What is Electronics Manufacturing?
Electronics manufacturing is the process of designing, fabricating, assembling, and testing electronic components, devices, and systems. It encompasses a wide range of products, from simple components like resistors and capacitors to complex systems such as computers, smartphones, and aerospace equipment.
The electronics manufacturing industry has grown significantly over the past few decades, driven by the increasing demand for electronic devices in various sectors, including consumer electronics, automotive, healthcare, and industrial automation. The industry is constantly evolving, with new technologies and manufacturing processes being developed to meet the changing needs of the market.
Key Processes in Electronics Manufacturing
1. Product Design and Development
The first step in electronics manufacturing is product design and development. This involves creating a detailed plan for the electronic device or system, including its functionality, performance requirements, and physical layout. Engineers use computer-aided design (CAD) software to create schematics, circuit diagrams, and 3D models of the product.
2. Printed Circuit Board (PCB) Fabrication
Once the product design is finalized, the next step is to fabricate the printed circuit board (PCB). PCBs are the foundation of most electronic devices, providing a platform for mounting and interconnecting electronic components. The PCB fabrication process involves several steps, including:
- Substrate preparation
- Copper foil lamination
- Photoresist application
- Exposure and development
- Etching
- Drilling
- Plating
- Solder mask application
- Silkscreen printing
3. Component Placement and Soldering
After the PCB is fabricated, electronic components are placed on the board and soldered in place. This process can be done manually for low-volume production or prototypes, but automated machines are typically used for high-volume manufacturing. There are two main methods for component placement and soldering:
- Through-hole technology (THT): Components with long leads are inserted through holes in the PCB and soldered on the opposite side.
- Surface mount technology (SMT): Components are placed directly on the surface of the PCB and soldered using a reflow oven.
4. Testing and Quality Control
To ensure the reliability and performance of the electronic device, various testing and quality control measures are implemented throughout the manufacturing process. These may include:
- In-circuit testing (ICT): Verifies the presence and functionality of individual components on the PCB.
- Functional testing: Checks the overall functionality of the assembled device.
- Burn-in testing: Subjects the device to elevated temperatures and operating conditions to identify early failures.
- X-ray inspection: Examines the internal structure of the PCB and components for defects.
- Automated optical inspection (AOI): Uses cameras and image processing software to detect surface-level defects.
5. Final Assembly and Packaging
Once the electronic device has passed all necessary tests, it undergoes final assembly and packaging. This may involve adding enclosures, displays, connectors, and other mechanical components. The finished product is then packaged for distribution and sale.
Advancements in Electronics Manufacturing
The electronics manufacturing industry has seen several significant advancements in recent years, driven by the need for smaller, faster, and more efficient devices. Some of these advancements include:
1. Miniaturization
As electronic devices become smaller and more compact, manufacturers have had to develop new techniques for fabricating and assembling miniaturized components. This has led to the widespread adoption of SMT, as well as the development of advanced packaging technologies such as:
- Chip-scale packaging (CSP): Packages the semiconductor die directly, resulting in a package that is only slightly larger than the die itself.
- System-in-package (SiP): Integrates multiple dies and passive components into a single package, enabling higher density and functionality.
- 3D packaging: Stacks multiple dies vertically, connected by through-silicon vias (TSVs), allowing for even greater density and performance.
2. Flexible and Printed Electronics
Flexible and printed electronics are emerging technologies that enable the fabrication of electronic devices on flexible substrates, such as plastic or paper. This allows for the creation of novel form factors and applications, such as wearable devices, smart packaging, and disposable sensors.
Printed electronics use various printing methods, such as inkjet, screen, and gravure printing, to deposit conductive inks and other materials onto the substrate. This enables low-cost, high-volume production of electronic devices, although the performance and reliability of printed electronics are generally lower than those of conventional electronics.
3. Industry 4.0 and Smart Manufacturing
Industry 4.0, also known as the Fourth Industrial Revolution, refers to the integration of advanced technologies such as the Internet of Things (IoT), artificial intelligence (AI), and robotics into manufacturing processes. In the context of electronics manufacturing, this has led to the development of smart factories, which leverage these technologies to improve efficiency, quality, and flexibility.
Some examples of Industry 4.0 applications in electronics manufacturing include:
- Predictive maintenance: Sensors and AI algorithms monitor equipment performance and predict when maintenance is required, reducing downtime and extending equipment life.
