History of Electronic Manufacturing Technology
Early Developments
The origins of EMT can be traced back to the early 20th century, with the invention of the vacuum tube and the subsequent development of radio technology. During World War II, the demand for electronic components increased significantly, leading to the establishment of dedicated electronic manufacturing facilities. In the 1950s, the invention of the transistor revolutionized the electronics industry, paving the way for smaller, more efficient electronic devices.
The Rise of Integrated Circuits
In 1958, Jack Kilby of Texas Instruments and Robert Noyce of Fairchild Semiconductor independently invented the integrated circuit (IC), which marked a turning point in EMT. ICs allowed for the miniaturization of electronic components and the development of more complex electronic systems. Throughout the 1960s and 1970s, advancements in IC technology led to the creation of microprocessors, memory chips, and other essential components of modern electronics.
Automation and the Digital Age
The 1980s and 1990s saw the widespread adoption of automation in electronic manufacturing, with the introduction of surface mount technology (SMT) and computer-aided design (CAD) tools. These advancements streamlined the manufacturing process and enabled the production of more complex PCBs and electronic devices. The digital age, which began in the late 20th century, further accelerated the growth of EMT, as the demand for consumer electronics, personal computers, and mobile devices skyrocketed.
Key Processes in Electronic Manufacturing Technology
Printed Circuit Board (PCB) Fabrication
PCBs are the foundation of most electronic devices, providing a platform for mounting and interconnecting electronic components. The PCB fabrication process involves several steps:
- Design: PCBs are designed using CAD software, which generates the necessary files for manufacturing.
- Material preparation: A substrate, typically made of fiberglass or other insulating material, is cut to size and cleaned.
- Copper cladding: A thin layer of copper is laminated onto the substrate.
- Patterning: The desired circuit pattern is transferred onto the copper layer using photolithography or other imaging techniques.
- Etching: Unwanted copper is removed using a chemical etching process, leaving only the desired circuit pattern.
- Drilling: Holes are drilled through the PCB to accommodate through-hole components and vias.
- Plating: The holes are plated with copper to ensure electrical continuity.
- Solder mask and silkscreen: A protective solder mask is applied to the PCB, and a silkscreen layer is added for component labeling.
Surface Mount Technology (SMT)
SMT is a method of mounting electronic components directly onto the surface of a PCB, as opposed to through-hole mounting. SMT offers several advantages, including:
- Smaller component sizes
- Higher component density
- Faster assembly speeds
- Improved reliability
The SMT process typically involves the following steps:
- Solder paste application: A precise amount of solder paste is applied to the PCB pads using a stencil or screen printing process.
- Component placement: Surface mount components are placed onto the solder paste using pick-and-place machines or manual methods.
- Reflow soldering: The PCB is heated in a reflow oven, melting the solder paste and creating a permanent bond between the components and the PCB.
- Inspection: The assembled PCB is inspected for defects using automated optical inspection (AOI) or manual methods.
Through-Hole Technology (THT)
THT involves mounting components with leads that are inserted through holes in the PCB and soldered onto the opposite side. While SMT has largely replaced THT in modern electronic manufacturing, THT is still used for certain components, such as connectors and large capacitors. The THT process involves:
- Component insertion: Through-hole components are manually or automatically inserted into the PCB holes.
- Wave soldering: The PCB is passed over a wave of molten solder, which fills the holes and creates a bond between the component leads and the PCB.
- Inspection: The assembled PCB is inspected for defects and solder joint quality.
Conformal Coating
Conformal coating is a process that involves applying a thin, protective layer of polymer material over the assembled PCB to protect it from environmental factors, such as moisture, dust, and chemicals. Common conformal coating materials include:
- Acrylic
- Silicone
- Polyurethane
- Epoxy
Conformal coating can be applied using various methods, such as spray coating, brush coating, or dip coating, depending on the specific requirements of the application.
