Introduction to Embedded PCB Technology
Embedded PCB technology is a revolutionary approach to circuit board design that involves embedding components within the layers of a multi-layer printed circuit board (PCB). This innovative technique offers numerous advantages over traditional surface-mount technology (SMT), including improved electrical performance, reduced board size, and enhanced reliability.
In this comprehensive article, we will delve into the world of embedded PCB technology, exploring its benefits, applications, design considerations, and manufacturing processes. We will also discuss the challenges associated with this technology and provide insights into its future prospects.
What is an Embedded PCB?
An embedded PCB is a multi-layer circuit board that contains embedded components within its layers. Unlike traditional PCBs, where components are mounted on the surface of the board, embedded PCBs have components placed inside the board itself, sandwiched between the layers of the PCB stack-up.
The embedded components can include passive devices such as resistors, capacitors, and inductors, as well as active components like integrated circuits (ICs) and sensors. These components are typically placed in cavities or cutouts within the PCB layers and are interconnected using conductive traces and vias.
Types of Embedded Components
Embedded PCBs can accommodate a wide range of components, depending on the specific application and design requirements. Some common types of embedded components include:
-
Resistors: Thin-film or thick-film resistors can be embedded within the PCB layers, offering precise resistance values and low parasitic inductance.
-
Capacitors: Embedded capacitors, such as ceramic or tantalum capacitors, provide decoupling and filtering functions while minimizing the board space required.
-
Inductors: Embedded inductors, including planar inductors and ferrite-core inductors, can be used for power management and signal conditioning applications.
-
ICs: Bare die or packaged ICs can be embedded within the PCB layers, enabling high-density integration and improved electrical performance.
-
Sensors: Various types of sensors, such as temperature, pressure, or optical sensors, can be embedded to create smart and intelligent PCBs.
Benefits of Embedded PCB Technology
Embedded PCB technology offers several significant advantages over traditional SMT-based PCB designs. Some of the key benefits include:
1. Miniaturization and Space Savings
By embedding components within the PCB layers, designers can achieve a substantial reduction in board size and thickness. This miniaturization is particularly valuable in space-constrained applications, such as wearable devices, implantable medical devices, and aerospace systems.
2. Improved Electrical Performance
Embedded components offer superior electrical performance compared to surface-mounted components. The shorter interconnect lengths and reduced parasitic inductance and capacitance lead to improved signal integrity, reduced crosstalk, and faster signal propagation. This makes embedded PCBs ideal for high-speed and high-frequency applications.
3. Enhanced Reliability and Durability
Embedded components are protected from external environmental factors, such as moisture, dust, and mechanical stress. This increased protection enhances the overall reliability and durability of the PCB, making it suitable for harsh operating conditions and mission-critical applications.
4. Simplified Assembly and Reduced Manufacturing Costs
By embedding components within the PCB layers, the assembly process becomes simpler and more streamlined. Fewer surface-mounted components need to be placed and soldered, reducing the overall assembly time and cost. Additionally, the use of embedded components can minimize the need for expensive packaging and interconnect solutions.
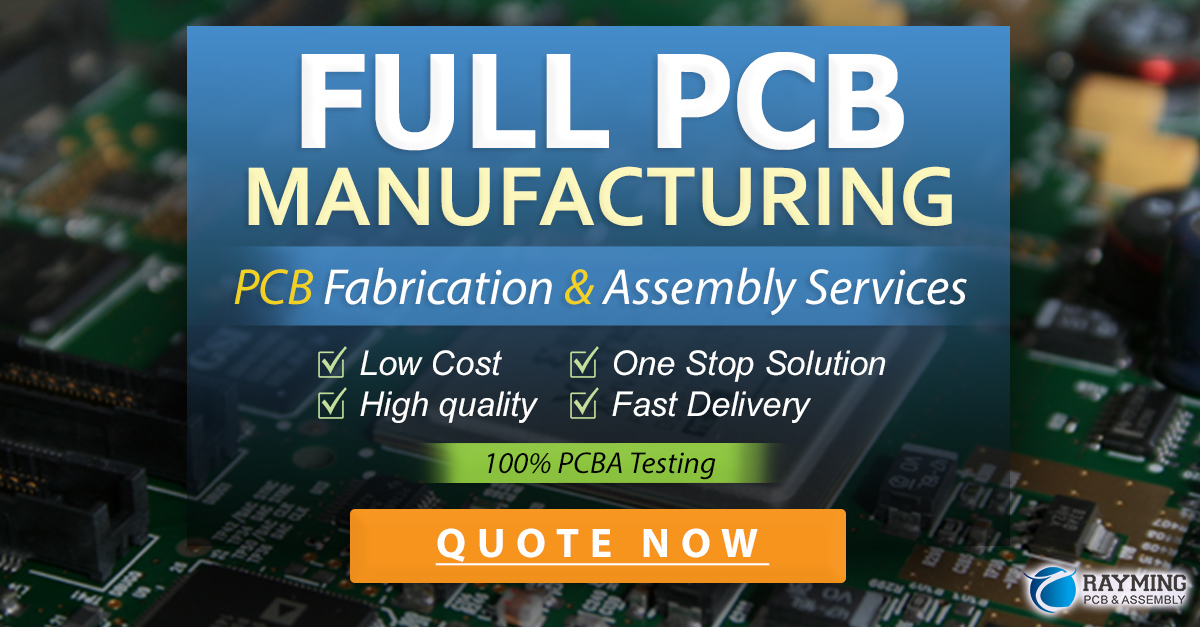
Applications of Embedded PCB Technology
Embedded PCB technology finds applications in a wide range of industries and domains, including:
-
Consumer Electronics: Embedded PCBs are extensively used in smartphones, tablets, smartwatches, and other portable consumer devices, where miniaturization and high-density integration are crucial.
