Introduction to Flexible PCBs (FlexPCBs)
Flexible printed circuit boards, also known as FlexPCBs or flex circuits, have revolutionized the electronics industry by providing a versatile and reliable solution for applications that require flexibility, durability, and compact design. Unlike traditional rigid PCBs, FlexPCBs are made from flexible substrate materials that allow them to bend, fold, and conform to various shapes and sizes. This unique characteristic has made FlexPCBs indispensable in a wide range of industries, including consumer electronics, medical devices, aerospace, automotive, and wearable technology.
What are FlexPCBs?
FlexPCBs are printed circuit boards that use flexible substrate materials, such as polyimide or polyester, to create a bendable and lightweight circuit board. These flexible substrates are laminated with conductive copper layers, which are etched to create the desired circuit pattern. The resulting FlexPCB can be bent, twisted, or folded to fit into tight spaces or conform to irregular surfaces, making them ideal for applications where traditional rigid PCBs are not suitable.
Advantages of FlexPCBs
-
Flexibility and Durability: The primary advantage of FlexPCBs is their ability to bend and flex without damaging the circuit or components. This makes them highly durable and resistant to vibration, shock, and thermal stress.
-
Space Savings: FlexPCBs can be designed to fit into tight spaces and conform to irregular shapes, enabling more compact and lightweight electronic devices.
-
Improved Signal Integrity: The reduced size and weight of FlexPCBs, combined with their ability to be placed closer to components, results in improved signal integrity and reduced electromagnetic interference (EMI).
-
Reduced Assembly Costs: FlexPCBs can replace multiple rigid PCBs and connectors, simplifying the assembly process and reducing overall manufacturing costs.
-
Enhanced Reliability: The flexible nature of FlexPCBs reduces the stress on components and solder joints, improving the overall reliability of the electronic device.
FlexPCB Manufacturing Process
The manufacturing process for FlexPCBs is similar to that of rigid PCBs, but with additional steps and considerations to accommodate the flexible substrate materials. Here’s an overview of the FlexPCB manufacturing process:
1. Design and Artwork Creation
The first step in the FlexPCB manufacturing process is to create the circuit design and artwork using electronic design automation (EDA) software. The design must take into account the specific requirements of the flexible substrate, such as bend radius, layer stackup, and material properties.
2. Substrate Preparation
The flexible substrate material, typically polyimide or polyester, is cleaned and prepared for the lamination process. The substrate thickness can range from 25 to 250 microns, depending on the application requirements.
3. Copper Lamination
A thin layer of copper is laminated onto the flexible substrate using heat and pressure. The copper thickness can vary from 9 to 70 microns, depending on the desired electrical properties and circuit density.
4. Photoresist Application
A photosensitive resist material is applied to the copper-laminated substrate. The photoresist will later be exposed to UV light through a photomask to create the desired circuit pattern.
5. Exposure and Development
The photoresist-coated substrate is exposed to UV light through a photomask that contains the circuit pattern. The exposed areas of the photoresist become soluble and are removed during the development process, leaving the desired circuit pattern on the copper layer.
6. Etching
The exposed copper areas are etched away using a chemical solution, typically cupric chloride or ammonium persulfate. This process removes the unwanted copper, leaving only the desired circuit pattern on the flexible substrate.
7. Photoresist Removal
The remaining photoresist is stripped away using a chemical solution, revealing the final copper circuit pattern on the flexible substrate.
8. Coverlay Application
A protective coverlay is applied to the FlexPCB to insulate and protect the exposed copper traces. The coverlay is typically made from the same material as the flexible substrate and is laminated using heat and pressure.
9. Drilling and Cutting
Holes are drilled through the FlexPCB for component mounting and interconnections. The FlexPCB is then cut to its final shape using a laser or die-cutting process.
10. Surface Finishing
To enhance solderability and protect the copper traces from oxidation, a surface finish is applied to the FlexPCB. Common surface finishes include:
- ENIG (Electroless Nickel Immersion Gold)
- OSP (Organic Solderability Preservative)
- Immersion Silver
- Immersion Tin
11. Solder Mask Application (Optional)
For some FlexPCBs, a solder mask is applied to protect the copper traces and prevent solder bridging during the assembly process. The solder mask is a thin, heat-resistant polymer layer that is applied using screen printing or photoimaging techniques.
12. Electrical Testing
The finished FlexPCB undergoes electrical testing to ensure that all circuits are functioning correctly and meet the specified performance requirements. This may include continuity testing, insulation resistance testing, and high-voltage testing.
13. Final Inspection and Packaging
The FlexPCB is visually inspected for any defects or anomalies, and then packaged for shipment to the customer. Packaging may include static shielding bags, moisture barrier bags, or custom packaging depending on the customer’s requirements.
FlexPCB Materials
Flexible PCBs are manufactured using a variety of materials that provide the necessary flexibility, durability, and electrical properties. The most common materials used in FlexPCB manufacturing are:
Substrate Materials
-
Polyimide (PI): Polyimide is the most widely used substrate material for FlexPCBs due to its excellent thermal stability, chemical resistance, and mechanical properties. It can withstand temperatures up to 300°C and has a low dielectric constant, making it suitable for high-frequency applications.