Quality Control and Testing in EMT
Automated Optical Inspection (AOI)
AOI is a method of inspecting PCBs and electronic assemblies using high-resolution cameras and advanced image processing software. AOI systems can detect a wide range of defects, including:
- Component placement errors
- Solder joint defects
- Missing or incorrect components
- Polarity errors
AOI is typically performed immediately after the SMT or THT process to identify defects early in the manufacturing process, reducing the risk of costly rework or product failures.
In-Circuit Testing (ICT)
ICT is a testing method that involves using a specialized fixture to make direct electrical contact with the nodes of a PCB. The fixture applies electrical signals to the PCB and measures the response, allowing for the detection of:
- Short circuits
- Open circuits
- Component value variations
- Incorrect component placement
ICT is often performed after the assembly process to ensure that the PCB functions as intended and meets the specified electrical requirements.
Functional Testing
Functional testing involves testing the complete electronic device or system to ensure that it performs its intended function correctly. This may include:
- Power-on testing
- Software testing
- Environmental testing (e.g., temperature, humidity, vibration)
- Compatibility testing
Functional testing is typically performed on a sample of the finished products to verify that they meet the desired performance and reliability standards.
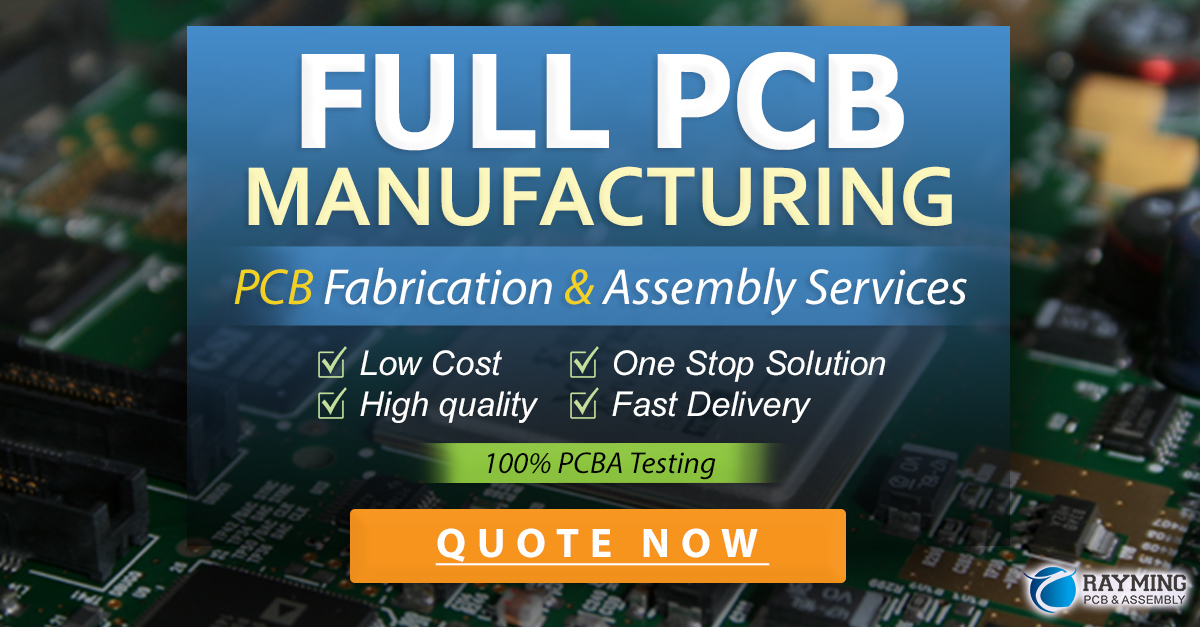
Current Trends in Electronic Manufacturing Technology
Miniaturization
The trend towards miniaturization continues to drive advancements in EMT, with the development of smaller, more powerful electronic components and devices. This trend is evident in the growing demand for Wearable Technology, Internet of Things (IoT) devices, and compact medical devices.
Flexible and Stretchable Electronics
Flexible and stretchable electronics are gaining popularity in applications such as wearable devices, medical implants, and soft robotics. These devices require specialized materials and manufacturing processes, such as printed electronics and 3D printing, to achieve the desired flexibility and stretchability.
