Types of Fiberglass Fabrics
Fiberglass fabrics are categorized based on their weave patterns, which influence the mechanical properties and appearance of the laminate. The most common fiberglass fabric styles include:
- Plain weave
- Twill weave
- Satin weave
- Unidirectional (UD) fabric
- Chopped strand mat (CSM)
- Woven roving
Plain Weave
Plain weave is the simplest and most common fabric style, characterized by alternating warp and weft fibers that create a checkerboard-like pattern. The warp and weft fibers are interlaced at right angles, resulting in a balanced and symmetrical fabric. Plain weave fabrics offer good stability, drapeability, and moderate mechanical properties. They are often used in general-purpose applications, such as marine hulls, automotive parts, and consumer products.
Advantages of Plain Weave Fabrics
- Balanced and symmetrical properties
- Good stability and drapeability
- Economical and widely available
- Suitable for a wide range of applications
Disadvantages of Plain Weave Fabrics
- Lower mechanical properties compared to other weave styles
- Prone to print-through and surface imperfections
Twill Weave
Twill weave fabrics feature a diagonal ribbing pattern, created by interlacing warp and weft fibers in a “over two, under two” pattern. This weave style offers better drapeability and a more aesthetically pleasing appearance compared to plain weave. Twill weave fabrics exhibit higher mechanical properties, particularly in the bias direction, making them suitable for applications that require improved impact resistance and fatigue performance.
Advantages of Twill Weave Fabrics
- Improved drapeability and conformability
- Higher mechanical properties, especially in the bias direction
- Enhanced impact resistance and fatigue performance
- Attractive appearance with diagonal ribbing pattern
Disadvantages of Twill Weave Fabrics
- Slightly higher cost compared to plain weave fabrics
- Reduced stability compared to plain weave
Satin Weave
Satin weave fabrics are characterized by long float fibers that run over several warp or weft fibers before interlacing. This weave style creates a smooth, lustrous surface with minimal crimp, allowing for better resin flow and improved aesthetics. Satin weave fabrics offer excellent drapeability and high mechanical properties in the direction of the long float fibers. They are commonly used in applications that require a high-quality surface finish, such as aerospace components, high-performance sporting goods, and decorative panels.
Advantages of Satin Weave Fabrics
- Smooth, lustrous surface finish
- Excellent drapeability and conformability
- High mechanical properties in the direction of long float fibers
- Improved resin flow and wet-out
Disadvantages of Satin Weave Fabrics
- Reduced stability and increased risk of fabric distortion
- Higher cost compared to plain and twill weave fabrics
- Prone to snagging and damage during handling
Unidirectional (UD) Fabric
Unidirectional (UD) fabrics consist of parallel fibers oriented in a single direction, with minimal or no transverse fibers. UD fabrics offer the highest mechanical properties in the fiber direction, making them ideal for applications that require exceptional strength and stiffness. However, they have poor properties in the transverse direction and are more challenging to handle and lay up compared to woven fabrics. UD fabrics are commonly used in high-performance applications, such as aerospace structures, wind turbine blades, and pressure vessels.
Advantages of Unidirectional Fabrics
- Highest mechanical properties in the fiber direction
- Excellent strength-to-weight ratio
- Ability to tailor properties by orienting fibers in desired directions
- Reduced crimp and improved resin flow
Disadvantages of Unidirectional Fabrics
- Poor properties in the transverse direction
- Difficult to handle and lay up
- Increased risk of fiber misalignment and waviness
- Higher cost compared to woven fabrics
Chopped Strand Mat (CSM)
Chopped strand mat (CSM) is a non-woven fabric consisting of randomly oriented short glass fibers held together by a binder. CSM offers isotropic properties, meaning that the mechanical properties are similar in all directions. This fabric style is commonly used in combination with woven fabrics to provide bulk and improve the resin-to-glass ratio in the laminate. CSM is often used in general-purpose applications, such as boat hulls, tanks, and panels, where moderate mechanical properties and low cost are desired.
