Introduction to PCB Drilled Holes
Printed Circuit Boards (PCBs) are essential components in modern electronics. They provide a platform for mounting and interconnecting electronic components. One crucial aspect of PCB design and fabrication is the creation of drilled holes. These holes serve various purposes, such as allowing component leads to pass through, enabling inter-layer connections, and facilitating mounting options.
In this comprehensive article, we will dive deep into the world of PCB drilled holes. We will explore the different types of drilled holes, their purposes, design considerations, manufacturing processes, and common challenges encountered. By the end of this article, you will have a solid understanding of PCB drilled holes and how to avoid surprises during the design and manufacturing phases.
Types of PCB Drilled Holes
There are several types of drilled holes used in PCBs, each serving a specific purpose. Let’s take a closer look at the most common types:
Through Holes
Through holes are the most basic type of drilled holes in PCBs. They extend completely through the board, from the top layer to the bottom layer. Through holes are primarily used for mounting through-hole components, such as resistors, capacitors, and connectors. They also enable electrical connections between different layers of the PCB.
Blind Vias
Blind vias are drilled holes that start from either the top or bottom layer of the PCB and terminate at an inner layer. They do not extend through the entire thickness of the board. Blind vias are commonly used in high-density PCB designs to save space and improve signal integrity. They allow for more compact routing and reduce the overall size of the PCB.
Buried Vias
Buried vias are drilled holes that are located entirely within the inner layers of the PCB. They do not extend to the top or bottom layers. Buried vias are used to create connections between inner layers without occupying space on the outer layers. They are particularly useful in complex, multi-layer PCB designs where space is limited.
Micro Vias
Micro vias are extremely small drilled holes, typically less than 0.15mm in diameter. They are used in high-density interconnect (HDI) PCB designs to achieve fine-pitch connections and high component density. Micro vias are usually laser-drilled and can be stacked to create multi-layer interconnections.
PCB Drilled Hole Design Considerations
Designing drilled holes in PCBs requires careful consideration of various factors to ensure proper functionality, manufacturability, and reliability. Here are some key design considerations:
Hole Size and Tolerance
The size of the drilled holes is a critical factor in PCB design. The hole diameter should be chosen based on the component lead size and the manufacturing capabilities of the PCB fabricator. It is essential to specify the hole size tolerance to ensure that the holes are neither too small nor too large for the intended components.
Component Type | Typical Hole Diameter |
---|---|
Resistors | 0.8mm – 1.0mm |
Capacitors | 0.8mm – 1.2mm |
Connectors | 1.0mm – 3.0mm |
Micro Vias | 0.1mm – 0.15mm |
Pad Size and Annular Ring
The pad size and annular ring are closely related to the hole size. The pad is the copper area surrounding the drilled hole, while the annular ring is the minimum width of the pad around the hole. The pad size should be large enough to accommodate the hole tolerances and provide sufficient area for soldering. The annular ring should be wide enough to ensure a reliable connection and prevent breakout during the drilling process.
Hole Diameter | Minimum Annular Ring |
---|---|
0.2mm – 0.5mm | 0.15mm |
0.5mm – 1.0mm | 0.2mm |
1.0mm – 2.0mm | 0.25mm |
2.0mm – 3.0mm | 0.3mm |
Drill to Copper Clearance
The drill to copper clearance is the minimum distance between the edge of the drilled hole and any adjacent copper features, such as traces or pads. Maintaining sufficient clearance is crucial to prevent short circuits and ensure the integrity of the PCB. The clearance requirements depend on the PCB fabricator’s capabilities and the specific design requirements.
PCB Layer | Minimum Drill to Copper Clearance |
---|---|
Outer Layers | 0.2mm |
Inner Layers | 0.15mm |
Via Spacing and Placement
When placing vias on the PCB, it is important to consider the spacing between them and their proximity to other components and features. Proper via spacing helps prevent signal integrity issues, such as crosstalk and electromagnetic interference (EMI). The minimum via spacing depends on the PCB fabricator’s design rules and the specific requirements of the design.