- Automated quality control: Machine vision systems and AI-powered defect detection algorithms identify and classify defects in real-time, enabling faster and more accurate quality control.
- Flexible automation: Collaborative robots (cobots) and reconfigurable manufacturing systems enable quick changeovers and customization, allowing manufacturers to adapt to changing market demands.
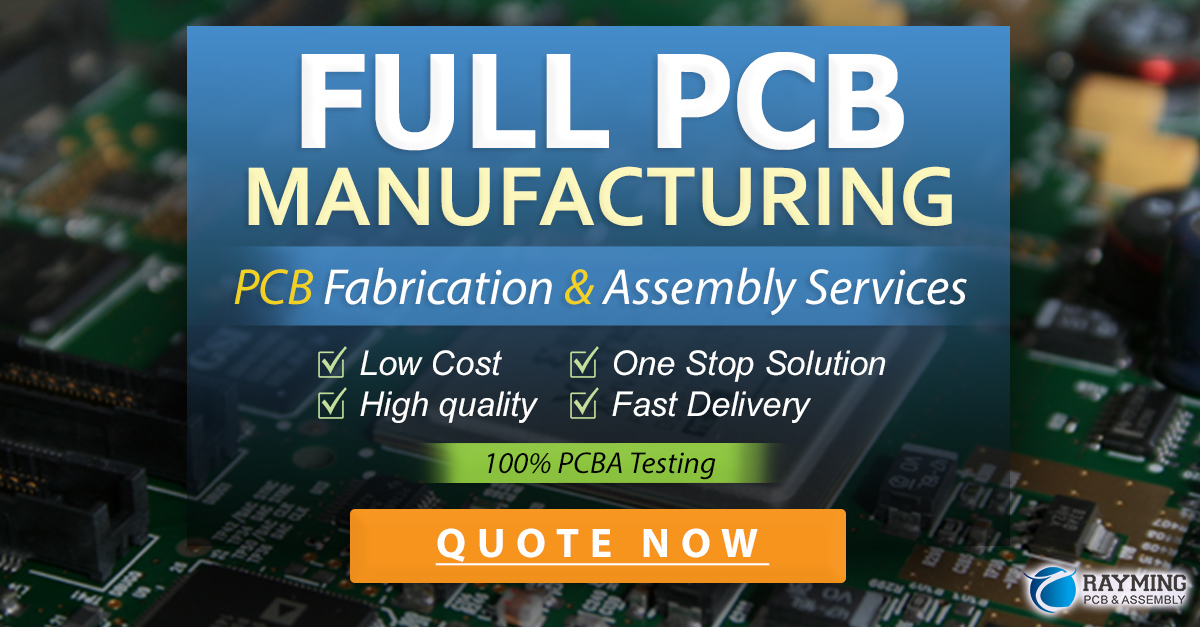
Challenges in Electronics Manufacturing
Despite the advancements in technology and manufacturing processes, the electronics manufacturing industry faces several challenges:
1. Supply Chain Disruptions
The global nature of the electronics supply chain makes it vulnerable to disruptions caused by natural disasters, geopolitical events, and other unforeseen circumstances. The COVID-19 pandemic, for example, highlighted the fragility of the supply chain, as lockdowns and travel restrictions led to shortages of raw materials, components, and finished products.
To mitigate these risks, manufacturers are exploring strategies such as diversifying their supplier base, increasing inventory levels, and localizing production.
2. Rapid Technological Change
The fast pace of technological change in the electronics industry can be both an opportunity and a challenge for manufacturers. On one hand, new technologies enable the creation of innovative products and open up new markets. On the other hand, they also require significant investments in research and development, equipment, and workforce training.
Manufacturers must stay up-to-date with the latest trends and technologies to remain competitive, while also managing the risks associated with investing in unproven or rapidly evolving technologies.
3. Environmental and Social Responsibility
As concerns about climate change, resource depletion, and social responsibility grow, electronics manufacturers face increasing pressure to adopt sustainable and ethical practices. This includes reducing greenhouse gas emissions, minimizing waste and the use of hazardous materials, ensuring fair labor practices, and managing the end-of-life disposal of electronic products.
Manufacturers are responding to these challenges by implementing sustainability initiatives, such as using renewable energy, designing products for recyclability, and participating in e-waste recycling programs. They are also working to improve transparency and accountability in their supply chains, through initiatives such as the Responsible Business Alliance (RBA) and the Conflict-Free Sourcing Initiative (CFSI).
