Understanding High Frequency Signals
Before diving into the specific factors that impact high frequency PCB design, it is essential to understand the nature of high frequency signals. High frequency signals, typically defined as signals with frequencies above 100 MHz, behave differently than their low Frequency Counterparts. At these higher frequencies, the wavelengths of the signals become comparable to the physical dimensions of the PCB traces, leading to a range of effects that can degrade signal quality and integrity.
Skin Effect
One of the primary characteristics of high frequency signals is the skin effect. As the frequency of a signal increases, the current tends to flow more on the outer surface (skin) of the conductor rather than uniformly throughout its cross-section. This phenomenon is due to the interaction between the alternating current and the magnetic field it generates. The skin effect leads to increased resistance and power loss in the conductor at high frequencies.
The skin depth, denoted as δ, is a measure of how far the current penetrates into the conductor. It is defined as:
δ = √(ρ / (π * f * μ))
Where:
– ρ is the resistivity of the conductor material
– f is the frequency of the signal
– μ is the permeability of the conductor material
As the frequency increases, the skin depth decreases, confining the current to a thinner layer on the surface of the conductor. To mitigate the impact of the skin effect, PCB designers often use wider traces or multiple parallel traces to increase the effective surface area for current flow.
Dielectric Losses
In addition to conductor losses, high frequency signals also experience dielectric losses. Dielectric materials, such as the substrate used in PCBs, have a complex permittivity that varies with frequency. At higher frequencies, the dielectric material absorbs more energy from the signal, leading to attenuation and loss.
The dielectric loss is characterized by the loss tangent (tan δ), which is a measure of the energy dissipated in the dielectric material relative to the energy stored. A higher loss tangent indicates greater dielectric losses. PCB designers must carefully select low-loss dielectric materials and consider the impact of dielectric losses when designing high frequency circuits.
Factors Influencing High Frequency PCB Design
Several key factors influence the performance and integrity of high frequency PCB designs. By understanding and addressing these factors, designers can create robust and reliable high frequency circuits.
Impedance Control
Impedance control is crucial in high frequency PCB design. Impedance mismatches between the source, transmission line, and load can lead to signal reflections, which cause distortions and degrade signal quality. To achieve impedance control, designers must carefully select the appropriate trace width, thickness, and spacing based on the desired characteristic impedance.
The characteristic impedance (Z0) of a transmission line is determined by its geometry and the dielectric properties of the surrounding material. For a microstrip transmission line, which is commonly used in PCB designs, the characteristic impedance can be approximated using the following equation:
Z0 = (87 / √(ε_r + 1.41)) * ln(5.98 * h / (0.8 * w + t))
Where:
– ε_r is the relative permittivity of the dielectric material
– h is the height of the dielectric between the trace and the ground plane
– w is the width of the trace
– t is the thickness of the trace
By controlling these parameters, designers can achieve the desired characteristic impedance and minimize impedance mismatches.
Signal Integrity
Signal integrity is a critical aspect of high frequency PCB design. As signals propagate through the PCB, they can suffer from various issues such as crosstalk, reflections, and electromagnetic interference (EMI). These issues can lead to signal distortions, jitter, and reduced noise margins, compromising the overall performance of the system.
To maintain signal integrity, designers must implement several techniques:
-
Proper grounding and shielding: Adequate grounding and shielding techniques help reduce EMI and minimize crosstalk between signals. Designers should use ground planes, stitching vias, and shielding enclosures to provide a low-impedance return path for high frequency currents and contain electromagnetic fields.
-
Trace routing and spacing: Careful trace routing and spacing are essential to minimize crosstalk and signal coupling. Designers should follow guidelines for trace spacing based on the signal frequencies and use techniques like differential pair routing and guard traces to reduce interference.
-
Termination and matching: Proper termination and matching techniques help prevent signal reflections and ensure clean signal transitions. Designers can use series and parallel termination resistors, as well as matching networks, to match the impedance of the source and load to the characteristic impedance of the transmission line.