Via Type | Minimum Via Spacing |
---|---|
Through Vias | 0.5mm |
Blind Vias | 0.3mm |
Buried Vias | 0.25mm |
Micro Vias | 0.2mm |
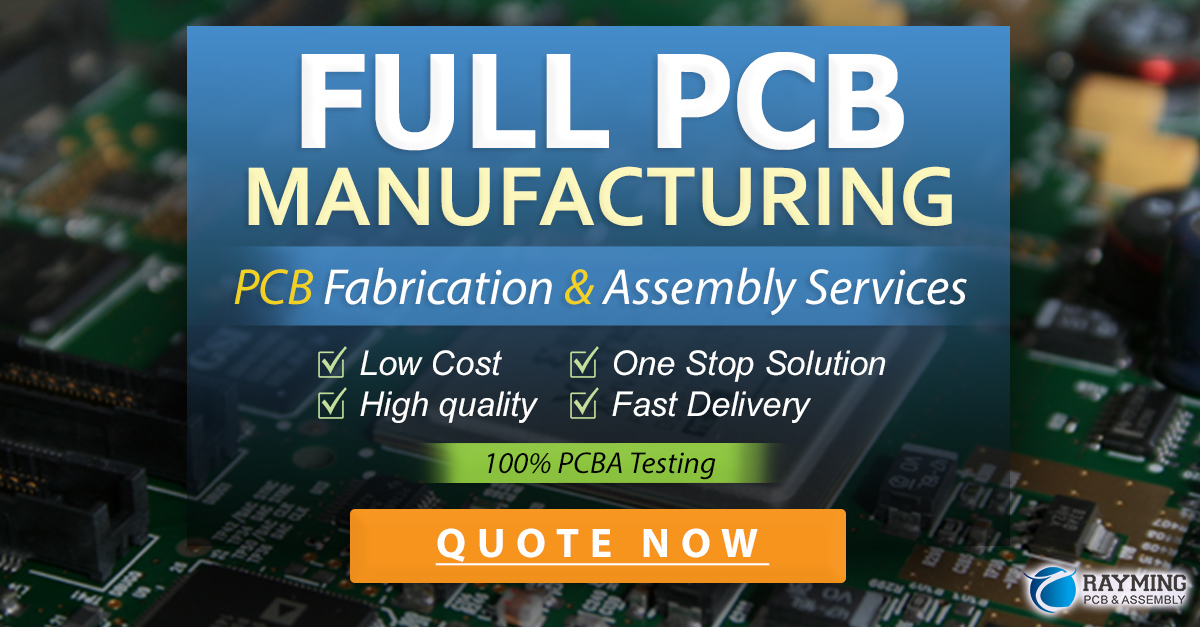
PCB Drilled Hole Manufacturing Process
The manufacturing process for PCB drilled holes involves several steps to ensure accurate and reliable hole creation. Let’s explore the key stages of the drilling process:
Drilling Methods
There are two primary methods for drilling holes in PCBs: mechanical drilling and laser drilling.
- Mechanical Drilling:
- Mechanical drilling uses high-speed drill bits to create holes in the PCB.
- It is suitable for creating larger holes, typically above 0.3mm in diameter.
-
Mechanical drilling is a cost-effective method for low to medium-volume production.
-
Laser Drilling:
- Laser drilling uses focused laser beams to create holes in the PCB.
- It is ideal for creating smaller holes, such as micro vias, with diameters below 0.15mm.
- Laser drilling offers high precision and the ability to create holes in specific layers of the PCB.
Drilling Sequence
The drilling sequence is an important consideration in the manufacturing process. It determines the order in which the holes are drilled and can impact the overall efficiency and quality of the drilling process.
- Stacked Drilling:
- Stacked drilling involves drilling all the holes in a specific area of the PCB before moving to the next area.
- It minimizes drill bit changes and reduces the overall drilling time.
-
Stacked drilling is commonly used for low to medium-volume production.
-
Sequence Drilling:
- Sequence drilling involves drilling all the holes of a specific size before moving to the next size.
- It minimizes drill bit changes and ensures consistent hole quality for each size.
- Sequence drilling is suitable for high-volume production and designs with a large number of holes.
Deburring and Cleaning
After the drilling process, it is essential to remove any burrs or debris from the drilled holes. Deburring ensures that the holes have clean and smooth edges, which is crucial for proper component assembly and reliable electrical connections. Cleaning the PCB after drilling removes any remaining debris and prepares the board for the subsequent manufacturing steps.