Advantages of Chopped Strand Mat
- Isotropic properties
- Low cost and easy to use
- Improved resin-to-glass ratio
- Good compatibility with woven fabrics
Disadvantages of Chopped Strand Mat
- Lower mechanical properties compared to woven fabrics
- Increased resin consumption
- Potential for voids and air entrapment during lamination
Woven Roving
Woven roving is a heavy-weight fabric made from continuous rovings woven in a plain weave pattern. The rovings are thicker than those used in standard woven fabrics, resulting in a coarser and more open weave structure. Woven roving fabrics offer high strength and stiffness, making them suitable for applications that require high structural performance, such as boat hulls, wind turbine blades, and infrastructure components.
Advantages of Woven Roving
- High strength and stiffness
- Excellent impact resistance
- Reduced layup time due to thicker fabric
- Good compatibility with chopped strand mat
Disadvantages of Woven Roving
- Coarse surface finish and increased print-through
- Higher resin consumption compared to finer woven fabrics
- Reduced drapeability and conformability
Factors Influencing Fabric Selection
When selecting a fiberglass fabric for a laminate, several factors must be considered to ensure optimal performance and cost-effectiveness. These factors include:
- Mechanical properties
- Drapability and conformability
- Surface finish and aesthetics
- Resin compatibility
- Cost and availability
Mechanical Properties
The desired mechanical properties of the laminate, such as strength, stiffness, and impact resistance, play a crucial role in fabric selection. Unidirectional fabrics offer the highest properties in the fiber direction, while woven fabrics provide a balance of properties in both the warp and weft directions. The weave style and fabric weight also influence the mechanical properties, with heavier fabrics generally offering higher strength and stiffness.
Drapability and Conformability
The ability of the fabric to conform to complex shapes and curves is essential for many applications. Satin weave fabrics offer the best drapability, followed by twill and plain weave fabrics. Unidirectional fabrics have limited drapability and are more suitable for flat or gently curved surfaces.
Surface Finish and Aesthetics
The surface finish and aesthetic requirements of the laminate can influence fabric selection. Plain weave fabrics tend to have a more pronounced print-through effect, while satin weave fabrics provide a smoother and more lustrous surface. Twill weave fabrics offer an attractive diagonal ribbing pattern that can enhance the visual appeal of the laminate.
Resin Compatibility
The compatibility of the fabric with the chosen resin system is crucial for achieving optimal laminate properties. Some fabric styles, such as satin weave and unidirectional fabrics, allow for better resin flow and wet-out, while others, like plain weave and chopped strand mat, may require higher resin consumption to achieve proper impregnation.
Cost and Availability
The cost and availability of the fabric should be considered when making a selection. Plain weave fabrics are generally the most economical and widely available, while specialized fabrics, such as high-performance unidirectional fabrics, may be more expensive and have longer lead times.
Fiberglass Fabric Properties
The properties of fiberglass fabrics are influenced by several factors, including the glass fiber type, fabric weight, weave style, and surface treatment. The most common glass fiber types used in laminates are:
- E-glass
- S-glass
- R-glass
E-glass
E-glass is the most widely used glass fiber type, offering a good balance of mechanical properties, electrical insulation, and cost-effectiveness. E-glass fabrics are suitable for a wide range of applications, including marine, automotive, and consumer products.
S-glass
S-glass fibers have higher strength and stiffness compared to E-glass, making them suitable for high-performance applications that require superior mechanical properties. However, S-glass fabrics are more expensive and have lower electrical insulation properties compared to E-glass.
R-glass
R-glass fibers offer improved mechanical properties and higher fatigue resistance compared to E-glass, while maintaining good electrical insulation properties. R-glass fabrics are commonly used in applications that require enhanced durability and long-term performance, such as wind turbine blades and pressure vessels.
The fabric weight, expressed in grams per square meter (gsm) or ounces per square yard (oz/yd²), determines the thickness and reinforcement content of the laminate. Heavier fabrics generally offer higher mechanical properties but may result in a thicker and heavier laminate.
Surface treatments, such as silane coupling agents, are often applied to glass fibers to improve their adhesion to the resin matrix and enhance the overall performance of the laminate.