-
Automotive Electronics: Embedded PCBs are employed in various automotive applications, such as engine control units, infotainment systems, and advanced driver assistance systems (ADAS), where reliability and performance are paramount.
-
Medical Devices: Embedded PCBs are used in medical devices, including implantable devices, wearable health monitors, and diagnostic equipment, where miniaturization and reliability are essential.
-
Aerospace and Defense: Embedded PCBs find applications in aerospace and defense systems, such as avionics, radar systems, and satellite communications, where high-performance and ruggedness are critical.
-
Industrial Automation: Embedded PCBs are employed in industrial automation systems, including process control, machine vision, and robotics, where compact size and reliable operation are necessary.
Design Considerations for Embedded PCBs
Designing an embedded PCB requires careful consideration of various factors to ensure optimal performance and manufacturability. Some key design considerations include:
1. Material Selection
The choice of PCB materials is crucial for embedded PCB design. The materials must have the appropriate electrical, thermal, and mechanical properties to support the embedded components and ensure reliable operation. High-performance materials, such as polyimide or liquid crystal polymer (LCP), are commonly used for embedded PCBs.
2. Layer Stack-up and Thickness
The layer stack-up and thickness of an embedded PCB must be carefully designed to accommodate the embedded components and provide the necessary interconnections. The number of layers, the thickness of each layer, and the positioning of the embedded components must be optimized to achieve the desired electrical performance and mechanical integrity.
3. Thermal Management
Embedded components generate heat during operation, and effective thermal management is critical to ensure reliable performance and prevent overheating. Thermal vias, heat spreaders, and thermal interface materials (TIMs) can be used to dissipate heat from the embedded components to the PCB layers and external heatsinks.
4. Signal Integrity and Power Integrity
Embedded PCB design must consider signal integrity and power integrity to ensure optimal electrical performance. This includes proper routing of high-speed signals, impedance matching, and power distribution network (PDN) design. Simulation tools and analysis techniques, such as electromagnetic (EM) simulation and power integrity analysis, are essential for validating the design.
5. Manufacturing Considerations
Embedded PCB design must take into account the manufacturing processes and constraints. The placement and orientation of the embedded components, the size and spacing of the cavities, and the alignment and registration of the layers must be carefully considered to ensure manufacturability and yield.
Manufacturing Process for Embedded PCBs
The manufacturing process for embedded PCBs involves several specialized steps and techniques. The general process flow includes:
-
Layer Fabrication: The individual PCB layers are fabricated using standard PCB manufacturing processes, such as etching, drilling, and plating.
-
Cavity Formation: Cavities or cutouts are created in the PCB layers to accommodate the embedded components. This can be done using laser drilling, mechanical drilling, or controlled depth routing.
-
Component Placement: The embedded components are placed into the cavities using pick-and-place machines or manual placement techniques. Precise alignment and positioning are critical to ensure proper interconnections.
-
Lamination: The PCB layers, with the embedded components in place, are laminated together using heat and pressure. The lamination process creates a solid, multi-layer structure with the embedded components securely sandwiched between the layers.
-
Via Formation: Vias are drilled and plated to create interconnections between the layers and the embedded components. Microvias and buried vias are commonly used in embedded PCB designs.