Common Challenges and Solutions
Drilling holes in PCBs can present various challenges that can impact the quality and reliability of the final product. Let’s discuss some common challenges and their solutions:
Hole Misalignment
Hole misalignment occurs when the drilled holes do not align accurately with the designed positions on the PCB. This can lead to component fitment issues and affect the overall functionality of the board.
Solutions:
– Use precise drilling equipment and maintain proper calibration.
– Implement robust registration and alignment techniques during the drilling process.
– Verify the drill file and ensure accurate data transfer to the drilling equipment.
Hole Breakout
Hole breakout refers to the unintended removal of copper around the drilled hole, resulting in a broken or incomplete annular ring. This can compromise the electrical connection and structural integrity of the PCB.
Solutions:
– Ensure sufficient annular ring width based on the hole size and manufacturing capabilities.
– Optimize the drilling parameters, such as feed rate and spindle speed, to minimize stress on the copper.
– Use backing materials or entry/exit boards to support the PCB during drilling and reduce the risk of breakout.
Drill Bit Wear and Breakage
Drill bits are subject to wear and tear during the drilling process, which can affect the hole quality and lead to drill bit breakage.
Solutions:
– Use high-quality drill bits suitable for the specific PCB material and hole sizes.
– Implement proper drill bit management, including regular inspection and replacement.
– Optimize the drilling parameters to minimize wear and extend drill bit life.
– Use proper coolant and lubrication to reduce friction and heat generation during drilling.
Copper Burrs and Smearing
Copper burrs and smearing can occur during the drilling process, resulting in rough hole walls and potential short circuits.
Solutions:
– Use sharp and well-maintained drill bits to minimize burr formation.
– Optimize the drilling speed and feed rate to reduce heat generation and minimize smearing.
– Implement effective deburring and cleaning processes to remove burrs and debris.
– Consider using specialized drill bits or drilling techniques, such as peck drilling, to minimize burr formation.
FAQ
- What are the most common hole sizes used in PCBs?
-
The most common hole sizes in PCBs range from 0.3mm to 1.0mm, depending on the component requirements. Typical sizes include 0.8mm for resistors and capacitors, 1.0mm for connectors, and 0.3mm to 0.5mm for vias.
-
How do I choose the appropriate pad size for a drilled hole?
-
The pad size should be selected based on the hole size, tolerances, and the required annular ring. A general rule of thumb is to make the pad diameter approximately 0.5mm larger than the hole diameter. However, it is important to consult the PCB fabricator’s design guidelines for specific recommendations.
-
Can I use the same drill bit for different hole sizes?
-
It is recommended to use specific drill bits for each hole size to ensure accurate and consistent hole dimensions. Using the same drill bit for different sizes can lead to hole quality issues and reduced drill bit life.
-
How can I minimize the risk of drill bit breakage during the PCB Drilling process?
-
To minimize drill bit breakage, use high-quality drill bits suitable for the PCB material and hole sizes. Regularly inspect and replace worn or damaged drill bits. Optimize the drilling parameters, such as feed rate and spindle speed, to reduce stress on the drill bits. Additionally, use proper coolant and lubrication to minimize friction and heat generation.
-
What are the advantages of using blind and buried vias in PCB design?
- Blind and buried vias offer several advantages in PCB design. They allow for more compact routing and higher component density by utilizing the inner layers of the PCB. Blind vias enable shorter signal paths and improved signal integrity, while buried vias help in creating efficient inter-layer connections without occupying space on the outer layers. These types of vias are particularly useful in high-density and multi-layer PCB designs where space is limited.
Conclusion
Drilled holes are a fundamental aspect of PCB design and manufacturing. Understanding the different types of drilled holes, their purposes, design considerations, manufacturing processes, and common challenges is crucial for creating reliable and high-quality PCBs.
By following best practices in hole design, such as selecting appropriate hole sizes, pad sizes, and annular rings, and considering drill to copper clearances and via placement, designers can ensure the manufacturability and functionality of their PCBs. Additionally, collaborating closely with PCB fabricators and understanding their capabilities and guidelines can help avoid surprises and achieve optimal results.
As technology advances and electronic devices become more complex, the importance of precise and reliable PCB drilled holes continues to grow. By staying informed and adopting industry best practices, designers and manufacturers can navigate the challenges and create PCBs that meet the ever-increasing demands of modern electronics.
Leave a Reply