Introduction
Flexible printed circuit boards (PCBs) have become increasingly popular in recent years, especially for use in LED lighting applications. Flex circuits, as they are often called, provide a number of benefits over traditional rigid PCBs. In this article, we will examine what makes flexible LED circuit boards so advantageous and some of the top applications where they excel.
What Are Flexible LED Circuit Boards?
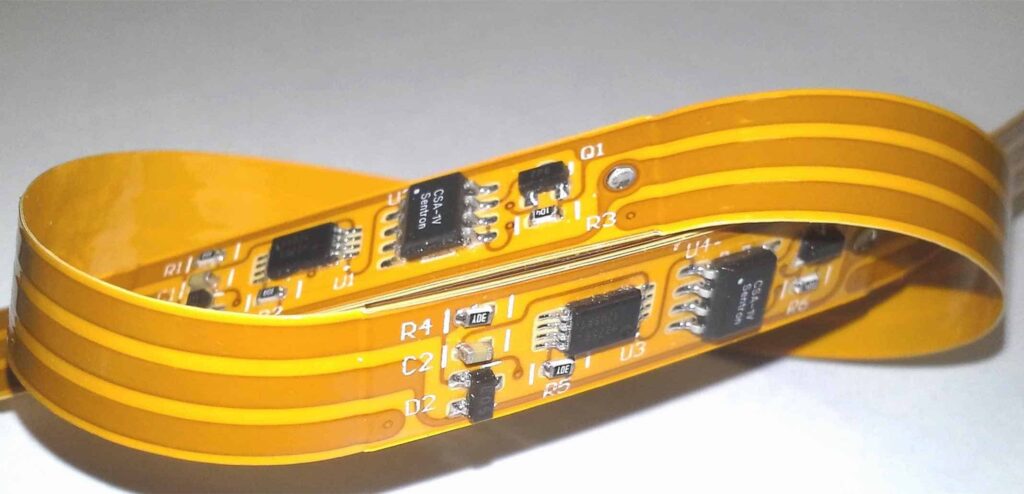
A flexible LED circuit board is a type of printed circuit board that is made of a flexible base material, such as polyimide or polyester film, with conductive traces etched or printed on top. The flexibility allows the PCB to bend and flex without damage to the traces. Components are then soldered onto the PCB as with a normal rigid board.
Flexible PCBs were initially designed for use in aerospace and military applications where size, weight, and reliability were critical factors. Today, flex circuits are found in all types of electronic devices from mobile phones to medical equipment. For LED lighting, the flexible form factor is ideal to conform to the tight spaces and curved surfaces found in modern lamp and fixture designs.
Benefits of Flexible LED Circuit Boards
Here are some of the top advantages of using a flexible PCB for LED lighting:
- Lightweight – Flexible circuits are extremely lightweight, often 80% lighter than rigid boards. This helps reduce overall weight in LED products.
- Thin profile – At a fraction of the thickness of rigid boards, flexible circuits can fit into very tight spaces and maintain a slim product profile.
- Shape conforming – The flexible nature allows circuits to bend, twist, and contour to almost any shape imaginable. Great for fitting into curved or irregularly shaped LED fixtures.
- Vibration/shock resistant – The flexible material dampens vibrations and withstands shocks better than rigid boards. Flex circuits are ideal for LEDs used in transport applications.
- Reliability – Flexible circuits can handle repeated bending without damage to traces. Some flex boards operate reliably at over 1 million flex cycles.
- Design freedom – With the ability to bend and twist, flexible circuits open new doors for innovative industrial design not possible with rigid PCBs.
- Efficient manufacturing – Flexible boards allow for reel-to-reel automated assembly, saving on manufacturing and assembly costs.
With these advantages in mind, flexible PCB technology is a natural fit for today’s LED lighting applications. Next, we will look at some of the top uses.
Common Applications of Flexible LED Circuit Boards
Flexible LED circuit boards are found in a diverse range of lighting products from large LED video displays to tiny wearable medical devices. Here are some of the most common applications for flex boards in LED lighting:
LED Tape Lighting
One of the most widespread uses is in LED tape lighting. These thin, flexible strips of LEDs can be adhered nearly anywhere to provide accent lighting. The flexibility allows the tape to bend around corners and mold to the contour of walls and architectural details. The thin profile keeps the lighting discreet and unobtrusive. Flex circuits are commonly used in LED tape lighting under cabinets, coves, alcoves, and staircases.
![LED tape lighting with a flexible circuit]
LED Neon Signs and Displays
For neon-like LED signs and displays, flexible circuits are indispensable. The ability to bend, curve, and shape the lighting into custom letters, logos, and graphics would not be possible with rigid PCBs. Flexible boards with molded interconnect technology can create a nearly seamless illusion of neon lighting. Flexible LED neon is used for retail signage, wayfinding, architectural accents, and more.
![Flexible LED neon sign spelling out Open]
Automotive Lighting
In automobile interiors, flex circuits enable slim, contoured LED lighting for subtle ambient lighting effects. Flexible strips can also integrate with onboard controls to create colorful animated lighting sequences. Exterior uses include flexible LED modules for adaptive headlights that bend to illuminate around corners. Flex circuits stand up to underhood environments and the vibrations of a moving vehicle.