3D Printing
3D printing, also known as additive manufacturing, is increasingly being used in EMT for prototyping, low-volume production, and the creation of complex geometric structures. 3D printing technologies, such as fused deposition modeling (FDM) and stereolithography (SLA), allow for the rapid fabrication of custom electronic enclosures, connectors, and even PCBs.
Industry 4.0 and Smart Manufacturing
Industry 4.0, or the fourth industrial revolution, refers to the integration of advanced technologies, such as artificial intelligence (AI), the Internet of Things (IoT), and big data analytics, into manufacturing processes. In the context of EMT, this means the development of smart factories that can optimize production, improve quality control, and reduce waste. Some key aspects of Industry 4.0 in EMT include:
- Machine-to-machine communication
- Real-time data collection and analysis
- Predictive maintenance
- Automated guided vehicles (AGVs) for material handling
Future Prospects for Electronic Manufacturing Technology
The future of EMT is closely tied to the ongoing technological advancements and the growing demand for innovative electronic products. Some of the key areas that are expected to shape the future of EMT include:
5G and Beyond
The deployment of 5G networks and the development of future generations of wireless communication technology will drive the demand for new electronic components and devices. EMT will need to adapt to the high-frequency, high-bandwidth requirements of these networks, which may involve the development of new materials and manufacturing processes.
Artificial Intelligence and Edge Computing
As AI becomes more prevalent in electronic devices, there will be a growing need for edge computing solutions that can process data locally, reducing latency and improving privacy. EMT will play a crucial role in the development of AI-enabled devices and edge computing hardware, such as specialized processors and sensors.
Sustainable and Eco-Friendly Manufacturing
With increasing environmental concerns and regulations, there will be a growing emphasis on sustainable and eco-friendly manufacturing practices in EMT. This may involve the use of biodegradable materials, the development of energy-efficient manufacturing processes, and the implementation of closed-loop recycling systems for electronic waste.
Quantum Computing
As quantum computing technology advances, there will be a need for specialized electronic components and devices that can operate at the quantum scale. EMT will need to adapt to the unique requirements of quantum computing, such as the need for cryogenic temperatures and the precise control of quantum states.
FAQ
1. What is the difference between SMT and THT?
Surface Mount Technology (SMT) involves mounting electronic components directly onto the surface of a PCB, while Through-Hole Technology (THT) involves inserting component leads through holes in the PCB and soldering them onto the opposite side. SMT has largely replaced THT in modern electronic manufacturing due to its advantages in terms of component size, density, and assembly speed.
2. What are the main steps in the PCB fabrication process?
The main steps in the PCB fabrication process include design, material preparation, copper cladding, patterning, etching, drilling, plating, and the application of solder mask and silkscreen layers. Each step plays a crucial role in creating a functional and reliable PCB.
3. What is the purpose of conformal coating in EMT?
Conformal coating is a process that involves applying a thin, protective layer of polymer material over an assembled PCB to protect it from environmental factors, such as moisture, dust, and chemicals. This helps to improve the reliability and longevity of the electronic device.
4. What are some of the key trends in EMT?
Some of the key trends in EMT include miniaturization, flexible and stretchable electronics, 3D printing, and the adoption of Industry 4.0 technologies, such as AI, IoT, and smart manufacturing. These trends are driven by the growing demand for innovative and efficient electronic products.
5. How is EMT likely to evolve in the future?
The future of EMT is expected to be shaped by advancements in wireless communication (5G and beyond), artificial intelligence, edge computing, sustainable manufacturing practices, and quantum computing. EMT will need to adapt to the unique requirements and challenges posed by these technologies to remain competitive and meet the evolving needs of the electronics industry.
In conclusion, Electronic Manufacturing Technology is a dynamic and constantly evolving field that plays a crucial role in the production of electronic components, PCBs, and complete electronic devices. As technology continues to advance, EMT will need to adapt to new challenges and opportunities, driving innovation and shaping the future of the electronics industry.
Leave a Reply