Introduction to Electroless Cu Deposition
Electroless copper (Cu) deposition is a chemical process that involves the deposition of a thin, uniform layer of copper onto a substrate without the use of an external electrical current. This process has gained significant attention in various industries due to its ability to provide a cost-effective and reliable method for creating conductive surfaces on both conductive and non-conductive materials. Electroless Cu deposition finds applications in printed circuit boards (PCBs), microelectronics, and other advanced technologies.
Advantages of Electroless Cu Deposition
Electroless Cu deposition offers several advantages over traditional electroplating methods:
- Uniform coating thickness, even on complex geometries and hard-to-reach areas
- Ability to deposit copper on non-conductive substrates
- Excellent adhesion and mechanical properties
- Cost-effective and scalable process
- Environmentally friendly compared to electroplating
Mechanism of Electroless Cu Deposition
The electroless Cu deposition process involves the reduction of copper ions (Cu^2+^) to metallic copper (Cu^0^) on a catalytic surface in the presence of a reducing agent. The overall reaction can be represented as follows:
Cu^2+^ + 2HCHO + 4OH^-^ → Cu^0^ + 2HCOO^-^ + 2H~2~O + H~2~
The key components of the electroless Cu deposition process are:
- Copper source: Typically, copper sulfate (CuSO~4~) or copper chloride (CuCl~2~) is used as the source of Cu^2+^ ions.
- Reducing agent: Formaldehyde (HCHO) is the most common reducing agent used in electroless Cu deposition. Other reducing agents include sodium hypophosphite (NaH~2~PO~2~) and dimethylamine borane (DMAB).
- Complexing agent: Complexing agents, such as ethylenediaminetetraacetic acid (EDTA) or tartrate, are used to prevent the precipitation of copper hydroxide (Cu(OH)~2~) and maintain the stability of the plating bath.
- pH regulator: Sodium hydroxide (NaOH) or potassium hydroxide (KOH) is used to maintain the alkaline pH of the plating bath, typically in the range of 11-13.
- Stabilizers: Stabilizers, such as 2,2′-bipyridyl or thiourea, are added to prevent the spontaneous decomposition of the plating bath and improve the stability of the deposited Cu film.
Steps in Electroless Cu Deposition
The electroless Cu deposition process involves the following steps:
- Surface preparation: The substrate surface is cleaned and pretreated to remove contaminants and activate the surface for copper deposition.
- Sensitization: The substrate is immersed in a solution containing a noble metal salt, such as palladium chloride (PdCl~2~), which adsorbs onto the surface and acts as a catalyst for the subsequent Cu deposition.
- Activation: The sensitized substrate is immersed in a solution containing a reducing agent, such as sodium hypophosphite, which reduces the adsorbed Pd^2+^ ions to metallic Pd^0^, forming catalytic sites for Cu deposition.
- Electroless Cu deposition: The activated substrate is immersed in the electroless Cu plating bath, where the Cu^2+^ ions are reduced to Cu^0^ on the catalytic surface, resulting in the deposition of a uniform Cu layer.
- Post-treatment: The Cu-coated substrate is rinsed, dried, and subjected to any necessary post-treatment processes, such as annealing or surface finishing.
Factors Affecting Electroless Cu Deposition
Several factors influence the quality and properties of the electrolessly deposited Cu film:
- Bath composition: The concentrations of the copper source, reducing agent, complexing agent, and stabilizers in the plating bath have a significant impact on the deposition rate, film morphology, and mechanical properties.
- Bath temperature: Higher bath temperatures generally lead to faster deposition rates but may also result in increased bath instability and reduced film quality.
- pH: The pH of the plating bath must be maintained in the alkaline range (11-13) to ensure efficient Cu deposition and prevent the precipitation of copper hydroxide.
- Agitation: Proper agitation of the plating bath is necessary to ensure uniform mixing of the reactants and prevent localized depletion of the Cu^2+^ ions at the substrate surface.
- Substrate surface: The surface roughness, cleanliness, and catalytic activity of the substrate play a crucial role in determining the adhesion and uniformity of the deposited Cu film.
Optimization of Electroless Cu Deposition
To achieve high-quality Cu films with desired properties, it is essential to optimize the various process parameters. Some strategies for optimization include:
- Design of experiments (DoE): Systematic variation of the process parameters, such as bath composition, temperature, and pH, to identify the optimal operating conditions.
- Surface pretreatment: Proper cleaning and activation of the substrate surface to ensure uniform and adherent Cu deposition.
- Bath stabilization: Use of appropriate stabilizers and regular monitoring of the bath composition to maintain the stability and reproducibility of the plating process.
- Process control: Implementation of in-line monitoring and control systems to ensure consistent bath conditions and film properties.