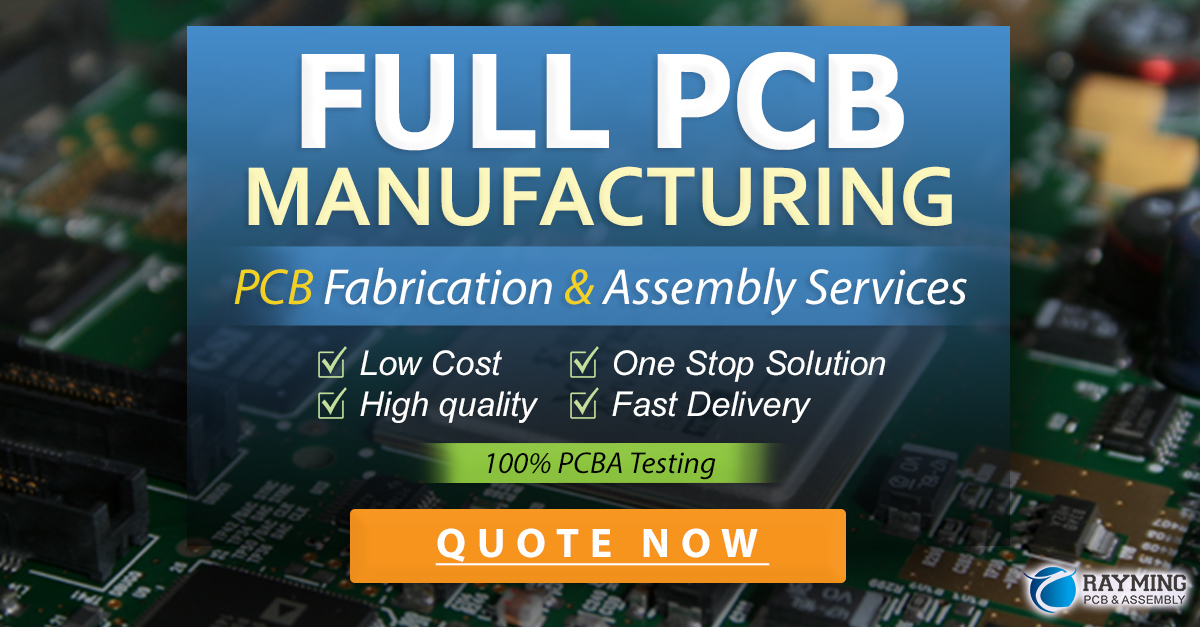
Layup Considerations
When incorporating fiberglass fabrics into a laminate, several layup considerations must be taken into account to achieve the desired properties and performance. These considerations include:
- Fiber orientation
- Stacking sequence
- Ply drop-offs
- Fabric handling and storage
Fiber Orientation
The orientation of the fibers in each layer of the laminate plays a critical role in determining the mechanical properties and performance of the structure. Fibers should be oriented in the direction of the primary loads to maximize strength and stiffness. In some cases, off-axis orientations may be used to improve shear strength or torsional stiffness.
Stacking Sequence
The stacking sequence, or the order in which the fabric layers are arranged, can significantly influence the laminate properties. Symmetrical and balanced stacking sequences are often used to minimize warpage and ensure uniform properties. Alternating fabric styles, such as combining unidirectional and woven fabrics, can be employed to achieve specific performance requirements.
Ply Drop-offs
Ply drop-offs are used to taper the thickness of the laminate in areas where reduced reinforcement is required. Proper design and execution of ply drop-offs are essential to avoid stress concentrations and maintain the structural integrity of the laminate.
Fabric Handling and Storage
Proper handling and storage of fiberglass fabrics are crucial to maintain their quality and ensure consistent laminate properties. Fabrics should be stored in a clean, dry environment, away from direct sunlight and sources of contamination. When handling fabrics, care should be taken to avoid damage, such as fraying or snagging, which can compromise the reinforcement properties.
Applications of Fiberglass Laminates
Fiberglass laminates are used in a wide range of applications across various industries, including:
- Marine
- Automotive
- Aerospace
- Wind energy
- Construction
- Sports and recreation
Marine
Fiberglass laminates are extensively used in the marine industry for the construction of boat hulls, decks, and structural components. The high strength-to-weight ratio, corrosion resistance, and durability of fiberglass laminates make them ideal for marine applications. Common fabric styles used in marine laminates include woven roving, chopped strand mat, and combination fabrics.