Medical and Wearable Devices
For portable medical devices and wearable tech, the tiny footprint and lightweight nature of flexible circuits are indispensable. Flexible LED lighting integrated into medical devices can provide illumination for examinations or treatments. In wearables, flexible LEDs create stylish, animated clothing, jewelry, handbags, shoes, and more. The possibilities are endless.
Other Uses
Beyond these applications, flexible LED boards are implemented in a wide variety of products including appliances, consumer electronics, drones, IoT devices, toys, and virtual reality gear. Anywhere size, weight, and reliability are important factors, flexible PCBs should be considered. With ongoing LED miniaturization and efficiency improvements, flex circuits will continue growing in popularity and new applications will emerge.
Design Considerations for Flexible LED Circuits
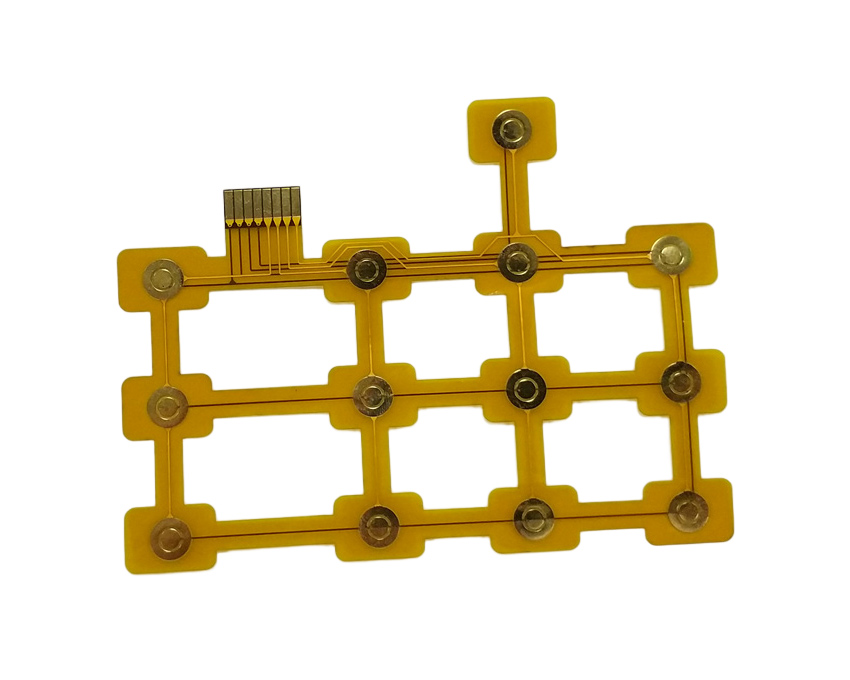
When designing a flex PCB for your LED lighting application, there are some important factors to consider:
- Bend radius – Avoid tight folds and bends that may damage traces. Plan layouts to accommodate the minimum bend radius.
- Stresses – Consider stresses such as tension, compression, and shearing from bending and flexing. Plan anchor points to relieve stress on solder joints.
- Thin traces – Use thin, etched traces rather than thick copper to improve flexibility and durability.
- Adhesives – Use appropriate adhesives to bond flex circuit layers and prevent delamination during movement.
- ESD protection – Flexible circuits require ESD protection measures for LEDs and control components.
- Thermal dissipation – Ensure adequate thermal dissipation is designed into the LED mounting pads and ground planes.
- Encapsulation – Protective coatings and potting compounds can be used to prevent wear and insulate circuits.
With careful design considering these factors, flexible LED boards can operate extremely reliably despite ongoing bending and flexing in application.
Proper design is also crucial for manufacturability and costs. Consulting early with your flexible PCB manufacturer is recommended to optimize the layout for their specific processes and requirements. This will avoid errors or revisions and result in the most cost-effective solution.
Conclusion
With their many advantages, flexible circuit boards are becoming the standard in LED lighting. Their lightweight, thin, and highly reliable nature makes flex PCB technology a perfect match for the tight confines and demanding environments found in modern LED applications. As LED lighting continues advancing into new shapes and products, flex circuits will play an integral role in enabling innovative and high performing designs. With a thoughtful approach to the layout and material selection, flexible LED boards can deliver lasting performance and value.
Frequently Asked Questions About Flexible LED Circuit Boards
What types of materials are used in flexible LED circuit boards?
The most common materials are polyimide (Kapton) and polyester (PET) films. These provide the needed heat resistance, flexibility, and durability. Other materials like PEN and PEEK films are used for more demanding applications.
Can components be mounted on both sides of a flexible circuit board?
Yes, components can be mounted on one or both sides of a flex board. Double-sided mounting is common but requires through-hole vias or other interconnects between layers.
How long do flexible LED circuit boards typically last?
Properly designed flex circuits can have extremely long lifespans of over 1 million flex cycles. With robust design and protective coatings, some applications see 10-15 years of reliable operation.
Can flexible circuit boards be bent into three-dimensional shapes?
Absolutely. Flexible circuits are ideal for complex 3D shapes like folds, coils, cylinders, spheres, etc. This enables unique LED lighting designs.
Are flexible LED circuit boards expensive compared to rigid PCBs?
For short runs and prototyping, flexible PCB costs may be higher. But for mass production, automated assembly of flex boards can achieve very low cost similar to rigid PCBs.
Leave a Reply