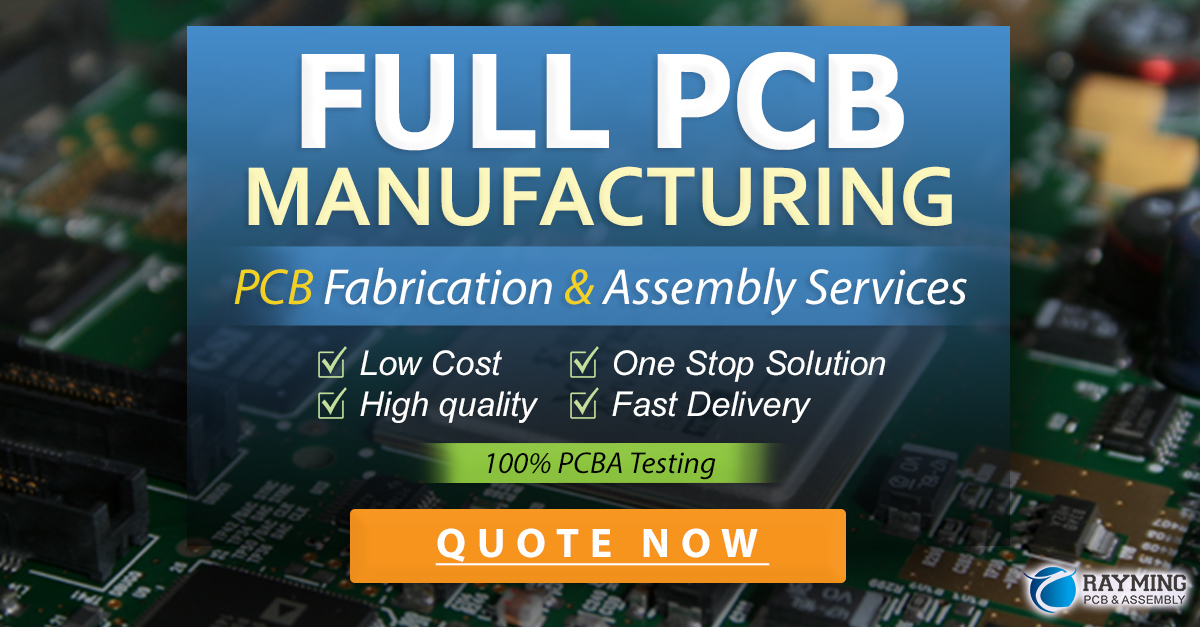
Applications of Electroless Cu Deposition
Electroless Cu deposition finds numerous applications in various industries, including:
- Printed circuit boards (PCBs): Electroless Cu is used as a seed layer for subsequent electroplating of Cu in the fabrication of high-density interconnects and Multilayer PCBs.
- Microelectronics: Electroless Cu is used for the metallization of through-silicon vias (TSVs) and redistribution layers (RDLs) in 3D integrated circuits and advanced packaging technologies.
- Electromagnetic interference (EMI) shielding: Electroless Cu is deposited on plastic housings and enclosures to provide EMI shielding for electronic devices.
- Decorative coatings: Electroless Cu is used as a base layer for subsequent electroplating of decorative metals, such as nickel and chromium, on plastics and other non-conductive substrates.
- Automotive and aerospace: Electroless Cu is used for the metallization of lightweight composite materials, such as carbon fiber reinforced polymers (CFRPs), for improved electrical conductivity and lightning strike protection.
Challenges and Future Perspectives
Despite its numerous advantages and applications, electroless Cu deposition faces several challenges that need to be addressed for further advancement:
- Bath stability: The inherent instability of the electroless Cu plating bath, especially at high temperatures and long operating times, remains a major challenge. The development of novel stabilizers and real-time monitoring systems is crucial for improving bath stability and process reliability.
- Environmental concerns: The use of formaldehyde as a reducing agent in electroless Cu deposition poses environmental and health risks. Research efforts are focused on developing eco-friendly and sustainable alternatives, such as glyoxylic acid and amino acids.
- Adhesion and reliability: Improving the adhesion and long-term reliability of electrolessly deposited Cu films, particularly on non-conductive substrates, remains a key challenge. Surface modification techniques and the use of adhesion promoters are being explored to enhance the interfacial bonding between the Cu film and the substrate.
- Integration with advanced manufacturing: The integration of electroless Cu deposition with advanced manufacturing technologies, such as 3D printing and roll-to-roll processing, presents new opportunities and challenges. The development of compatible materials and processes is essential for realizing the full potential of electroless Cu in these emerging applications.
Conclusion
Electroless Cu deposition is a versatile and cost-effective method for creating conductive surfaces on a wide range of substrates. Its ability to provide uniform and adherent Cu films without the need for an external electrical current has made it an indispensable tool in various industries, from PCBs and microelectronics to automotive and aerospace. As the demand for advanced materials and technologies continues to grow, electroless Cu deposition is expected to play an increasingly important role in enabling the next generation of electronic devices and systems. However, addressing the challenges related to bath stability, environmental sustainability, and process reliability will be crucial for the continued success and widespread adoption of this powerful technique.
Frequently Asked Questions (FAQ)
-
What is electroless copper deposition?
Electroless copper deposition is a chemical process that involves the deposition of a thin, uniform layer of copper onto a substrate without the use of an external electrical current. -
What are the advantages of electroless Cu deposition compared to electroplating?
The advantages of electroless Cu deposition include uniform coating thickness on complex geometries, ability to deposit on non-conductive substrates, excellent adhesion and mechanical properties, cost-effectiveness, and environmental friendliness. -
What are the key components of an electroless Cu plating bath?
The key components of an electroless Cu plating bath are the copper source (e.g., CuSO~4~ or CuCl~2~), reducing agent (e.g., formaldehyde), complexing agent (e.g., EDTA), pH regulator (e.g., NaOH), and stabilizers (e.g., 2,2′-bipyridyl). -
What are the main applications of electroless Cu deposition?
The main applications of electroless Cu deposition include printed circuit boards (PCBs), microelectronics, electromagnetic interference (EMI) shielding, decorative coatings, and metallization of lightweight composite materials in the automotive and aerospace industries. -
What are the challenges and future perspectives of electroless Cu deposition?
The challenges and future perspectives of electroless Cu deposition include improving bath stability, developing eco-friendly reducing agents, enhancing adhesion and reliability of Cu films on non-conductive substrates, and integrating electroless Cu with advanced manufacturing technologies, such as 3D printing and roll-to-roll processing.
Leave a Reply