-
Surface Finish: The outer layers of the embedded PCB are finished using standard surface finish techniques, such as solder mask application and surface plating.
Challenges and Limitations of Embedded PCB Technology
While embedded PCB technology offers numerous benefits, it also presents some challenges and limitations that must be considered:
-
Design Complexity: Embedded PCB design is more complex than traditional SMT-based design. It requires specialized design tools, simulation techniques, and expertise to ensure optimal performance and manufacturability.
-
Manufacturing Challenges: The manufacturing process for embedded PCBs is more complex and requires specialized equipment and processes. Ensuring proper alignment, registration, and interconnections of the embedded components can be challenging.
-
Cost Considerations: Embedded PCB technology can be more expensive than traditional SMT-based PCBs due to the specialized materials, processes, and equipment required. However, the cost can be justified for applications that require the benefits offered by embedded PCBs.
-
Limited Component Availability: Not all components are suitable for embedding within the PCB layers. The availability of embedded-compatible components may be limited compared to surface-mount components.
-
Repair and Rework Challenges: Repairing or reworking an embedded PCB can be more difficult than a traditional SMT-based PCB. Accessing and replacing embedded components may require specialized techniques and equipment.
Future Prospects and Research Directions
Embedded PCB technology is a rapidly evolving field with significant potential for future advancements. Some of the key research directions and future prospects include:
-
Advanced Materials: The development of new, high-performance materials specifically tailored for embedded PCB applications is an active area of research. These materials aim to provide enhanced electrical, thermal, and mechanical properties to support the demands of advanced embedded PCB designs.
-
3D Integration: The integration of embedded components with 3D packaging technologies, such as through-silicon vias (TSVs) and 3D stacking, is a promising avenue for future embedded PCB designs. This combination can enable even higher levels of miniaturization and functionality.
-
Intelligent and Adaptive Embedded PCBs: The integration of sensors, actuators, and processing capabilities within embedded PCBs can enable the development of intelligent and adaptive systems. These smart embedded PCBs can sense and respond to environmental conditions, enabling novel applications in various domains.
-
Additive Manufacturing: The application of additive manufacturing techniques, such as 3D printing, to the fabrication of embedded PCBs is an emerging research area. Additive manufacturing has the potential to enable more complex geometries, faster prototyping, and customized embedded PCB designs.
-
Simulation and Design Automation: The development of advanced simulation tools and design automation methodologies specific to embedded PCB design is an ongoing research focus. These tools aim to streamline the design process, optimize performance, and ensure manufacturability.
Frequently Asked Questions (FAQ)
-
Q: What is the difference between an embedded PCB and a traditional PCB?
A: An embedded PCB has components embedded within the layers of the multi-layer PCB, while a traditional PCB has components mounted on the surface of the board. -
Q: What are the main benefits of using embedded PCB technology?
A: The main benefits of embedded PCB technology include miniaturization, improved electrical performance, enhanced reliability, simplified assembly, and reduced manufacturing costs. -
Q: What types of components can be embedded in an embedded PCB?
A: Embedded PCBs can accommodate a wide range of components, including resistors, capacitors, inductors, ICs, and sensors. -
Q: What are the key design considerations for embedded PCBs?
A: Key design considerations for embedded PCBs include material selection, layer stack-up and thickness, thermal management, signal and power integrity, and manufacturing constraints. -
Q: What are the challenges and limitations of embedded PCB technology?
A: The challenges and limitations of embedded PCB technology include design complexity, manufacturing challenges, cost considerations, limited component availability, and repair and rework challenges.
Conclusion
Embedded PCB technology represents a significant advancement in circuit board design, offering numerous benefits such as miniaturization, improved electrical performance, enhanced reliability, and simplified assembly. By embedding components within the layers of a multi-layer PCB, designers can create highly integrated and compact electronic systems suitable for a wide range of applications.
However, the adoption of embedded PCB technology also presents challenges and considerations, including design complexity, manufacturing processes, and cost factors. Designers must carefully evaluate the specific requirements and constraints of their applications to determine the suitability of embedded PCB technology.
As research and development in this field continue, we can expect further advancements in materials, manufacturing techniques, and design methodologies. The integration of embedded PCBs with emerging technologies, such as 3D packaging and additive manufacturing, holds great promise for future electronic systems.
Embedded PCB technology is poised to play a crucial role in shaping the future of electronics, enabling the development of smaller, smarter, and more reliable devices across various industries. As designers and manufacturers embrace this technology, we can anticipate innovative and groundbreaking applications that push the boundaries of electronic system design.
Leave a Reply