Resistance | 105°C | 130°C | 150°C | 170°C |
As evident from the table, FR4 PCBs offer the best overall performance, followed by FR3, FR2, and FR1 PCBs. The choice of FR PCB depends on the specific requirements of the application, such as the operating environment, electrical performance, mechanical strength, and cost constraints.
Frequently Asked Questions (FAQ)
1. Can FR1 PCBs be used in high-temperature applications?
No, FR1 PCBs are not suitable for high-temperature applications due to their low temperature resistance (105°C). For applications that require higher temperature resistance, FR2, FR3, or FR4 PCBs should be used.
2. Are FR4 PCBs more expensive than FR1 PCBs?
Yes, FR4 PCBs are generally more expensive than FR1 PCBs due to their superior materials, performance, and manufacturing process. However, the higher cost is justified for applications that require high reliability, durability, and performance.
3. Can FR2 PCBs be used in aerospace applications?
While FR2 PCBs offer better performance than FR1 PCBs, they may not be suitable for most aerospace applications due to their limited temperature resistance and mechanical strength. FR3 or FR4 PCBs are typically recommended for aerospace applications.
4. What is the main difference between FR3 and FR4 PCBs?
The main difference between FR3 and FR4 PCBs lies in their performance characteristics. FR4 PCBs offer higher temperature resistance, lower moisture absorption, and better thermal conductivity compared to FR3 PCBs. As a result, FR4 PCBs are more widely used in demanding applications.
5. Are all FR PCBs certified with the UL 94V-0 flame retardancy rating?
Yes, all FR PCBs (FR1, FR2, FR3, and FR4) are certified with the UL 94V-0 flame retardancy rating, which is the highest rating for PCBs. This ensures that the PCBs have excellent flame-retardant properties and can help prevent the spread of fires in electronic devices.
Conclusion
In conclusion, FR PCBs are essential components in modern electronics, providing a reliable and safe platform for mounting and connecting electrical components. FR1, FR2, FR3, and FR4 PCBs offer different levels of performance, reliability, and cost, making them suitable for a wide range of applications.
Understanding the differences between these FR PCBs is crucial for selecting the right type for a specific application. FR1 PCBs are suitable for low-cost, low-performance applications, while FR2 and FR3 PCBs offer better performance and reliability for more demanding applications. FR4 PCBs are the most advanced and widely used type, offering the best overall performance and suitability for a vast array of applications, from consumer electronics to aerospace systems.
By choosing the appropriate FR PCB for a given application, manufacturers can ensure the safety, reliability, and performance of their products while meeting the required cost and regulatory standards.
Leave a Reply