-
Filtering and decoupling: Filtering and decoupling capacitors help suppress high frequency noise and provide a stable power supply to the active components. Designers should place decoupling capacitors close to the power pins of ICs and use power supply filtering to attenuate noise.
Material Selection
The choice of materials used in a high frequency PCB design has a significant impact on its performance. Designers must carefully select the substrate material, conductor material, and any additional components based on their electrical and mechanical properties.
For the substrate material, common choices include FR-4, Rogers, and Isola materials. Each material has its own dielectric constant (ε_r), loss tangent (tan δ), and thermal properties. Low-loss materials like Rogers are often preferred for high frequency applications due to their excellent dielectric properties and low dissipation factors.
Material | Dielectric Constant (ε_r) | Loss Tangent (tan δ) | Thermal Conductivity (W/mK) |
---|---|---|---|
FR-4 | 4.3 – 4.7 | 0.02 – 0.03 | 0.3 – 0.4 |
Rogers RO4003C | 3.38 | 0.0027 | 0.71 |
Isola I-Tera MT40 | 3.45 | 0.0031 | 0.4 |
For the conductor material, copper is the most commonly used due to its excellent electrical conductivity and relatively low cost. However, in high frequency applications, designers may opt for alternative conductor materials like silver or gold to reduce skin effect losses and improve conductivity.
Thermal Management
Thermal management is an important consideration in high frequency PCB design. As the operating frequencies increase, so does the power dissipation in the components and traces. This can lead to increased temperatures, which can affect the performance and reliability of the PCB.
To manage thermal issues, designers should:
-
Use thermal vias: Thermal vias are used to transfer heat from the components to the ground plane or other heat-dissipating layers. They provide a low-resistance path for heat flow and help distribute the heat more evenly across the PCB.
-
Implement heat spreaders: Heat spreaders are conductive materials, such as copper or aluminum, that are used to spread the heat generated by components over a larger area. They help reduce hot spots and improve overall thermal dissipation.
-
Consider component placement: Proper component placement is crucial for effective thermal management. Designers should place heat-generating components away from sensitive circuits and provide adequate spacing for airflow and heat dissipation.
-
Use thermal simulation tools: Thermal simulation tools help designers analyze the temperature distribution across the PCB and identify potential hot spots. These tools allow designers to optimize the layout and thermal management strategies before finalizing the design.
High Frequency PCB Design Best Practices
To ensure successful high frequency PCB designs, designers should adhere to best practices and guidelines. Some key best practices include:
-
Keep traces as short as possible: Minimizing trace lengths helps reduce signal attenuation, delay, and reflections. Designers should place components close together and use direct routing paths whenever possible.
-
Use ground planes: Ground planes provide a low-impedance return path for high frequency currents and help minimize EMI. Designers should use continuous ground planes and provide adequate grounding for all components.
-
Avoid sharp corners and discontinuities: Sharp corners and discontinuities in traces can cause signal reflections and impedance mismatches. Designers should use smooth transitions, such as curved traces or mitered corners, to maintain signal integrity.
-
Match trace lengths: Matching trace lengths is important for maintaining signal synchronization and minimizing skew. Designers should route critical signals, such as clock and data lines, with equal trace lengths to ensure proper timing.
-
Use simulation and analysis tools: Simulation and analysis tools, such as electromagnetic field solvers and signal integrity analyzers, help designers optimize their high frequency PCB layouts. These tools provide insights into signal behavior, impedance, and potential issues before the design is finalized.