-
Polyester (PET): Polyester is a lower-cost alternative to polyimide for less demanding applications. It has good flexibility and electrical properties but lower thermal stability compared to polyimide.
Adhesive Materials
-
Acrylic: Acrylic adhesives are commonly used to bond the copper layers to the flexible substrate. They offer good adhesion strength, flexibility, and electrical properties.
-
Epoxy: Epoxy adhesives provide higher bond strength and better thermal stability compared to acrylic adhesives. They are often used in high-reliability applications or when the FlexPCB needs to withstand higher temperatures.
Coverlay Materials
-
Polyimide: Polyimide coverlays offer the same advantages as polyimide substrates, providing excellent thermal stability, chemical resistance, and mechanical properties.
-
Polyester: Polyester coverlays are a lower-cost option for less demanding applications, offering good flexibility and electrical properties.
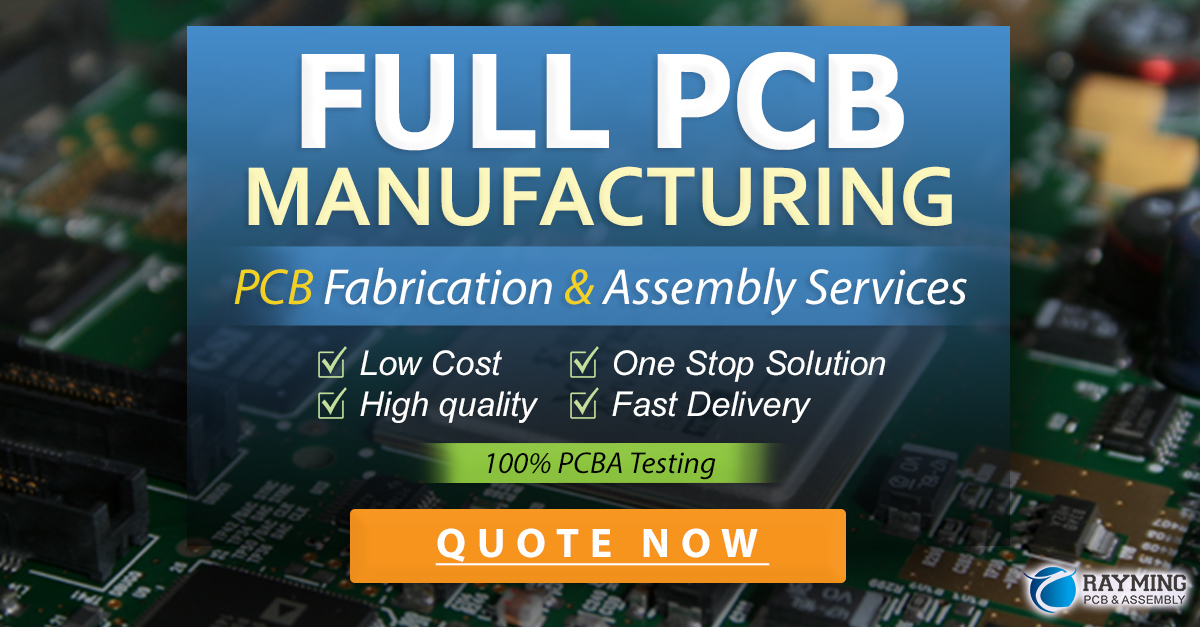
FlexPCB Design Considerations
When designing a FlexPCB, several factors must be considered to ensure optimal performance, reliability, and manufacturability. These include:
Bend Radius
The bend radius is the minimum radius that a FlexPCB can be bent without causing damage to the copper traces or substrate. The bend radius is determined by the thickness of the substrate, copper layers, and any stiffeners used. A general rule of thumb is to keep the bend radius at least 10 times the total thickness of the FlexPCB.
Layer Stackup
The layer stackup of a FlexPCB refers to the arrangement of conductive layers, insulating layers, and adhesives. The number of layers and their arrangement can affect the flexibility, electrical properties, and manufacturing complexity of the FlexPCB. Common layer stackups include single-sided, double-sided, and multi-layer configurations.
Conductor Width and Spacing
The width and spacing of the copper traces on a FlexPCB must be carefully designed to ensure adequate electrical performance and manufacturability. Narrower traces and smaller spaces can increase circuit density but may also increase the manufacturing complexity and cost. The minimum trace width and spacing are determined by the capabilities of the manufacturing process and the electrical requirements of the application.
Stiffeners and Reinforcements
Stiffeners and reinforcements can be added to specific areas of a FlexPCB to improve mechanical stability and prevent damage during handling or use. These can be made from materials such as polyimide, FR-4, or metal and are typically bonded to the FlexPCB using adhesives.
Applications of FlexPCBs
FlexPCBs are used in a wide range of industries and applications where flexibility, durability, and compact design are essential. Some of the most common applications include:
Consumer Electronics
FlexPCBs are widely used in consumer electronic devices such as smartphones, tablets, laptops, and wearables. They enable compact and lightweight designs while providing reliable interconnections between components.