Automotive
In the automotive industry, fiberglass laminates are used for the production of body panels, hoods, and structural components for high-performance vehicles and race cars. The lightweight and moldable nature of fiberglass laminates allows for the creation of complex shapes and aerodynamic designs. Twill and satin weave fabrics are often used in automotive laminates for their attractive appearance and good mechanical properties.
Aerospace
Fiberglass laminates find applications in the aerospace industry for the manufacture of secondary structures, such as fairings, interior panels, and control surfaces. High-performance unidirectional and woven fabrics, often in combination with carbon fibers, are used to achieve the required strength, stiffness, and weight savings.
Wind Energy
In the wind energy sector, fiberglass laminates are used for the construction of wind turbine blades. The high fatigue resistance and good mechanical properties of fiberglass laminates make them suitable for the demanding operating conditions of wind turbines. Unidirectional and biaxial fabrics are commonly used in the main structural elements of the blades, while woven fabrics are employed in the blade root and trailing edge.
Construction
Fiberglass laminates are used in the construction industry for the production of architectural panels, cladding, and reinforcement elements. The corrosion resistance, durability, and low maintenance requirements of fiberglass laminates make them attractive for use in harsh environments. Woven roving and combination fabrics are often used in construction laminates.
Sports and Recreation
Fiberglass laminates are widely used in the sports and recreation industry for the manufacture of equipment such as fishing rods, golf club shafts, and bicycle frames. The high strength-to-weight ratio and tailorable properties of fiberglass laminates allow for the creation of high-performance sporting goods. Unidirectional and high-performance woven fabrics are commonly used in this sector.
Frequently Asked Questions (FAQ)
- Q: What is the difference between plain, twill, and satin weave fabrics?
A: Plain weave fabrics have a simple, alternating over-under pattern, providing good stability and balanced properties. Twill weave fabrics feature a diagonal ribbing pattern, offering better drapeability and mechanical properties in the bias direction. Satin weave fabrics have long float fibers, creating a smooth surface and excellent drapeability, with high mechanical properties in the direction of the long floats.
- Q: When should I use unidirectional fabrics in a laminate?
A: Unidirectional fabrics are best used when you require the highest mechanical properties in a specific direction, such as in applications that demand exceptional strength and stiffness. However, unidirectional fabrics have poor properties in the transverse direction and are more challenging to handle and lay up compared to woven fabrics.
- Q: Can I combine different fabric styles in a single laminate?
A: Yes, combining different fabric styles in a laminate is a common practice. For example, using a combination of woven fabrics and chopped strand mat can help improve the resin-to-glass ratio and achieve the desired mechanical properties. Alternating between unidirectional and woven fabrics can also be used to tailor the laminate properties for specific applications.
- Q: How do I select the appropriate fabric weight for my laminate?
A: The fabric weight selection depends on the desired thickness, reinforcement content, and mechanical properties of the laminate. Heavier fabrics generally offer higher strength and stiffness but may result in a thicker and heavier laminate. It is essential to consider the specific requirements of your application and consult with a composite materials expert or supplier to determine the optimal fabric weight.
- Q: What are the key factors to consider when storing and handling fiberglass fabrics?
A: When storing fiberglass fabrics, it is crucial to keep them in a clean, dry environment, away from direct sunlight and sources of contamination. Proper storage helps maintain the quality and consistency of the fabrics. When handling the fabrics, care should be taken to avoid damage, such as fraying or snagging, which can compromise the reinforcement properties. It is also important to follow the manufacturer’s guidelines for handling and storage to ensure the best results in your laminate.
In conclusion, the selection of fiberglass fabric styles in laminates is a critical aspect of designing and manufacturing composite structures. Each fabric style offers unique properties and advantages, and the choice depends on the specific requirements of the application, such as mechanical properties, drapability, surface finish, and cost. By understanding the characteristics and benefits of different fabric styles, designers and manufacturers can optimize their laminates for performance, durability, and cost-effectiveness. Proper layup considerations, including fiber orientation, stacking sequence, and ply drop-offs, are also essential for achieving the desired properties and performance of the laminate. With the wide range of applications across various industries, fiberglass laminates continue to play a vital role in the development of lightweight, high-performance structures.
Leave a Reply