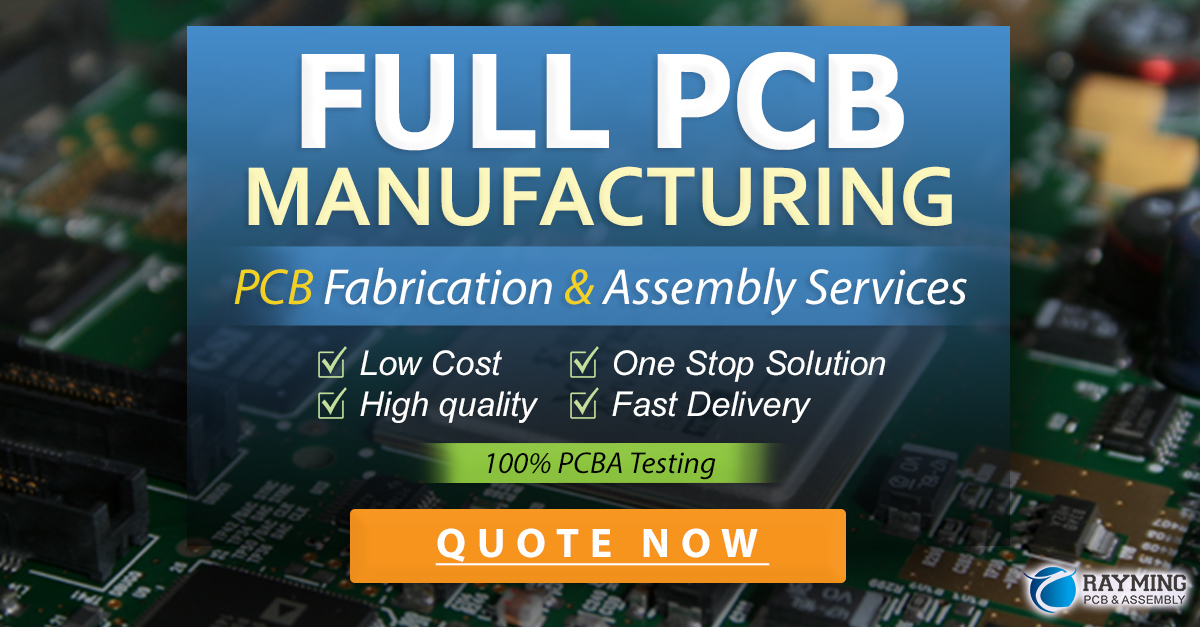
Frequently Asked Questions (FAQ)
- What is considered a high frequency in PCB design?
-
In PCB design, signals with frequencies above 100 MHz are typically considered high frequency. However, the exact frequency threshold may vary depending on the specific application and the design requirements.
-
Why is impedance control important in high frequency PCB design?
-
Impedance control is crucial in high frequency PCB design because impedance mismatches can lead to signal reflections, which cause distortions and degrade signal quality. By controlling the impedance of the transmission lines, designers can minimize reflections and ensure proper signal propagation.
-
What are some common challenges in high frequency PCB design?
-
Some common challenges in high frequency PCB design include managing signal integrity, mitigating crosstalk and EMI, selecting appropriate materials, and ensuring proper thermal management. Designers must carefully consider these factors and implement appropriate techniques to overcome these challenges.
-
How can designers minimize crosstalk in high frequency PCB designs?
-
Designers can minimize crosstalk in high frequency PCB designs by implementing proper trace routing and spacing, using guard traces, and employing differential pair routing. Additionally, using ground planes and shielding techniques can help reduce crosstalk and electromagnetic interference.
-
What simulation and analysis tools are used in high frequency PCB design?
- Various simulation and analysis tools are used in high frequency PCB design, including electromagnetic field solvers, signal integrity analyzers, and thermal simulation tools. These tools help designers analyze signal behavior, impedance, EMI, and thermal performance, enabling them to optimize their designs before fabrication.
Conclusion
High frequency PCB design requires a comprehensive understanding of the factors that influence signal integrity, impedance control, and overall performance. By considering skin effect, dielectric losses, impedance matching, signal integrity, material selection, and thermal management, designers can create robust and reliable high frequency circuits.
Adhering to best practices, such as minimizing trace lengths, using ground planes, avoiding discontinuities, and employing simulation and analysis tools, helps designers overcome the challenges associated with high frequency PCB design.
As the demand for high-speed electronic devices continues to grow, mastering the art of high frequency PCB design becomes increasingly critical. By staying informed about the latest techniques, materials, and tools, PCB designers can push the boundaries of performance and deliver cutting-edge solutions for a wide range of applications.
Leave a Reply