Medical Devices
The flexibility and durability of FlexPCBs make them ideal for use in medical devices such as hearing aids, pacemakers, and implantable sensors. They can conform to the shape of the human body and withstand the harsh environments inside the body.
Automotive Electronics
FlexPCBs are increasingly used in automotive electronics, particularly in applications such as instrument clusters, infotainment systems, and sensors. They offer improved reliability and space savings compared to traditional wiring harnesses.
Aerospace and Defense
In aerospace and defense applications, FlexPCBs are used in avionics systems, satellites, and military equipment. Their ability to withstand extreme temperatures, vibrations, and shocks makes them essential for these demanding environments.
Industrial Equipment
FlexPCBs are used in various industrial equipment, such as robotics, automation systems, and power electronics. They provide reliable interconnections and can withstand the harsh conditions often found in industrial settings.
FlexPCB vs. Rigid PCB
While FlexPCBs offer many advantages over traditional rigid PCBs, they may not be the best choice for every application. Here’s a comparison of FlexPCBs and rigid PCBs:
Characteristic | FlexPCB | Rigid PCB |
---|---|---|
Flexibility | High | Low |
Durability | High | Moderate |
Space Savings | High | Low |
Weight | Low | Moderate |
Cost | Higher | Lower |
Design Complexity | Higher | Lower |
Manufacturing Complexity | Higher | Lower |
Thermal Stability | High | Moderate |
Signal Integrity | High | Moderate |
The choice between a FlexPCB and a rigid PCB depends on the specific requirements of the application, such as size constraints, environmental conditions, and performance needs.
Future of FlexPCB Technology
As electronic devices continue to become smaller, more powerful, and more interconnected, the demand for FlexPCBs is expected to grow. Advances in materials science, manufacturing processes, and design tools will drive the development of new and innovative FlexPCB solutions. Some of the emerging trends in FlexPCB technology include:
Stretchable Electronics
Researchers are developing stretchable FlexPCBs that can elongate and conform to complex, dynamic surfaces. These stretchable electronics have potential applications in wearable devices, soft robotics, and biomedical implants.
Transparent FlexPCBs
Transparent conductive materials, such as indium tin oxide (ITO) or graphene, are being explored for use in FlexPCBs. Transparent FlexPCBs could enable new applications in displays, solar cells, and optical sensors.
3D Printed FlexPCBs
Additive manufacturing techniques, such as 3D printing, are being adapted for the production of FlexPCBs. 3D printing could enable the rapid prototyping and customization of FlexPCBs, as well as the creation of complex, three-dimensional circuit structures.
High-Frequency FlexPCBs
As wireless communication technologies continue to advance, there is a growing need for FlexPCBs that can operate at high frequencies, such as 5G and beyond. New substrate materials and manufacturing processes are being developed to enable the production of high-frequency FlexPCBs with improved signal integrity and reduced losses.
FAQs
-
Q: What is the typical turnaround time for FlexPCB manufacturing?
A: The turnaround time for FlexPCB manufacturing varies depending on the complexity of the design, the materials used, and the manufacturing process. Typical turnaround times range from 2-3 weeks for standard designs to 4-6 weeks for more complex, custom designs. -
Q: Can FlexPCBs be repaired if damaged?
A: While FlexPCBs are highly durable, they can be repaired if damaged, depending on the extent and location of the damage. Minor damage to copper traces or solder joints can often be repaired using soldering techniques. More extensive damage may require specialized repair services or replacement of the FlexPCB. -
Q: How do I choose the right substrate material for my FlexPCB application?
A: The choice of substrate material depends on the specific requirements of your application, such as temperature range, chemical resistance, and mechanical properties. Polyimide is the most common substrate material for FlexPCBs due to its excellent thermal stability, chemical resistance, and mechanical strength. Polyester is a lower-cost alternative for less demanding applications. -
Q: Are FlexPCBs more expensive than rigid PCBs?
A: Yes, FlexPCBs are typically more expensive than rigid PCBs due to the specialized materials, manufacturing processes, and design considerations involved. However, the cost of FlexPCBs has been decreasing in recent years as manufacturing technologies have improved and demand has increased. -
Q: Can FlexPCBs be combined with rigid PCBs in a single assembly?
A: Yes, FlexPCBs can be combined with rigid PCBs in a single assembly, known as a rigid-flex PCB. Rigid-flex PCBs offer the benefits of both FlexPCBs and rigid PCBs, providing flexibility where needed and mechanical stability in other areas. Rigid-flex PCBs are commonly used in applications where space is limited, and the PCB needs to conform to a specific shape or fit into a tight enclosure.
Conclusion
Flexible PCBs have become an essential technology in the electronics industry, enabling the development of smaller, lighter, and more durable electronic devices. The FlexPCB manufacturing process, while similar to that of rigid PCBs, involves specialized materials, design considerations, and manufacturing techniques to achieve the desired flexibility and performance.
As the demand for flexible and wearable electronics continues to grow, FlexPCB technology is poised for further innovation and advancement. By understanding the FlexPCB manufacturing process, materials, and design considerations, engineers and designers can create innovative and reliable electronic products that meet the evolving needs of consumers and industries alike.
Leave a Reply