The Future of Electronics Manufacturing
Looking ahead, the electronics manufacturing industry is poised for continued growth and transformation, driven by several key trends:
1. 5G and the Internet of Things (IoT)
The deployment of 5G networks and the proliferation of IoT devices are expected to create significant opportunities for electronics manufacturers. 5G’s high speed, low latency, and massive connectivity will enable new applications in areas such as autonomous vehicles, smart cities, and industrial automation. This will drive demand for 5G-enabled devices, as well as the infrastructure and components required to support them.
Similarly, the growth of the IoT will create demand for a wide range of connected devices, from smart home appliances to industrial sensors. Electronics manufacturers will need to develop new products and manufacturing processes to meet the unique requirements of these devices, such as low power consumption, small form factors, and seamless connectivity.
2. Artificial Intelligence (AI) and Edge Computing
AI is increasingly being integrated into electronic devices, enabling new capabilities such as voice recognition, image processing, and predictive maintenance. However, the high computational requirements of AI algorithms often require data to be processed in the cloud, which can introduce latency and security concerns.
Edge computing is an emerging paradigm that addresses these challenges by processing data closer to the source, i.e., on the device itself or on a local server. This enables faster response times, reduced bandwidth requirements, and improved data security. Electronics manufacturers will need to develop new hardware and software solutions to support edge computing, such as high-performance processors, energy-efficient memory, and optimized AI algorithms.
3. Sustainability and Circular Economy
As environmental concerns continue to grow, electronics manufacturers will face increasing pressure to adopt sustainable practices and contribute to the circular economy. This will require a fundamental shift in how products are designed, manufactured, and managed throughout their lifecycle.
Some key strategies for promoting sustainability in electronics manufacturing include:
- Design for sustainability: Designing products that are energy-efficient, durable, and easy to repair, upgrade, and recycle.
- Sustainable materials: Using renewable, biodegradable, and recycled materials in product design and packaging.
- Closed-loop manufacturing: Implementing processes for recovering and reusing materials from end-of-life products.
- Product-as-a-service: Exploring new business models that prioritize access over ownership, such as leasing and subscription-based services.
Conclusion
Electronics manufacturing is a dynamic and rapidly evolving industry that plays a crucial role in enabling technological progress and economic growth. As the demand for electronic devices continues to grow, manufacturers must navigate a complex landscape of technological, economic, and social challenges.
By embracing advancements in areas such as miniaturization, flexible electronics, and Industry 4.0, and by prioritizing sustainability and social responsibility, electronics manufacturers can position themselves for success in the years ahead. The future of electronics manufacturing is bright, but it will require ongoing innovation, collaboration, and adaptability to meet the evolving needs of the market and society.
FAQs
1. What is the difference between through-hole technology (THT) and surface mount technology (SMT)?
THT involves inserting component leads through holes in the PCB and soldering them on the opposite side, while SMT involves placing components directly on the surface of the PCB and soldering them using a reflow oven. SMT allows for smaller, denser PCBs and is more suitable for high-volume production, while THT is often used for larger components or in applications that require greater mechanical strength.
2. What are some of the key challenges facing the electronics manufacturing industry?
Some of the key challenges include supply chain disruptions, rapid technological change, and increasing pressure to adopt sustainable and socially responsible practices. Manufacturers must also navigate a complex landscape of regulations, standards, and intellectual property issues.
3. How is the Internet of Things (IoT) impacting electronics manufacturing?
The growth of the IoT is creating demand for a wide range of connected devices, from smart home appliances to industrial sensors. This requires manufacturers to develop new products and manufacturing processes that can meet the unique requirements of these devices, such as low power consumption, small form factors, and seamless connectivity.
4. What is the role of artificial intelligence (AI) in electronics manufacturing?
AI is being integrated into various aspects of electronics manufacturing, from product design and process optimization to quality control and predictive maintenance. AI algorithms can analyze vast amounts of data from sensors and other sources to identify patterns, detect anomalies, and make predictions that can improve efficiency, quality, and reliability.
5. How can electronics manufacturers contribute to a more sustainable future?
Electronics manufacturers can adopt a range of strategies to promote sustainability, such as designing products for energy efficiency, durability, and recyclability; using sustainable materials; implementing closed-loop manufacturing processes; and exploring new business models that prioritize access over ownership. By prioritizing sustainability throughout the product lifecycle, manufacturers can reduce their environmental impact and contribute to a more circular economy.
Leave a Reply